The development of the Kanowit field offshore Sarawak, Malaysia, requires the drilling of two subsea development wells with a semisubmersible rig. Previous experience identified the need for solids-free drilling fluid to ensure maximum reservoir productivity and that the quality of the produced gas remains within required specifications. A cost-effective option was to use a less-dense solids-free drilling fluid and use managed-pressure drilling (MPD) to compensate for the difference in density with backpressure.
Introduction
The Kanowit development has a water depth of approximately 78 m and is the first subsea gasfield-development program in Malaysia. The purpose of the program is to extract gas from a carbonate reservoir in an area prone to severe circulation losses. The Kanowit initiative also calls for the drilling and completion of two subsea development wells, Kanowit-SS1 and Kanowit-SS2, by use of a semisubmersible drilling rig.
Offset wells in the area have identified the need for the use of solids-free drilling fluids to ensure that impurities from the drilling process are not passed on to the gas-processing facilities once the wells are put on production. The high reservoir pressure of the Kanowit field, which required an equivalent mud weight of more than 15 lbm/gal (1.8 specific gravity), required the use of high-density solids-free drilling fluids such as cesium formate. However, the costs associated with the use of such a drilling fluid, as well as the high probability of losing a large volume of fluid when the fractured-carbonate reservoir is drilled, made this option economically impractical.
A more cost-effective option was to use a less-expensive, less-dense solids-free drilling fluid such as sodium/potassium formate, and to use MPD technologies to compensate for the difference in density by the exertion of backpressure in a closed-loop-circulation drilling system throughout the drilling operation. The use of the MPD system mitigates the expected circulation-loss risk by using the constant-bottomhole-pressure (CBHP) drilling technique to keep the level of overbalance to a minimum while drilling through the carbonate reservoir. The early-kick-and-loss-detection capabilities of the MPD system, in conjunction with the underbalanced drilling fluid, allow for the collection of critical geopressure-environment data. Furthermore, the MPD system would enable the rig to shift immediately to pressurized mud-cap drilling (PMCD) should the level of circulation losses become severe.
For a discussion of the technical definitions, equipment, and applications of MPD, please see the complete paper.
Kanowit MPD-System Design
The primary objective of the Kanowit field MPD system is to reach target depth with minimal drilling complications and to avoid uncontrolled events by maintaining BHP. This approach was applied in designing the MPD system for use in the drilling operations of the 12¼- and 8½-in.-hole sections of the two Kanowit wells. Engineering preparations and calculations were made to perform early kick and loss detection in the 12¼-in.-hole section. In addition, preparations were made for PMCD operations in the event that severe circulation losses were encountered while drilling the top of the carbonate reservoir and for running and cementing the 9⅝-in. casing. Similar preparations were made for conducting CBHP operations in the 8½-in.-hole section. Engineering calculations were performed to determine the backpressure that the MPD system needed to exert during drilling and during connections. The density of the drilling fluid that needed to be displaced into the well to compensate for the backpressure from the MPD system (when tripping needed to be performed) was also determined beforehand. A plan for conducting PMCD operations for the 8½-in.-hole section was also put in place in the event of severe circulation losses. Finally, kick simulations were made and procedures were created to ensure that an MPD well-control matrix was in place and to distinguish what situations were to be handled with MPD equipment, and what constituted a well-control situation.
The rotating-control-device (RCD) system used for the project is specifically designed for offshore deployment. It is equipped with an upper flange that can tie back into the rig diverter system so that returns can be taken through the conventional route, even if the RCD body is already rigged up but the RCD bearing assembly is not installed. This process minimizes the spillage of drilling fluid into the environment. Tying back to the rig diverter system would have required a telescopic slip joint that allows for passage of the RCD bearing assembly. However, because of space constraints, a mud funnel was installed instead and the connection to the rig diverter system was no longer pursued.
As in typical RCD deployments on a floating rig involving subsea blowout preventers, the RCD was installed on top of a mud cross installed on top of the rig slip joint that has been collapsed. A special crossover was fabricated to increase the pressure rating of the riser system from 500 to 1,500 psi, effectively making the RCD (whose dynamic pressure rating at a rotational speed of 100 rev/min is 1,000 psi) the weak link in the system. The resettable riser-protection pressure-reducing valve installed in the mud cross was set at 1,000 psi in accordance with this limitation. Hydraulic modeling performed for the two wells suggests that maximum backpressure will be in the 700- to 800-psi range.
Other RCD-system components include the valving, piping, and hoses for an annular-injection line to facilitate PMCD operations. Lines connecting to the trip-tank pump to facilitate filling the well during conventional tripping operations with the RCD bearing assembly in place and a bleedoff line are also in the system. The flow from the trip-tank pump was routed through the RCD, across the well, and through the MPD choke manifold. This allowed the hole fill to be measured through the trip tank and the flow to be measured by use of a mass flowmeter on the MPD choke manifold, thereby creating a faster detection system for losses and gains; the same flow path was used during flow checks. A backpressure pump line to energize the MPD chokes with flow during connections was also installed; this in turn was connected to the MPD backpressure pump or to one of the rig mud pumps. The main flowline was connected to the automated MPD choke manifold to facilitate BHP control and wellbore and surface-system monitoring.
