Groups of wells communicate and interfere with and hit each other. It’s an unruly scene but it can offer some production benefits. The first of these stories looks at how competing fracture networks can add drainage in rock that might otherwise be missed and the tradeoffs that come with that benefit for those planning drilling and fracturing.
ConocoPhillips quantified the impact of these competing fractures at its four-well test site. A second story looks at how the operator used the site to track how fast those communication channels close up and to identify what could be the choke point causing it.
A third story looks at the method used by Devon Energy to measure the degree of interference between wells and is using to create more, cost-effective communication among wells.
For Further Reading
URTeC 2570 Analysis of a Multi-Well Eagle Ford Pilot by K. Raterman, Y. Lue, B. Roy, et al., ConocoPhillips.
URTeC 3040 Well-to-Well Interference: Quantifying Connectivity and Understanding How Much Is Too Much—a STACK Case Study by T. Ingle, H. Greenwood, M. Wilkins, et al., Devon Energy.
SPE 191407 A New Technique for Quantifying Pressure Interference in Fractured Horizontal Shale Wells by W. Chu, K. Scott, R. Flumerfelt, Pioneer Natural Resources; C. Chen, Kappa Engineering.
Fracturing Within the Lines Is Neither Realistic Nor Productive
Some fractures grow like weeds, extending 1,000 ft or more, far beyond the area in which they were intended to grow.
The industry term for fracture growth that invades areas drained by other wells is “interference.”
The word was coined by fracturing experts hoping to replace the term “frac hit” after it became clear that the fractures running from one well to the next did more than just “hit” things. The term “interference,” though, still suggests overlapping fracture networks can promote wasteful competition for resources or damage.
A recent paper from Devon Energy looked at the relationship between interwell connectivity and production and asked “how much is too much?” (URTeC 3040). Their answer seems to be “more is better among groups of wells fractured around the same time.”
“Well-to-well connectivity should not always carry a negative connotation. As this study showed, when using a set well spacing, increased connectivity may lead to higher well performance,” said Trevor Ingle, a completion engineer for Devon, at the end of his 2020 Unconventional Resources Technical Conference (URTeC) presentation.
A similar message was delivered in a paper from ConocoPhillips, which used a highly instrumented, four-well test site in the Eagle Ford to observe long fractures draining rock in the area beyond the densely fractured near-wellbore area (URTeC 2570).
“The major message we wanted to convey is that there was interwell interference during and after completions,” said Kevin Raterman, an engineering fellow for ConocoPhillips.
The conclusions of the paper, which offered a rare look at fracture growth among nearby wells, challenged the widespread assumption held by “a lot of people in the industry today [that] there is too much interference among wells.”
It concluded that development decisions need to consider the tradeoff between the production impact of interference on each well and the added output from added wells.
When ConocoPhillips evaluated adding wells to the four-well pilot, it concluded “the per-well production degradation was easily offset by the additional well count,” Raterman said.
It should be noted that both papers were focused on situations where fractures grew into productive rock. When new wells are fractured near an old horizontal well, that is often not the case. Depleted zones around those wells can encourage fracture growth into rock with little oil and gas potential, resulting in production disappointments.
Development plans that add wells in an area are likely to mean more oil recovered within that unit, but less recovered per well.
ConocoPhillips observed competition, but not “extensive overlap” among fracture networks. Long fractures provided a net production gain by extending into areas where the drainage is “patchy and inconsistent.”
They also appeared to be inevitable. “It appears that inter-well communication is established fairly early in the pumping operation suggesting that even a radical alteration of the completion design may have limited impact on the outcome,” the paper said.
The downside for these long fractures is their short life span. The paper said, “A picture emerges of uneven drainage which degrades significantly with time.”
A Gathering System
While fracturing its four-well test site in the Eagle Ford, ConocoPhillips observed rapid development of overlapping fracture networks.
“The first well laid down a fracture system that was quite extensive across every well in that configuration. And with subsequent completions, many of the original fractures laid down in one well were essentially utilized in the subsequent wells,” the paper said.
For those who warn of the dangers of interference, this sounds like spending to fracture the same rock over and over.
But the paper said overlapping long fractures “do not necessarily portend a competitive drainage fiasco.” The area drained by those fractures is not sufficient to “set up a battle for the same resource.” They found there was not enough spatial overlap by fractures to create a “commonly shared fracture plane.”
ConocoPhillips’ descriptions suggest these long fractures from adjacent wells work like a subsurface pipeline system.
They are conductive—in the weeks after fracturing, these links equalize the pressure among wells.
If one well is shut in, inter-well fracture connections can reroute the oil and gas to other wells. But if all the wells are flowing, the oil and gas will normally go to the nearest well.
