This paper provides an overview of an engineering-design methodology that can be followed for tubular-equipment sizing and selection for use in complex wells. A typical list of reservoir and well parameters required to set up the well model for thermal and stress-loading analysis is presented. Furthermore, a full well-casing and tubing-design-integrity analysis is performed on a complex, high-rate, high-pressure/high-temperature (HP/HT) example well with various anticipated operating loads.
Introduction
The purpose of tubular-design analysis and validation is to analyze tubing loads, design integrity, and buckling behavior under complex mechanical- and thermal-loading conditions, as well as fluid pressure effects. It is very important to perform thermal and pressure analysis for a well and then to use estimated temperature and pressure profiles in a tubular-stress analysis in well-completion designs. This is true for any well completion and is especially important in HP/HT wells, deepwater wells, and subsea wells (with emphasis on recognition of annulus fluid expansion). Thermal and stress analysis helps to estimate whether the proposed or existing completion for the well is fit for purpose when subjected to varying well-operating conditions during the life of the well. Therefore, for a proper completion design, it is critical that this analysis be performed while the completion is still in the planning stage.
Tubing-Size Selection Through Nodal Analysis
An analytical approach or nodal analysis of a production system provides a graphical means of representing the capability of a well to produce (or inject) fluids. Tubing is considered the most significant component of the overall production system of a well. Hence, tubing selection, or, more specifically, tubing-size selection, is critical to ensuring that the production (or injection) of the well will be efficient.
The primary goal of tubing-size selection is to ensure that production (or injection) targets can be met. Various completion types can be examined as part of this process as well (e.g., conventional completions, selective completions, intelligent-well completions, and artificial-lift completions). Nodal analysis provides a graphical representation of how pressure will change with flow rate or depth. The most common graphical representation is a reservoir inflow-performance curve combined with an associated tubing-performance curve. Using this graphical representation, the optimal tubing-size selection can be determined for a well (HP/HT or otherwise). The graphical representations can be plotted against each other for a comparison of relative performance.
In general, more than three-quarters of the total available energy of the well is spent moving the well fluid from the bottom of the well to the top. Hence, the tubing-size selection is an important first step. However, it should be noted that other factors such as well deviation, multiphase flow, flowline size (and length), surface-choke effects, and separator conditions can be significant in the nodal analysis as well. For purposes of this paper, however, these additional factors will not be discussed.
The tubing-size selection is initiated with the well and reservoir information. The required data include (but are not limited to) the well-casing plan, well trajectory, well-fluid properties, bottomhole temperature and pressure, well productivity, permeability, and target production and injection rates. If a completion type is already being considered, the planned well-completion schematic with the completion type and packer locations would be a starting point for the nodal analysis. It should be noted that this step in the analysis will result in tubing size only.
Methodology for Thermal and Stress Analysis
A well model is created in a thermal-and-stress-analysis software program with given well details. Tubing-design analysis is carried out in sequence by first performing thermal and pressure modeling of the entire tubing string using suggested operational-load scenarios (operational scenarios typically are provided by the well or asset owner). Typical operational-load scenarios include circulation, injection, production, shut-in (with varying lengths of time), and stimulation operations.
Output from the thermal simulation is used by the software in the calculation of pressure profiles along well depth. Estimated pressure profiles are used as part of the selection process not only for the tubulars but also for the tubing-material selection, packer selection, seal-assembly design, design of surface facilities, and design of stimulation treatments. Because annular-pressure expansion is a key factor for HP/HT wells, it will rely heavily on this thermal simulation.
The simulated thermal analysis and pressure profiles are then accessed for complex and detailed tubing-stress analysis. The accessed results are then analyzed to validate that the simulated load scenarios are within manufacturers’ stated tubing-design criteria and packer-operating limits.
If free-to-move tubing is part of the completion design, then tubing movement also is estimated to ensure that movement is within proposed/allowable sealbore length (if used). In addition, annular-pressure buildup in the annuli is estimated to ensure it is within allowable tubular (tubing/casing) design limits.
