In view of Saudi Aramco’s aspiration to be the leading digitalized energy company by 2022, the company is accelerating the adoption and scaleup of robotic technologies to address corporate challenges and introduce new improvement opportunities. These disruptive and multipurpose technologies serve the energy sector by delivering safer, cost-effective, and efficient inspection capabilities, emergency response, aerial mapping, project monitoring, security surveillance, environmental monitoring, and many other key industrial applications.
Unmanned aerial vehicles (UAVs), commonly known as drones, are becoming a critical enabler for inspection by integrating high-resolution sensors and cameras to collect visual data on the condition of assets such as rigs, platforms, tanks, columns, and elevated structures. Thus, reduce the cost by minimizing the need to erect and take down scaffolding, enhance safety by avoiding the need for inspectors to work at height or enter dangerous confined spaces. In addition, UAVs are equipped with various sensors such as cameras, radiometric thermal sensors, optical gas imaging, hyperspectral, LiDAR and others. This customization expands UAVs’ capabilities and widens the applications portfolio to support environmental, construction, pipelines, security, and aerial mapping.
Robots are also game-changing technology that boost the performance of capital-intensive infrastructures. Intelligent autonomous robots deliver routine inspection, high-quality data, and support during emergencies. In this article, the emerging robotic technologies for oil and gas operations are covered with real field uses cases and realized benefits to business.
Introduction
Robotics have undergone dramatic changes in the past 5 years through the development and advancement of high-quality sensors, motors, and low-cost navigation systems that caused an exponential increase in the number of flying, driving, and swimming robotic systems. The oil and gas sector is adopting these technologies to enhance operations, reduce cost, enable responsiveness, and guarantee the safety and integrity of employees and industrial facilities. Some of these robotic systems will reside permanently at a facility, such as a refinery or gas plant, while others will be pooled as part of a technician’s toolkit. Moreover, artificial intelligence (AI), data analytics, and the internet of things (IoT) are becoming an integral part of the next-generation robots that are fully autonomous and capable of remote operations. This robotics advancement has the potential to transform how the oil and gas industry operates, and greatly facilitates the real-time data-driven, decision-making process and prediction capabilities.
According to a recent World Economic Forum (WEF) report, robotics and drones are expected to be the highest adopted technologies, with the highest growth in the oil and gas sector for the next 3–5 years (Fig. 1).
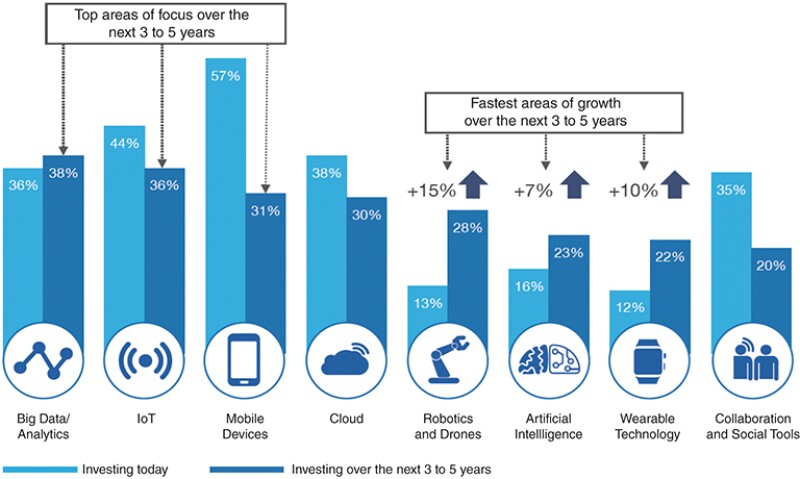
Robotics Focus Areas
Robotic technologies can be deployed in a wide range of market domains, each having its own needs and requirements. In general, the robotics domain is classified into three focus areas: air, ground, and subsea (Fig. 2).
