When trying to understand the well-to-well events known as frac hits and fracture-driven interactions (FDIs), the first idea to embrace is this: they are not all the same.
“And the key physical mechanisms are not the same,” said Mark McClure, who added that, “Until you’ve really dialed in on what those are, you’re really in the dark.”
McClure is the cofounder and CEO of ResFrac Corp. In March, the modeling firm began a multiclient study to diagnose the relationships between parent and child wells—or what many consider to be the ultimate subsurface challenge facing the shale sector.
Participating operators are Marathon Oil, Hess Corp., Pioneer Resources, Arc Resources, Birchcliff Energy, SM Energy, and Ovintiv Inc. These independent E&Ps represent a cross section of some of the most active plays in North America: the Midland and Delaware basins and the Bakken and Montney shales.
But what makes the study unique, McClure said, is that it involves 10 rich data sets from well pads that were subjected to a number of cross-validating diagnostics: tracers, pressure/interference monitoring, geochemistry, and fiber optics. ResFrac has been using that data to calibrate its coupled reservoir-fracture models to see what knobs clients might want to turn in the future to improve well economics.
The study is also trying to unearth some firm answers about what is really happening during offset stimulations, why it is happening, and what can be done to mitigate negative outcomes. ResFrac and its clients expect to wrap up this part of the study by the year’s end and to submit an abstract for an SPE technical conference in 2022.
As the study nears an end, McClure offered some of his key observations that he noted are supported by previous research found within industry literature.
So, What’s the Worst That Can Happen?
A growing chorus of subsurface experts consider unwanted chemical reactions in the fracture network as one of the major damage mechanisms resulting from FDIs. McClure is not only among them, he said chemical effects represent the “worst” that can happen when parents and children interact.
“This is where you see wells get hit, they lose 80% of their production, and it doesn’t come back,” he explained. Some in the industry have taken to calling the byproduct of these chemical reactions “shmoo” or “gunk.” For answers as to why this is happening, McClure points to two technical papers in particular.
- In 2018, Calgary-based Canbriam Energy (renamed Pacific Canbriam Energy after a 2019 acquisition) presented URTeC 2902707 which explains how a black, sticky residue was being produced from its Montney parent wells following the stimulation of a newer infill well. What the engineers initially called “debris” was found to be silica proppant and formation fines that were covered with heavy-end hydrocarbons and iron oxides, the latter acting like a “cement” to bind all the material together inside the fracture network.
- Another sticky problem serves as the focus of URTEC 2487, which includes authors from friction-reducer maker Downhole Chemical Solutions and Denver-based shale company E&P Ovintiv. Published last year, this paper speaks to an emulsion some call “gummy bears” that forms when friction reducer, water, and naturally occurring formation irons mix together. This particular problem appears to be most commonly observed in Oklahoma’s shale plays.
The common denominator between these two cases is believed to hinge on the interaction between irons and fracturing fluids, particularly the polyacrylamide friction reducers used in slickwater treatments. The iron originates from inside the formation before becoming one of many substances found in produced water, which is routinely recycled for stimulations in new wells.