If simulated resultant parameters exceed tubing/casing allowable strength (burst, collapse, axial, triaxial), then a sensitivity analysis is carried out either to select suitable casing/tubing or to prevent tubing-load conditions from exceeding design limits by establishing constraints or controls in previously simulated operational-load scenarios.
Case Study: Tubing-Design Analysis for an HP/HT Well
To illustrate the process better, an example analysis of an HP/HT well is shown here. The conditions for this example well include the following:
- Vertical HP/HT well; platform-based
- Deep water (1400-m water depth)
- N2 in the production riser
- Completion brine between the mudline and production packer
- Reservoir pressure of 11,000 psi
- Reservoir temperature of 300°F
- Gas producer (target production of 80 MMscf/D).
The tubing and packer-design analysis is performed under various standard well-operating scenarios (tubing loads) per the operator’s tubing-design requirements. Different operators will employ varying degrees of safety factors in the design of their tubulars, and these safety factors should be honored as part of the design.
Discussion of Example-Well Case-Study Results
Simulated thermal and pressure profiles along the well will guide the temperature and pressure rating for the equipment that may be required for well completion during the well-planning stage (Fig. 1 and Fig. 2). A critical area of focus is the use of this temperature- and pressure-profile information in calculating tubular stress and annular-pressure buildup (APB). Metallurgists also can use the temperature- and pressure-profile information to estimate the potential for corrosion for the metallurgy selected for the downhole equipment.
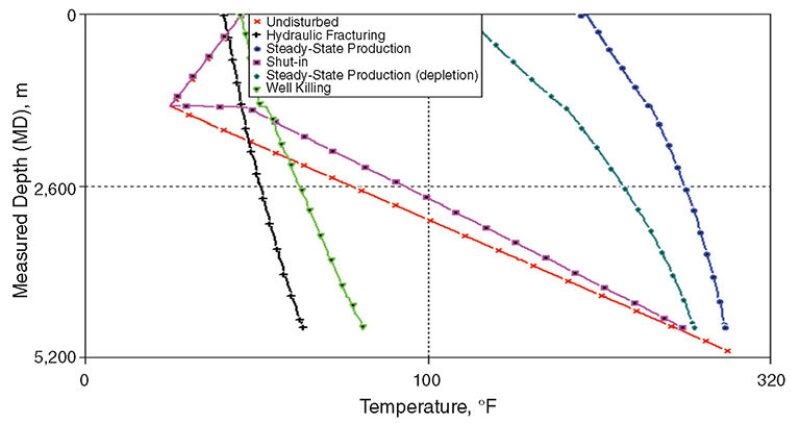

Selection of the proper metallurgy is a relatively mature process with respect to corrosion performance. The relatively large capital expenditures for high-nickel-alloy-content materials make proper selection of metallurgy a huge consideration for HP/HT wells. In addition to standard industry practices, previous knowledge of reservoirs in a particular area also can play a vital role in the proper selection of completion-equipment materials and metallurgy.
Once the temperature and pressure profiles have been constructed for varying well-flow injection and circulation operations, tubing- and packer-stress analysis is performed to estimate the associated axial forces and differential pressures. The objective of this step is to analyze whether the tubing and the packer are within the selected design limits (relevant design envelopes) when subjected to any of the previously mentioned well-operating scenarios.
Observation of the tubing-stress analysis indicates that the pressure-test-tubing operational scenario is outside of the design limit for the selected tubing. In addition, observation of the packer envelope indicates that the “pressure-test-tubing” and “tubing-evacuation” operational scenarios also are outside the limits of the packer-operational-envelope limits.
Optimizing the Example-Well Completion Design
The operational scenarios are outside the stress limits that were first selected for the tubing and packer. To optimize the design, the same size tubing was selected (as determined by the nodal analysis), but a higher grade of tubing was used. Also, a different packer with a larger operating envelope that could accommodate the simulated loads was selected.
