Paraffin and inorganic scale buildups that interfere with flow measurements or clog up production are a fact of life for many oil and gas companies. But they don’t have to be.
That’s one of the big promises touted by specialty chemical company Aculon which is looking to expand its presence in the oil and gas market.
Founded in 2004, the San Diego-based firm offers a line of nanocoatings that are mostly tailored to repel water and oils. And while you may not have heard of Aculon, the realm of chemistry tech it operates in has become so well-established that there’s a good chance you’ve used some version of its technology.
Edward Hughes, CEO of Aculon, highlighted that some of the company’s biggest clients include smartphone and computer makers that use the nanocoating to protect their devices from water damage or to improve aesthetics, e.g., for anti-fingerprinting on laptop shells.
“Our goal is to enable our customers to basically make better products,” said Hughes. “We do this by having a suite of technologies, all related to surface modification, that essentially change the energy of a surface. It could be metal, it could be glass, it could be a polymer.”
How It Works
Surface energy influences what will and will not bond with any given material. Aculon’s antifouling product is designed to lower that energy, which means less oil and water will stick to the treated surface.
A good way to think of this effect is as the opposite of an adhesive, such as what’s used in tape, which is designed with a high surface energy.
Hughes said Aculon’s process of modifying surface energy is a fairly straightforward process that takes place in a matter of minutes. With a trained operator, he said, “It can be dipped, it can be wiped, and it can be sprayed onto the various applications.”
Once applied, the nanocoating is just a few molecules thick which makes it invisible to the human eye but plenty thick enough to prevent water or oil from ever physically touching the material underneath.
As Aculon makes a renewed push into the oil and gas sector, Hughes added that the company is looking beyond antifouling to see if its chemistries can be used downhole for production enhancement.
All of this is to say that Aculon is not new to the oil and gas industry. It has been quietly building its track record in upstream for more than a decade and earlier this year expanded its oil and gas team to take advantage of recent successes.
1,000 Treatments and No Reports of Fouling
Aculon’s most popular product in the oil field today is an omniphobic nanocoating that’s used for antifouling applications.
It's marketed by Aculon’s US distribution partner, KopMan Industries, which developed a proprietary approach to apply the nanocoating. The Corpus Christi, Texas-based service firm has performed antifouling treatments on more than 1,000 meters and other pieces of oilfield equipment for about 20 operators over the past 6 years.
Of all that hardware, KopMan reports that none have failed as a result of fouling. This includes the first instruments that the company treated with the antifouling chemistry in 2018.
That work, performed for an undisclosed oil and gas producer in the Eagle Ford Shale in south Texas, involved multiple Coriolis flowmeters. The meters represent a critical component of Lease Automatic Custody Transfer (LACT) units, which are used across US onshore to measure and allocate oil volumes before they reach midstream transportation networks.
The LACT units in the pilot had a combined capacity of 80,000 BOPD that had been suffering from paraffin buildups—a common symptom experienced across the play due to the nature of the Eagle Ford’s especially light grade of crude.
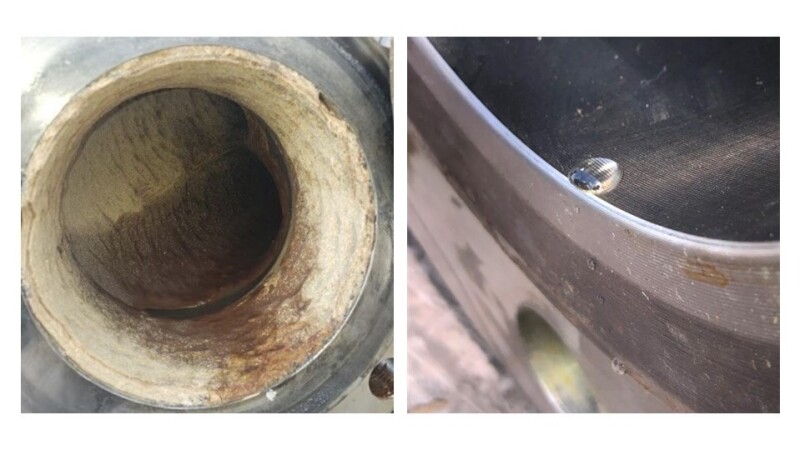
Clay Wernli, founder and CEO of KopMan, described the oil flowing through the LACT units as “a relatively clean product, but it was still carrying that paraffin molecule and when it started to cool down, it dehydrated inside of the meter and created an eggshell.”
Another factor promoting buildups inside these units is that they sat at the point of custody transfer which means the crude flowing through them had already been through separator and stabilizer systems. With stabilized crude, the light ends of the hydrocarbon chain are removed, which leaves the oil with a much reduced capacity to keep paraffin in solution, and thus, making it more likely that it will precipitate out and form deposits.
As the waxy accumulation forms into that “eggshell” Wernli referenced, it forced the LACT units to be routinely taken out of service every few weeks for cleaning.
That was to deal with the bigger problem, which Wernli shared is that the buildups throw off crude measurements—an issue called "drift." In the pilot case, this meant the operator would sometimes flow 80,000 BOPD but only record from its metering units a combined total of 77,000 BOPD.
But since being treated with the Aculon-developed nanocoating almost 5 years ago, KopMan claims that the meters have not required a single cleaning and that those measurements are reading true as a result. About 18-months following the pilot, Wernli added that the unnamed operator ordered the surface-altering treatments for the rest of its Coriolis meters in its Eagle Ford asset. (In addition to addressing paraffin, the nanocoating product repels inorganic scales.)
Wernli emphasized that the 2018 pilot proved not only that the nanocoating works—and on a long-term basis—but that the old approach of dealing with paraffin buildups represents a costly way to deal with the symptoms, not the root cause of the problem.
“We were always mitigating the flow stream instead of mitigating the actual surface property,” said Wernli, adding that the status quo involves using solvents, dispersants, and other chemistries to keep the paraffins solubilized.
Is EOR Next?
Aculon is in now the middle of a study that may determine whether its technology can be used as an enhanced oil recovery (EOR) agent. The idea is that a nanochemistry will bond with the rock, just like it does to metal and glass, and then change its wettability to promote the mobility of oil vs. water.
To help provide guidance on this effort, Aculon hired Satya Gupta, a former technology fellow with Baker Hughes who has published 75 papers on a range of oilfield chemistry topics including unconventional fracturing fluids.
The company said its EOR chemistries have been tested using corefloods and microfluidics. Hughes at Aculon said this laboratory work has yielded “terrific results” but the company has not yet announced plans for a field trial.
This is a good point to remind that the nanocoating technology developed by Aculon does have its limits. That is perhaps most true for the issue of corrosion.
Hughes emphasized that the nanocoating technology does not work like anticorrosion treatments such as chrome plating.
“We can certainly slow [corrosion] down,” he said, adding, “We like to say we’re as good as the underlying substrate.”
In other words, the nanocoating might not prevent corrosion if it is applied to a surface material that's not stable, or is contaminated or has some flaw that allows for water ingress.