This is the first of several articles on the subject of water management for unconventional hydraulic fracturing. These articles are intended to cover the major aspects of the subject, focusing on the technologies being used.
The first installment provides an overview of the critical issues. The subject will be placed in the context of other types of water treating in the oil and gas industry, as well as in other water treatment industries. The introductory material is necessary to lay the groundwork for the eventual discussion of where the technology is likely to go in the next several years. To be able to make that projection, it is necessary to fully understand the context of where the technology is today and how it got here.
Subsequent articles will discuss the different shale plays, the fluid characteristics, regulations, environmental impact, and water treating technologies.
Hydraulic Fracturing and Water Treating
Hydraulic fracturing (HF) is not new. Not counting the recent activity in shale and coal seam gas (or coalbed methane, as it is known in the United States), nearly 2.5 million conventional HF operations have been carried out in the world. HF of conventional oil and gas fields uses essentially the same fluids, in different proportions, rates, and volumes compared with the shale reservoirs. While the details are important from a water management perspective, the fact that similar fluids are used suggests that the historical experience is important in selecting water treating technology. In one form or another, HF has been practiced for at least 50 years. The historical development and current practice of hydraulic fracturing is well explained by Hlidek and Economides et al. (2008).
Most of the conventional HF operations did not involve water treating of the flowback fluids. Most flowback fluids in conventional HF operations have gone to disposal wells or waste disposal sites. However, a significant number of HF operations have been carried out offshore, where water treating is common practice. Nearly all offshore HF operations involve water treating to prevent the contamination and upsets of the main processing system.
Historically, fluids besides water have been used, and many techniques have been tried. In the early days of HF, gelatinized petroleum (i.e., napalm) was used. It is still used to a limited extent today in vertical wells, where limited fluid volumes are required. Its advantage is that water handling is not required. However, given the volumes involved in unconventional HF, it is too costly. Also, safety considerations related to the handling of flammable materials have moved the industry from oil- to water-based fluids.
Pointing out that HF is not new is based on the observation that some of the water treating practices and technologies being promoted these days are difficult to rationalize. Some of the new technologies seem to defy scientific reason, yet are getting a surprising amount of attention. Some older technologies that have been discarded for good reasons are being resurrected. In some cases, incredibly high costs are being incurred. Operators seem to be learning the hard way what works and what does not. Halldorson (2013) wrote about this issue and reminded readers that, “… if it sounds too good to be true, it probably is.”
The term unconventional hydraulic fracturing refers to HF in unconventional resource development. The generally accepted unconventional resources are shale gas, shale oil, coal seam gas, and oil sands (also known as tar sands). The permeability of a conventional oil and gas field is in the range of approximately 10 millidarcies to 0.1 darcy. Beach sand has a permeability of approximately 1 darcy. Concrete has a permeability of 1 microdarcy. The permeability of most of the shale reservoirs being developed today is generally less than 1 microdarcy, in the nanodarcy range (e.g., Eagle Ford, 100 nanodarcies; Marcellus, 10 to 100 nanodarcies; and Haynesville, 20 nanodarcies). Thus, the term unconventional is appropriate, but is not limited to the shales.
The oil sands are an unconventional resource that is either surface mined or developed using steam injection. They are never developed using hydraulic fracturing because the oil viscosity is too high. Opening high conductivity fractures will not make the oil flow. Heat is typically applied, in the form of steam, to lower the viscosity. Though this may seem completely different from water treating of shale HF flowback fluids, I will eventually discuss the similarities and point out that at least one important technology for shale has its origins in the Canadian oil sand fields.
Coalbeds containing natural gas can be developed with or without HF. When HF is used, obviously the productivity is higher. HF of coal seams uses the same fluid types as in shale and conventional reservoirs. Typically, coal seams are developed using vertical wells and the HF, if applied, is done only in a single vertical interval. Coal seams may also be acid stimulated before the HF—a common HF practice in conventional and shale reservoirs. Finally, the coal seams are usually nearly saturated with water, requiring extensive dewatering before gas will flow. Despite these differences, the fluid types are similar to those in shale and conventional HF operations.
For the most part, the fluids used in conventional and unconventional HF comprise the same set of ingredients. Most contain proppant, but not all. Most contain polymer and some also contain surfactant.