If a packer with a larger operating envelope (i.e., a different packer) is not available or feasible, this scenario possibly could be tackled by implementing a strategy for well-completion-landing conditions (i.e., landing the completion in compression or tension). If the tubing is not attached to the packer, then the length of the sealbore might need to be changed to compensate for the anticipated tubing movement. In addition, various other completion strategies or combinations can be investigated to keep tubing/packer loads and tubing movement within allowable design limits, because other scenarios might be responsible for the current unacceptable conditions. These could include landing the completion in tension or compression, latching the tubing to the production packer, or applying pressure in the annulus during high-potential-load scenarios that may lead to exceeding the design limits.
APB for Casing-Design Validation
Once the thermal and stress analyses for the packer and the tubing have been determined, a critical area of concern for HP/HT wells is APB. This is even more critical in subsea wells where venting options are not possible or, at best, are severely limited. APB is usually the result of
- Temperature changes, primarily during well flow
- Hot-fluid injection that can cause fluid expansion
- Confined annular fluids that will generate pressure buildup because of fluid expansion
- A great temperature difference from bottomhole to surface that increases the likelihood of APB (e.g., HP/HT wells)
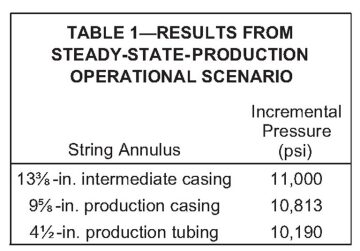
Given here is a scenario in the example well that illustrates the potential effects of APB. Table 1 presents the results from the steady-state-production operational scenario. Fig. 3 and Fig. 4 are the associated APB plots for the example well during this operational scenario. As noted in the table, the annular pressures of the 9⅝- and 13⅜-in.-casing segments exceeded the burst ratings of those casings. The failures are noted graphically in Figs. 3 and 4 by the pink line exceeding the envelope stress circles. To prevent this pressure buildup from creating a problem in this well, certain operational procedures can be planned to relieve pressure buildup in the annuli. However, in cases where pressure bleedoff cannot be achieved, upgrading the casing weight/grade to one with higher-mechanical-strength properties during the well-planning stage to ensure that casing failure does not occur during well life may be considered. Additionally, multistring-casing designs or variations to the top-of-cement locations also can be considered.

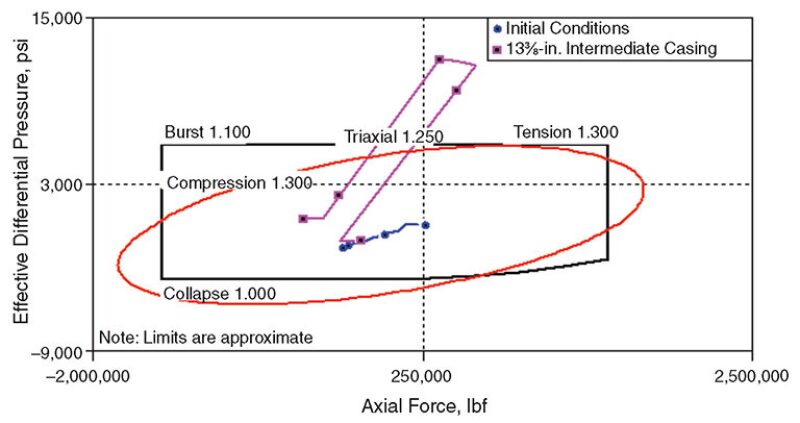
This article, written by JPT Technology Editor Chris Carpenter, contains highlights of paper OTC 24852, “Importance of Thermal/Stress-Loading Analysis for Tubulars in HP/HT Wells,” by Norman Shahreyar, SPE, and Douglas Finley, SPE, Halliburton, prepared for the 2014 Offshore Technology Conference Asia, Kuala Lumpur, 25–28 March. The paper has not been peer reviewed. Copyright 2014 Offshore Technology Conference. Reproduced by permission.