Silviu Livescu, the technical director for SPE’s Digital Science and Engineering Analytics (DSEA) discipline, asked me whether the unprecedented ability to identify underperforming wells and the rebound in wellhead oil and gas prices has led to a boom in well remediation activities (e.g., well cleanouts, reperforation, acidization, refracturing, and sidetracking).
To be honest, I don’t know. But I don’t think remediation activities have increased much over the prepandemic levels.
Rehabilitating underperforming or inactive wells, or strings, should be the normal response to “relatively good” product prices. The methodologies will vary from one operator to another, with the capabilities of the local service providers or the mobilization costs for state-of-the-art tools.
I have always been fascinated by the intellectual challenges around skin damage identification and business opportunities that cost-effective, low-risk remediation techniques represent for adding incremental asset value.
The insidious deterioration in inflow performance is often masked or complicated by other reservoir-related processes. Moreover, while the asset is contract-, facility- or equipment-limited, there is only a weak business case to maximize the inflow performance relationship or injectivity indices.
Moreover, there may be better, low-risk, modest-cost opportunities to optimize the production system using an integrated production model (IPM) or modern process controls. Nevertheless, the process of building the IPM will often result in an inventory of wells for which performance is deemed to be “low or off.” This inventory will include opportunities to add value by extending the plateau or accelerating resource recovery. Moreover, there is always a small element of capture in having the wells decline more acutely into the economic limit (Fig. 1).
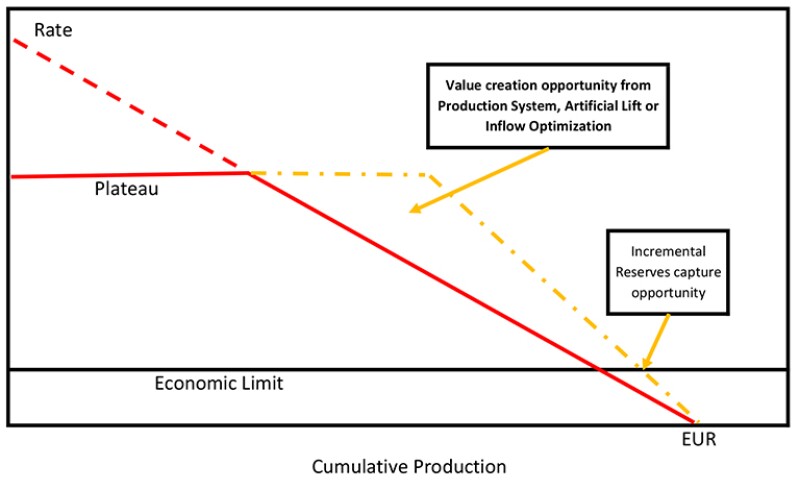
DSEA algorithms offer a great way of ranking these value-creation opportunities and sequencing well-servicing campaigns. The ranking criteria will depend on the decision metrics used by the specific operators and their joint-venture partners and, possibly, based on the terms in the production-sharing agreement. This is a good reason for production and facilities generalists to keep abreast with modern decision analysis technologies via the SPE Management Technical Section.
My first inclination has always been to check for fill in underperforming producers and injectors with modest well inclinations. Accumulated fill can result in partial penetration skin or a reduction in the effectively drained permeability thickness (kh). Over my career, I have seen significant uplift from simple wellbore and perforation or sand-control device cleaning operations.
However, holdup depth measurements are quite an expensive exercise on high-angle or near-horizontal wells. Where equipment and crew mobilization costs dominate, problem investigation and diagnosis plans need to include a decision tree on what else should be done while the coiled tubing or downhole tractor is still on location, potentially including the entire first-stage remediation program.
Nevertheless, some of the dumbest decisions that I have made related to not putting enough thought into the design of solids, gunk, or scale cleanout operations include:
- Underestimating the complexity of the challenges or the risks with local standard practices
- Inadequate jetting or lifting velocities below the tubing shoe
- Failure to approximate the reservoir pressure or to use a suitable, easily removed, nondamaging loss circulation material to control the fluid losses during reverse-out operations
- Selecting a bottomhole assembly that was too large or stiff to get through buckled sections of the tubing or applying inadequate annulus pressure to limit incremental buckling during flow
- Failing to grab or analyze samples of recovered materials for root-cause analysis and repeat-treatment risk mitigation
- Reluctance to run a value of information (VOI) assessment on the use of more-expensive tools or techniques (e.g., e-line or smart coil, larger outside diameter coiled tubing, or a downhole camera)
- Failure to rerun these VOI assessments when things start to go wrong
- Inadequate contingency funds, planning, or spare parts and fishing tools within a reasonable mobilization time under standard or agreed contract terms
- Inadequate auditing of the qualifications and experience of the on-site supervisors
- A poor process in passing the baton from the job design team to the execution team
I suspect that there are now machine-learning-driven remediation program design tools to help the service company personnel avoid many of these stumbling blocks.
Moreover, we know that problems can be minimized by the operator funding a multifunctional exercise to run through the jobs on paper and conduct a hazard identification or risk mitigation exercise with the service company personnel and in-field job supervisors. (Obviously, this is even more effective if it builds on the lessons captured during the last campaign.) The expression “an ounce of prevention is worth a pound of cure” dates to the 13th century and was popularized by Benjamin Franklin in the 1700s.
Automated decline cure or rate-time analysis and integrated production performance models (e.g., PERFORM, PIPESIM, PROSPER, SAM, Wellflo, Wellflow, and WEM) can help identify these well-performance problems and the uplift opportunities. VOI analysis also can be preprogrammed and used to determine if a single or multirate test or production-logging operation will improve the probability of success or identifying the optimal pathway to the optimal remediation program.