Polymer is one of the most important components from a water treating standpoint. Based on polymer types, there are four types of HF fluid:
- Slickwater—partially hydrolyzed polyacrylamide (HPAM)
- Linear polymer—polysaccharides, such as guar, hydroxyethyl cellulose, and xanthan
- Gelled polymer—crosslinked polysaccharides
- Hybrid—combinations of slickwater polysaccharides
Salinity is also important, since many of the polymers work best in fresh water. Even if fresh water is pumped into the ground, the fluid that flows back (flowback fluid) may be highly saline. In that case, recycling will involve desalination, which is difficult in the presence of polymer. Solids are typically present in the flowback fluid. Thus, polymer type and concentration, solids, and salinity are the important properties of flowback fluid from a water treating perspective.
In formulating either an unconventional or a conventional HF, the polymers listed above are typically used. There are sound technical reasons in that both types of HF use fluids from the same general set of ingredients, suggesting there is existing industry experience in dealing with these fluids. There is experience from polymer flooding in which HPAM is used and from other industries such as food, beverage, pulp, and paper.
Water Treatment and Management
From a water treating perspective, what is unique about shale? To date, the only economical technique for developing shale oil and gas is to drill long horizontal wells and apply HF to multiple zones along the horizontal run. The much higher volumes of fluid required for unconventional HF make it different from conventional HF. Whereas a conventional HF may require about 2,000 bbl of water per well, an unconventional HF may require between 50,000 and 120,000 bbl of water per well.
The high injection volume also gives rise to high fluid volume on flowback. Load recovery is the measure of how much of the injected fluid flows back. It depends on factors, such as water saturation of the shale, leakoff rate of the fluids, and the development of a proppant pad. In the Marcellus Shale, for example, water saturation is essentially zero and load recovery is roughly between 15% and 20%, with many cases falling outside of this range. Using these values, between 15,000 and 25,000 bbl of water are returned to the surface. This is more than the volumes for conventional HF operations, in which only a few hundred to fewer than 1,000 bbl of water typically flow back.
The flowback of a conventional HF and an unconventional HF (shale or coal seam) typically occurs at similar rates of roughly 1 to 3 bbl/min. The flowback rate is dictated by the necessity to keep the fractures open. When proppant is used, the fluid flowback rate must be slow enough to prevent viscous fluid forces from pulling proppant out of the fractures. Thus, both conventional and unconventional HF flowback operations occur at similar rates.
Fluid volume, not fluid type and flowback rate, is the unique feature of shale HF fluid management, compared with conventional and coal seam HF. In the next column, I will address how fluid volume affects the selection of technology. For now, fluid volume must be addressed.
Fluid volume affects key aspects of development, such as water sourcing (acquisition) and water disposal. Given the large fluid volumes, water management is required at an early stage of field development. This is a significant departure from traditional oil and gas field development, in which water production typically occurs after startup. Water treating facilities are typically added late in field life. Halldorson said, “With the shales, suddenly water management went from an afterthought to a driving force for unlocking hydrocarbon production.”
Water management for unconventional hydrocarbons requires that decisions be made at an early stage in the development of a field to minimize overall water management costs. When these decisions are not made early, or when they are not implemented in a timely manner, the number of water management options may be scarce and the cost of water management can escalate by an order of magnitude.
This was the early experience for some Marcellus Shale operators who delayed water management planning and were forced to pay upward of USD 0.5 million per well in transportation and disposal costs. Through lack of planning, their only available option was to transport the flowback fluids several hundred miles by truck.
As pointed out by King (2012), brine handling is one of the riskiest activities involved in HF. It involves a high likelihood of the occurrence of a hazardous event, such as a truck crash, a spill, or leak of brine. Where trucking is concerned, it also has a significant effect on human life by significantly increasing traffic.
Developing a Water Management Strategy
Halldorson identifies five factors that dominate water management in shale HF:
- Disposal
- Fresh water
- Regulatory and community concerns and regulations
- Recycling and reuse
- Transport
Decisions regarding each of these drivers must be agreed upon to develop a cost-effective water management strategy that minimizes environmental impact and is acceptable to local communities.