With the automated MPD choke manifold in place, drilling can be performed under a variety of options. While drilling, the system can change automatically from one mode to another as the well encounters different environments.
- Controlling flow out—manual or automatic
- Controlling pressure—manual or automatic
- Automatic kick detection and control—pore-pressure determination
- Automatic loss detection—fracture-pressure determination
- Automatic detection of many common drilling events
A photograph of the actual RCD setup installed on the Kanowit wells is provided in Fig. 1.
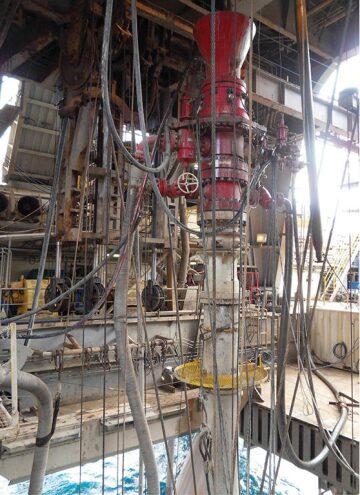
Kanowit MPD-Program Implementation
The 12¼-in.-hole sections of the two Kanowit wells were drilled conventionally, but with the RCD and MPD equipment rigged up in the event that either PMCD or CBHP techniques were required to reach section target depth (TD). The automated MPD manifold was placed on line. The RCD was rigged up before drilling the 12¼-in. hole, and in-casing tests to optimize the performance of the automated MPD manifold were performed before drilling out cement and the float shoe from the preceding hole section. However, very few issues were encountered that required the intervention of the MPD system in the hole section. Likewise, the circulation losses encountered were not severe enough to necessitate PMCD operations.
In the 8½-in.-hole section of the first well, drilling was carried out with an approximately 13-lbm/gal brine composed of sodium/potassium formate that was both statically and dynamically underbalanced in relation to the pore pressure. The MPD equipment was therefore used to maintain a 150-psi overbalance throughout the operation. Total depth was reached without a major incident. Once it was established that the well was stable and the risk of severe circulation losses was minimal for the well that had been drilled, it was decided to use high-density solids-free brine (cesium formate in particular) as the tripping fluid. A tripping density of approximately 15 lbm/gal at standard conditions was prepared to balance the pore pressure. This fluid was circulated around the well, using the hydraulics model of the automated MPD system to maintain a BHP equivalent of approximately 15 lbm/gal. However, fluid returns to the surface as measured by the mass flowmeter indicated that the density of the tripping fluid was lower than required. Therefore, the pumps were stopped and a second circulation of cesium formate was required to bring the overall fluid density up to an adequate tripping margin.
For the second well, the 8½-in. section was drilled to TD with a drill-in fluid of approximately 13 lbm/gal. Approximately 500 psi of surface backpressure (SBP) was held at surface to maintain overbalanced conditions dynamically. SBP was increased to 750 psi during connections to compensate for the loss of annular friction. The average rate of penetration experienced was 15 m/h.
The automated MPD system was used to perform formation anomaly tests (FATs) safely, providing information about the highest actual pore-pressure value of the formation being drilled. Performing this test was possible in this application because the drilling fluid used was statically and dynamically underbalanced. Furthermore, because the size of the anomaly was minimal (because of the early-detection capabilities of the MPD choke manifold), the anomaly was circulated out of the system safely at a full drilling rate instead of slow circulating rates, which gave the process greater time efficiency.
A dynamic formation-integrity test (FIT) was also performed on both wells. Backpressure was increased until circulation losses were detected by the automated MPD manifold, effectively determining fracture pressure and the upper bound of the drilling window for the reservoir section. Though the dynamic FIT was performed repeatedly, a similar value for fracture pressure was achieved using the automated MPD system each time the test was performed. This supports the idea that if the level of detection is higher in terms of precision, FITs and leakoff tests can be conducted without lowering the fracture pressure of a given formation, at least for carbonate formations in this particular instance.
The automated MPD system is capable of performing FATs and FITs at any point during drilling, providing the opportunity to collect geopressure-environment data—information that has aided the drilling decision-making process for both of the Kanowit development wells.
Overall, the MPD system performed optimally during the drilling operation for both Kanowit development wells. The system performed to expectations in holding backpressure and maintaining control of the BHP to drill the wells safely and efficiently to TD with a statically and dynamically underbalanced solids-free drilling fluid. It performed well in detection mode and even when the chokes were placed on manual control.
This article, written by JPT Technology Editor Chris Carpenter, contains highlights of paper SPE 164573, “Managed-Pressure Drilling With Solids-Free Drilling Fluid Provides Cost-Efficient Drilling Solution for Subsea Carbonate-Gas-Development Wells,” by Trigunadi Budi Setiawan, Mohammad Mizuar Bin Omar, Mohammad Zarkashi Bin Sulaiman, Mohammad Zarir Bin Musa, Muffaz Fadzli, and Thanavathy Patma Nesan, Petronas Carigali, and Chad H. Wuest, Julmar Shaun S. Toralde, and Prem Ananthan Sridharan, Weatherford, prepared for the 2013 IADC/SPE Managed Pressure Drilling and Underbalanced Operations Conference and Exhibition, San Antonio, TX, USA, 17–18 April. The paper has not been peer reviewed.