The well-performance analysis tools can then be tuned to the actual flowing bottomhole pressures at the tested rates.

The well shown in Fig. 2 had tested at 425 Mscf/D at 500 psi wellhead pressure with a total skin of +5 and a ΔP skin of >1,000 psi. The reservoir management team (RMT) had expected a modest negative skin from this completion. This information begs lots of questions and seeds a brainstorming session by the RMT.
- What is the most likely root cause of this unexpected behavior?
- A modest skin frac or a short, u-shaped sidetrack might achieve an effective skin of –5 and an initial rate of over 1.8 MMscf/D.
- With less risk and investment, it might be possible to double the rate and achieve a modest negative skin by reperforating with modern state-of-the-art guns or with a propellent-powered water-hammer treatment (as discussed in SPE 68920).
- What about new coiled tubing supported stimulation treatments or pinpoint acid treatments?
- What other low-cost/low-risk options have emerged since the turn of the century?
Note that the inflow performance ratios for this well are so steep that incremental compression will currently add only a modest uplift at the current reservoir pressures.
A remediation project should follow the normal project management process by weighing up the available technical options in Stage 2 (Fig. 3). This review needs to include the HSE, technical and commercial risks and evaluate the available risk-management options.

It is also important to recognize that the RMT may have set constraints on the maximum effective drawdown beyond the damaged zone, the optimal producing gas/oil ratios or water/oil ratios at any given cumulative production volume, or pattern voidage replacement ratios.
As Amir Al-Wazzan, production assurance manager for technology deployment and innovation at Dragon Oil, pointed out to me, the decision on whether to select a conventional or cutting-edge remediation technology will depend on the resources available from the local service providers and the costs and perceived risks involved in mobilizing, deploying, and using the latest technologies. In many cases, it is highly attractive to use familiar, proven technologies to clean out, revitalize, and re-equip idle wells or underperforming wells. Workovers may offer greater upside, but the options may be limited by the available budget and the perceived HSE or well integrity risks.
Pilot testing of new technologies needs to be benchmarked against providing an equal effort into optimizing and supervising well-established approaches for well remediation in a specific asset and region. Nevertheless, as Livescu suggested, data mining and modern data analysis techniques allow us to do a much better job in finding good field analogies where new approaches to well remediation and restimulation have proven to have a high probability of commercial success.
Dan Hill, professor at the College of Engineering at Texas A&M, said in the promotional SPE Live for his 2022–2023 Distinguished Lecture “Acid Stimulation of Carbonate Formations: Matrix Acidizing or Acid Fracturing?” that most carbonates are so acid soluble that achieving a negative skin should be relatively easy. His talk presents a relatively simple methodology for evaluating whether to attempt an acid fracture stimulation or a complex wormhole configuration with a well-executed matrix acid treatment. This decision depends on the rock properties and closure stress, which will vary with depth and with reservoir pressure decline.
I am eager for the opportunity to see the entire presentation and ask questions about
- Cost-effective options for effective diversion, especially in a remedial setting
- How to limit acid leakoff because of wormholing during acid fracturing operations
- The best option for treating dirty, back-reef carbonates or carbonate-cemented, moderate-to-low-permeability sandstones
- What the application areas are for combinations of acid and propped fracturing
- His thoughts on the recent discussion on SPE Connect about the desirability of a tubing cleaning and pickling treatment before an acid stimulation
In Schlumberger’s SPE Tech Talk“New Single-Stage Sandstone Acidizing Solution—High Efficiency and Low Risk,” Pedro Artola and Temi Yusuf pointed out that this proprietary one-step acid blend provides a low-risk, low-volume, cost-effective method to stimulate sandstone reservoirs containing less than 20% carbonates. The blend is specifically designed to avoid the overspending challenges with conventional low-strength, mud acid treatments at temperatures of up to 150°C. A single fluid also helps reduce treatment complexity in multistage treatments in treating zones with more than 6 m of net pay, where diversion is required.
I have also found it quite challenging to identify the most cost-effective options for treating underperforming or damaged water-injection and saltwater disposal wells. The root causes on injection-well damage will generally depend on the water-plant and wellhead filtration strategy, the nature of any water treatment deficiencies, the nature and frequency of process upsets, and the corrosion or fluid-scaling tendencies that often vary over the life of the asset.
In well-established injection wells, this likely involves damage to the thermally induced fractures, rather than being restricted to the perforation tunnels. With thick pay zones, this poses significant treatment diversion challenges. Moreover, in high-angle or near-horizontal injection wells, there will likely be multiple, near-parallel fractures, only a few of which will control the well performance.
In any event, it is often necessary to conduct at least part of the treatment close to the pressure limits of the completion or wellhead and, potentially, at the fracture propagation pressure.
The SPE Production and Facilities Advisory Committee have been discussing the need for additional, vertically integrated, specialized events on well remediation to disseminate the latest experience and experience in pilot testing of new technologies. However, it is possible that these topics are adequately covered by presentations at SPE regional workshops or the larger sections (such as Saudi, Gulf Coast, Aberdeen/Stavanger, and Brazil) and at cross-functional events such as SPE's Annual Technical Conference and Exhibition, the International Petroleum Technology Conference, regional Offshore Technology Conference events, and Offshore Europe.
To avoid overlap in this content and competition for sponsorship dollars and quality papers and presentations, I have started a discussion chain on SPE Connect to solicit your input.