Nearly in parallel with Halldorson, a colleague and I devised a water management strategy (Walsh 2013; Walsh and Crisp 2013) that focuses on five key drivers:
- Hydrology of the field (or region)—defines availability of fresh water
- Regulatory requirements—define disposal options
- Fracture fluid quality—defines the required quality of water
- Flowback fluid characteristics—defines the treatment requirements
- Stage of field development—defines the availability of technology
The similarity between the two lists is striking. Halldorson’s inclusion of community concerns is spot-on and something that I missed. He also noted that transport should be minimized as much as possible because of cost and risk.
A number of water management options are associated with each of the drivers. By providing the required input, the appropriate options can be refined. The next step is to populate a cost model from which the final water management strategy can be developed.
In general, a decision framework organizes the required data in a logical way and provides a logical sequence of decision making, which ultimately leads to an overall strategy. In the case of water management for HF operations, a decision framework defines the variables that affect water management options and suggests the best strategy, whether it be recycle, reuse, disposal, or beneficial use.
Table 1 shows each driver and a simple question that helps to define the meaning of the driver.
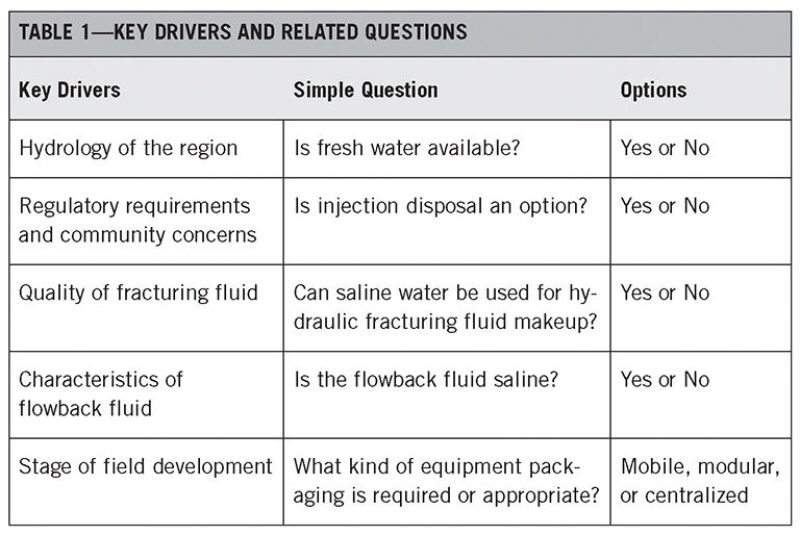
The hydrology of the region could otherwise be referred to as sourcing or acquisition of fresh water. The hydrology of the field defines the availability of freshwater sources. In some regions in which shale resources are found, there is a plentiful supply of fresh water, and an operator can acquire fresh water by simply filling a water truck from a municipal water supply for a relatively small cost. In the Marcellus region of the eastern US, this is the case.
In the western US, this is not the case. Many of the unconventional fields there have been drought-stricken for decades. Acquiring water from brackish or saline aquifers is an option. Reverse osmosis is used to generate fresh water. However, such water withdrawal may result in further lowering of the freshwater table. In those cases, the hydrology of the regional water system must be understood.
Considering this driver, the main question is whether there is a plentiful and inexpensive source of fresh water. If the answer is no, then options for acquisition of water must be considered, including the option to recycle or reuse flowback water.
Regulatory requirements and community concerns could be known as disposal of flowback and produced water. Regulations set strict constraints on the disposal of flowback and produced water, as well as the disposal of any waste generated from treatment of that water. In the US, as in many other countries, the detailed regulations are developed by regional government bodies. Often these regulations are based on past history of industrial development. If past activity has resulted in an adverse environmental impact, then permits for disposal wells are difficult to obtain. The adverse historical experience of associate mine drainage or acid mine drainage has had an effect on the Marcellus Shale development.
Community concerns are no less important than regulations. Public pressure can slow down or stop certain disposal options or development. Community concerns start with environmental impact, but can include issues such as road traffic, transient workers, property value, fire and explosion hazard, and many others. The outcome of community activism does not necessarily result in the best overall outcome for the community and is, therefore, difficult to predict.
Considering this driver, the main question is whether disposal wells are available. If the answer is no, then options for disposal of water must be considered, including the option to recycle or reuse flowback water.
