Controlling inorganic sulphate and carbonate scales with polymer, phosphonate, and phosphate ester scale inhibitors is commonplace in the oilfield services industry. It is well understood in what environments induvial inhibitor types work best; for example, sulphonates are very effective for sulphate scale control in low temperatures (SPE 80229) whereas phosphonates are much less effective under these same conditions but improve at higher temperatures (SPE 179889).
Less well understood is the potential for scale inhibitors utilizing synergistic interactions with blends of polymers, phosphonates, and phosphate esters to reduce chemical cost, treatment rates, and transport logistics, resulting in a more effective scale management program with a reduced operational footprint.
To evaluate performance of a selected range of blended inhibitors, ChampionX performed a trial on a North Sea produced water system, which was applying monoethanolamine (MEA) phosphonate-type scale inhibitor as well as novel cleaning programs to counter a high carbonate saturation ratio in the heater (SPE 204365). The objective was to find an improved scale inhibitor formulation that would outperform MEA phosphonate to control the high calcite saturation ratio brine. In this application, produced fluids pass through a heater with a skin temperature between 90°C and 105°C.
Identifying the Scale Challenge
Studies of synergistic properties of phosphonates and polymer scale inhibitors show there is potential to create blends of existing chemicals to make a formulation that shows a performance greater than either inhibitor component on its own. Four generic scale inhibitors that could effectively prevent scale at 105°C were considered.
1. A poly aspartate acid, generally found to be thermally stable to 120°C
2. The incumbent MEA phosphonate chemical, which is widely used for this type of scale inhibition at elevated temperature
3. A phosphate ester, found to be thermally stable at temperatures of 90°C
4. Phosphonate-functionalized biopolymer, which showed good carbonate inhibition properties and excellent environmental properties
The goal was to develop a synergistic blend that would mitigate the legislative (cost of REACH registration) and economic (cost of new raw material product set up within the supply chain system) issues associated with the development of new classes of scale inhibitor for a relatively small market.
There are two primary methods of scale inhibition in produced water. The first is crystal nucleation inhibition, which prevents the onset of scale formation itself by keeping the ions in solution. This mechanism of inhibition is best evaluated via dynamic scale loop (DSL) tests. The polymer-type scale inhibitors (such as carboxylic acid functionated homo and copolymers, for example VS-Co) work well within this test, as they prevent deposition at low treatment rate.
The other principal inhibition mechanism is crystal-growth inhibition. This prevents the continued growth of microscale crystals as the inhibitor interacts with the scale crystal surface to prevent further addition of sulphate/barium ions. This is best evaluated via static bottle tests. Phosphonate-type scale inhibitors, for example, diethylenetriamine penta (methylene phosphonic acid), work well within this type of test.
Determining Inhibitor Efficiency
As carbonate scale was the main issue to be addressed, only DSL test methods were used to try and better understand the inhibition mechanism working for both the standalone chemicals and the blended products. It was also important to determine the minimum inhibitor concentration (MIC) needed to effectively treat the produced water system across the range of inhibitor chemistries selected.
Testing was performed at 105°C and 130 psi. The pH of the brines was adjusted to 7.1 and run at 6 mL/min through a 1-m-long (1-mm ID) stainless steel scaling coil. Differential pressure was measured across the coil to determine buildup of scaled deposition and performance of the scale inhibitor being tested. Inhibition efficacy was defined as the ability of the chemical under examination to control scale (<1 psi) for three times the period it had taken for a “scale blank” to form (time to exceed 1 psi across the scale coil).
Following the initial screening of potential synergistic blends, additional testing was carried out to assess the impact of dissolved iron (30 ppm) on the “scale blank” formation rate and the ability of the inhibitor to function in the presence of ferrous iron, a known potential issue for some generic scale inhibitors (Johnson et al. (2005); Graham et al. (2003); SPE 80254; NACE 00114).
Chemical and produced-brine compatibility testing was applied over the full range of concentration, starting at “drum strength” down to final diluted concentration (most likely the MIC). These tests were carried out with the synthetic produced water (excluding the bicarbonate/sulphate ions) over a period of 24 hours from room temperature to process temperature of 105°C. Visual observations were made upon mixing, after 2, 4, and finally at 24 hours. The concentration of chemical evaluated ranged from 0 ppm to 100%.
