ConocoPhillips knocked out paraffin problems plaguing its Eagle Ford wells by using gas composition data to identify where paraffins are likely to form.
Paraffins had long been a problem in the area for the operator, and in 2010, ConocoPhillips decided to build facilities at each well that were independent from a fluid separation and processing standpoint. The company also instrumented the facilities beyond industry standards.
Those decisions helped facilitate the operator’s discovery that gas composition could correlate to paraffin production, according to SPE 220746, presented at SPE’s Annual Technical Conference and Exhibition (ATCE) in New Orleans.
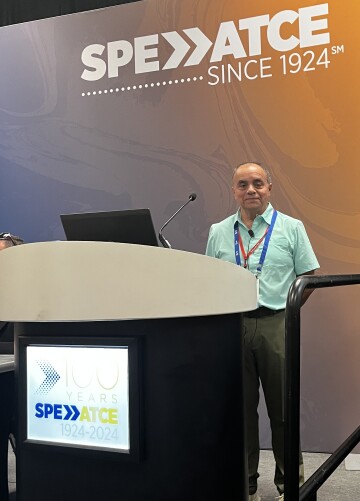
Jesus Contreras, an Eagle Ford production engineer for ConocoPhillips, said during ATCE that the company had tried a number of the traditional methods–including chemical inhibitors and pigging–to combat the paraffins, which were causing significant production losses.
Starting in 2016, ConocoPhillips created a graphical model tracking connections between assets and developed a fieldwide plan for chemical injection at the well-pad level to mitigate potential plugs throughout the gathering system. Contreras said the systems-based approach provided learnings but failed to solve the larger problem.
In 2020, the team shifted its focus and created a pigging algorithm, which was essentially a hydraulic model that could answer whether a pig could be launched, determine its travel time between two points, and indicate where it would end up. According to the paper, the objective was to prevent losing pigs in the pipelines due to the complexity of the gathering system.
But, Contreras said, the problem was more basic.
“The problem is not a hydraulic system. The problem is not a pipeline. The problem is the wells,” which were producing the paraffins. So, let's try to find ‘Who are the bad guys? Where are they located? And what can you do to try to solve the problem?’”
The operator compared flowline pressure and low-pressure separator pressure and determined that in wells producing paraffin, diverging flowline pressure indicated paraffin buildup (Fig. 1), according to the paper coauthored by Contreras, Javier Vasquez, Trey Harton, and Prapul Garikipati.
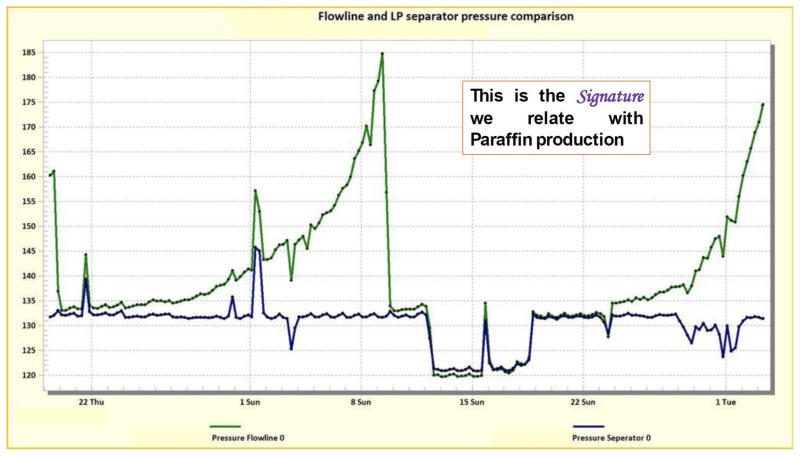
The team studying the problem validated the paraffin production signature over the course of 3 months, testing more than 50 wells. The signature was 98% effective at identifying paraffin-related problems.
The team also identified where paraffin blockages were located on the surface at the pad site (Fig. 2).
