Hydrocarbon production losses resulting from parent-child well interactions during completion operations are a significant challenge in the Eagle Ford. A patent-pending rigless chemical frac hit remediation process was implemented in the Eagle Ford formation resulting in a 60% increase in oil production, a 30% increase in BOE reserves, and a payback in less than 4 months. A thorough engineering and lab study was conducted to design the process which addressed the damage mechanisms of capillary phase trapping, reduced hydrocarbon relative permeability, paraffin deposition, and minor scale deposition.
Background and Challenge
The Eagle Ford Shale play located across South Texas is a prolific unconventional resource producing approximately 967,000 BOPD and 6 Bcf/D of natural gas through 2021 (US Energy Information Administration). Like other unconventional reservoirs, Eagle Ford wells have high initial production rates but decline rapidly. Later-life production rates can significantly influence well economics and base production profitability.
Production in the Eagle Ford rapidly started increasing around 2010 with the implementation of horizontal drilling and hydraulic fracturing. However, as operators started to develop their acreage, they quickly turned to drilling of infill wells, also known as child wells. Lindsay et al. (SPE 189875) reported that by the beginning of 2015, the number of child wells being drilled in the Eagle Ford surpassed the number of existing or parent wells. This resulted in an acceleration of child-parent interactions, defined as interwell communication between the child and the parent during the fracturing of the child well. Known as fracture-driven interference or frac hits, these interactions have been of intense interest in the industry due to the potential degradation of production in both the parent and child well.
Miller et al. (SPE 180200) reported that in 1,210 instances studied in the Eagle Ford, the parent well experienced a negative production event approximately 41% of the time. Kairos Energy Services conducted a study on Eagle Ford parent wells that experienced negative production events from a frac hit to quantify the change in production. A total of six wells were analyzed where each had modern completions and were brought onto production in 2019 or later.
Decline curve analysis was run on both the oil and gas streams before the frac hit to generate a forecast to compare against actual post-frac-hit production. Actual and forecast production was averaged across the six wells and production responses were analyzed 6 months before and after the frac hit. Fig. 1 shows the forecast vs. actual cumulative production for both oil and gas, respectively.
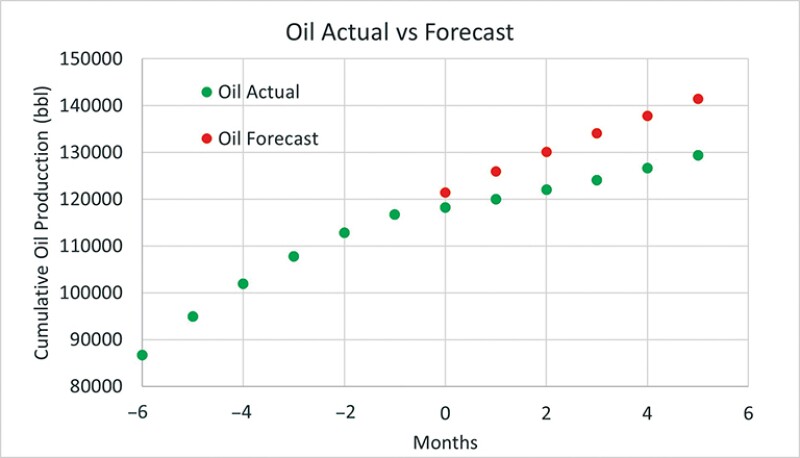
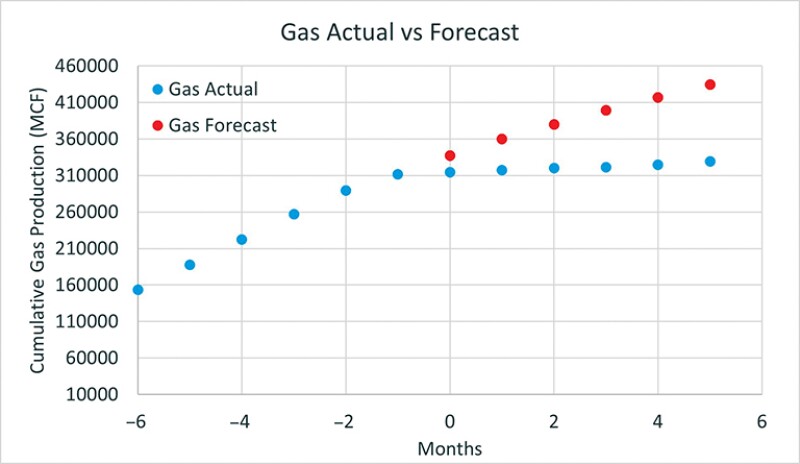
The divergence in production post frac hit can be clearly seen, resulting in an average per well loss of 20,500 bbl of oil and 245,000 Mcf of gas 6 months following the frac hit. All wells showed a significant increase in water production directly after the frac hit, indicating hydraulic communication. The gas/oil ratio (GOR) was significantly suppressed, decreasing from 4,820 ft3/bbl to 3,850 ft3/bbl 6 months post frac hit. The 30-day average water cut also showed a sustained change, increasing from 46% to 63% 6 months post frac hit.