The quality of fluid required to perform a successful HF job varies, depending on the type of shale. Shale varies in quartz and clay content, brittleness and ductility, the pressure required to propagate a fracture, the extent of pre-existing microfracturing, and the extent of microfracturing that will occur as a result of the HF. These factors combine to dictate the optimal fluid type for achieving the required degree of enhanced production. The optimal HF fluid type may require freshwater makeup. For example, HF fluids based on nonionic HPAM are less sensitive to dissolved salts than the anionic form (which is typically referred to as a slickwater fluid). Some of the polysaccharides are also less sensitive to ion content.
For this driver, two questions must initially be answered. The first question is whether fresh water is required for makeup of the HF fluid. If so, then recycling of HF from flowback will generally require desalination. Desalination in the presence of polymers, surfactants, and other suspended solids generally requires the use of mechanical evaporation since membranes become fouled quickly.
If recycling of the flowback fluid is to be carried out, the characteristics of the fluid that flows out of the well are critical in determining the type of technology that will be successful.
As a general rule, the fluids pumped into the ground do not necessarily determine the fluids that flow back out of the ground. In some cases, there is a close correlation. In other cases, there is not. In the Marcellus Shale, for example, even freshwater HF fluids typically become saline through contact with the shale.
In the early stage of development of an unconventional field, a number of individual wells are drilled and completed. In the US, mineral rights are owned by the land leaseholders. Several wells will be drilled to either secure acreage or determine the extent of the hydrocarbon-bearing zone. Intensive in-field drilling and completion of isolated wells generally requires water treating equipment that is mobile. Such equipment is compact and placed on a flatbed truck.
As field development progresses, the leases become secure and the drilling campaign becomes more structured. Clusters of wells are drilled. It is then possible for several adjacent wells to be developed in sequence or simultaneously, facilitating the use of a modular water treating system. In this case, a daisy chain or hub and spoke type of water piping arrangement can be constructed to feed the water treatment unit and to convey treated water to the wells that require it. When a few or several wells are involved, the construction cost of a modular treating system becomes justified.
Later in field life, there may be many wells in relatively close proximity. Over time, the construction of a water conveyance network, together with a centralized facility, becomes justified. This is the current trend in the Marcellus Shale. It has also been successfully implemented in the Pinedale Anticline in southwestern Wyoming (Boschee 2012).
Conclusion
Developing a water management strategy for shale development is relatively straightforward. Five key drivers must be addressed. These define the extent of reuse and recycling that will be economically required, as well as the type of technology (mobile, modular, and centralized). A strategy must be developed early in the development of a field to avoid a costly lack of alternatives.
In the next article, I will discuss the technologies available for water treating of unconventional resources. As always, your comments are welcome.
For Further Reading
Boschee, P. 2012. Handling Produced Water from Hydraulic Fracturing. Oil and Gas Fac.1 (1): 22–26.
Hlidek, B.T., Economides, M.J., Martin, T. et al. 2008. Modern Fracturing—Enhancing Natural Gas Production. Energy Tribune Publishing.
Halldorson, B. 2013. Successful Oilfield Water Management. Paper AADE-13-FTCE-14 presented at the American Association of Drilling Engineers National Technical Conference and Exhibition, Oklahoma City, Oklahoma, 26–27 February.
King. G. 2012. Hydraulic Fracturing 101: What Every Representative, Environmentalist, Regulator, Reporter, Investor, University Researcher, Neighbor and Engineer Should Know About Estimating Frac Risk and Improving Frac Performance in Unconventional Gas and Oil Wells. Paper SPE 152596 presented at the SPE Hydraulic Fracturing Technology Conference, The Woodlands, Texas, 6–8 February.
Walsh, J.M. 2013. SPE Training Course on the Science and Technology of Water Treating. Houston, 26–27 February.
Walsh, J.M. and Crisp, G. 2013. Water Management for Hydraulic Fracturing. Oral presentation made to the International Desalination Association Conference on Water Recycling and Desalination for the Oil and Gas Industry, Banff, Alberta, Canada, 12–14 May.
John M. Walsh is SPE Technical Director for Projects, Facilities, and Construction and principal engineer of water treating for oil and gas with the GHD Group. He can be reached at John.Walsh@ghd.com.