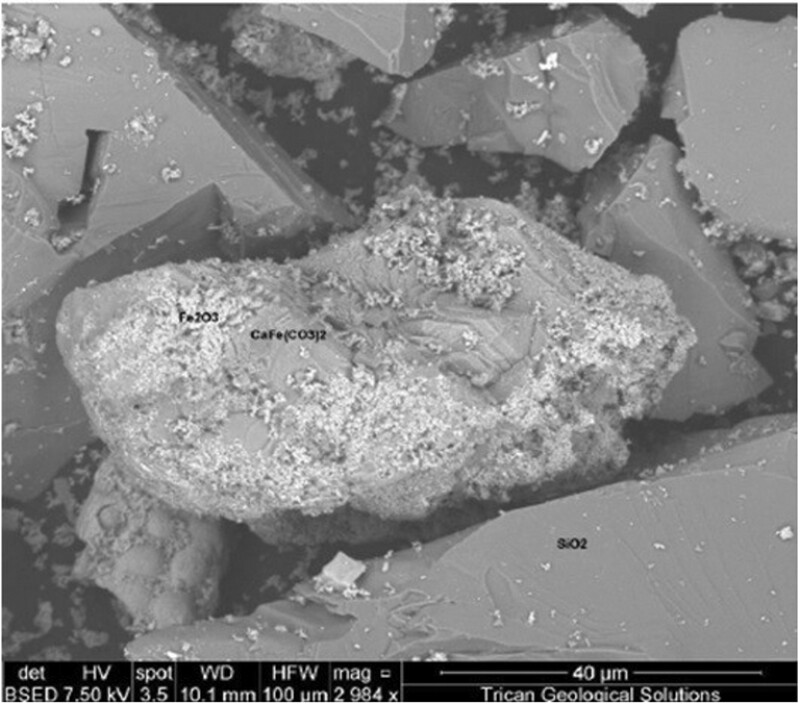
McClure said this helps explain why an FDI may represent a potent chemical shock to the fracture system.
“When you have a frac hit, it’s frac fluid contacting this producing fracture that is full of hydrocarbons which may have been experiencing chemical changes over time,” he said. “And when the frac fluid arrives, you’re introducing this polyacrylamide, you’re introducing oxygen that’s dissolved in the frac fluid, and that can then react with the iron to make iron oxide.”
Evidence is also building that the initial parent well may be suffering from fracturing fluids that are incompatible or overly reactive with the formation. Again, this problem is believed to be most common in Oklahoma and in the Montney.
That said, some of the companies that have observed compatibility problems have been taking a deeper look at the exact chemistries they are using to stimulate their wells. McClure has been working with an operator on this front and said he believes that modified fracturing-fluid chemistries “can have a substantial positive impact.”
What’s Not Happening Down There?
One of the things that McClure has not seen any evidence of in the study’s data set is the impact of major stress rotation. The implication is that fractures, which McClure holds are predominantly planar in nature, are generally propagating out perpendicular to their wellbore with only minor deviations.
While this still leaves room for asymmetric fracture growth on either side of the wellbore, it means FDIs are simpler and probably more predictable than first assumed.
This is in contrast to a large number of technical papers delivered to the industry early on. Some of the modeled fractures have been dubbed “spaghetti fracs” because “they look like the fractures just turned 90° and then zoom off in a different direction,” said McClure.
In a word, he says the impact of stress rotation has been “overblown.”
The reason comes down to a point that McClure has been championing for years, which is that estimating the principal stresses in low-permeability reservoirs is extremely difficult and fraught with potential missteps.
- What completions engineers want to know is the difference between the minimum and maximum principal stresses that are pushing and pulling against the rock matrix, or anisotropy.
- In a perfect world, horizontal wells are landed perpendicular to the maximum principal stress so that the induced fractures will grow out from the wellbore in the direction of that stress.
- If the minimum and maximum principal stress were to flip, or reverse, after depletion, then it might have a big impact on subsequent wells stimulated in the immediate area.
However, McClure doesn’t see that happening often. He says the reason why this has become a big topic is that too often the anisotropy has been assumed to be on the low end.
For instance, if the maximum stress is only 200–400 psi above the minimum stress, then the scales don’t have to be tipped much at all to result in a pronounced stress-rotation effect.
McClure conceded that depletion effects can lead to minor stress rotation and that if fractures hit an offset wellbore, they can also then exchange fluids with other fractures by connecting via the outside of the casing.
By contrast, in wells where long-term depletion is not as much of a factor, the new fractures being induced stage after stage are far more likely to push past each other without intersecting. This is due to the stress-shadow effect, which is a compressive force that forms around a propagating fracture and at least temporarily shields it from meeting up with another fracture.
