Every activity within a well alters the pressure being exerted on the open hole, and every mitigation technique attempts to maintain the desired pressure within acceptable limits. If the pressure becomes too low, kicks, borehole breakouts, and hole collapse are the primary consequences (Fig. 1). Pressure that is too high can damage the reservoir, induce fluid losses, and slow down operations. When these unfortunate events occur, remedial actions are usually necessary, increasing safety exposure, nonproductive time, and the overall costs of the project.
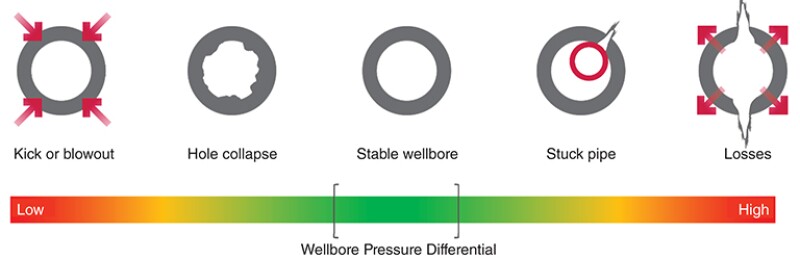
To mitigate these concerns, operators have used the techniques of managed-pressure drilling (MPD) to maintain annular pressure and create a pressure-tight barrier against drilling hazards and manage inflow from the formation during drilling. While conventional drilling uses the hydrostatic pressure of the drilling mud to manage the pressure of the wellbore, MPD uses a combination of surface pressure, hydrostatic pressure, and annular friction to balance the exposed formation. Over the decades, MPD has been associated as a technology that is used only on problematic wells and only as a last resort. However, recent developments have highlighted that managing pressure is not just for drilling operations or just the most challenging wells.
When integrated at the beginning of operations as part of a comprehensive well plan, managing pressure becomes a performance-enhancing solution for any type of well classification, including development, directional, multilaterals, and horizontals. Wellbore stability is maintained throughout the entire operation and pressure is dynamically altered in the annulus, enabling any operation to become faster with fewer challenges while delivering a more productive well and reducing overall costs and exposure to hazardous risks. The managed-pressure approach has even been leveraged to fully optimize a field/reservoir development program.
An example of how MPD techniques can be incorporated into an overall well plan occurred on an ultradeepwater exploration well drilled by TotalEnergies in the Mexican waters of the Gulf of Mexico (SPE 200503). The operator and the service providers wanted to manage the pressure during the entire well program—including drilling, tripping, running casing, and cementing—to address pore pressure uncertainty, pressure ramp increase, and a narrow pore pressure/fracture gradient (PP/FG) window.
The seafloor rested under 10,748 ft (3276 m) of water, and with the exploratory nature of the well, the conventional solution involved an excessive number of casing strings and an overbalanced mud weight (MW). Integrating MPD techniques enabled the operator to adjust the bottomhole pressure instantaneously, the result being a recognition that conventionally cementing a string of 13⅜ -in. casing to isolate the critical formation and safely continue drilling further stages of the well was impractical. To make the situation even more challenging, the engineers did not precisely know the size of the hole.
A collaboration between the engineering teams of the operator, the cementing service provider, and MPD professionals resulted in a generated plan. A tail slurry of 15.86 ppg (1.90 SG) followed a 12.52 ppg (1.50 SG) lead gas-tight slurry. At a total depth of 13,622 ft (4152 m), the combination kept the equivalent circulating density (ECD) at 9.18 ppg (1.10 SG) without exceeding 9.51 ppg (1.14 SG). At the casing shoe, located at 12,801 ft (3902 m), the plan called for a 9.01 ppg (1.08 SG) without exceeding 9.35 ppg (1.12 SG), as shown in Fig. 2.
