The nanotechnologies enjoying commercial success in the oil field today are small in number, and for the most part, can be categorized as single-well applications. Examples include the dissolvable ball-drop systems used in horizontal well completions and the specialty additives operators are using to enhance drilling fluids.
The next big leap for this area of emerging technology will be the development of nanoparticles that work on larger scales, either in production operations or for fluid treatment.
Counted among the industry’s nano-pioneers, Saudi Aramco is getting closer to the deployment of nanoparticles for a number of reservoir-wide applications. Others are working on creating nanoparticles that will improve the performance of waterflooding, and university researchers in Texas are developing a magnetic nanoparticle that aims to make offshore water treatment more efficient, and possibly more economic.
These concepts were presented at SPE’s Annual Technology Conference and Exhibition held last year in Dubai. Taken together, they offer a small, yet compelling, sample of the ideas still working their way through the pipeline.
Kirk Rainey, the vice president of A&I Ventures in Houston and a former chemical-enhanced oil recovery expert at Shell, has been involved with nanotechnology consortiums for more than 7 years. Speaking generally, he explained that the oil and gas industry is interested in nanoparticles partly because of the potential efficiencies they offer. It helps to think of nanoparticles from a chemical perspective; their collectively high-surface-area—typically where chemical reactions take place—means even relatively small volumes can make a big impact.
“The negatives include the fact that in many cases engineering these nanoparticles, or nanostructures, can be very costly,” said Rainey. “And while it may be easy to do on a small scale, learning how to scale something up to the oil field is going to take a lot of effort, and the ability to do that is sometimes unknown.”
That point about scale is very important, especially when discussing reservoir applications. Rainey emphasized that if large doses of nanoparticles are needed, then their cost must be relatively low to justify their use. He said the ability to strike such a balance will separate “laboratory curiosities” from viable commercial products.
The following projects highlighted at ATCE address some of these challenges and other industry concerns that include whether nanoparticles will remain stable under reservoir conditions, precipitate out of the fluids they are infused into, or simply do what they were designed for.
Nano Tracer Test a Success
Saudi Aramco’s continued research efforts have resulted in what the national oil company is reporting as the first successful inter-well field test of fluorescent nanoparticle tracers (SPE 181551). The long-range experiment is one of the latest examples of the company’s efforts to “illuminate” reservoir behavior with nanoparticles and help it maximize recoveries. Though the test began in mid-2014, detectable amounts of the original 300-kg batch of nanoparticles were still being recovered from a producer well throughout last year.
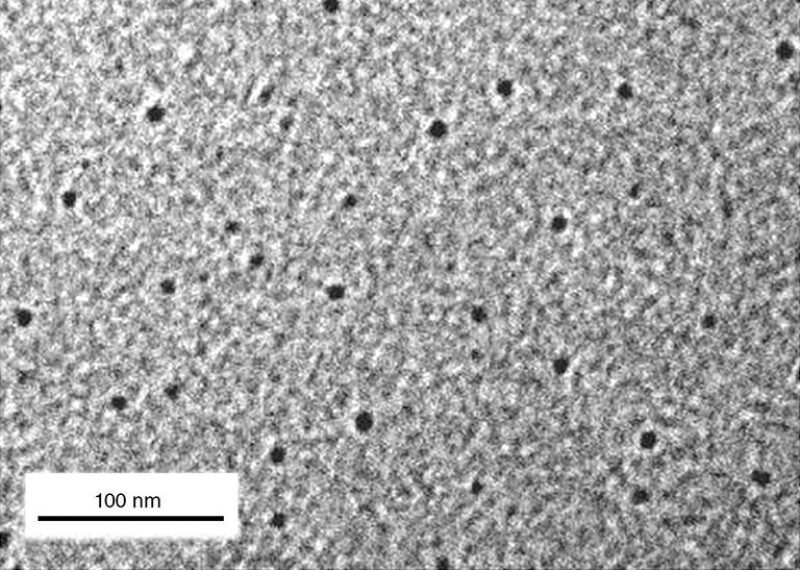
“Ten years ago, trying to suggest that maybe nanoparticles could be used in the reservoir was a completely mad idea and everyone laughed,” said Erika Ellis, a physicist at Saudi Aramco who works on the company’s nanoparticle projects. “But now we’ve pushed nanoparticles as a tracer material through a reservoir and have successful results—and this is the first time that it’s ever been done.”