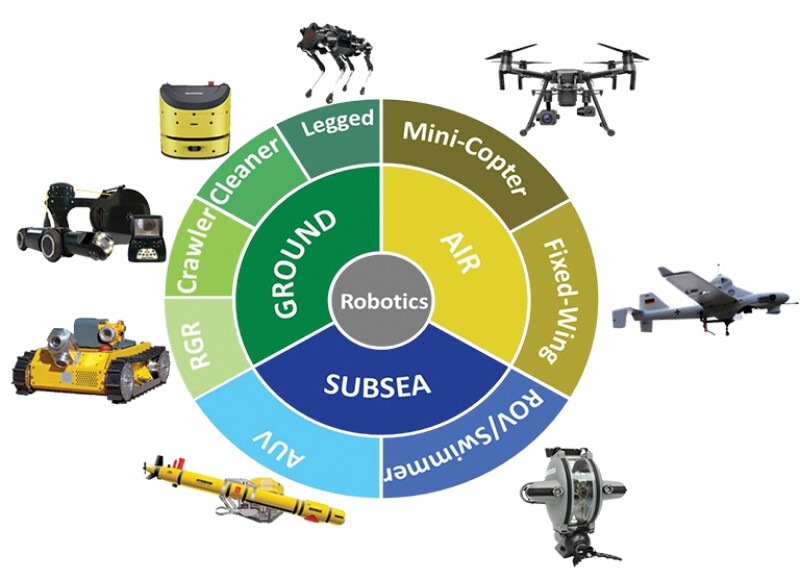
Saudi Aramco’s inspection department of engineering services is leading the robotics and UAV track as part of the digital transformation program. Its objective is to accelerate the development and deployment of robotics technologies through a structured program aiming to reduce operational cost, improve efficiency, enhance safety, and resolve corporate technical challenges.
Air Robots
Air robots hover and maneuver in air using various forms of propelling techniques such as wings or spinning propellers. There are two main categories of air robots: the mini-copter UAV for short-range and the fixed-wing UAV for long-range applications.
The mini-copter UAVs are widespread in the market and increasingly adopted in the oil and gas sector, as this type of UAV presents increasingly attractive opportunities to enhance operations, reduce cost, improve safety, and enable an agile response. The fixed-wing UAVs target widespread operations, such as pipelines and offshore operations for surveys, emergency response, marine oil-spill monitoring, and other applications.
In 2019, the estimated mini-copter UAV market size for professional drones in the US was about 392,000 drones, worth $1.6 billion. Moreover, sales and revenue are expected to reach 2,679,000 drones and 12.6 billion by 2025 (Fig. 3).
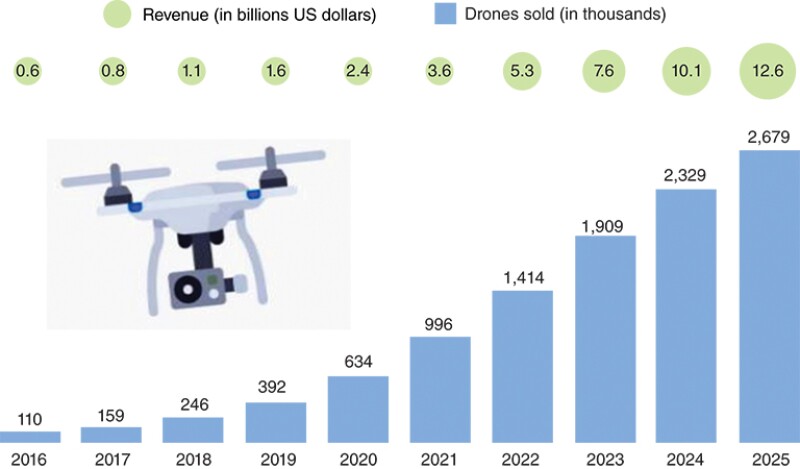
There is a vast range of industrial applications for mini-copter UAVs covering industrial visual inspection, confined-space inspection, surveying, mapping, thickness measurement, project construction management, environmental monitoring, security and surveillance, and aerial photography and videography.
In the conventional inspection method, scaffolding would be erected around oil tanks so that inspectors can climb and check the condition of the tank. Moreover, for flare stack tip inspection, there is limited access to the flare tip, and the only way to carry out such inspection is during planned shutdown periods or emergency shutdowns.
By using the UAV technology, the inspector flies the UAV around the tank and collects high-resolution images and thermal data without the need for scaffolding. The inspector checks the tank conditions for any deformation, cracks, corrosion, or coating deterioration. For a flare stack tip, the UAV is used to inspect the flare tip’s condition for anomalies and hotspots. The use of UAVs results in potential cost avoidance and enhanced safety, as inspectors do not need to work at height. Furthermore, it allows inspection to be carried out without the need for shutdown.
In 2019, Saudi Aramco expanded its UAV fleet by introducing 18 new UAVs. These UAVs support field operations covering inspection activities of onshore and offshore flares, storage tanks, elevated structures, power system infrastructure, aerial mapping, and environmental monitoring. Seven of these UAVs were dedicated to support live-video streaming capabilities to the oil supply planning and scheduling (OSPAS) department and emergency control centers during emergency situations.
