In one of the operator’s Malaysian fields, hydrodynamic slugging, or two-phase liquid/gas flow instability in the pipeline, has caused losses in flow capacity and intense vibration at the separator, leading to integrity issues. To understand how the behavior of foams in a pipeline affect or alleviate slugging performances, foam behavior was simulated using the OLGA (short for “oil and gas”) simulator, a commercial dynamic multiphase-flow-simulation software. This study showed that foams were able to slow gas velocity and diminish liquid fluctuations, thus reducing slugging in a problematic pipeline.
Challenges Posed by Slugging
Hydrodynamic slugging or instability of waves at certain liquid/gas flow rates in the pipeline were concerns in several fields in Malaysia. In one such field, almost 50% of the loss in flow capacity (i.e., liquid holdup) from a producing pipeline was the result of slugging, causing gas‑production deferments of as much as 30 million scf/D. Severe vibrations from the pipeline to the separator often were felt at the platform, leading to questions about the mechanical integrity of the separator and anticipated high maintenance costs.
The issues of slugging can be solved with the use of foams introduced into the pipeline to slow down gas velocity and enhance mixture with liquid.
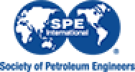