Undoubtedly, a portion of the observed production loss can be attributed to lost or stolen reserves from the child well. Certainly, incompatibilities with frac fluids could be contributing to parent well damage including increased scaling tendencies, organic deposition, and negative reactions with polyacrylamide friction reducers. However, the sustained changes in both the GOR and water cut indicate changes in the flow dynamics at the parent well.
The large influx of water into the parent well’s depleted pore spaces and fractures will increase capillary pressure, resulting in water blocking and increasing water saturation, reducing hydrocarbon relative permeability. Also known as capillary phase trapping, this mechanism will reduce hydrocarbon flow and is worsened in the pressure-depleted parent wells vs. new wells. This data set, albeit relatively small, validates these sustained effects, resulting in reduced hydrocarbon production and lost reserves.
Candidate Selection
Kairos worked with a South Texas operator to identify a large inventory of existing wells that had experienced lost production from frac hits. The first candidate well was in La Salle County in the oil window of the Eagle Ford. The well has a perforated interval of 9,966 ft and was completed in April 2019 with 40 fracture stages, 20 million pounds of proppant, and 420,000 bbl of completion fluid. The well experienced a frac hit in December 2019, which reduced the estimated ultimate recovery (EUR) by 75% (Fig. 2).
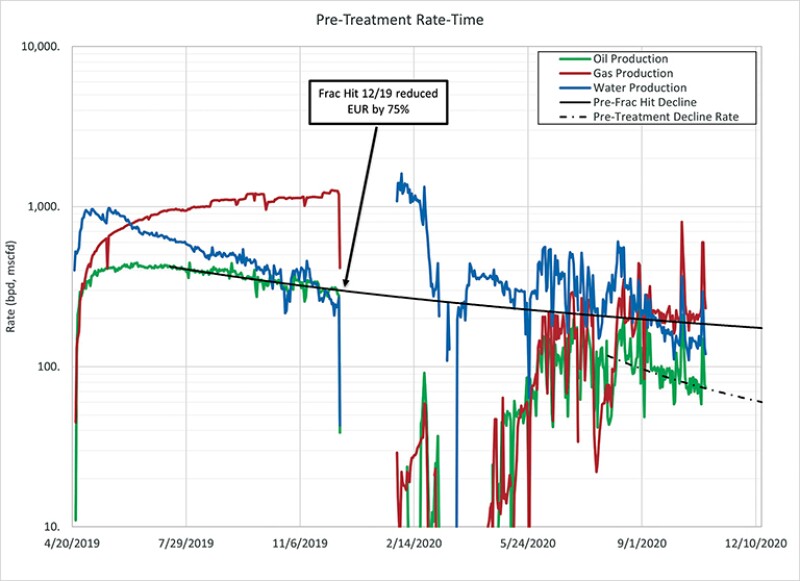
After the frac hit, hydrocarbon production slowly returned over an 8-month period. Oil production returned to approximately 150 BOPD, or approximately 50 BOPD below the forecast decline rate, and the gas rate returned to roughly one-sixth of the original rate. This proportionally larger reduction in gas than oil is consistent with the findings reported above and is in part due to the disproportionate effects of capillary phase trapping on gas production. Post-frac-hit oil production peaked at 150 BOPD and then went on a decline of 16% per month.
