Competition among drill-bit makers can be measured by the performance of a thin layer of industrial diamond. It is both the cutting edge of the tools, as well as the technology race among competitors seeking a competitive edge. The thumb-size cylinders made of tungsten carbide topped with a thin layer of industrial diamond are mounted in pockets in the heavy metal heads of fixed cutter bits, which have become a key product line.
The ability of these fixed cutters to efficiently grind through rock has quickly made diamond drill bits the dominant bit design, representing 80% of the footage drilled worldwide last year. That represents a rapid shift in buyer preferences in a market where bits using roller cones were once as dominant. That allowed Schlumberger’s Smith Bits to grab the largest share of a dynamic market where rivals such as Baker Hughes, National Oilwell Varco (NOV), and Halliburton see opportunities to move ahead if they can find new ways to significantly increase cutter performance.
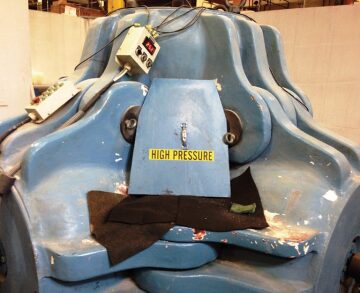
There are many factors in determining drill-bit success, but the one that gets the most attention is narrowing the performance gap between man-made and natural diamonds. Diamond bit demand growth has tracked the marked improvement in cutters. “Compared to the cutter of 10 years ago, a cutter today is 30 times more abrasion-resistant than they were. It wears 30 times slower,” said Rob Arfele, technology discipline manager for fixed cutter drill bits at Halliburton.
Given the marketing value of better cutters, companies are working on projects to continue this rapid pace of improvement. Achieving those gains will be a tall order. But there is plenty of room for performance improvement through better monitoring and control to prevent conditions that damage drill bits, he said.
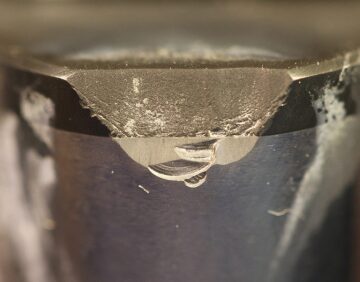
Customer focus on the longevity of industrial diamond on the tip of the cutter will ensure that drill-bit makers, and their diamond suppliers, continue to aggressively seek ways to make tougher industrial diamonds. “Drill bit and PDC cutter problems and challenges are well known to the industry. The first company to market with solutions is likely to capture and maintain a market advantage,” Arfele said.
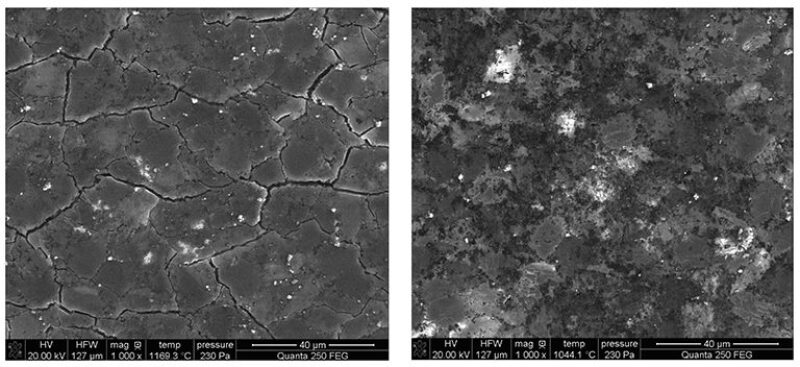
Unconventional onshore development has demanded mass production drilling, with efficiency measured by an ever declining number of days per well drilled. It puts a premium on longer drilling runs for cutters at a time when the force exerted by powerful new drilling rigs can generate extreme heat while grinding through rock. High temperatures can cause a polycrystalline diamond compact (PDC) to crack, oxidize, or turn into graphite, a soft form of carbon used in pencils.
