Emeakpo Ojonah, Halliburton
While the world is transitioning into a greener and less-carbon-rich energy source, the fact remains that there is a growing need for exploration and production of hydrocarbons in previously untapped resources. These frontier reservoirs, while extremely hot, are prolific and make the footprint of the exploration activity much smaller than shallower drilling, which would require many more wells to deliver the same amount of hydrocarbon. These frontier wells, classified as high-pressure/high-temperature (HP/HT) wells, are defined as wells with reservoir or bottomhole temperatures higher than 300°F and which require pressure-control equipment with a rating above 10,000 psi. HP/HT wells can be found offshore in the North Sea and Gulf of Mexico, or on land—as seen recently in the Gongola Basin.
Fluid identification, which is a critical process in fluid sampling, continues to be a challenge in temperatures above 350°F. At temperatures up to 450°F, fluid identification is currently achieved by bubblepoint and compressibility measurements, which cannot quantitatively measure contamination levels of the subject sample fluid.
A possible solution to this problem would involve using pyroelectric detectors in the process of estimating a property of a downhole fluid. The method and apparatus in this approach involves exposing a fluid to modulated light downhole and sensing changes in the intensity of infrared radiation from the downhole fluid, to estimate the level of filtrate contamination and other properties.
The pyroelectric detector senses changes in the intensity of light by converting the transient changes in temperature of its detector and performs the spectroscopic fluid analysis by optically filtering the light allowed to impinge on it, converting the changes in temperature of the pyroelectric detector to a signal which can then be used to estimate the property of the downhole fluid.
If successfully implemented, this would enable the wireline-logging industry to develop an optical fluid analyser capable of quantitatively measuring fluid contamination levels in high-temperature (greater than 300°F) environments.
Theory
Pyroelectric infrared detectors (PIR) convert the changes in incoming infrared light to electric signals. Pyroelectric materials are characterized by having spontaneous electric polarization, which is altered by temperature changes as infrared light illuminates the elements.
Pyroelectric detectors (Fig. 1) are thermal detectors, meaning they produce a signal in response to a change in their temperature. Below a case temperature (Tc) known as the Curie point, ferroelectric materials such as lithium tantalate exhibit a large spontaneous electrical polarization. If the temperature of such a material is altered, for example by incident radiation, the polarization changes. This change in polarization may be observed as an electrical signal when electrodes are placed on opposite faces of a thin slice of the material to form a capacitor. When the polarization changes, if the external impedance is comparatively high, the charges induced in the electrodes can be made to produce a voltage across the slice. The sensor will only produce an electrical output signal when the temperature changes; that is, when the level of incident-radiation changes.
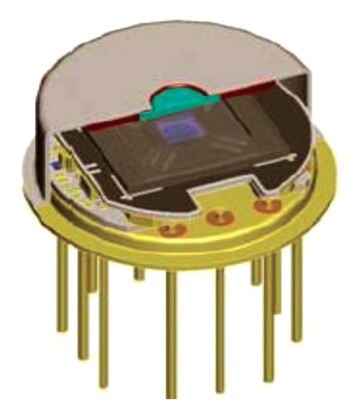
This process is independent of the wavelength of the incident radiation; hence, pyroelectric sensors have a flat response over a very wide spectral range. The limiting feature on the spectral range is the window material used in the manufacture of the sensor housing. By using different windows materials, it is possible to detect radiation at different frequencies.
Some applications of a pyroelectric detector include motion sensors, light controls, temperature measurements, flame detectors, automatic door switches, and home security.
Properties of reservoir fluids and gases can be analysed downhole using near and mid-infrared light detection. The mid-infrared or “fingerprint” region of the spectrum is preferable for identifying specific chemical compounds and for achieving higher sensitivity to small concentrations of chemicals. At much higher temperatures, background mid-infrared radiation (MIR) that is emitted by the fluid-identification tool may affect any readings taken by photodetectors. In contrast, pyroelectric detectors do not respond to background MIR. Because these detectors respond only to changes in light intensity, they can operate at much higher temperatures as compared to a typical photodetector.
Another effect of high temperatures on photodetectors is the response of the photodiodes. For the same amount of light, the response of most photodiodes reduces with increasing temperature because the internal shunt resistance of the photodiode decreases as the temperature increases. As DiFoggio et al. (2008) noted in a US patent, the effect increases for photodiodes with longer wavelengths, such as those sensitive to light in the MIR (2.5 to 11 micron) range.
Typically, the longer the wavelength a photodiode can detect, the lower the photodiodes shunt resistance at room temperature. The shunt resistance drops even further at elevated temperatures. Pyroelectric detectors respond to the rate of temperature change (such as that caused by absorbing a blinking light) rather than to temperature itself. Thus, pyroelectric detectors are not affected by high temperatures, so long as these temperatures are far below the detector’s Curie temperature, which is about 620°C for lithium tantalate. This makes the pyroelectric detector well-suited for performing downhole spectroscopy.
Application
The pyroelectric detector can be used to perform spectroscopic analysis of fluid by optically filtering the light that impinges on it, converting the rate of temperature change to a signal, and analyzing the signal to estimate the property of the downhole fluid.
A soft modeling technique can then be applied to the spectroscopic analysis to estimate a physical characteristic or a chemical characteristic of a downhole fluid or gas. The physical characteristic will include the density and viscosity of the downhole fluid, while the chemical characteristic will include the composition of the fluid or gas. Formation cleanup will be estimated from a series of property determinations (such as successive viscosity estimates) of the downhole fluid, or from a direct estimation of the percentage of filtrate contamination in the downhole fluid.