In addition, the UAV-based methane detection technology was introduced to detect and quantify the concentration of methane and other hydrocarbon gas leaks. This effort reflects Saudi Aramco’s commitment to reduce greenhouse-gas emissions (Fig. 4).
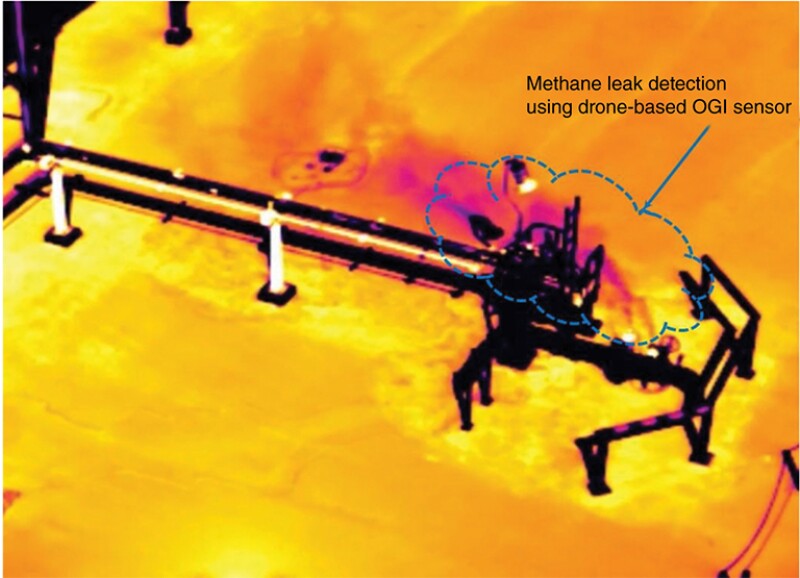
The UAV is integrated with two sensors to detect and measure methane.
- Optical gas imaging (OGI). This sensor (specialized radiometric thermal camera) is used to detect, visualize, and pinpoint gases such as methane, ethane, propane, butane, and benzene.
- Tunable diode laser absorption spectroscopy (TDLAS). Once a gas is detected by OGI, this sensor (tunable laser diode) emits a laser beam at a specific wavelength toward the gas, which absorbs the laser beam in accordance to its characteristics. Every molecule has a unique light absorption characteristic/curve, and this physical property is used to identify and quantify gas concentration.
An UAV-based radio-frequency identification (RFID) solution was developed in-house to enhance pipe inventory management by integrating the RFID payload for quick and effective material inventory. The UAV solution resolved the limited mobility of the conventional ground inventory practices due to limited aisle accessibility. This technology was able to accurately identify, count, and locate 4,000 pipes in 4 minutes at a pipe yard using RFID and GPS coordinates.
Ground Robots
Ground robots are mobile or fixed robots that operate manually or semiautonomously to support field operational activities, including inspection and maintenance tasks, and perform first-level visual and thermal inspection, read gauges, sniff gas leaks, hear surrounding and mechanical vibrations, and support emergency responses. This robot comprises a base (platform), payload sensors, and operation controller (Fig. 5).
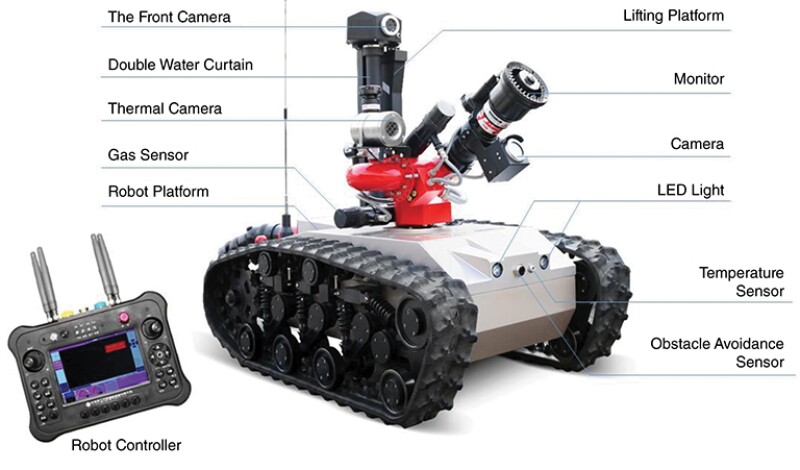
In 2019, Saudi Aramco deployed the first explosion-proof multipurpose firefighting robot equipped with multiple visual and thermal cameras, heat tracking sensors, gas detector, as well as 12 bar water connections to support effective and safe firefighting operations at a closer proximity to the fire source. The robot has the capability to send live-video streaming to the mobile command center and OSPAS emergency room through the company secured network.