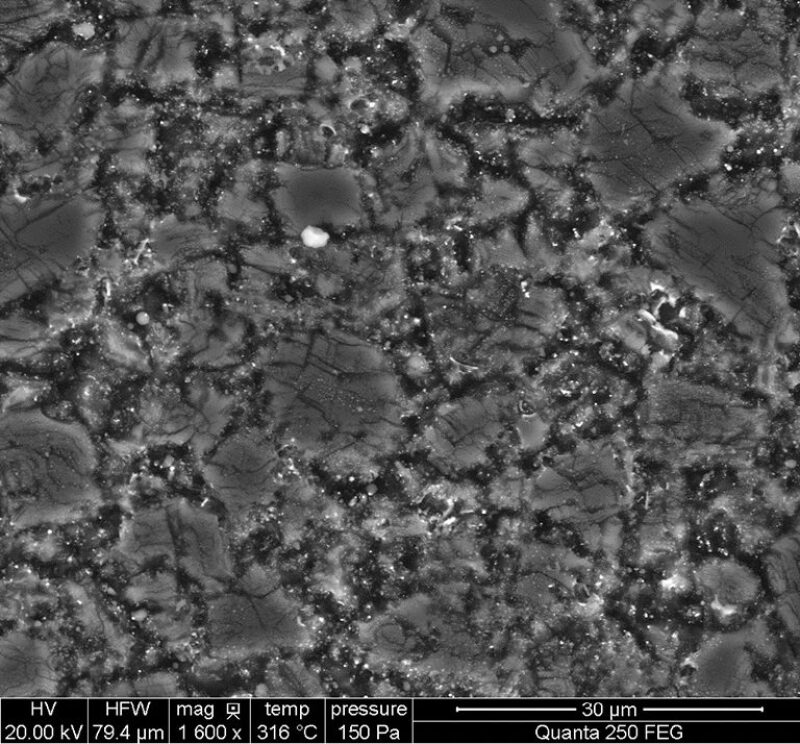
“The critical edge is the cutter tip. The edge experiences extremely high localized temperatures,” said David Zhan, research and development manager at National Oilwell Varco Materials Technology. He has been using scanning electron microscope imaging under reservoir conditions to study the causes of failure as it happens.
NOV and Baker Hughes offered a detailed look at how they are using advances in materials science to build tougher polycrystalline diamond-tipped cutters. Baker Hughes is working on using nanotechnology to re-engineer the molecular structure of the PDC to make it tougher.
“There is work being done around using nanomaterials to improve PDC performance,” said Aaron Dick, PDC Cutter team lead of the Baker Hughes Drill Bits product line.
A common target of the work is cobalt, a critical ingredient during manufacturing and a costly problem thereafter. “The PDC depends on a distributed network of crystal strongly bonded together. The trick is to get them bonded together using a metal catalyst, which is generally cobalt. It is also what bonds the table to substrate material (tungsten carbide),” said Anthony DiGiovanni, a diamond research scientist at Baker Hughes. “Without cobalt catalyst, you would need to apply more pressure and heat than are commercially viable today. The problem is the cobalt remains, and when it heats up due to the intense abrasion common during drilling, that metal expands far more than the diamond and it starts breaking it apart.”
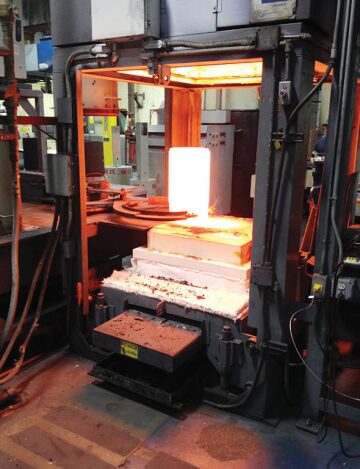
The expansion of cobalt causes cracks to develop, leading to failure. Using a scanning electron microscope, Zhan created movies showing what happens when PDC samples are heated under reservoir conditions. Ultimately the result is thermal failure, with irregular cracks appearing as the material darkens, turning the once uniform surface into something resembling the cracked mud at the bottom of a dried pond.
Leaching
There is a treatment for the problem: leaching out much of the cobalt by soaking the PDC in acid. But that has its limits—some of the metal is sealed in spaces the liquid cannot reach and is left behind—and it comes at a cost. Leaching was invented by NOV, which collects royalties on the process.
“The whole industry is working on (improved) leaching” methods or some other way to further reduce the effect of cobalt, DiGiovanni said. “One of the emerging technologies that will help improve cutter technology is nanotechnology.”
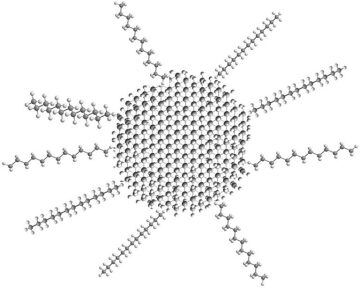
Throughout the industry, the goal is a PDC cutter able to stand up longer to the high heat generated while grinding through hard, variable formations. The rule of thumb in the industry is that heat causes damage in PDC above 750°C and leaching can push that limit to around 1,200°C. A company finding a cost-effective way to push those limits higher could gain a valuable edge.