Kairos performed an engineering study and numerical simulation model showing the well had a good initial stimulated reservoir volume and sufficient current bottomhole pressure, indicating the well had good potential for enhancing production. This analysis combined with a thorough laboratory study allowed us to design a treatment to address the following mechanisms:
- Water block and poor relative permeability to oil and gas in the proppant pack
- Oil analysis showed wax content of 38%, indicating likelihood of paraffin deposition
- Scale modeling showed moderate acid-soluble scaling
Products were designed to address each of these mechanisms. For example, K-Flow 2002 was recommended to remove water block and improve relative permeability to oil. It comprises a proprietary mixture of carefully selected nanoparticles and surfactant combinations that are stable and effective at reservoir conditions. Fig. 3 shows that the product, diluted to 1 gal per thousand in fresh water, significantly increased the oil flow rate in a proppant pack as compared to fresh water. Furthermore, the interfacial tension (IFT) between the oil and water and surface tension between gas and water were measured and are also shown in Fig. 3. The IFT baseline was measured at 31.2 dyne/cm, and surface tension was 59 dyne/cm. Reducing these parameters is important to reduce capillary pressure and improve hydrocarbon relative permeability. The product met the goals of reducing IFT by an order of magnitude to approximately 10–1 dyne/cm and to cut surface tension by approximately 50%.
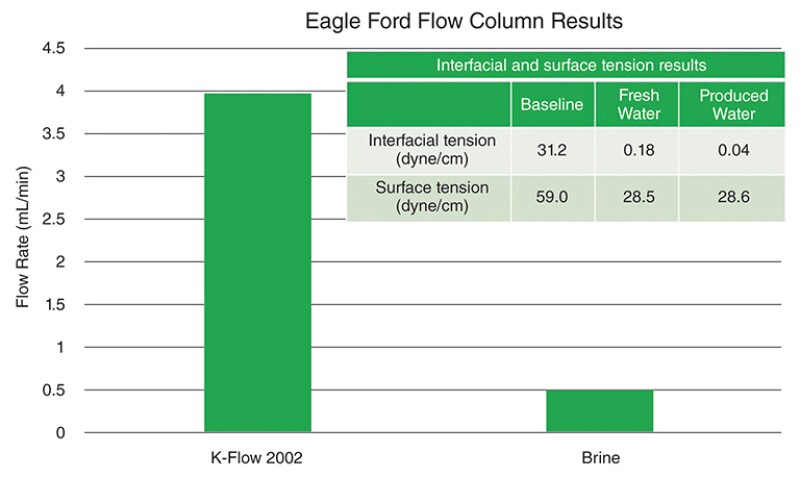
A synthetic acid was identified to dissolve scale, and a proprietary solvent package was utilized to de-oil scale and clean up paraffin deposition. A scale inhibitor and biocide were tested and chosen to ensure clean, protected fluid was being injected.
Design and Execution
The total treatment volume was slightly less than 10,000 bbl, which was designed based on the calculated propped fracture volume and the wellbore volume. The treatment volume is designed to contact both the wellbore and hydraulic fracture network. The treatment is divided into 10 stages. Each stage comprises the chemistry designed to remediate the identified damage mechanisms, and the stage volume is designed to target a certain number of fracture stages. In between each stage, a biodegradable diverter is deployed to distribute the fluid to the next set of target perforations. The well is on rod lift with a tubing anchor, and the treatment was designed to inject down the annulus at a rate of 8 bbl/min.
The full treatment volume was injected, and target pressure increases were observed on seven out of the nine diverter drops. The maximum allowable treatment pressure was reached approximately 50% into the treatment, and the injection rate was reduced slowly throughout the treatment to stay below the maximum treating pressure. Distinct pressure increases or rate reductions were observed on 77% of the diverter drops, validating the use of diversion in this application. No health, safety, or environmental events occurred during the job. The well was shut in for 48 hours, then returned to production, minimizing downtime.