For remote and unmanned field operations, the next generation of ground and legged robots are under development to enable reliable and highly agile and maneuverable robotic platforms, to support remote field operations, inspection, surveillance; and by integrating top-mounted robotic arms with multiple axis freedom, it can perform jobs such as controlling valves and local panels. The inspection departmnet is working closely with technology suppliers to advance the development and testing of these platforms (Fig. 6).
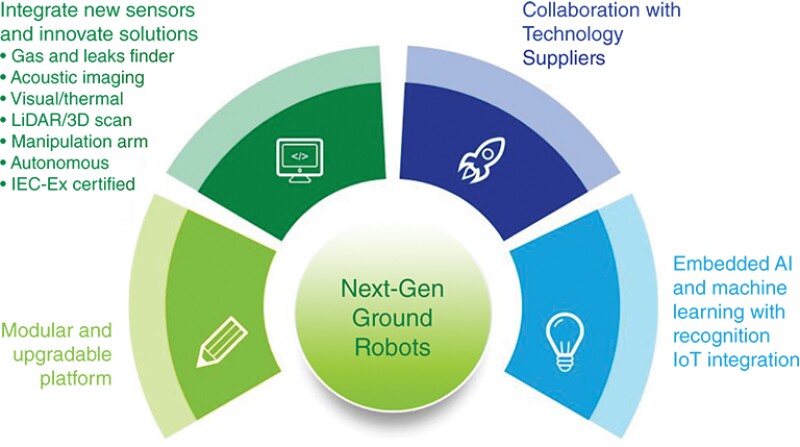
Subsea Robots
Subsea robots operate in the marine environment and navigate in the water using thrusters. The number of thrusters define their degree of freedom and their ability to move in various directions and achieve different orientations. These robots have a wide range of subsea applications such as inspection, exploration, marine life research, and surveys.
There are two types of subsea robots: remotely operated vehicle (ROV) and autonomous underwater vehicle (AUV). The ROVs are tethered subsea robots that deliver data, images, and videos to the operator. They are equipped with various sensors and a grabber that can perform subsea inspection and testing functions. This technology minimizes the need for boats and divers to inspect and monitor subsea assets, such as pipelines, foundations, and submarine composite cable and water intakes. The AUVs are untethered fully autonomous robots that generate high-resolution subsea surveys.
Saudi Aramco has successfully deployed an industrial-grade mini-ROV as a multipurpose solution for subsea assets inspection and monitoring by transmitting real-time video streaming and capturing high-resolution images of foundations, pipelines, composite cables, and concrete encasements.
Conclusion
Robotic technologies are rapidly accelerating and becoming smarter and more versatile. Saud Aramco is maximizing the deployment of these cutting-edge and disruptive technologies to enhance operations and realize benefits. AI, data analytics, and IoT are becoming an integral part of the emerging robots that are fully autonomous and capable of remote operations. This robotics advancement has the potential to transform how oil and gas companies operate. Furthermore, the combination of these technologies and capabilities will greatly facilitate the real-time, data-driven decision-making process and prediction abilities.
References
Whitepaper: Digital Transformation in the Oil and Gas Industry by B. Weinelt, World Economic Forum. January 2017, pp.8–9.
Projected Commercial Drone Revenue Worldwide 2016–2025 by I. Wagner, Statista. 6 March 2020.
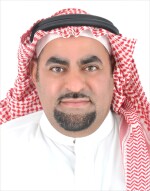
Soliman A. Al-Walaie is a senior engineering consultant in the inspection department of Saudi Aramco with more than 22 years of experience in industrial networks, unmanned aerial vehicles, and robotics engineering. He is the technical leader of the UAV and robotics domain in Saudi Aramco, which is part of the Digital Transformation Program. He holds a BS in electrical engineering from King Saud University, Saudi Arabia, and an MS in telecommunications from University of Maryland, College Park.
Osama B. Bahwal is an engineering specialist in the inspection department of Saudi Aramco with more than 25 years of experience in IT technologies and project management. He holds a BS in electronic and communications engineering from King AbdulAziz University, Saudi Arabia.
Sarah S. Alduayj works as a business system analyst in the Saudi Aramco Digital Transformation Program. She is responsible for planning the Saudi Aramco digital transformation (DT) road map along with ensuring the delivery of DT use cases. She is currently vice chairing the IEEE Computer Society at Saudi Arabia. She holds an MSc in advanced computer science from the University of Birmingham, UK.