A new rotary-steerable system (RSS) was designed to give geometrically greater dogleg-severity (DLS) capability while still being able to withstand the increased bending stresses. This high-build-rate RSS was able to eliminate controlled rate of penetration (ROP) as a limiter, which resulted in 39% ROP improvement. In addition, the development of a high-build-rate RSS provided multiple benefits, including elimination of ROP and logging-while-drilling limitations, increased curvature capabilities, and higher reliability of the system with respect to high-bending-related issues.
Introduction
Directional-Drilling Methods. In the early days of directional drilling, the process involved jetting and the use of bent subs as the main methods for deviating a wellbore. These methods largely have been superseded by the use of engineered bottomhole assemblies (BHAs) for inclination-only control and motor or rotary-steerable BHAs for complete 3D control.
Simple BHAs (Inclination Control). In simple BHAs, placement of stabilizer elements determines the net force on the bit and results in either a building or a dropping tendency of the BHA.
A stabilizer placed close to the bit acts as a fulcrum, with one side being forced down by the weight of drill collars.
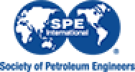