Many oil and gas companies are interested in exploring the potential of 3D but are unsure of what to make of the technology. A complete 3D model of an installation may look impressive, but, on its own, a model is no different from a map. And, like a map, a 3D model can quickly become outdated unless it is updated continually.
This is a common issue with computer-aided-design (CAD) drawings of assets, which often seem to be obsolete as soon as an asset is put into production. Modifications or changes to the asset, such as sagging under heavy loads, mean that companies still must conduct manual measurements. As a result, the CAD drawing simply cannot be trusted on their own. No matter how detailed the drawing, a static 3D model cannot capture the dynamic nature of operations at an installation.
A static model, however, is better than no model. In many cases, oil and gas companies simply do not have CAD drawings of their assets.
Photogrammetry offers a solution to these challenges. By stitching together images to create photorealistic 3D models, oil and gas companies—indeed companies in all heavy-asset industries—can create digital representations of the industrial reality at their installations.
While it may sound complicated, photogrammetry is actually a simple, low-cost technique for creating 3D models, and it can be accomplished by a single worker carrying a standard camera or operating a drone.
The process involves shooting high-quality images or video footage of the asset to be digitized, identifying and matching features that are visible across multiple images, and then using triangulation to turn the images into a 3D structure of the object (Fig. 1). The images also contain texture information about the asset, which can be added to the finished 3D models to make them photorealistic.
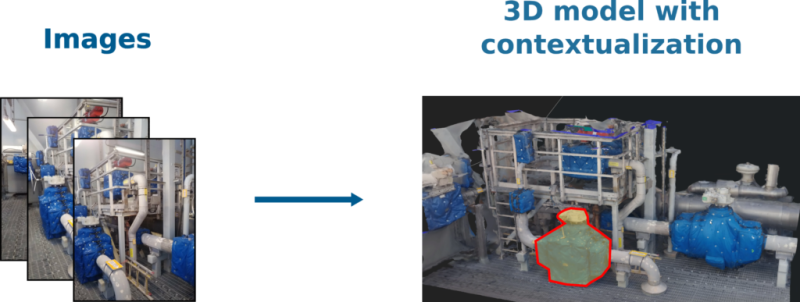
Fig. 1—An example of how images can be turned into
a 3D model.
Once rendered, the 3D models can be made available throughout a company as a part of every worker’s toolkit. Uses include
Photorealistic 3D models help workers familiarize themselves with their surroundings, giving them a powerful, up-to-date tool for navigating installations and locating equipment.
Companies can incorporate the 3D models into their planning work, virtually navigating the installation to determine the optimal path to a destination and seeing whether bulky equipment can be safely transported to the area where it is needed.
The 3D models can be useful for inspection work. As a company continues to capture new scans of its installations, engineers can also study the different scans to see how the condition of equipment changes over time.
The photorealistic 3D models can also complement CAD models; the two can be compared to detect changes in an environment.
More Data, More Context
Photorealistic 3D models on their own already offer several features that can benefit oil and gas and other heavy-asset companies. However, the real potential of 3D is unlocked when it is combined with different technologies in order to make data more accessible.
Live sensor data is an obvious candidate. By using computer vision to read all the asset tags visible in the images used to create a 3D model, a company can link all the data it collects about the different equipment captured by the model to their digital counterparts. The result is a photorealistic digital twin that reveals new insights about previously separate data sources.
This technology has a wealth of potential in the oil and gas industry. One example is a 3D model of an engine room on a floating production, storage, and offloading vessel, in which each component is clearly labeled with live-streamed data about pressure, temperature, and more. As long as the 3D model is kept up-to-date and the data collected is of sufficiently high quality, inspecting the engine room could be as simple as pulling up the model on a computer or smart device.
The up-to-date factor is one of the major obstacles keeping oil and gas companies from exploring photogrammetry. Having a worker walk around an installation and capture hundreds of pictures every day can be a full-time job in itself.
This is where automation can help. In the future, autonomous drones and robots could conduct daily photography rounds, navigating every nook and cranny of an installation to update the 3D models continuously. Applying computer vision to those models could help detect corrosion or a faulty cable, automatically add the potential issues to a work order, and notify engineers.
That future is not far off. Photogrammetry can be a piece of it, one part of a larger industrial digitalization strategy that aims to liberate data from its silos, connect it to other relevant information, and make it available to the workers who need it.
Oil and gas companies already can get a sneak peek of the digitalized future. All they need to do at this stage is grab a camera and head out into the field.