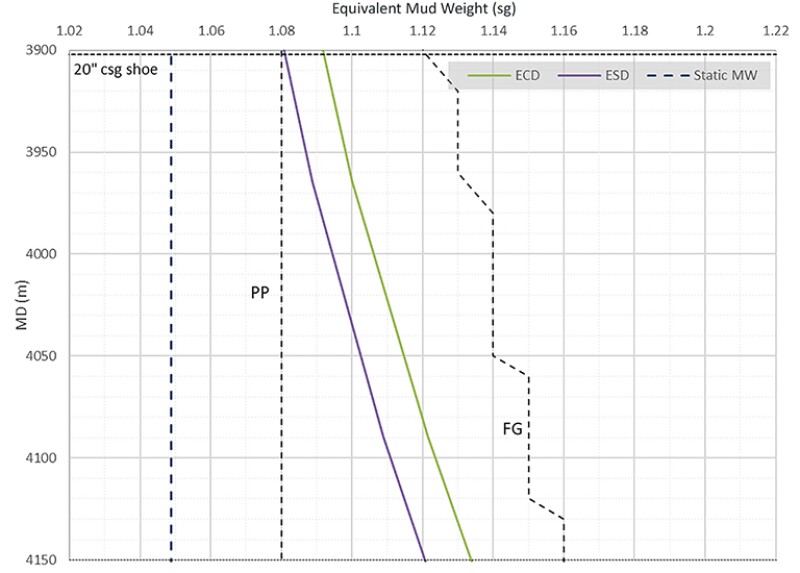
Field personnel executed the operation flawlessly with full returns observed throughout the entire cementing process and no influxes detected, verifying the MW window. The application of MPD techniques for cementing operations saved 5 days, the equivalent of $3.5 million, and eliminated the need to run an intermediate contingency 16-in. casing liner.
MPD techniques are not only beneficial for cementing or drilling operations but also as part of the abandonment phase. Tullow Oil, an operator in the North Sea, needed to re-enter and re-abandon a previously abandoned gas well (SPE 195718). Remotely operated vehicles revealed a leak through the 9⅝-in. casing, and laboratory tests confirmed the bubbles were reservoir gas. The operator concluded the installed cement plugs insufficiently isolated the reservoir from the environment and, if action was not taken, a high reservoir recharge potential existed.
Citing the costs, time, and risk associated with a traditional coiled tubing intervention, the operator opted for the recommendation to drill through the two cement plugs above a potential high-pressure zone to target depth. One plug rested at 1,074 ft (327 m) while the other sat at 6,162 ft (1867 m). To keep the pressure under control, the annular fluid returns were diverted away from the rig floor via a customized MPD spread featuring a rotating control device (RCD) to create a closed loop.
The team easily milled out the plugs and reached the target depth without any well control issues or lost-time incidents. The RCD controlled and diverted all the fluids and managed wellbore pressure during the standard operations of drilling, stripping, and making connections. Constant management kept the pressure within the predetermined safe limits during both static and dynamic conditions.
The MPD technology enabled drilling through the existing cement plugs and mitigating any risks from the trapped gas. Additionally, using the correct MPD equipment enabled drilling through both plugs without any plugged choke events. The subsequent re-plugging and re-abandoning operations lasted only 9 days, half the estimated 18 days that would be required using the conventional coiled tubing methods.
Shell needed to run and cement casing strings in the challenging deepwater conditions of the Gulf of Mexico (SPE 194554). What attracted the operator to consider MPD was this technology’s ability to precisely manipulate and manage the annular pressure using a statically underbalanced mud weight within a narrow pressure window.
For this situation, the operator assumed the pressure window at the toe of the casing string would be approximately 100 psi (0.6 MPa), yet downhole measurements revealed the actual window to be 50 psi (0.3 MPa) when losses were encountered while drilling the openhole section through the target reservoir. To overcome this challenge, the team needed to keep losses at an acceptable rate while simultaneously avoiding an influx or formation collapse.
