Throughout the life of a well, it may be necessary to isolate existing perforations for the purpose of recompleting an alternative section of the wellbore or to prevent the production of unwanted fluids such as water from a given zone or interval.
Traditional methods may involve setting a plug, straddling the perforations, or performing a chemical or cement squeeze, all of which can be complex and costly and typically result in restricted access to the wellbore.
To address these challenges, TAQA developed ZoneStop, a cost-effective, low-complexity, patented product that isolates existing perforations and/or formation intervals enabling shutoff of the target zone and permanent isolation. ZoneStop can effectively seal and prevent flow into and out of the target interval.
As shown in Fig. 1, ZoneStop is a sized, swellable elastomer particulate blend slurried at surface, then pumped from the surface into the target zone and allowed to swell in situ to provide an effective seal.
The swellable particulates are batch-mixed at surface and pumped downhole using standard cementing or rig equipment. The design and volume of the particulate material and carrier fluid are based on the well conditions and design, and on the properties of the zone requiring isolation. The swellable elastomer particles are based on a proprietary recipe that is purposely designed to swell under downhole conditions. The swelling mechanism is driven by a combination of superabsorbent polymers and osmotic components to optimize the speed and strength of the swelling process while ensuring chemical resistance and plug permanence.
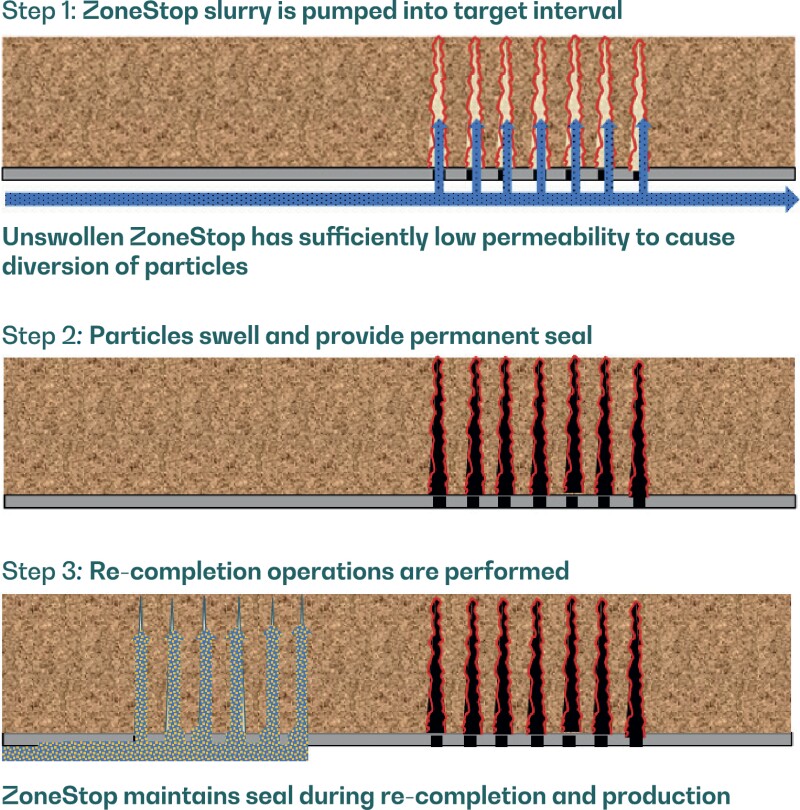
This technology has been deployed in different applications such as enhanced cement placement and perforation isolation prior to recompletion and refracturing of unconventional reservoirs.
For applications in plug and abandonment, ZoneStop has been applied in the Permian Basin as precursor to cement to help cure gas-migration issues between the production and intermediate casing. ZoneStop controlled losses for an extended period of time and enabled effective cement placement. With ZoneStop, the well was successfully plugged and regulatory requirements were satisfied. No pressure buildup on annuli between the production casing and intermediate casing annulus or intermediate casing and surface casing was observed after this treatment.
The technology has been applied in multiple field trials to effectively isolate perforated intervals.
In one application, ZoneStop was applied to selectively isolate perforations to prevent losses and enable gravel packing of another zone. This demonstrated that the swellable material could be used to replace the cement in isolating troublesome perforations while maintaining fullbore access in the well.
In another application, ZoneStop was applied to isolate a water-bearing zone in a gas producer. The water-bearing zone was selectively isolated by pumping the swellable particulates into the perforations. Isolation of the perforations was verified by pressure test. The producing zone was returned to production after the treatment, and fullbore access to all intervals was maintained.
To enhance plugging performance for zones with larger void spaces that may result from large vugs, fractures, or from poor cement isolation, an extension of the technology has been developed.
A novel binding agent was developed to improve the plugging efficacy by consolidating the swellable particulates. Initial testing was conducted using a specially designed apparatus replicating a fracture where the fracture aperture could be varied for each test. The particle and binder slurries were prepared and then pressure was applied to force this slurry through the fracture aperture. If a plug was formed, then the differential pressure was increased to a maximum of 500 psi to evaluate the plug integrity. These third-party slot tests demonstrated a significant enhancement in plugging potential with the addition of the temperature-activated binding agent.
The next generation of ZoneStop can plug slot gaps up to 12.7 mm compared with 3.5 mm for the particulate slurry alone. The plug was capable of consistently withstanding 500-psi pressure differential during testing when applied against the plug.
This extension of ZoneStop opens the possibility of zonal isolation under more severe conditions such as fractured formations, vugs, large casing leaks, and for refracturing. This new approach can also help to reduce the overall quantity of material required to create an effective and permanent plug.
In this spirit, TAQA is also evaluating the application of this technology to prevent lost circulation of drilling fluids, one of the main challenges facing drilling and cementing operations, where having material that is small enough to fit through a drill bit and then swell to more than twice its size will create a significant positive impact.
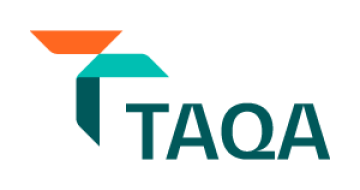