A drive down a gravel road in the Loma Campana follows the steep early learning curve in the Vaca Muerta.
There are large pump jacks on old single wells left from the early days when vertical wells were drilled on scattered sites in a place that looks a lot like West Texas.
There are pads with four vertical wells forming a rectangle. That pattern reduced the time needed to drill the wells by shortening the trip from well to well for older rigs not built to walk or slide on skids. Still it used two rigs, and the wells were far less productive than horizontal ones.
A flexible pipeline snakes along the edge of the road leading to a fracturing site where it supplies the fresh water needed for the job. Flexible water lines have become a common sight, replacing fleets of trucks pounding down the bumpy, unpaved roads.
The drive ends at a pad where a fracturing crew was preparing for the 40th and last stage of the job that zippered back and forth between the two horizontal wells that are the first of a program to test the next block north, the Bandurria Sur, which is being developed by a partnership operated by YPF and Schlumberger’s exploration and production arm.
A crew from Schlumberger was doing the pressure pumping. The cost of the job is accounted for as an in-kind payment to the partnership, but every YPF manager who was asked about the deal pointed out that the service company had to offer the lowest bid to get the& work.
The water supply line reduces the number of tanks needed for storage to the 12 required to hold enough water for a stage and then some. On the edge of the site there is a production line waiting to be hooked up when the well begins flowing to transport the water, oil, and gas away to a processing facility.
The connection allows them to add oil and gas production during the pilot phase. Wellhead flares are not a noticeable part of the landscape in a country where flaring is strictly limited by regulations born many years ago to maximize gas supplies.
The system allows early production, but as exploration spreads, companies there will need to find a way to build the pipelines and processing facilities to keep up. The development map generally follows pipeline access, but gathering lines and process facilities are needed. A large area with rich-gas potential in the western part of the plan lacks any infrastructure at all.
YPF is looking for ways to speed development of process plants, as well as the cost, by creating standard modular units that allow quick design and construction of new processing plants, said Pablo Bizzotto, vice president for upstream at YPF.
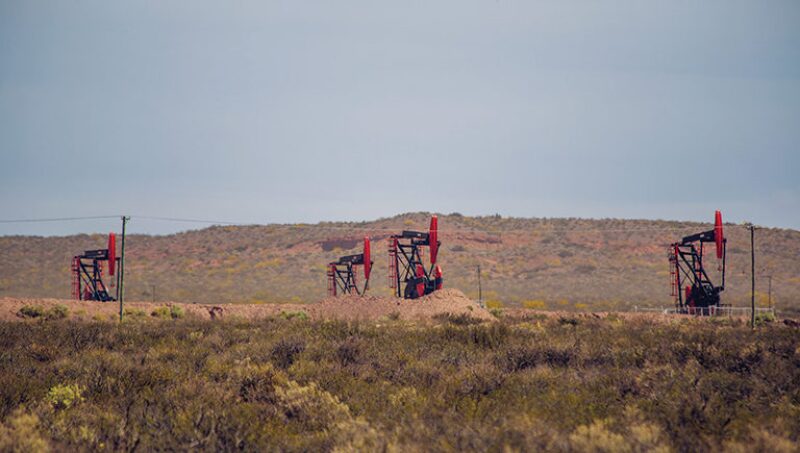
Standard Pad
The pad is a half-sized version of the current YPF standard for development, a four-well line 10 m apart on the surface, spreading out to 300 m apart in the reservoir.
The spacing in the production zone is wide by US standards. Two drawings from Matias Weissel, manager of unconventional projects for YPF, show how far YPF is going to avoid interference during fracturing.
One shows the four wells spreading out and running in the same direction. A cross section indicates that the depth of the wells alternates, so they are separated both horizontally and vertically. A second diagram shows two wells going north and two south with adjoining wells at different depths, further reducing the chance that pressure used to fracture one well will affect a nearby well.
“We feel comfortable spacing from 300 m,” said Luciano Monti, subsurface unconventional manager for YPF. While tighter spacing could add production, “there will be more well interference.”
At this early stage, drillers in the Vaca Muerta are working on a blank canvas. The blocks granted by the government are enormous compared with the confines of leases granted by private landowners in the US, which can force design changes that limit production. While US drilling and completion costs are lower, increasingly dense development in plays such as the Permian Basin means new wells are not as productive as older ones close by.
The well designs are following the lead of US operators, but at a distance. For example, laterals in Argentina are getting longer, which saves money by extending the reservoir that can be reached from a single vertical section, normally 2500 m deep or more.
The standard lateral length has crept up from 1500 m in 2015 to more than 2000 m, and in late 2017, YPF was drilling a well with a 3200-m lateral.
While US operators are drilling even longer laterals and fracturing them at more points, the trend is toward convergence. A table comparing YPF’s completion designs to those of Pioneer Resources shows they are not so different and getting less so over time.
YPF is testing to see if production will suffer if it replaces large particles of ceramic proppant pumped to ensure high conductivity near the wellbore with lower-cost coarse sand, which is common practice in the US. The Argentine company is adjusting the even (geometric) spacing of its fracturing stages, based on the rock properties measured by gamma ray logs during drilling.
Wells on the pads are drilled, cased, and cemented in three sections, allowing the rig to be drilling the next well down during a period when it would otherwise be offline.
YPF has responded to the challenges of drilling in this high-pressure formation by using managed pressure drilling on problem wells. By using it to quickly apply backpressure, it can keep moving forward when it otherwise would have to stop and add mud to control the well, which can cause formation damage, said Giovanni Landinez, general manager for drilling and completions in the YPF unconventional unit.
A new oilfield labor contract permitting unionized crew members to do a wider range of jobs with more efficient equipment and methods means the most efficient pressure pumping crews now are completing 100 stages per month, up from 40 just 2 years ago, Bizzotto said.
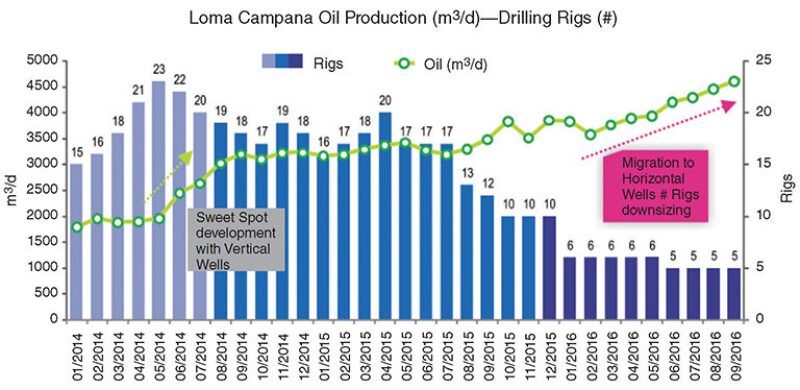
Frac crews that used to have 25 workers now have 18, and drilling crews have one less person on the derrick, said Monti.
Completions there lag the pace in West Texas, where the fastest crews are doing two to three times as many stages per month, said Joseph Sites, president and chief executive office of Allied-Horizontal Wireline Services, who works in both markets. Slower completions significantly add to the cost per stage for those paying day rates compared to the US. But he sees YPF working hard to close the gap.
“Some of the best technology in the world for hydraulic fracturing is sitting in Argentina. They bring it in by request.” Sites said. More importantly, he sees workers at YPF each day trying to drive down the cost of developing Argentina’s oil and gas. “It comes from, ‘we are never fully satisfied’ and ‘we are up against it making the economics of the wells work.’”