Completions are another phase of oil and gas operations that can benefit from the techniques associated with managing pressure. Weatherford experts devised a plan to run the lower completion, displace the open hole, and perform an acid job. The openhole displacement would be the only operation where the open hole and the gravel-pack assembly were exposed to the circulation of the synthetic-based mud (SBM), openhole spacers, and the completion fluid. For a successful completion, MPD techniques were needed to maintain openhole stability and minimize losses, preventing ECD reduction at the heel and toe of the open hole. It was also imperative to keep the SBM from displacing down the work string as well as around the annular space between the open hole and the screens and gravel-pack assembly.
In combination with real-time downhole measurements, MPD enabled field personnel to deploy the sand-control screen to the target depth with minimal-to-no losses while maintaining complete control of the well, including openhole stability. The downhole pressure remained within the range of 9.15 ppg (1.10 SG) and 9.25 ppg (1.11 SG) with an 8.3 ppg (0.99 SG) mud weight. The open hole was displaced with kill-weight brine, successfully keeping losses to a minimum by managing both the surface backpressure as well as the downhole ECDs. The breaker was then pumped in two stages—heel-to-toe and then toe-to-heel—keeping losses low with a 9.15 ppg (1.10 SG) pressure and the choke at optimum position to avoid any restriction on the surface equipment.
The successful operation proved that the tools and techniques developed and used for managed-pressure drilling can improve efficiency and reduce risks during a lower completion operation in a tight-margin well. The same is true for well abandonment operations, cementing jobs, and a host of other operations commonly experienced on nearly every type of well. Managed-pressure technology is an adaptive, precise, and proactive means to control the annular-pressure profile, ensuring a stable wellbore and avoiding costly surprises across the entire life cycle of the well.
For Further Reading
SPE 200503 Successful Managed Pressure Cementing on an Exploratory Well Operation in Ultra-Deep Waters of Mexico by R. Bermudez, M. Arnone, et al.
SPE 195718 Novel RCD and MPD Techniques Enable Safe Re-Entry and Decommissioning of a Leaking Suspended Well by G.L. Carvalho, A. Adenipekun, S. Ignjatic, A. Hunter, T. Clay, and E. Stoian.
SPE 194554 Using Managed Pressure Drilling and Early Kick/Loss Detection System to Execute a Challenging Deepwater Completions Job in the Gulf of Mexico by J. Hernandez, M. Arnone, J. Valecillos, J. Vives, R. van Noort, D. Groves, and A. Hawthorn.
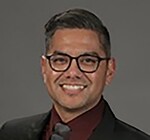
Rudy Flores is currently the US MPD operations manager for the drilling and evaluation group at Weatherford International. He began his career in underbalanced drilling with compressible multiphase fluids. Since beginning his career with Weatherford 14 years ago, he has worked with MPD/UBD technologies in various capacities including field engineer, field supervisor, project engineer, and technical manager. He holds a BS in petroleum engineering from Texas A&M University.
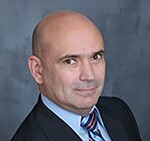
Maurizio Arnone is the MPD engineering and operational performance support team leader for Weatherford North America. He has 25 years of experience on drilling and drilling-related technologies and applications, working for operators and service providers across the oil and gas industry. For the past 16 years, he has been involved with different roles related with the application of MPD on land, shallow-, and deepwater areas with Weatherford, working directly in 19 countries and five continents across the globe. He holds BS and MS degrees in mechanical engineering from Universidad de Los Andes and Universidad Central de Venezuela, respectively, and an MS in mechanical engineering from University of Houston.
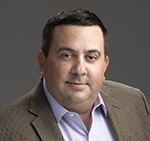
Chad Wuest is currently the global product line manager for intelligent MPD at Weatherford. He was previously global product line manager for offshore MPD and prior to this held several management positions in the Asia Pacific region, including operations and business development. He has been in the oil and gas industry for more than 24 years.