Initial screening of a maleic acid copolymer for chemical and brine compatibility carried out prior to DSL evaluation showed this class of chemical was not suitable for further evaluation due to its poor compatibility with the high calcium-ion concentration within the field brine and so was not evaluated further.
Experimental Results
While the brine was able to block the DSL coil within 8 to 10 minutes, evaluation of the “scale blank” time under process conditions confirmed that scale control was going to be challenging.
The four generic scale inhibitors that passed the chemical and produced-brine compatibility evaluation were considered at this stage of the study. Fig. 1 presents the DSL profile for the incumbent MEA phosphonate, evaluated at 60 ppm within the case study brine. It had been observed that 50 ppm was unable to control scale formation, but scale formation was prevented at 60 ppm. Therefore, 60 ppm MIC was the value all other single chemical and synergistic blends would need to outperform.
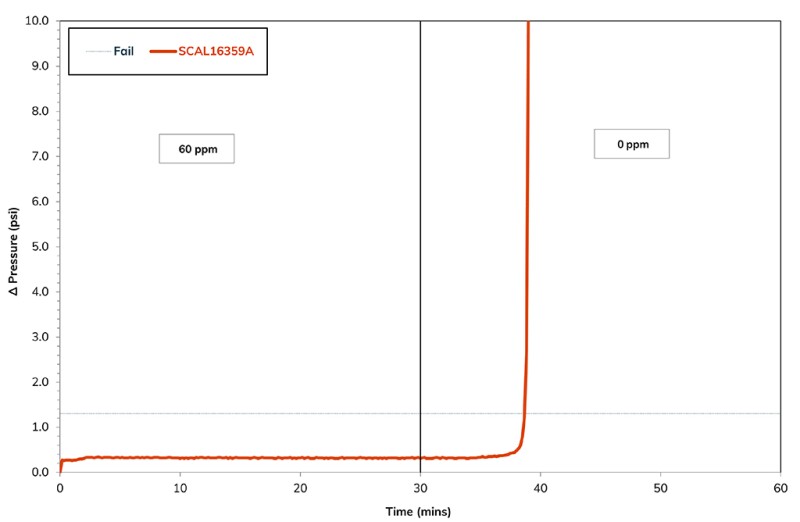
Fig. 2 presents the differential pressure profile during the evaluation of the phosphonate-functionalized biopolymer from 50 ppm down to 25 ppm within the synthetic produced brine. The concentration required to prevent scale formation was only 30 ppm, while the MEA phosphonate required 60 ppm. As both chemicals in the evaluated formation were similar, the performance advantage of this chemical is clear, as the product activity was not the reason for the improved performance.
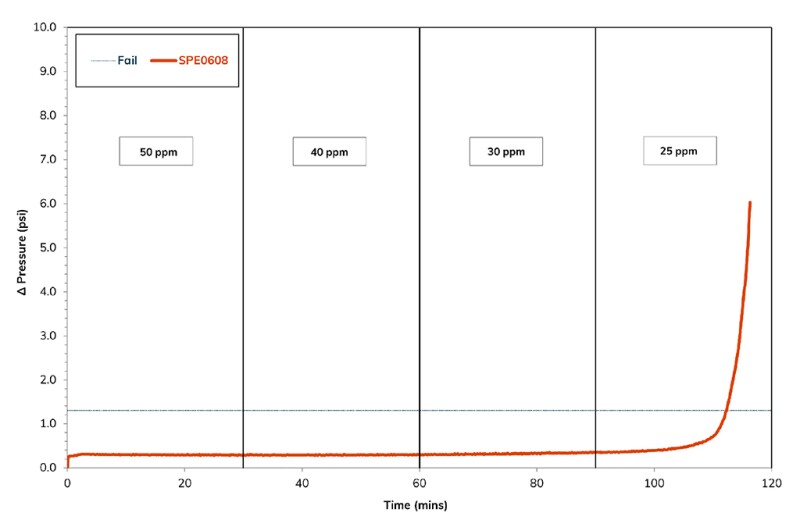
While the phosphate ester and the poly aspartic acid-based inhibitors showed slightly better performance than the incumbent chemical, neither were taken further in the evaluation. Reasons for this include
- Lower compatibility with the high-calcium brine, which may lead to pseudo-scale in a field application.
- Yellow phosphorus, the raw material used to make phosphonates, is in short supply.