Tests and Results
In exploring the feasibility of this concept, testing was conducted on 12 different base oils used in drilling mud and crude oil (#996), including BG3900, B C14-C16 LAO, DF01, Eco-flow, Escaid, HDF-2000, Iso-Tech, NX-3500, Omnidrill, Paratec, Syndrill, and Syntec. Infrared light was passed through these liquids over a path length of 0.025 mm and their spectra were captured by a detector. This experiment was conducted with a mid-range infrared spectrometer (Fig. 2) with a diamond optical window. A total of 64 data sets were taken for each fluid across the mid-infrared wavelength of 6 microns to 11 microns.
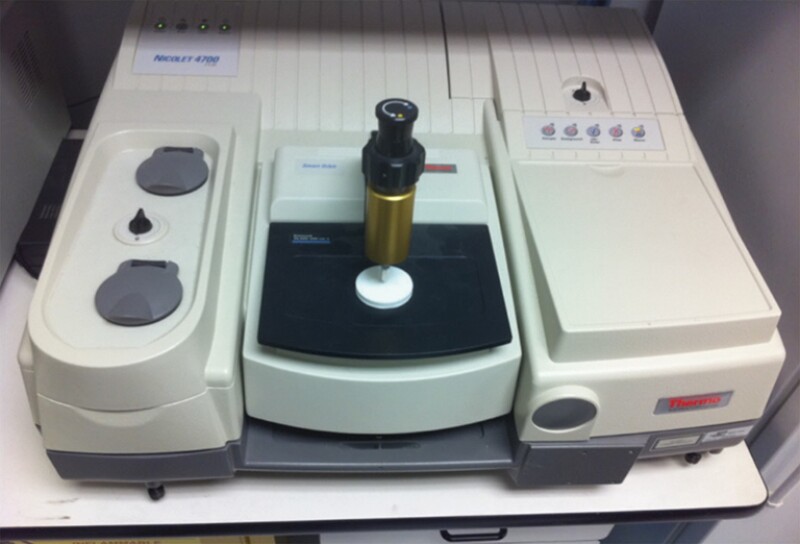
The results of the test revealed that there are two distinct peaks found in the base oils that do not occur in crude oil: the olefin and ester peaks. These peaks can be clearly identified in the mid-range infrared (Fig. 3).
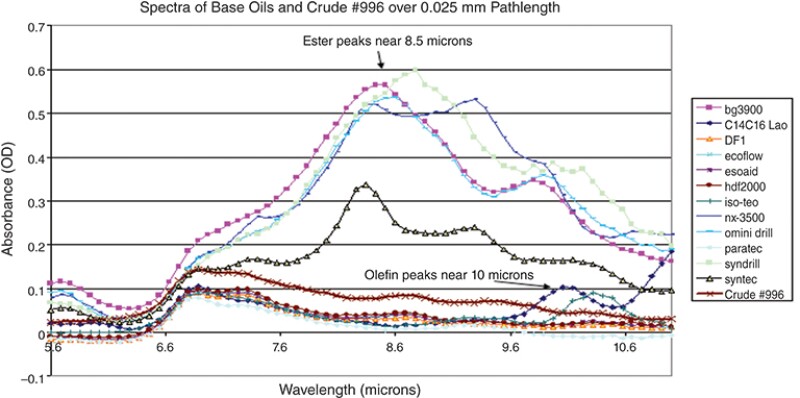
As Fig. 3 shows, not all the base oils had both peaks distinctly represented in them. While BG3900, Syndrill, NX-3500, Omnidrill, and Syntec had both the olefin and ester peaks distinctly represented, only the olefin peak is seen distinctly in B C14-C16 LAO and Iso-Tech, and the ester peak appears in only Escaid, HDF‑2000, and Ecoflow. Paratec shows no distinct peak for either ester or olefin, as this base oil is processed from crude oil and thus shows similar characteristics to crude (this will be one limitation of this method). Base oils that are derived from crude or any of its processed compounds such as diesel cannot be clearly identified from crude oil.
Discussion
Test results from the initial experiments suggest that the science is tenable and can be applied to the spectroscopic analysis of fluids. The present limitations of the science will be the analysis of drilling fluids that have been “cut” from crude oil, mixed with crude itself. Presently, due to environmental reasons, most exploration companies have refrained from the use of drilling mud processed from crude. One of the leading oilfield services companies is conducting an ongoing exercise to collect data on what percentage of oil-based drilling muds are of this category. The other limitation will be the engineering challenges associated with implementing the science downhole: most challenging will be a high-gain, high-temperature amplification circuitry for signal amplification.
Reference
Method and Apparatus for Analyzing a Downhole Fluid Using a Thermal Detector (2008).US Patent Number 7,423,258 B2
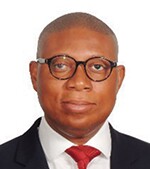
Emeakpo Ojonah has over 15 years of experience working in the oilfield services (OFS) industry with a career spanning more than nine countries, including Nigeria, Uganda, Angola, US, Vietnam, Japan, Korea, Thailand, and Brunei Darussalam. He has worked in senior technical and commercial roles at both Baker Hughes and most recently, Halliburton. As a leader in technical engineering management on a national and global scale, he specializes in cutting-edge technologies and techniques, from testing to introduction and execution, and provides expert support to the oil and gas, geothermal, and carbon-capture-and-storage industries. Ojonah is a member of the Society of Petroleum Engineers and served as the Publicity and Communications Chair of the SPE Vietnam section from 2017 to 2018.