The test built upon years of research and development of the company’s own brand of carbogenic nanoparticles called Arab-dots, or simply A-dots. They are named for the Arab D formation, a major carbonate reservoir in the supergiant Ghawar oil field. Contained within the A-dots are even smaller bits of fluorescent material that are easily detectable using an instrument called a fluorometer.
And though it was planned to be executed using an injector and a producer well with a reservoir distance of between 150–200 m, the test was carried out in wells with a respective distance of 475 m. Instead of jeopardizing the test, the increased distance only underscored the reservoir-transit capabilities of the A-dots.
Another unplanned factor involved a number of injector well shutdowns, which also ended up being a good thing because it proved that the A-dots moved right along with the erratic water front. The strong correlation also allowed the research team to figure out that it takes 10 months for the A-dots to move from the injector to the producer—a parameter that will help measure their performance in the future.
According to Ellis, the project has given Saudi Aramco data that suggest its nanoparticle tracer may be more effective than the commercial chemical tracers it uses. One of the problems with chemical tracers is that they are prone to spread out in a wide scope, sometimes missing the flow stream of a producer well, she said.
This may happen because the molecules of chemical tracers are in fact smaller than some nanoparticles, including A-dots, which measure about 10 nm in circumference, or about 1/1000th the width of a human hair.
The result is that the chemical tracers will follow many pathways, some that flow with the oil and water and some that do not. Ellis said the data show that the larger A-dot particles move in a much more direct line toward the producer, which is why the responses of produced fluids and the nanoparticles were so similar during and after the injector shutdowns.
The other big benefit of using A-dots as a tracer is that at USD 3 per/kg, they will be highly competitive with other tracer technologies once the company begins manufacturing them at an industrial scale. Their low cost comes thanks to the simple bucket reaction used to make them, which involves mixing citric acid and ethanol, plus heat.
One of the mysteries of the A-dots is that Saudi Aramco’s researchers say they do not know why they are so resilient to the challenges that other nanoparticles are more susceptible to such as flocculation (clumping), precipitation out of hot brine, and absorption to carbonate rocks. Though they know their chemical composition—a mix of carbon, hydrogen, nitrogen, and oxygen—Ellis said that the reason for the uncertainty is because the A-dot’s chemical structure is too heterogeneous to be properly described.
Nanomapping, Mass-Tagging, and Seawater Fracturing
But even if they are unsure of how they work, the researchers now have evidence that the A-dots are capable of holding up to reservoir conditions for long periods of time and over long distances. Ellis said this has left the door wide open for a much wider application suite for the A-dots and other nanoparticles that the company is researching.
The company is already using nanoparticles in drilling fluids, presumably for wellbore strengthening, but it is looking toward even more emerging concepts such as magnetic reservoir mapping and hydraulic fracturing mapping. The idea behind these “nanomappers” is that they will slow down an electromagnetic wave as it is pulsed from an injector to a producer well.
The difference between the wave’s travel time through the fluids before and after they have been infused with magnetic nanoparticles may allow engineers to visualize a water drive front, or in a monobore scenario, what a well’s fracture network looks like.
The company is also working with research partners to develop a new set of nanoparticles, some that are fluorescent and some that will be used for mass-tagging—an innovation that intends to offer tracer resolution measured on the atomic scale. The plan for mass-tagging involves using a common nanoparticle that is proven to be reservoir-tolerant and then “we can pick any molecule out of an infinite range of possibilities, attach it to the nanoparticle and boom, you have a specific barcoded tracer,” Ellis explained.
Another future step is to finish the development of a line of chameleon A-dots that will alter their fluorescence spectrum when they come into contact with crude. A different variety, called nanocore shells, are to be used to encapsulate droplets of acid and release them at a specific point inside the reservoir to etch out wider pore paths that will improve hydrocarbon flow.
In yet another nano-project, Saudi Aramco is trying to enable the use of untreated seawater for hydraulic fracturing in sandstones (SPE 181283). The company has gone to great lengths to protect its freshwater resources by using seawater for its enhanced oil recovery projects and is seeking a similar strategy for its burgeoning unconventional program that is focused on tight gas production to replace the oil Saudi Arabia currently burns for power generation.