Evaluation of the synergistic performance of MEA phosphonate and phosphonate-functionalized biopolymer. Varying ratios of MEA phosphonate and phosphonate-functionalized biopolymer were then evaluated to assess synergistic performance. The results are summarized in Table 1.
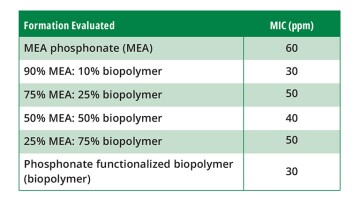
The performance of the 10% phosphonate-functionalized biopolymer formulation was the same as 100% of this polymer chemical. As the concentration of the biopolymer increased, the MIC increased. In fact, at 50% and 25% MEA phosphonate, there was a dilution-like effect, which appeared not to add to the performance based on the generic chemical’s concentration being tested.
This observation supports the idea that a polymer-type scale inhibitor (biopolymer) is working via nucleation inhibition and is more effective against carbonate scale formation than even a MEA phosphonate. The performance of the MEA phosphonate and biopolymer (90:10) has a significantly lower MIC value than the biopolymer concentration within the blend. This would suggest some synergistic interaction of the two chemicals is occurring to reduce the rate of scale nucleation within the brine.
Evaluation of the synergistic performance of MEA phosphonate and poly aspartic acid. To evaluate if a synergistic performance could be observed when MEA phosphonate and poly aspartic acid were tested at a single ratio in the case study brine, the two chemicals were formulated at a ratio of 75:25.
While the poly aspartic acid showed a higher MIC than the phosphonate-functionalized biopolymer, the chemistry is phosphorus-free. Based on testing, this presents the opportunity to reduce the amount of phosphonate within the blended formulation due to the observed synergistic effects. The combination of being able to reduce the treatment rate from 60 ppm for the phosphonate-only formation to 30 ppm for the phosphonate and polymer blend results in a 62% reduction in the amount of phosphonate required to control the carbonate scale formation, subsequently reducing the cost of treatment.
As the study progressed, it was noted that 30 ppm iron was present within the produced water, which can have a negative impact on carbonate scale formation and inhibitor performance. Therefore, additional DSL tests were conducted to evaluate the “blank time” with 30 ppm iron present as well as the impact the iron (ferrous iron and iron carbonate—siderite) would have on the incumbent chemical and the blend of MEA phosphonate and poly aspartic acid, as shown in Table 2.
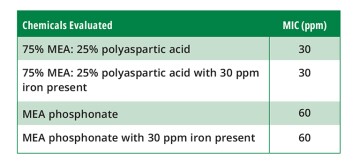
The “scale blank” time averaged 11 minutes—3 minutes longer than without iron present. The longer blank time is most likely due to the disruption in calcite formation that iron is known to create, leading to delayed scale-growth bridging of the DSL coil.
The incumbent DSL profile for 60 ppm of the MEA phosphonate tested within a brine containing 30 ppm of ferrous iron shows no negative impact on the MEA phosphonate, as was expected. Likewise, in the DSL profile for 30 ppm of the MEA phosphonate and poly aspartic acid (75:25) tested within a brine containing 30 ppm of ferrous iron, there was no negative impact on the blended chemicals performance, as the MIC remained at 30 ppm.
It was apparent that 30 ppm of ferrous iron and potential iron carbonate scale formed within the test brine did not impact the performance of the inhibitors.
Chemical and produced brine compatibility results. Following the DSL testing elements of the evaluation, a final chemical formulation and brine compatibility study was carried out to ensure the formulations generated were compatible with the produced water. Based on the results, it was apparent that the formation of MEA phosphonate and biopolymer (as well as the MEA phosphonate and poly aspartic acid formulation) were fully compatible with the produced water it would encounter during field application. Therefore, there was no risk of pseudo-scale formation across the full concentration range experience as the injection chemical dilutes to its MIC concentration of 30 ppm.
Cost Performance of Synergistic Blends
One of the key benefits of synergistic blends is that they reduce treatment rates by working at a lower concentration than the individual components. With specific synergistic ratios, the potential to reduce product costs can also be achieved.
In the case of phosphonate-functionalized biopolymer, the active scale inhibitor evaluated in this study costs 40% more than the MEA phosphonate, so when the MIC of the single-component formulations were reviewed, there was less cost benefit than the MIC values of the formulation (60 ppm for MEA phosphonate vs. 30 ppm for biopolymer) would suggest.