To back his findings, McClure cited research from geoscientist Jens-Erik Lund Snee and Mark Zoback, the renowned seismologist with Stanford University who is both a former professor of McClure’s and a senior executive advisor of ResFrac.
A recent paper by Lund Snee and Zoback and focusing on North America shows that “the major shale plays have, at a minimum, 1,000–1,500 psi of stress anisotropy,” said McClure, adding that a large portion of them “have several 1,000s” of psi in stress anisotropy. This particularly includes plays or sections of a play with a high degree of strike/slip faults.
McClure’s confidence here is furthered by the study’s modeling runs that relied on downhole fiber-optic data collected during the hydraulic-fracturing treatment.
The value of fiber-optic data has been rising in recent years after operators started using it to see how fractures open up and actually intersect with a neighboring pad well.
Preloads and “Free” Loads
In dealing with FDIs, many operators have turned to preloading. There’s no consensus on the practice, but McClure said he’s seen plenty of cases where preloading works, or would have worked if it were implemented.
“All you’re trying to do is fill the well and the near-wellbore region of fractures with water instead of oil and gas. This is because a mixture of oil and gas is highly compressible, and water is only slightly compressible,” he explained.
It’s not that preloading stops FDIs dead in their tracks; it’s that the torrent of high-pressure stimulation fluid is forced to push against a more pressurized fracture, dampening its intensity. Some of McClure’s key points on preloading include:
- When stages in child wells show a heavy bias, or asymmetry, toward the parent, it’s likely that well is a preloading candidate.
- Preloading with a chemical package is “very important” since it will help remediate scale and any water-block damage caused by the injected water.
- The right recipe requires understanding the formation and can include solvents, surfactants, or citric acids that will react slowly enough to reach deeper into the fracture system.
To know whether a preload will help also depends on whether an operator understands the severity of asymmetric fracture growth vis-à-vis a depleted parent.
McClure pointed to a paper delivered by Devon Energy in 2020 that outlined how it uses sealed-wellbore pressure monitoring to diagnose FDIs. In SPE 199731, Devon shows two zipper-fractured wells that were offsetting a parent well that had produced around a half million bbl of oil prior to the infill completions. No preloading was done on the parent, so fractures from the child well closest to it showed a heavy bias toward the depleted area. This was clear from a lack of FDIs in the monitor well which was on the other side of this child well. Then, about midway through the child well completion, FDIs were picked up in the monitor well—a signal that the asymmetry was reduced in the heel section.
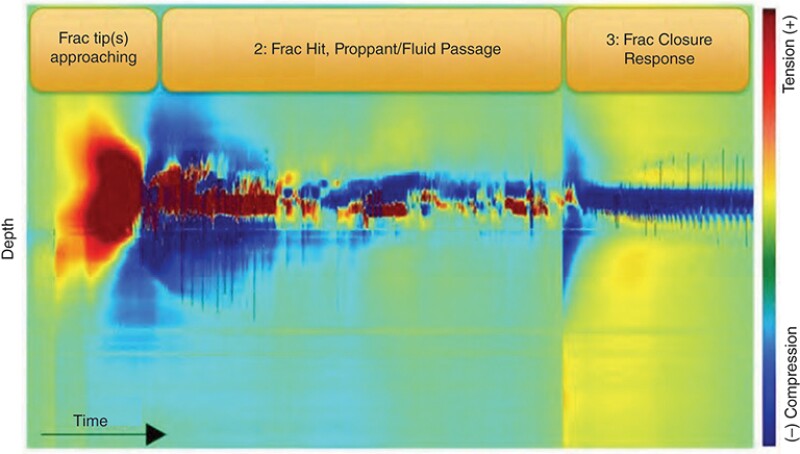
To McClure, this showed that the parent well was being filled up by the first few dozen stages, allowing the heel section stages to tap into more-pressurized sections of the reservoir.
