Picture this: pump schematics floating in the line of sight of the technician who’s about to maintain a pump on the Vito production platform. It’s not science fiction. It’s augmented reality (AR), and it’s one of several technologies Shell is relying on to enhance the way workers carry out their tasks.
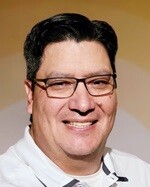
HoloLens AR headsets, digital twins, wireless sensors, and iPads are key components of Shell’s digital worker initiative, Colin Muirhead, information digital technology manager for Shell’s Gulf of America assets, told JPT.
The combination of technologies is “allowing our operators to make the best use of their time and to really limit the safety exposure,” he said.
The Class1, Division 2 AR headsets fit on top of a hard hat to make what Shell refers to as “remote assist” possible. When the HoloLens user joins a Teams call, other meeting participants can see what the user is seeing. Meeting participants also can put drawings and more in the user’s field of vision, he said.
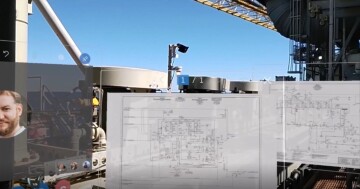
“It provides a real collaborative experience, both on the troubleshooting side, inspections, and other opportunities that you don’t really get with standard video and standard engagement,” Muirhead said.
The AR headsets not only streamline maintenance work but also speed up commissioning and inspection timelines. He said Shell started using the headsets while Vito was under construction at Kiewit Offshore Services in Ingleside, Texas, to minimize travel to the fabrication yard for activities such as internal inspections.
The operator ran an AR headset pilot project and evaluated virtual reality (VR) and extended reality (XR) technology at the Vito platform to improve safety for workers, enable work via remote and hands-free collaboration, save time and costs on travel, and reduce offshore trips to the platform, according to Shell-authored paper OTC 32496, which details the Vito operating model as well as startup and ramp-up activities.
Muirhead said the more work that Shell can link to remote operations, the greater the cost advantage. He highlighted the potential to transfer tasks to onshore staff for remote management or to oversee the work being conducted remotely.
“It also creates reduced safety exposure by not having to fly people on helicopters offshore or be in harm’s way while work is being done offshore,” he said.
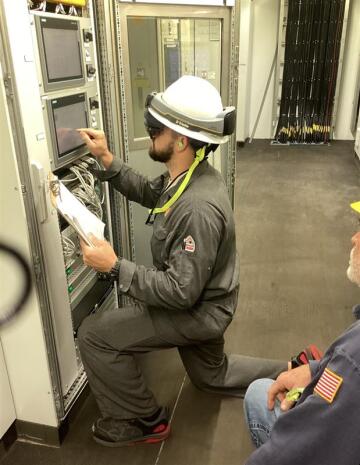
The Vito production semisubmersible, which reached first oil in February 2023, is a template for two other Gulf projects: Whale, which began production in January, and Sparta, which is expected onstream in 2028.
Vito features a smaller, simplified design, but that also means fewer personnel onboard (POB), Muirhead said.
“A normal asset in the Gulf of America would have somewhere over 100 POB at any given day. Vito is different. Vito has a maximum of 60 POB, so this starts to create a little bit of a different way of working that’s required to operate the asset, and this is where we start to get our digital worker,” he said.
Remote Inspections
He said inspectors from the US Bureau of Safety and Environmental Enforcement (BSEE) have been able to remotely inspect offshore facilities while a Shell worker equipped with a HoloLens headset demonstrated the area in question. It started with a pressurized welding enclosure, which BSEE must inspect before offshore welding occurs.
“It’s an inspection that takes 30 minutes to do, but it takes you a day to fly somebody out there and a helicopter flight. And then it’s a quick inspection, and then they leave,” he said. “We got some inspectors with BSEE to start doing these remotely using HoloLens. And it turns out it’s really a win-win for us because they don’t have to fly out there and spend their time on helicopters and coming out. And we get a faster turnaround on some of these inspections that allows us to get to the work faster.”
