Energy is the number one cost of producing oil. Batteries offer new capabilities for reducing those costs and are one of the rare cases where we can improve both efficiency and capability. But what is critical for ensuring those benefits is the correct implementation and utilization of the technology.
Batteries provide the greatest ROI when they are used directly alongside a primary power source—whether that is a diesel generator, gas engine, solar panel, utility-scale power plant, etc. Clearly a battery requires some method of charging, but the notion that a ‘hybrid’ approach likely makes the most sense is increasingly commonplace.
However, it is easy to build a bad hybrid. Simply adding a battery onto an existing power system can result in a large capital expense with near zero benefit. Or the implementation of a battery could increase capability, reliability, and efficiency. Ensuring the latter of those two outcomes requires understanding three critical elements: the battery itself, the overall objectives, and the operational profile.
What To Understand About the Battery
Unsurprisingly, it is beneficial to increase one’s familiarity with the battery itself. The important thing to understand is that, from the standpoint of system level performance, batteries are fraught with tradeoffs. Of all the performance qualities of a battery—power, energy, weight, volume, cost, cycle life, safety—there is rarely any benefit to be gained in one aspect without sacrifice in at least one other.
This is why it is important to match the needs of the application to a battery with the corresponding capabilities. On top of that, factors such as quality, thermal management, and the Battery Management System (BMS) will determine the ability of the system to deliver the performance that is promised on the spec sheet in the real world.
Some of the most fundamental factors that must be considered in initial battery technology selection are power, energy, cycle life, and cost. Power and energy are intertwined and drive some of the most basic capabilities. They are also in direct tradeoff with each other—an increase in energy density almost always comes with a decrease in power density and vice versa.
Assessing battery lifetime is complex, and battery technologies are available today that can easily perform tens of thousands of cycles, while many are rated for less than 1,000 cycles. Ultimately, lifetime will be determined by how the battery is operated in the field.
The fact that cost is another critical factor certainly comes as no surprise. However, what is critical is not to be overly focused on cost, particularly in terms of $/kWh. Cost should be evaluated in terms of total cost of ownership over the lifetime.
Understanding the Real Objective for Battery Implementation
Batteries yield the best ROI when operating alongside a primary power source. In these cases, the role of the battery is to help that power-generating component do what it does best. Many industrial and oil and gas applications rely on diesel gensets, which can be very efficient. However, these gensets are often operated outside of their optimal range, which greatly compromises system efficiency.
For successful battery hybrid system implementation, the entire objective is to simply, but explicitly, avoid any inefficient loading of the genset. When the genset is running, it should always be at or near peak efficiency. This is how to achieve attractive ROI figures from battery technologies.
This familiar story is illustrated in Fig. 1 which shows the relationship between load percentage and fuel consumption rate for a representative diesel genset. Operating this genset at 20% load, compared to its peak at 80% load, for instance, results in 27% worse fuel consumption. Inefficiency gets exponentially worse as load percentage further decreases—operations that are far more common than most people are aware.
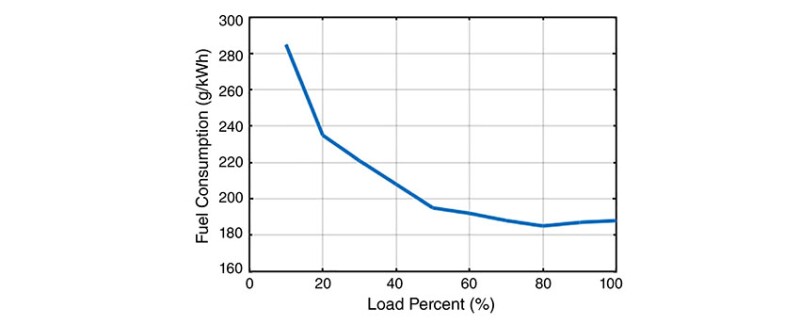
Most people are familiar with the combustion engine fuel curve and that being the basis for the general concept of a hybrid. However, the key is that for the wide range of different industrial applications of gensets, each brings a different operation and different reasons for why the genset may be loaded so inefficiently—and thus each calls for a different approach for how we should employ the battery and what kind of battery to use.
