All-metal progressing cavity pumps (AMPCPs) are frequently used in oil and gas applications to produce high temperature fluids to surface but can exhibit accelerated wear during operation that results in decreasing volumetric efficiency over the pump’s life. In the complete paper, the authors present a proposed condition indicator that estimates the wear experienced by an AMPCP at any point in operation and takes into consideration the potential effects of downhole operating conditions. The proposed condition indicator also can be extrapolated into the future and used to estimate the potential remaining useful life (RUL) of an AMPCP.
Introduction
AMPCPs are composed of a metal stator and rotor, which enables them to operate in much higher temperature fluids compared with standard elastomeric PCPs. Because of metal-on-metal contact between the stator and rotor, AMPCPs typically experience more accelerated wear than elastomeric PCPs, resulting in reduced pump efficiency and shorter overall pump life.
While decreasing pump efficiency can be a result of pump wear, it also can be caused by changes in operating conditions, such as increasing pump differential pressure or decreasing pump speed.
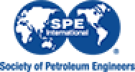