With the world experiencing an ever-increasing demand for energy, all commercial sources are needed to support the energy “grid.” These include cogeneration of electricity by manufacturing plants, geothermal, hydroelectric, nuclear, coal, oil, gas, wind, and solar. Each of these sources has both benefits and issues. As renewable energy sources, particularly wind and solar, gain momentum, the hope is that these technologies will one day have the capacity and efficiency to meet ever-increasing demand for power. Until then, however, fossil fuels will remain the dominant source of world energy supply, to 2050 and beyond. But to supply the energy needed, oil and gas producers must improve safety, efficiency, and affordability. For example, North American oil and gas, coupled with continuous recovery innovation, may be plentiful enough to meet future regional demand until renewable energy can close the gap and dominates the market.
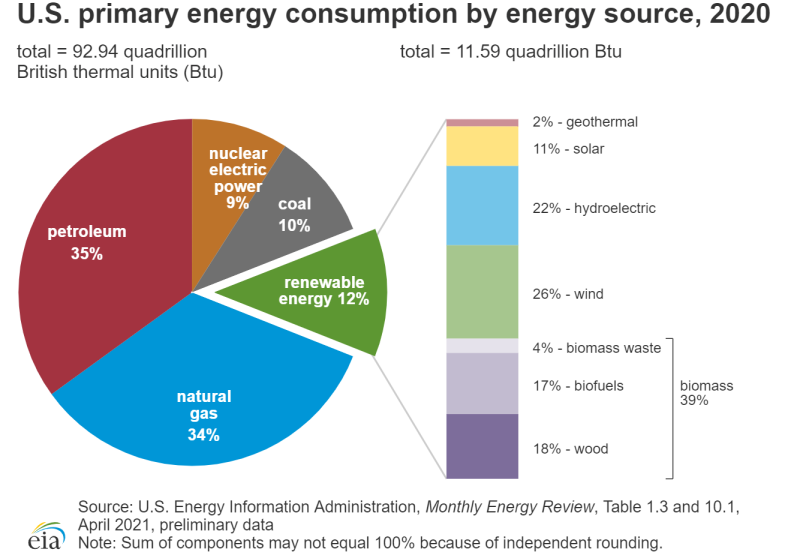
Over the past decade, the improved recovery of fossil fuels from shale reservoirs has been astonishing. Horizontal drilling and multi-stage fracturing technologies have enabled producers to connect to and recover more of the available resource. This has led to the US becoming one of the top oil-producing countries in the world after years of declining production.
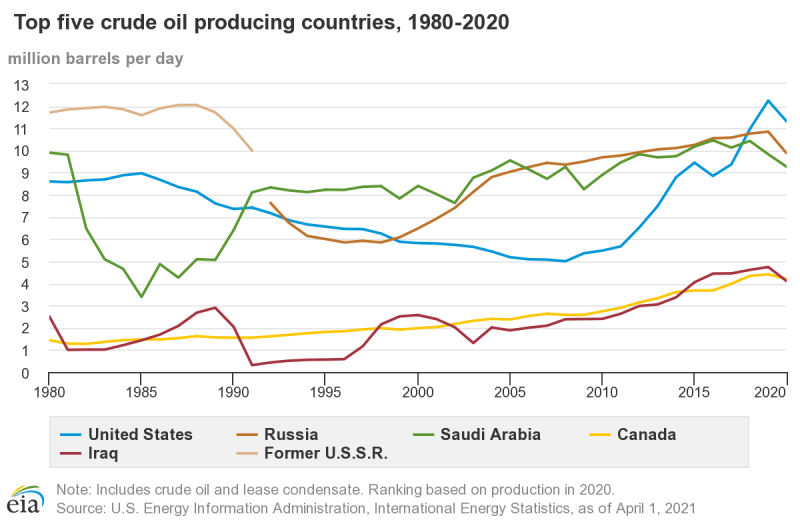
In a short period of time, Innospec Oilfield Services, (IOS) has witnessed first-hand the industry shift in fracturing fluid chemistries from viscous guar-based or surfactant-based gels to hybrid fracs to slickwater fluids. The shift occurred as operators discovered how to carry more proppant to the fracture with slickwater treatments which also reduced costs and lessened fracture damage caused by the earlier fluid systems. More recently, the frac trend has gone towards even more water, sand, pumps, treating rate, longer laterals, shorter well spacings, and fewer chemicals.
This evolution created opportunities for companies like IOS to develop innovative chemical designs. One early example of this innovation was IOS’s revolutionary VisLink™ Oil-Based Crosslinker, a crosslinker for ultra-low loadings of guar. Following this, was IOS’s introduction to its HiRate™ D60 Dry-on-the-Fly Friction Reducer with Big FRed™ Dry Blender. Following our mind-set that chemistry can accomplish the customer’s goals more simply, IOS developed two new chemical innovations: HiRate™ Plus emulsion powder suspension and HiRate™ MAXX 3200G powder suspension friction reducers. Both systems have proven instrumental in the fracturing fluid evolution.