This project has not yet left the laboratory, but the initial data points are positive. In presenting the paper, Ghaithan Al Muntasheri, the chief technologist for the production technology team at Saudi Aramco, described the nanoparticles as “nano-crosslinkers” that increase peak fluid viscosity—an important factor for proppant transportation—by 23% to 116%. Such levels of viscosity should significantly reduce the need for synthetic polymers or guar.
With the nanoparticles, the fracturing fluids tested remained stable at temperatures up to 300°F and were effective even with a very high salt content of 56,000 ppm. Al Muntasheri said current technologies do not work at such extreme temperatures and can only tolerate 35,0000 ppm of salt.
Core flood and proppant pack testing also showed that the regained permeability was more than 90% with the nanoparticles. And critically, the nanoparticle fluid system is compatible with scale inhibitors that would be needed to offset the obvious formation damage associated with introducing seawater to a reservoir.
Al Muntasheri said in a fracturing treatment the nanoparticles would represent about 0.02% of the total volume of fluids used, which he estimated would be 500-700 kg in weight, for a cost of USD 100,000 or less.
The paper goes on to report that this approach does not require any modification to the pumping equipment used for the fracturing job, and because of its delayed reaction to temperature, which helps the fluids maintain a high viscosity, less horsepower is required for pumping. This operational benefit may result in a longer lifetime for pumping units.
Nanocapsules for Waterflooding Conformance
Low-cost polymer gels are among the most popular tools used in waterflooding treatments to selectively shut off high-permeability channels that are generating excess water production. Though polymer gels are widely used because they are effective, their big drawback is that the gelation process tends to begin quickly in the near-wellbore area, leaving the bulk of the reservoir unaffected.
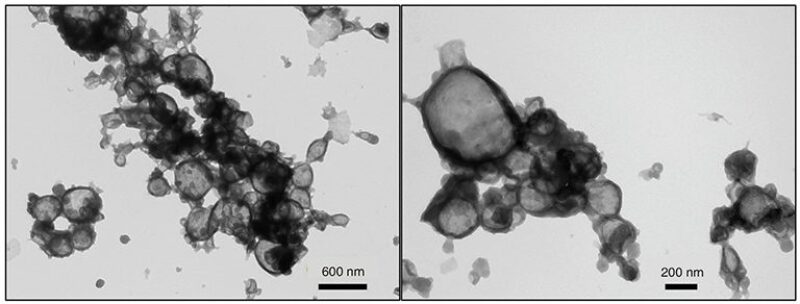
Chemists at the Research Triangle Institute in Raleigh, North Carolina, think they can improve the conformance capabilities for one of the most widely used gel systems, partially hydrolyzed polyacrylamide (HPAM), by placing its main reactant, chromium (III), inside time-released nanocapsules (SPE 181547).
This concept has received a great deal of fanfare in the medical industry for its potential to deliver cancer-killing drugs and other medicines to specific parts of the human body.
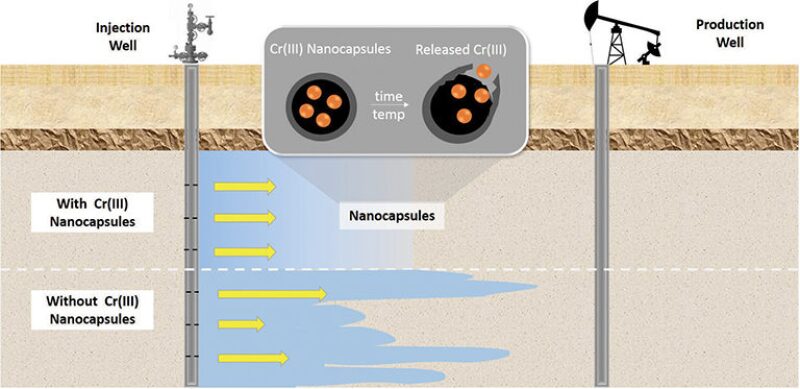
In the case of waterflooding, the nanocapsules would be used to delay the exposure of chromium to HPAM, allowing the two constituents to travel deeper inside the reservoir before forming into a gel. Computer modeling suggests that this could result in oil production improvements of single-digit percentages.
The paper’s authors note that a company called Brightwater has developed another nanoparticle-based technology that also seeks to block off water channels. However, Leah Johnson, a chemist with RTI International, said her team believes its work represents the first time that anyone has sought to encapsulate chromium for a conformance application.