“It wants to follow the path of least resistance; that will almost always be to the nearest well,” Raterman said.
Establishing Connections
There are not that many long, conductive fractures and even fewer creating conductive connections among wells. But after 400 days, large pressure differences were seen between the wellbore and locations beyond the near-wellbore area, indicating drainage soon declined in the far-field area.
The ConocoPhillips paper raised the question: Is it necessary to reduce well spacing and stacking distances to ensure all that rock is efficiently drained?
The question was echoed in the Devon paper, which also considered tighter well spacing as a way to significantly increase production per development unit.
Based on field data gathered from wells in the STACK formation in Oklahoma, Devon showed that more closely spaced wells had more fracture interconnections than wider-spaced wells.
It estimated the inter-well interference—connectivity—by measuring the pressure change associated with nearby producing wells by using a downhole pressure gauge in a well.
Devon used a system called the Chow Pressure Group to create an average conductivity score. It showed that closely spaced wells scored consistently higher, suggesting the wells as a group produced more.
When Devon considered the economics, it began looking for other ways to increase connectivity.
Tighter spacing presents a tradeoff: more wells increase the production of the overall development, but each of those wells will produce less because each is getting a smaller slice of the pie.
ConocoPhillips faced a similar tradeoff when it considered adding a third layer of wells on top of the four wells in its test site. “The geochemical data showed the upper part of the Eagle Ford was not draining efficiently,” Raterman said. Based on pilot testing, it was estimated that new wells would produce about 15% less than a well with no others nearby.
ConocoPhillips accepted the tradeoff because of its estimate of the production potential added by more wells.
Devon also expected a large estimated ultimate recovery (EUR) gain from denser development, but the reduced expected output per well was a bigger factor. “You need to understand the per-well relationship because it is often a better indicator of unit economics,” Ingle said.
It stuck to wider spacing and found that pumping considerably more proppant per foot also delivered results that justified the investment.
Denser development and the use of more proppant are hardly new ideas. What was different were their evaluations to determine what to do and to evaluate the effectiveness of their ideas.
“Interference has been around forever. This allows us to assign a unique number to it. That is valuable,” said Hart Greenwood, a reservoir engineer for Devon.
Cause-and-effect relationships in shale can vary unpredictably. The Devon paper described how it continued to push up the amount of sand pumped. Past a certain level, the rate of improvement slowed.
As is often the case when fracturing designs change, these trends were non-linear with many variables at work.
The fact that the trend did not hold was disappointing, but on the plus side, Ingle said the Chow Pressure Group predicted there would be a limit to the benefits that more proppant could deliver.
“This was good for the team as it allowed us to refine our expectations about what incremental performance we might see,” he said.
Regular data gathering is needed because conditions vary based on the location and other variables.
“This will and should always be an economic exercise, so we do not anticipate that the conclusion we arrived at here will be perfectly analogous in every resource play,” Ingle said.
Searching for Ways To Ensure Lasting Fracture Interference
The simple message from ConocoPhillip’s multiwell test site is that groups of fractured wells are all interconnected. But not for long.
Understanding those fast-fading connections helps explain why production drops quickly in these wells.
When a group of four wells began producing in the Eagle Ford, the data from the heavily instrumented test site showed “all the wells are interconnected by hydraulic fractures.”
During the first 60 days of production, downhole measurements by 45 pressure gauges placed in and in between the wells declined in unison as oil and gas were produced.
The pressure data showed “a strong shared system response among the wells,” said, Kevin Raterman, an engineering fellow for ConocoPhillips, who presented a paper on the test site results at the Unconventional Resources Technical Conference (URTeC 2570).
Another sign of inter-well connections was seen when more water was produced after fracturing the lower two wells, even though less water was pumped into them than the upper wells where completion methods varied. The paper said the extra water likely flowed down from the upper wells.
When one well was shut in, it was observed that its production was diverted to other wells. Modeling based on the data concluded that interwell fractures could shift 70% of the production from a shut-in well to the others.
Otherwise, these long fractures worked like an oil-and-gas-gathering system, sending the production to the nearest well.
At 400 days, the long fractures had become far less conductive. There were wide gaps in the pressure levels in the wells compared to gauges measuring pressure declines away from the well, suggesting the long connections between them had deteriorated.
There were differences of more than 4,000 psi between 39 of the 45 pressure gauges and the bottomhole pressure in the wells. Three gauges were no longer registering pressure declines but instead detected rising pressures; 20 of them were showing “no further signs of continuing depletion.”