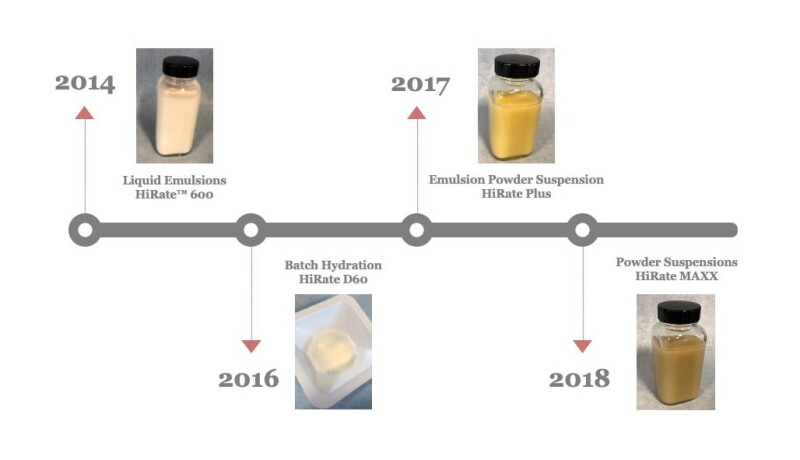
Within the US shale basins there is still ample room to further improve operational efficiencies by maintaining a continuous focus on innovative chemistry. Producing more oil and gas at comparable costs is a viable goal. Success requires a change in conventional thinking to focus on reducing the cost of each barrel of treating fluid. A novel, and uniquely developed friction reducer was utilized to improve proppant placement and distribution in the fracture network, while maintaining the cost per barrel treated. To that end, IOS’s patented HiRate Plus series, a blend of powdered friction reducer (FR) and emulsion FR, was developed.
When mixed, these two FRs provides a synergistic response to friction reduction, more than either FR pumped separately. The enhanced performance is due, in part, to the bi-modal distribution of particle sizes. This distribution causes rapid hydration from the smaller polymer particles in the product whereas the larger-sized particles suspended in the HiRate Plus series hydrate slower, offering a continuous release-like behavior while transiting through the wellbore. This combination is especially beneficial for extended reach laterals.
As an added benefit, blending these two FR’s, polymer emulsion and powder, naturally increases polymer activity, for better treating efficiency. It is intuitive that mixing these two FR’s can cause long-term stability issues with the product, and in fact this approach is not recommended by most other polymer manufactures. However, IOS’s technology team, convinced of the enhanced benefits of the mixed product, overcame the stability issue, providing customers with both high performing product and long-term product stability. Once the stability issue was resolved, each subsequent new generation of the HiRate Plus series has steadily improved friction reduction performance, offering affordable treatments in a broad spectrum of well and reservoir conditions.
HiRate™ MAXX 3200G was developed because many of Innospec’s clients in the Woodford/Cana, Delaware, and Eagle Ford basins had struggled for years with a rubbery-like substance. This substance would adhere to surface treating equipment and cause lost production. As a chemical company and a solutions provider, IOS’s R&T group, with their knowledge and experience of FR chemistry, wanted not only to prevent the formation of this substance, but to fundamentally understand the cause of the issue. Many companies have worked on a solution, but a long- term resolution was difficult to find. After surmounting some major scientific obstacles, IOS was able to introduce the HiRate™ MAXX 3200G friction reducer to minimize this challenge.
Improving Sustainability
As the call for renewable resources grows louder, IOS is committed to producing new chemistries—based on sustainable raw materials whenever reasonable and possible. IOS product formulations now include chemistries that assure better protection of the environment. Smarter formulations also benefit the health and safety of company employees and others who could potentially be impacted by our products. These include contractors, customers, and local communities—making company responsibility a key part of IOS’ culture.
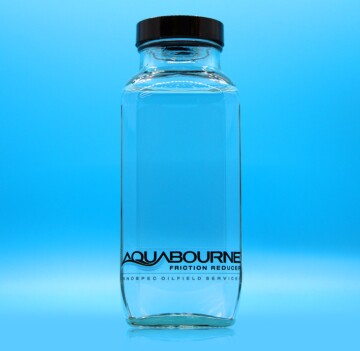
In Q4 2021, field trials confirmed that AquaBourne even exceeded pre-hydrated or batch mixed dry FR performance without additional personnel or complicated equipment on location. Until this field trial, the dry FR, with its associated equipment and personnel as all-in costs, was the industry “gold standard” in low-cost slickwater treatments. This field trial confirmed that a lower cost option to the dry FR is both technically and commercially viable. As a liquid FR, AquaBourne simplifies FR delivery with less chance of lost-time incidents occurring on location. AquaBourne pumps like a conventional liquid FR but offers dry-powder performance. In a stage versus stage field trial against a regional competitor, AquaBourne was able to lower treating pressure while keeping frac rate stable at lower FR concentrations. The graph below is a snapshot from the actual treating plot.