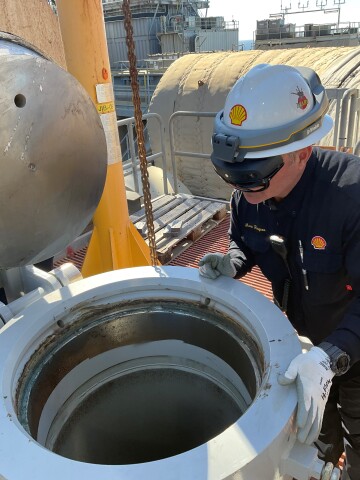
At another platform, BSEE needed to inspect changes to the gas lift system before a well at the Ursa platform could resume production, but weather was going to delay a trip to the facility by 2 or 3 days. BSEE agreed to a remote inspection.
“They used the interactive capability of HoloLens to do this inspection, where you can see the operator showing him what was done, the line that was impacted, and then he drew on it in his field of vision,” Muirhead said. “This is the piece that was changed, and it was circled in the vision so you could see easily around what was done there.”
That inspection made it possible to get the well onstream “2 to 3 days ahead of when we would have got it on” if a BSEE inspector had gone in person.
“For us, that’s hundreds of thousands of dollars in value and production that was unlocked because we were able to do that,” he said.
Powerful Combos
When the AR headsets are used in conjunction with a digital twin, a worker has all the available information about that asset at their fingertips. “It gives you a real sense of what’s happening at the asset,” Muirhead said.
It also sometimes yields unexpected value. When an offshore support engineer needed to locate a particular bleed valve on Vito, she turned to the digital twin. But the digital twin bleed valve and the real-world bleed valve didn’t match.
Muirhead recalled, “She looked at it, and said, ‘That handle is on the wrong side.’ ”
Investigation revealed that the incorrect valve had been installed, which could have resulted in system damage amounting to hundreds of thousands of dollars. By identifying the issue, a correction was made before any damage occurred, he explained.
“Our aspirations for the digital twin are that it really becomes the operations cockpit, so to speak, for the asset. That means bringing in other pieces of data that you can then see at your fingertips,” he said.
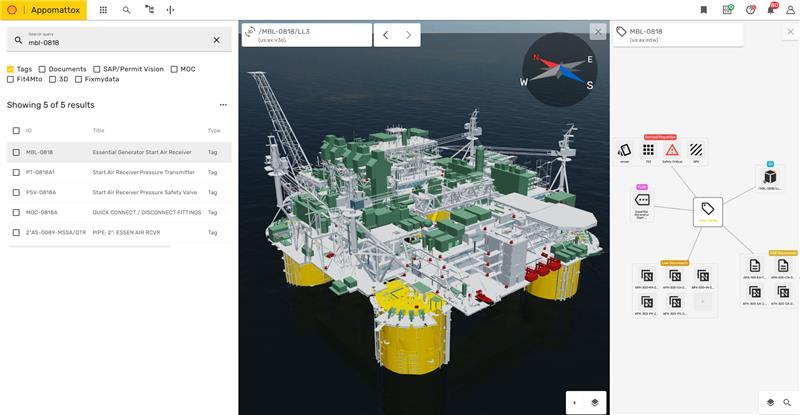
Shell has equipped each of its operated platforms in the Gulf with a HoloLens headset and has implemented the digital twin technology on its eight newest platforms in the region.
Shell is quickly increasing its use of wireless sensors because they provide a cost-effective method for collecting more data on offshore facilities, Muirhead said, adding that this information can be integrated into digital twins.
At Ursa, offshore workers had to read and record pressure gauge data manually on their iPads to assess whether any action was required.
“That took somewhere in the realm of 2 hours to do the work, and that’s a person that has to spend time going and doing that,” Muirhead said.
Now, with wireless sensors on the pressure gauges, data is automatically fed into the reporting systems and triggers an alert when the reading falls outside of the acceptable range.
“We’re optimizing our operations on deck, and we’re allowing our operators to go where the work is needed, not just to make a round to go check on something,” he said.
Muirhead added that the use of Class 1, Division 2 iPads, introduced about 7 years ago, “certainly is going to be a staple for us going forward for our assets in the Gulf of America.”
The combination of technologies is not just making a difference in the Gulf but is expanding to the company’s global operations.
For Further Reading
OTC 32496 Vito Operating Model and Startup Ramp Up (SURU) by J. Rincon, I. Greenlee, R. Hamerski, J. Rayborn, Shell Exploration & Production Company, et al.