On a cost performance basis, the reduced treatment rate resulted in a 30% reduction in material cost relative to the MEA phosphonate. The synergistic formulation of MEA and biopolymer (90:10) has an MIC of 30 ppm, therefore it can be inferred that it would be possible to reduce the treatment rate by half, resulting in a 48% reduction in raw material cost (relative to the MEA phosphonate). Even when the more expensive raw material and additional manufacturing costs are included, this still represents a significant saving over the application at 30 ppm biopolymer-based scale inhibitor alone.
In summary, synergistic interaction of scale inhibitors has the potential to reduce chemical treatment rates, logistics of chemical transport, chemical cost, and improve the operational footprint of a scale management program.
Conclusions
The scaling tendency of the brine evaluated had an impact on the MIC required to control sulphate scale formation and the degree of synergy observed between the blended chemicals tested. Based on the data presented in this and previous studies, it is not possible to read across synergistic inhibitor performance results from one brine or operating conditions to another, meaning detailed, field-specific performance testing in the laboratory is recommended.
However, the study did conclude that the performance of currently available, environmentally acceptable scale inhibitor chemicals can be enhanced if synergistic interaction can be identified, and formulations created.
The current regulatory challenges with REACH mean the methods outlined in this study offer the potential to reduce chemical treatment rate, cost, and environmental impact by evaluating the synergistic interaction of the current range of commercially available, environmentally suitable scale inhibitors. When successful, this would eliminate the high registration costs and time delays to the market associated with new molecule development.
In essence, synergistic blends offer the ability to overcome supply chain issues. For instance, rather than source scarce raw materials for phosphonate, phosphonate-based chemicals can be made to work at lower treatment rates by combining them with specific phosphorus-free polymeric scale inhibitors.
For Further Reading
SPE 80229 Barium Sulphate Inhibition in Subsea Systems—The Impact of Cold Seabed Temperatures on the Performance of Generically Different Scale Inhibitor Species by N. Laing and G.M. Graham.
SPE 179889 Impact of Reservoir Temperature on Scale Inhibitor Retention—The Challenge of Ultra-Low Temperature Sandstone Reservoirs by M.M. Jordan, C.J. Johnston, and L. Sutherland.
SPE 204365 Online Cleaning of Carbonate Deposits: The Potential and Limitations of a Novel Cleaning Method by M.M. Jordan, L. Sutherland, and C.J. Johnston. Johnson, T., Roggelin, C., Simpson, C., and Stalker. R.
Phosphonate-Based Scale Inhibitors for High‑Iron and High-Salinity Environments. Presented at Chemistry in the Oil Industry, IX Manchester Conf. Centre, 31 October–2 November 2005.
Graham, G.M., Stalker, R., Williams, H. L., and Littlehales, I.J. The Impact of Dissolved Iron on the Performance of Scale Inhibitors Under Carbonate Scaling Conditions, Paper 17, NIF 14th International Oilfield Chemistry Symposium, Geilo, Norway, 23–26 March 2003.
SPE 80254 The Impact of Dissolver Iron on the Performance of Scale Inhibitors Under Carbonate Scaling Conditions by G.M. Graham, R. Stalker, and R. McIntosh.
NACE 00114 The Performance of Barium Sulphate Inhibitors in Iron-Containing Waters in Both Aerated and Anaerobic Systems by L.S. Stoppelenburg and M.D. Yuan.
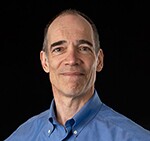
Myles M. Jordan, SPE, is the director of marketing at ChampionX. Since joining the company in 1997, he has been responsible for the development of topside/downhole inorganic scale control programs within the Americas, North Sea, Middle East, and West Africa. He has authored or coauthored over 185 papers on deployment challenges with oilfield scale inhibitors. Jordan holds a BSc in geology and chemistry from the University of Glasgow and a PhD in sedimentary geochemistry from Manchester University.
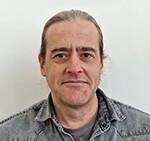
Michael Johnston is a senior chemist with ChampionX with 21 years’ experience in the oil and gas industry. He started his career with Capcis Ltd., where he was seconded to Nalco Ltd. to work with the corrosion team. In 2007 he joined ChampionX and in 2009 transferred to the scale team where he continues in his current role. He holds a BSc in applied chemistry from the Robert Gordon University.