Depending on how you look at that observation, it is either a reason to adopt preloading or to consider another option.
Regardless whether it mitigates an FDI, preloading is not always the right fit since well economics can be sensitive.
One of the biggest deterrents is the fact that the injection water and the pumping units required for a preload do not necessarily represent a low-cost operation—especially when tens of thousands of barrels are needed to fill the void. Based on the data he’s seen, McClure noted that diminishing returns tend to kick in once preload levels top 20,000 bbl of injection water.
This bring us back to that other option, which McClure said is probably most suitable for operators seeing only minor production losses from FDIs.
“I think that the mitigation strategy that is most intriguing to companies is in changing the frac order—because it’s nearly free,” he said, explaining that operators are choosing to stimulate the first infill well on a pad that is closest to the depleted parent well. “The idea is that it’s sort of sacrificial, that [this well] is going to take the bullet for the rest of the wells,” said McClure.
For those times when preloading and simply reloading a well won’t work, there is another step that can be taken. Instead of sacrificing a well, or at least some of its initial stages, why not just skip drilling or completing it? This saves capital and leaves a wider well spacing between the parent and the infill children.
“I think some operators are finding that this largely avoids much of the issue they’ve seen with underperformance,” McClure said. “They’re giving up a little bit of potential acreage there, but they’re leaving a buffer and getting a great return on the wells that they did drill.”
It’s Not Bad All Over
The risk of production-harming chemical effects appears to be relatively low in plays such as the Bakken in North Dakota’s Williston Basin and the Midland Basin in west Texas. “For the most part in the Midland Basin and in the Bakken, frac hits are not often crushing wells,” said McClure.
While client data reflect that wells in these two regions are less vulnerable, McClure said the reasons are not yet fully understood. Geology is certainty playing a role, as it does in all cases, but more research and reservoir studies will be needed to offer better answers.
This does not mean that FDIs are not a concern for either Midland or Bakken operators. It means that they are more addressable through well spacing.
Parent wells in the Midland region do show some production loss, but many of them are able to return to pre-FDI rates. Child wells in the play also tend to underperform those original pad wells, but not by a startling margin.
However, Bakken wells have been telling a different story for years.
ResFrac and others have observed parent wells actually seeing an uplift in production after a frac hit. One theory is that Bakken fractures are relatively less complex and more linear.
If this is the case, then an FDI may have a similar effect to a re-frac by reconnecting far-field propped fractures with the wellbore—thus offering an explanation to the uplift operators there have reported.
There are exceptions, as always. McClure said he’s seen data from both the Midland Basin and Bakken wells that showed dramatic and even total production loss.
However, he believes these losses may be the result of “massive frac hits” that activated a fault and caused mechanical damage to the well, or where the parent wellbore was filled to the brim with proppant.
“That could happen anywhere if well spacing is very tight,” said McClure. “But it seems to me that the typical well spacings that most operators are using in the Midland and Williston Basins, they’re seeing modest but not terribly severe impacts.”
For Further Reading
SPE 199731 Monitoring the Pulse of a Well Through Sealed Wellbore Pressure Monitoring, a Breakthrough Diagnostic With a Multi-Basin Case Study by K. Haustveit; B. Elliott; J. Haffener; et al., Devon Energy.
URTeC 2902707 An Integrated Approach to Optimizing Completions and Protecting Parent Wells in the Montney Formation, N.E.B.C. by J. Nieto; G. Janega; B. Batlai; and H. Martinez, Canbriam Energy.
Nature Communications vol. 11, article number 1951, Multiscale Variations of the Crustal Stress Field Throughout North America by J. Lund Snee and M. Zoback.
URTEC 2487 Performance of Friction Reducers in Iron-Rich Environments by S. Hazra, DynaChem Research Center; M. Van Domelen and W. Cutrer, Downhole Chemical Solutions; and N. Peregoy, P. Okullo, and B. Darlington, Ovintiv Inc.