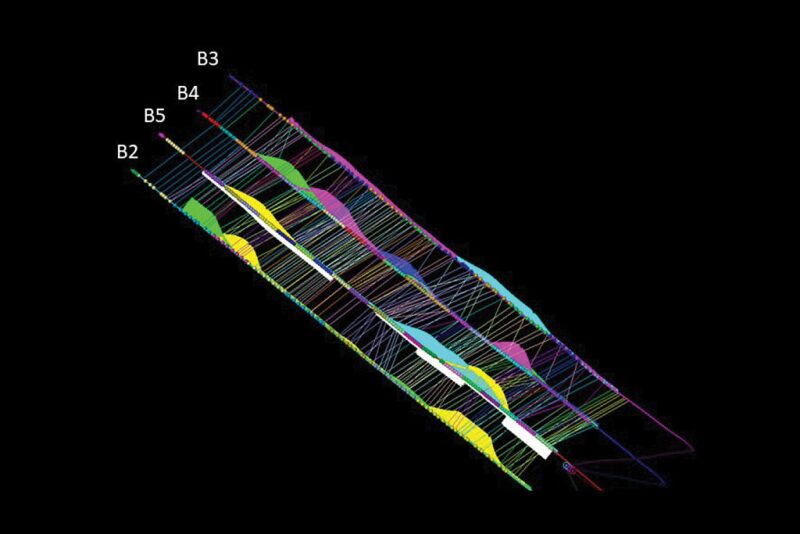
Long-Term Issues
In the years since those wells were completed in 2015, Raterman said he has thought a lot about whether there is a way to extend the productive life of these fractures.
“We have not come up with a mitigation method other than to go back to pump more proppant into the well at a significant cost. I would hope at some point” there are alternatives, he said, in an interview.
After ConocoPhillips completed the pressure measurements that showed shrinking fracture conductivity, it pumped large volumes of water into two wells to increase the pressure that had been depleted by production.
This method is used within the industry to discourage fracture growth into the depleted rock around old wells, which hurts the performance of the new wells.
In this case “the test was only designed to determine if water injection could effectively repressurize the reservoir after depletion,” Raterman said.
They tested two producing wells by pumping in 65,000 bbl of water, with one well getting 55,000 bbl and the other 10,000 bbl.
The test did increase the reservoir pressure around those wells. But there were troublesome side effects—afterwards oil and gas output dropped in the test wells while water production rose.
“You must recognize water is not a great thing to put in a well in any context where you lack the energy to remove it,” Raterman said.
The test raised an interesting question. When they began pumping water into the fractures, it was far more difficult than expected. After establishing the water flow, the pressure required for injection dropped sharply.
Raterman said, “That raised the question ‘why are we seeing such a high entry pressure in the near-well connection?’ Is there some sort of blockage?”
Although the unexpectedly high entry pressure is a problem, it is a more manageable one than a fracture that has closed because of the drawdown of oil and gas.
The challenge now is finding and analyzing the blockages and figuring out what can be done to remove them to allow oil to flow out of enhanced-oil-recovery treatments such as gas injection.
One possibility is that the perforations are being clogged by scale in the same way wells can be blocked. Raterman said, “There are any number of things that could be going on.”
Devon’s Fracturing Challenge Communicating at a Distance
Devon Energy engineers figured out that adding more tightly spaced wells would produce significantly more oil from an area, based on cutting edge pressure testing and analysis.
The bottom line in the pitch for tighter well spacing was: “From the lightest well spacing (widest) to the densest, there is an increase in total unit recoverable oil of 55%,” according to a Devon paper (URTeC 3040).
At the heart of this argument was extensive well-to-well pressure data in the Oklahoma STACK, which they evaluated using the Chow Pressure Group. The technique enabled Devon to score the degree of well-to-well fracture interference—the product of overlapping conductive fractures among wells.
It has continued using the method, which deploys a downhole pressure gauge in a shut-in well to measure the pressure change due to production at a nearby well. The Chow method was used to convert the data into an average score of a series of readings that could be used to compare the degree of interference due to fracture interconnections among wells.
The technique depends on accurately measuring and interpreting small pressure changes. The paper goes into detail on how to gather good data.
Devon studied the relationship between the interference score and production by evaluating many well pairs and development units—groups of long horizontal wells. A chart showed a sample of the work—tests that measured interference between 25 well pairs in 10 development units with varying spacing and proppant loads.
The analysis confirmed the conclusions in a paper by Pioneer Natural Resources (SPE 191407) which first described the system, said Hart Greenwood, a reservoir engineer for Devon.
Devon’s recent paper concluded that drilling units where the interference is greater will ultimately recover more oil “due to less stranded resource between the fracture tips.”
