We believe that neither physics nor machine learning alone can compete against a unified hybrid approach. Integrating physics and machine learning combines the best of the two worlds, resulting in higher accuracy, better scalability, and cost efficiency. In short, hybrid models will be invaluable in the future of modeling in the industry.
Flow simulations facilitate production optimization by monitoring and planning the flow of oil and gas in wells and pipelines. Production optimization in the oil and gas industry can focus on a wide range of objectives such as maximizing production outputs; cost-effective operations; and, more recently, carbon-effective production targets. Regardless of the core objective, flow simulations can help address production efficiencies and achieve targets.
Real-time access to multiphase flow rates from all wells and pipelines is of critical importance for effective production optimization. This information provides operators situational awareness and allows them to react immediately. More importantly, they can proactively optimize operations and avoid deferred, or even lost, production. A trial-and-error approach to production optimization is not an option.
Virtual flow metering (VFM) can deliver real-time well rates for effective production optimization. For the best possible outcome, it is essential to address the full operating envelope throughout the life of an asset. To deliver the most accurate real-time well rates, we have developed a self-adjusting, hybrid virtual flow meter that combines state-of-the-art physics-based and machine-learning approaches (Fig. 1).
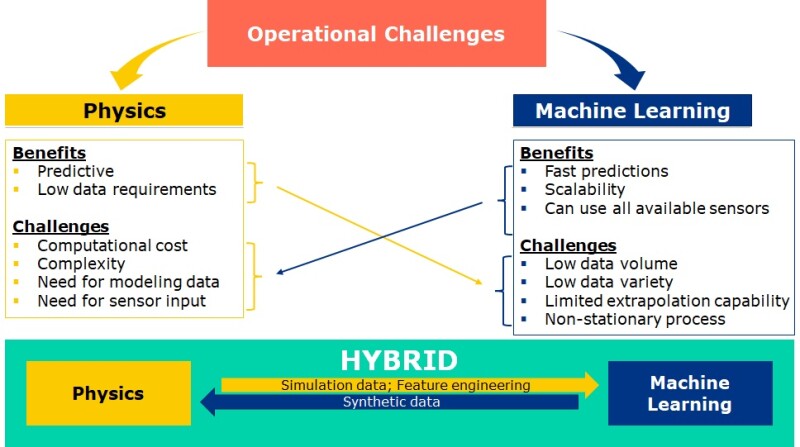
Physics-Based vs. Machine-Learning VFMs
A physics-based approach to virtual flow metering relies on multiphase flow simulations. Physics-based modeling builds on well-understood concepts in, for example, thermodynamics, fluid dynamics, fluid modeling, and optimization techniques. If the physics model is accurate, this approach is often a good solution. Yet, it requires deep domain knowledge and may incur significant computational cost.
Machine learning solutions are based on learning algorithms that uncover the relationship between sensor data and target variables in a historical dataset. The machine-learning approach does not require deep knowledge about physics, but rather a good understanding of the learning algorithms and statistics. Yet, limited data sets or changes in operational conditions limit general applicability of this approach.
Use Machine Learning To Improve Physics-Based Modeling
Machine-learning methods are designed to exploit large data sets, reduce complexity, and find new features in data.
One way to use machine-learning models is to generate synthetic data for the physics-based models. Where physics-based simulations only consume sensor data directly related to the simulation model, machine learning can incorporate any sensors. By that, machine-learning models can provide synthetic data and improve the robustness and accuracy of physics-based models.
Another means to use machine learning is to create proxy models that mimic physics-based models. Here, machine-learning algorithms are applied to real-life data as well as data generated by physics-based simulators to train machine-learning models that are faster and easier to deploy at scale.
Incorporate Physics Into Machine Learning
The common approach to incorporate physics into machine learning is feature engineering. In feature engineering, several measurements are combined to create physically meaningful features rather than using individual measurements directly. This approach, of course, requires both domain and machine-learning knowledge.
Feature engineering can be refined even further if measurements are combined with simple physics models that incorporate static data such as fluid properties, geometry data, and information about equipment. These high-level features will not only improve the accuracy of the machine-learning model but also make it more transparent and comprehensible.
Turbulent Flux’s Hybrid Modeling Philosophy
At Turbulent Flux, we believe that physics-based modeling and machine learning are complementary rather than competing modeling strategies. We use machine-learning models to improve one or more components of a physics-based model. One example of this philosophy, where machine-learning models incorporating high-level feature engineering augment physics-based simulations, is the FLUX VFM (Fig. 2). This approach has repeatedly proven capable of average full-scale errors below 5% for all phase flow rates.
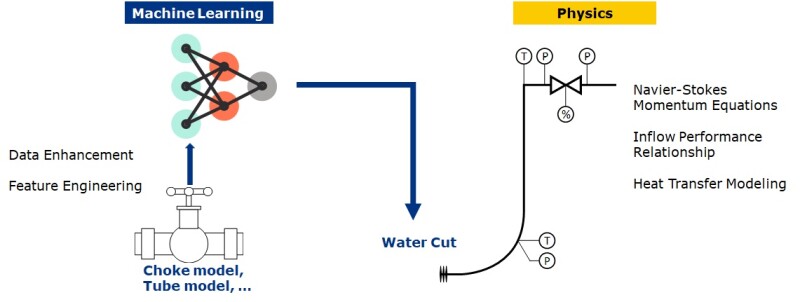
A concrete example is a case study where the hybrid FLUX VFM delivers real-time well rates for gas, oil, and water for all wells in a mature oil field. A pure physics-based solution can deliver very accurate estimates for the gas and total liquid flow rates. In addition, machine-learning models incorporating high-level feature engineering accurately predict the oil/water ratio. The best possible accuracy for the three-phase well rates is attained when physics-based simulations are combined with the machine-learning models. The answer, a hybrid model orchestrated in a unified solution that accurately predicts all three phases independent of constantly changing operating conditions (Fig. 3).
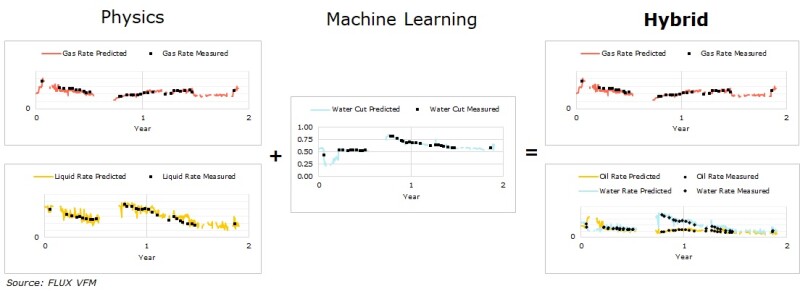