Baker Hughes has invested in nanotechnology development to create diamonds with an internal structure that minimizes the “mechanical binder” (cobalt) left behind, according to an SPE paper. That paper and patent applications filed by the company describe how it could use a mixture of particle sizes—incredibly fine bits of nanomaterial, and grains of diamond that are hundreds of times larger. When bonded by heat and pressure the smaller grains will fill the space around the big ones, crowding out the cobalt.
Researchers at Baker Hughes have been working to find ways to turn advanced materials science research into an industrial process in partnership with Element Six, the industrial diamond-making arm of DeBeers, whose name is a reference to carbon’s place as the sixth element listed on the periodic table.
One milestone for the partners has been developing a way to handle the minute particles, whose size gives them unique properties that are useful in the final product and trouble while making it. They are extremely small, with particles less than 500 nm and possibly far smaller, which is one reason they are in the realm of nanotechnology. Things that tiny have a powerful attraction to each other relative to mass. To put it simply, they tend to clump and require treatment to keep them apart in solution.
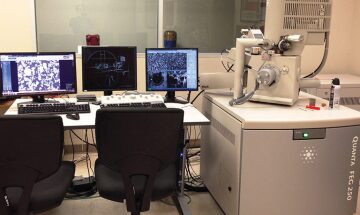
To overcome that obstacle, Baker Hughes had to find a way to “functionalize” them using a chemical coating that keeps them apart by balancing the natural attraction among the particles. In a jar full of water, the functionalized particles remain in solution for days. This is critical for diamond making because it allows the manufacturer to control the distribution of the nanoparticles in the finished product. Another option is the nanoparticles may also be functionalized in a way that attaches them to the larger particles, according to the patent application.
An experiment described in an SPE paper in 2012 used detonation nanodiamonds—carbon particles created by a controlled explosion and then processed to remove impurities. It allowed Baker Hughes to create a PDC cutter that has abrasion properties nearly as good as a leached diamond, according to the SPE paper. The paper predicted that as the cost of nanodiamonds goes down and production methods improve, this could be a way to improve drill bit performance.
Baker Hughes is working on a method that incorporates nanomaterials that will be predominantly diamond, but declines to offer details. The patent, filed in 2010, avoids offering a specific recipe for the process, leaving many options open. For example, the nanoparticles are said to “comprise at least one of a metal, a metal alloy, an intermetallic compound, a carbide, a nitride, and an oxide.”
While the company has made progress on nano-engineered diamond materials, it is a long-term effort. “It is extremely difficult,” DiGiovanni said. “There are a lot of challenges to overcome.”
Improved Analysis
While NOV is profiting from leaching and seeking ways to improve it, the company is also seeking other methods to reduce the problems caused by cobalt. In the past year, the company has been working to squeeze out more of the cobalt during manufacturing, Zhan said, adding the method is a trade secret.
Diamond properties can be managed by paying close attention to the quality of the raw materials, because “the diamond-diamond bond is very sensitive to any impurities,” Zhan said. How pressure is applied can affect the distribution of the cobalt, as does the size of the bits of diamond used to make it.
He has been comparing the particle size and a numerical ranking of strength, abrasion resistance, and thermal capacity, and has found there are trade-offs. He is always looking for ways to use less catalyst, perhaps ultrafine coatings on the diamond bits. “We can do better to minimize cobalt in the diamond table,” he said.
The path to better cutters will depend on improved failure analysis, Zhan said. Competitors in this business already spend a lot of energy examining used cutters to investigate what caused them to dull, which includes applying extreme magnification. Based on images made while heating PDC samples, he came to some conclusions that differed from the common wisdom.
Samples, which had not been leached, failed at significantly higher temperatures than commonly thought—around 1,000°C—and leached PDC began to come apart at 1,250°C. Both tests were done in a low vacuum and Zhan said the presence of oxygen would likely cause failure at a lower temperature. For that reason, he suspects that attaching cutters to drill bit heads using “vacuum cutter brazing” could reduce the risk of microcracks that could cause early failure.
When he examined the failure of cutters that had been leached, microcracks appeared within the diamond grains. According to Zhan, that is an indication that the diamond is being turned into graphite, indicating that graphitization may be more common than widely assumed.
Zhan said all of those may reveal problems offering avenues for making better cutters. “Cutter material characterization is the key to the next generation of cutter development,” he said.