The potential total gain by adding wells was large, but not enough to convince the company to drill and complete more wells that will each produce less—because tighter spacing means the wells are competing for reserves.
While denser development will increase the total production in a unit, “you need to understand the per-well relationship because it is often a better indicator of the unit economics,” said Trevor Ingle, senior reservoir engineer at Devon, who delivered the paper at 2020 URTeC.
“Due to the economic tradeoffs between capital spending, this relationship [connectivity], and commodity prices, we felt our economic objectives were better met at a lighter well spacing pattern,” he said.
Lighter meant relatively widely spaced wells and a search for another way to increase the level of inter-well interference.
Devon wound up with a familiar solution—pumping more sand which it said would produce greater numbers of longer, better-propped fractures to provide extended conductive pathways for increased fracture interference.
During the presentation Ingle offered a “conceptual model” of how more proppant could lead to more inter-well connections with the caveat: reality is more complex.
Devon noticed that even when the amount of proppant pumped was light, moderate connectivity was still measured. They explained that one fracture within a stage often takes in the most fluid and sand, creating a dominant fracture extending out beyond the other fractures.
To increase the level of interference, they pushed up the sand pumped per foot in fractures by 60% from their base amount. That design delivered the expected gains in conductivity and production.
“We were able to build an economic model based on the extra costs of the completion volume and increased performance. It did illustrate that we were adding net present value on a unit basis, which met our economic objectives,” Ingle said.
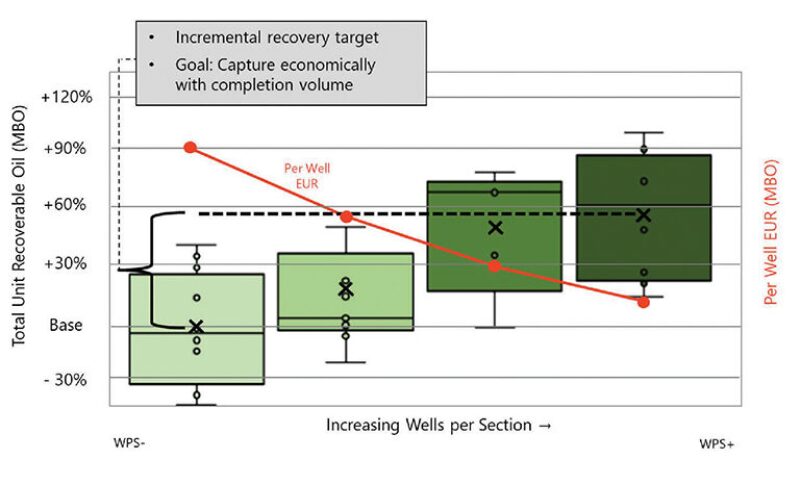
Adding proppant may be particularly effective in that part of the Anadarko formation because the geology and stress regime favor the creation of long planar fractures, said Kyle Haustveit, subsurface engineering manager for Devon.
Those long, straight fractures generally allow proppant to flow further out into the formation. Pumping more sand in other formations where fractures branch out may not be as effective because it is hard to pump proppant around turns.
Interference testing over time can track if fractures are losing conductivity.
“It is important to test [interference] over time. Your basin may be different than the STACK, most places are,” Greenwood said.
Numerical interference measurements make it possible to determine whether an incremental change delivers the expected gain based on the trend from past results.
Devon’s testing showed that when it pushed the amount of proppant pumped to double the base amount, the rate of improvement slowed. That reduced the financial reward for pumping more, but if proppant prices are low, higher volumes could still be a good business decision, Greenwood said.
Since the testing period covered in the paper, Devon has built Chow Pressure testing into its routine for starting up well pads. It uses a procedure that minimizes production delays and the cost of gathering the data.
Production begins on one well per day. In 24 hours sufficient data is collected—around 18 hours’ worth—and used to set up the next test.
Temporary pressure gauges placed on new and old wells nearby allow the measurement of interference from different angles and distances. Each pressure gauge is placed in a “side-pocket mandrel” in the tubing, which is also equipped for gas lift.
Wireline is used to install and remove the gauges so the data can be retrieved and the device moved to another well.
Devon has found multiple uses for the system, which it has been using since 2018. If no interference is detected between wells at different depths, that may identify isolated reservoir rock for later development.
Establishing values for connectivity might make it possible to tailor fracturing designs to predictably hit specific interference levels.
Devon started using the Chow Pressure Group soon after it saw Pioneer’s paper about its new idea. Since then the idea has spread.
“There are quite a few companies using this,” Haustveit said. He predicted more SPE papers to come with new methods and tweaks to the current ones.