The nanocapsules are formed through a complex inverse miniemulsion technique that involves multiple steps of combining hydrophobic elements and surfactants with a water-based solution containing the chromium. In one phase, as the solution is stirred, nanodroplets of chromium are formed and in the next step a reaction takes place that encapsulates them.
In addition to establishing an effective encapsulation process, the researchers also found that the early formulations of their nanocapsules effectively delayed the gelation process for up to 17 days. They also observed that the nanocapsules will remain intact for at least 48 hours when exposed to 122°F (50°C) synthetic seawater, suggesting that the long-term delivery of chromium is quite possible.
“There’s a variety of different degradable chemistries we’re looking at to incorporate into the shell,” Johnson said, explaining that some of those chemistries are water sensitive while another is more reactive to temperature. “So we can really tune the concentration of the degradable chemistries within the shell to release at different time points.”
Further work is being done with the University of Texas at Austin (UT) and Tufts University in Massachusetts to understand the mobility of the nanocapsules through sandpacks. The early results from this work show that the nanocapsules remain about the same size when exiting a sandpack, which Johnson said is “very promising.”
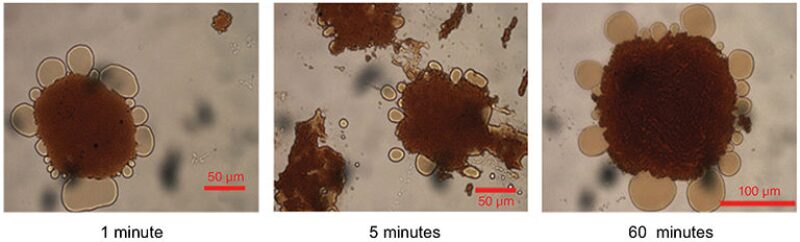
Magnetic Oil Separation
In another project, researchers at UT are working on a magnetic nanoparticle technology to remove the micron-sized oil droplets left dispersed in produced water after it has been treated by conventional separation technologies, e.g., gravity and membranes (SPE 181893).
In testing, the experimental system removed 99% of the oil droplets and may eventually lead to the development of a compact and highly efficient separation system for offshore installations that are challenged by space constraints and the high cost of water treatment.
When the magnetic nanoparticles are introduced to produced water, they surround the oil droplets in a way that is reminiscent of how white blood cells attack a foreign bacteria or virus. In most cases, it takes about 5 minutes for all the nanoparticles to find an oil droplet, and in a rapid-mix chamber that time can be reduced to just 3 minutes or less.
The nanoparticles are attracted to the oil droplets through electrostatic forces. This is achieved by coating the nanoparticles with a positively charged polymer since most oil droplets have a negative charge. And the weaker that negative charge is, the quicker the reaction takes place.
Saebom Ko, a research associate at UT who is helping to lead this research project, explained, “After attaching to the oil droplets, the small nanoparticles get bigger, and so whenever you have a magnetic field, the particles will move very quickly to where the magnet is placed.”
In a real-world scenario, the mix of nanoparticles and oil would be pulled to the side of a treatment tank where the next trick is to recover them while letting the treated water flow out. That part of the process is to be addressed with a small continuous flow system that the UT researchers hope to have ready for testing next year.
The UT researchers also found that crude types with a higher acidity need more magnetic nanoparticles to be effectively separated. And so far, the upper limit for oil content in the test fluids has been 0.25% by weight, but the plan is to step that up in future work.
Pending the results of the continuous flow system and further funding, Ko said the last item on the agenda would be to build a pilot system. Because the nanoparticles are costly, she added that a critical requirement of a field-system will be a way to separate them from the oil droplets at the end of the process so they can be reused.
“That will be the hardest part,” Ko said. “But if you can reuse the nanoparticles many times, then cost-wise, you have some competition” with conventional separation technologies.
For Further Reading
SPE 181547 Nanocapsules for Controlled Release of Waterflood Agents for Improved Conformance by Leah Johnson et al., RTI International.
SPE 181283 Nanomaterials-Enhanced High-Temperature Fracturing Fluids Prepared with Untreated Seawater by Leiming Li and Ghaithan A. Al-Muntasheri, Saudi Aramco.
SPE 181893 Oil Droplet Removal From Produced Water Using Nanoparticles and Their Magnetic Separation by Saebom Ko et al., University of Texas at Austin.
SPE 181551 Oil Industry First Interwell Trial of Reservoir Nanoagent Tracers by Dmitry Kosynkin and Mohammed Alaskar, Saudi Aramco.