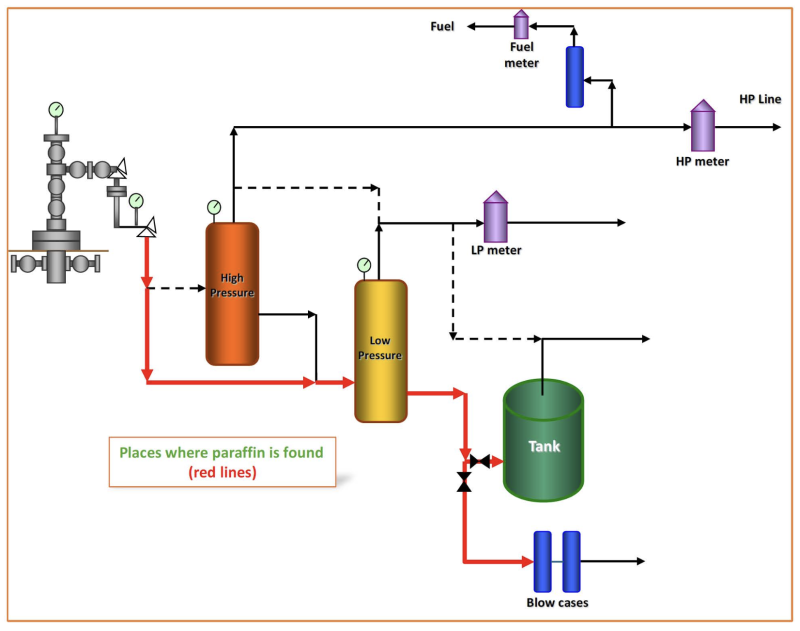
The method was effective at identifying paraffin in “relatively depleted wells with low temperatures—conditions that allow paraffin to precipitate as a solid,” the paper stated.
That left the problem of detecting paraffins in situations with higher temperatures and flow rates which kept the paraffins in suspension.
Contreras said that in 2020, an unrelated project delivered a means to solve that problem. Over the course of a decade, ConocoPhillips collected 65,000 Eagle Ford gas samples for royalty purposes, which prompted the production engineering team to consider correlating paraffin production with the gas composition of the wells, according to the paper.
“People forget the Eagle Ford is a gas condensate reservoir,” Contreras said.
Correlating the paraffin production and gas composition proved to be “an amazing breakthrough,” he added.
The team trained a machine-learning algorithm on paraffin-producing wells with known gas composition alongside wells without paraffin issues but with known gas composition. The team also cleaned up the data by excluding wells that used artificial lift, ensuring that lifting gas did not interfere with the analysis.
According to the paper, the resulting model generated a per-well probability that established the well’s likelihood of producing paraffin, independent of temperature or flow rate. Contreras called it the “paraffin risk index” and said more than 1,900 wells in the Eagle Ford have been categorized based on their risk of producing paraffins, with classifications of high, medium, or low risk.
For the first time, ConocoPhillips had a comprehensive understanding of which wells were likely to produce paraffin based on gas composition, but the company still had to work to do: it had to create operational processes that would “optimize manpower, reduce chemical consumption, and systematically address paraffin plugs in the gathering system,” the paper stated.
ConocoPhillips’ team linked the paraffin risk index results back to the hydraulic model and visualized the information in a model of the gathering system (Fig. 3), which the paper said allowed the operator to “treat the probability of paraffin production as if it were a regular concentration of an impurity within the system.”
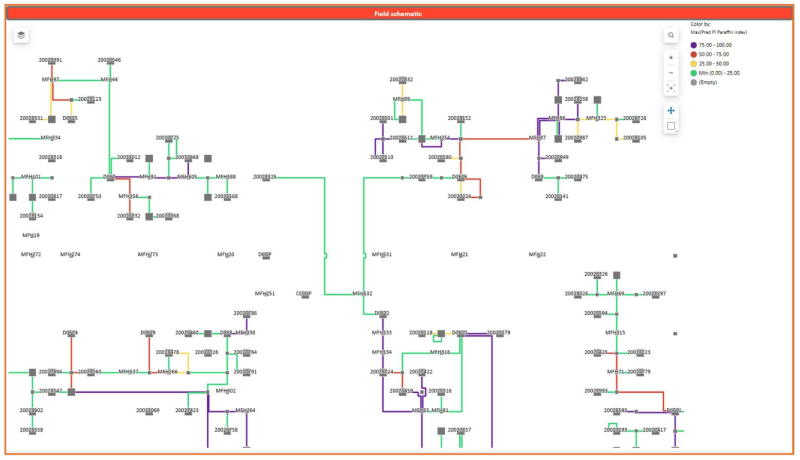
By combining surface cleanouts and machine learning, ConocoPhillips said it was able to reduce pigging operations by 25% and decrease operational losses in the Eagle Ford. The operator said the result is equivalent to the cumulative life cycle of one Eagle Ford well per year. Further, the company said its Eagle Ford gathering system has been free of paraffin plugs since 2019.
For Further Reading
SPE 220746 Paraffin Production in Eagle Ford: Learning, Applying, and Executing Out-of-Box Strategies for Living With This Challenging Issue by J.D. Contreras, J.R. Vasquez, T.W. Harton, and P. Garikipati, ConocoPhillips.