Results
The rate vs. time plot shows after 6 months, oil production is up 60% over the post-frac-hit decline rate, and gas production has approximately doubled (Fig. 4). A step change down in oil and gas production is observed at day 775 and was due to an approximately three times increase in pipeline pressure. The rate vs. cumulative oil plot shows a 22% increase in oil EUR and incorporating the increased gas recovery, a 30% improvement in BOE EUR is forecast (Fig. 4). The treatment paid back in 4 months with a multiple of invested capital of 8.8 ($45/bbl of oil, $2/Mcf of gas).
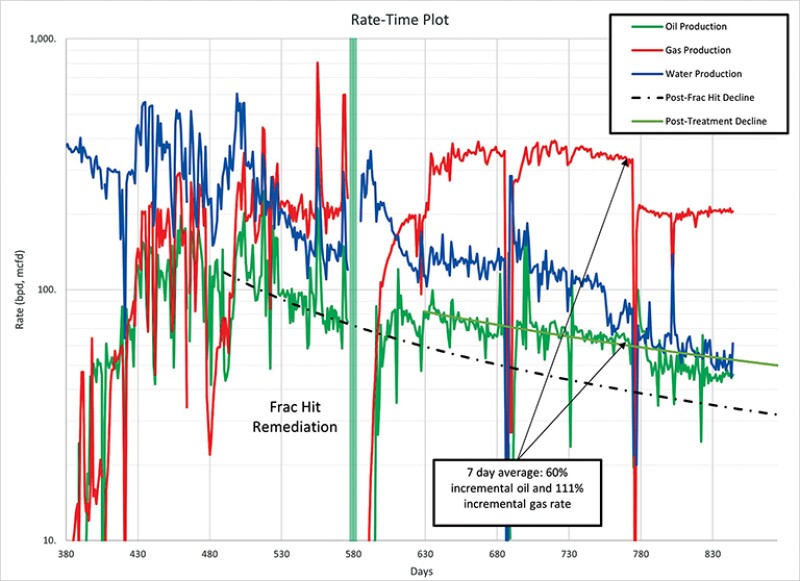
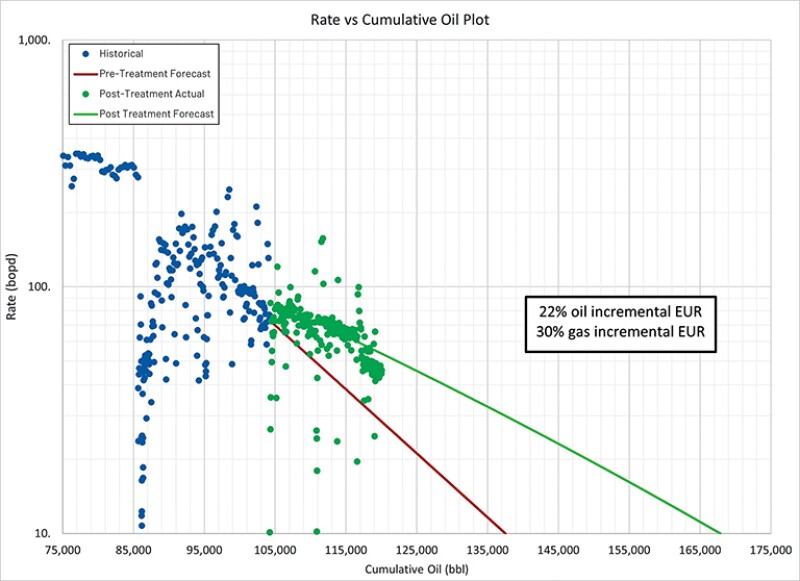
The operator is now evaluating additional wells and applications to commercially scale up the technology. This technology provides an economic avenue to capture a portion of the production and reserves loss following a frac hit.
For Further Reading
SPE 189875 Production Performance of Infill Horizontal Wells vs. Pre-Existing Wells in the Major US Unconventional Basins by G. Lindsay, G. Miller, T. Xu, et al., Schlumberger.
SPE 180200 Parent Well Refracturing: Economic Safety Nets in an Uneconomic Market by G. Miller, G. Lindsay, J. Baihly, et al., Schlumberger.