Furthering our sustainable product offerings, IOS recently released its’ patent pending AquaBourne™ series of friction reducers, which focuses on affordable performance as a friction reducer, less formation and proppant pack damage, and reduced environmental impact. Unlike its predecessors, this latest innovation is the industry’s first oil-free liquid suspension, high-efficiency friction reducer. AquaBourne is based on a sustainable water-based carrier fluid, effectively eliminating the need for mineral oils or surfactants. With its’ water-based composition, AquaBourne possesses a 61% reduced carbon footprint resulting in a more favorable FracFocus disclosure for companies directed to demonstrate their ESG awareness and progress.
Although a water-based FR product seems counter-intuitive with, at best, a short shelf-life, the AquaBourne carrier fluid has proven that it can deliver. AquaBourne was designed to prevent polymer hydration while in inventory. Moreover, the polymer slurry remains stable for long periods of time, even at elevated temperatures encountered in some of the most extreme conditions around the world where oil and gas are produced. Rapid polymer hydration only occurs when the carrier fluid is diluted in the frac water.
AquaBourne was developed to have excellent dispersion in water–regardless of water quality–and rapid hydration and yield in fresh- to heavy-brine frac waters. These products have shown better utilization of the polymer than oil-based products, so every polymer strand in the product contributes to friction reduction and the fracturing process. The active polymer does not need to shed an oil coating prior to hydration, so more polymer is transferred to the water phase to enhance product performance. Lastly, the AquaBourne series can be customized to meet any formulation and/or manufacturing modifications needed to satisfy operator objectives.
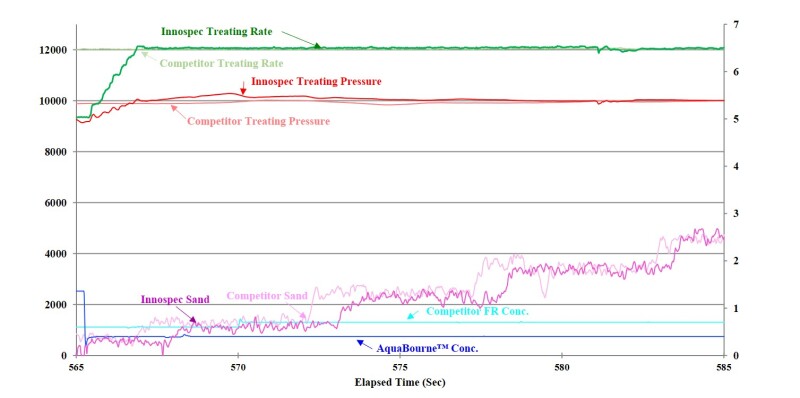
In the oilfield, improving ESG scores often means compromising performance and/or increasing cost. IOS believes AquaBourne FR enables companies to demonstrate a better ESG commitment while also improving efficiency by shortening stage pump times and lowering the cost of treatment. AquaBourne can provide a positive for your bottom line.
Unlike chemical distributors, IOS also supports its chemistries with well-site application specialists. IOS operational team members have many years of experience with various pressure pumping companies and they provide an excellent balance between understanding the chemistry’s uniqueness and the best mode of application. Fully understanding the customer’s objectives, IOS well-site professionals engage with pumping company personnel to recommend best practices needed to plumb the products into the frac equipment. Their job is to assure the product pumps correctly and, when things don’t go as planned, quickly troubleshoot the situation, and resolve the issue. Their presence is designed to prevent chemical-related lost time incidents and provide product QA/QC on location to be sure the products meet customer expectations.
At its core, IOS is chemistry driven. As leaders in surface active and polymer chemistries, IOS finds the right chemical solution to a customer’s challenge, independent of the degree of difficulty or complexity. That’s because only IOS possesses the unique ability to start at the molecular level— which allows the building of viable solutions from thought to commercialization. It is the kind of responsible innovation that will evolve alongside our energy partners as the industry continues to meet the world’s ever-increasing energy demands while embracing ESG initiatives.
For more information about Innospec Oilfield Services Friction Reducer portfolio, go to www.Innospec.com or you can email us at OilfieldAmericas@InnospecInc.com
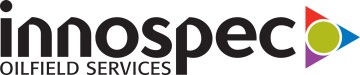