For a genset on land, it may be oversized and low loaded because it needs power capacity available for peaks or intermittent loads. For an offshore vessel, we have more generators online than necessary due to imperative redundancy and blackout prevention requirements. Insight into how to evaluate these differences and design a system to address them comes from analysis of the operational profile.
Bringing It All Together: Operational Profile
Fig. 2 shows two different load profiles that would dictate different approaches to hybrid power system design.
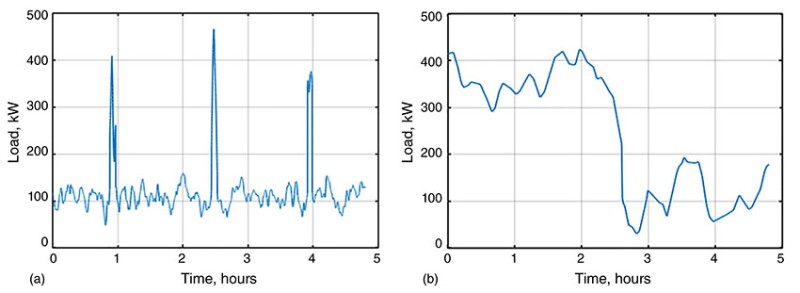
Profile A in Fig. 2 would typically call for a 500‑kW (+) genset and it would be running at an average of 100 kW, netting 20% average load and thus 27% more fuel wasted than necessary (using values from Fig. 1). However, if it were an option to use a 200-kW genset with a small, high-power battery for peak loads, that genset would average 50% load and result in only approximately 5% wasted fuel—cutting 22% out of what is often the biggest line item in the operational expense budget.
It is also important to note that the financial savings from reduction in maintenance are typically of the same magnitude as the fuel consumption savings. And additionally, if the load was fairly constant around 400 kW on a 500-kW generator, the system is already operating highly efficiently, and it is not worth considering a hybrid or battery solution.
Profile B in Fig. 2 also represents a variable load profile but is distinctly different. Two options could be considered: one where the battery would take the larger loads or one where the battery would take the smaller loads. In either case the objective would be for the genset to be operated at or near its peak efficiency any time it is on.
In evaluation of profile B, if we employed the same thinking as profile A—using a 200-kW genset and a battery supplying around 370 kW avg—given approximately 2.5 hours of operation, this would result in a sizeable battery of 925 kWh. Conversely, if the lower power operation was supplied by battery, averaging 100 kW for 2.5 hours, this would necessitate a larger genset, but only a 250‑kWh battery.
Either configuration addresses the objective of ensuring the genset always runs at maximum efficiency. And either of these approaches could potentially be the most desirable; at that point the design decision would depend on the rest of the operations and other external factors and cost implications. These examples illustrate why the specifics of load profile and operations drive so much of the hybrid or battery system configuration decision making.
Previously we referenced the range of genset use cases—from on-site power on land to offshore operations at sea, with many cases in between. Even within each particular use case, the load profile can be as different as those shown in Fig. 2. Yet, detailed load profile data is rarely available. In many cases high-level summary data, such as time spent in different modes of operation, might be available. These different tools give different levels of insight and answers, as we ask the same important questions: How often is it high-loaded? What kind of loading do we spend most of our time at? Is fuel efficiency the primary factor—what about all-electric operations, or blackout prevention or spinning reserve functionalities?
How To Tackle These Challenges
The mindset and toolset for working through these issues is exactly as described in the JPT article, “Engineer of the Future.” Using new tools to solve old problems—the battery is a tool in a toolkit, it gives us a new lens to think about how to solve those same challenges. Last but not least, high-quality data is paramount. The more informed the design team is and the more aspects of operation and functionality that can be accurately considered, the better the end result will be.
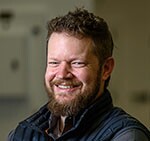
Ben Gully, chief technologist of SPOC Grid Inverter Technologies, is a subject matter expert in lithium-ion battery systems. He has been working with lithium-ion batteries in maritime, stationary, automotive, and various industrial applications for over 15 years including research of lifetime and safety, system design and product development, and development of advanced chemistries. He holds a PhD in dynamic systems and controls from The University of Texas at Austin.