Two points stand out in the development and status of technology for production and facilities. The first is the amount of innovative ongoing work related to piping, pipelines, and materials for severe service. The second is the amount of work involving the use of digital simulations, including computational fluid dynamics (CFD).
Pipes are the arteries and veins of production and facilities, yet too few of us are concerned about their technical status. Fortunately, others among us are concerned about this topic. As oil production moves to increasingly hostile and remote environments, the need is increasing for reliable yet affordable pipeline technology that meets the demands of severe environments. Because of the scale and the environmental severity experienced by high-pressure/high-temperature (HP/HT) and other severe service, pipelines can be prohibitively expensive to duplicate in testing facilities. Research and development increasingly uses experience-validated digital simulations and modeling, sometimes synergistically. The technical community continues to respond to severe-service challenges with research and development on, for example, how to implement corrosion-resistant-alloy (CRA) technology, how to specify and use composite materials for pipelines, and how to better install and maintain piping (including deep-sea risers and subsea lines) constructed with conventional metallurgies.
Of the papers I considered for this feature, one reported on an investigation of the fatigue aspects of CRA welds for pipes in HP/HT service using finite-element analysis, while another reported on the development of an understanding of welding residual stress with the use of computational-welding-mechanics simulations. Another group of investigators provided an overview of research on the use of composite flowlines, risers, and pipework in offshore applications. An improved understanding of vortex-induced vibration was presented by another group of investigators, who used 3D dynamic CFD simulations. In a transition from the pipeline to facilities design, other investigators developed a methodology for sizing two-phase separators and slug catchers by use of a combination of dynamic pipeline modeling and CFD.
But the use of digital simulations and modeling does not stop here. Operator training and process safety are being enhanced by the use of plant simulators and virtual reality. Flow assurance is taken to a new level by the development of a fully compositional wax-deposition model to help explain the location and physical character of pipeline wax deposits.
Overall, it is clear that digital-simulation capabilities are quietly revolutionizing the way in which technology is developed and deployed within our industry. The fundamental understanding afforded by a variety of digital simulations is unprecedented and will continue, allowing for the rapid development and deployment of more-reliable, better-performing piping and facilities technologies.
This Month's Technical Papers
Composite Flowlines, Risers, and Pipework in Offshore Applications
A Plant Simulator To Enhance the Process Safety of Industrial Operators
Sizing Gas/Liquid Horizontal Separators Handling Nonstable Multiphase Streams
Additional Reading
OTC 24797 Modeling the Shearing Effect of Flowing Fluid and Wax Aging on Wax Deposition in Pipelines by Xiaohong Zhang, Infochem-KBC, et al.
OTC 25039 Welding Residual Stress and Pipeline Integrity by R. Törnqvist, DNV GL, et al.
OTC 25063 Numerical Studies of Vortex-Induced Vibration of a Circular Cylinder at High Reynolds Number by M. Mobassher Tofa, Universiti Teknologi Malaysia, et al.
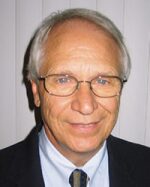
Ted Frankiewicz, SPE, has more than 30 years of experience with oilfield process systems and produced-water treatment. He holds a PhD degree in physical chemistry from the University of Chicago. Frankiewicz holds 15 patents. His experience includes hands-on operations, equipment design and manufacturing, and process engineering. Frankiewicz has worked for Occidental Petroleum, Unocal, Natco Group, and SPEC Services. At Unocal, he was responsible for developing water-treatment systems for the Gulf of Thailand to remove mercury and arsenic as well as residual oil from produced water. At SPEC Services, Frankiewicz designed equipment and process systems for, and diagnosed performance issues with, facilities and water-treatment systems internationally for major and independent operators. He was an SPE Distinguished Lecturer in 2009–10 and is a member of the JPT Editorial Committee.