With the availability of more-complex smart-well instrumentation, immediate evaluation of the well response is possible as changes in the reservoir or well occur. Most current work in distributed measurements looks at distributed-acoustic-sensing (DAS) or distributed-temperature-sensing (DTS) data individually, which limits inferences about multiphase-flow problems. The objective of this work was to look at these two types of data together and determine what improvements can be achieved in multiphase-flow problems compared with the conventional methods of looking at DAS and DTS alone.
Introduction
Two prominent tools that provide compartmental-monitoring and control capabilities of horizontal wells are fiber-optic distributed measurements and inflow-control valves (ICVs). The combination of both tools provides an opportunity to adjust well production by choking valves on the basis of observations made in real time, to hinder production of unfavorable fluids. Changing downhole conditions provide new production data, and this management loop can be closed with an effective production-optimization algorithm.
In this paper, the authors present the basic procedure to use DAS measurements for inflow profiling.
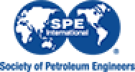