Bottle tests are the preferred method to test petroleum emulsion stability in the industry today. A new technique using nuclear magnetic resonance (NMR) is available to evaluate both stability and demulsification behavior of emulsions. The NMR scans the water fraction throughout the entire length of the emulsion sample. These rapid measurements are designed to dynamically probe the emulsion, capturing its separation as a digital image. This case study presents the ways NMR has helped predict the effects of future well line-up changes.
Introduction
Emulsion stability negatively impacts oil processing operations and plant design. The assessment of emulsion stability is performed at wellheads and gas/oil separation plants (GOSPs). Bottle tests are largely used for emulsion assessment, due to their simplicity and low cost. These tests depend on the visual identification of the separated water layer as the only quantifiable parameter. NMR is one of the alternative methods for emulsion assessment that can provide information for all emulsion components. These components include the water layer; the oil/water interface—including the rag layer (the dense-pack zone [DPZ] of droplets above the interface); the remaining water-in-oil emulsion; and the dry-oil continuous phase. The DPZ—or rag layer—is of particular importance for oil processing, as its occurrence in separation vessels can lead to process upsets, resulting in excessive concentration of oil at the vessel’s water outlets. This interfacial phenomenon is particularly critical in the production of heavy oils, oils with high solid content, and oils forming highly stable emulsions. NMR is not only capable of measuring the water fraction throughout the entire emulsion sample, but can also provide a digital image of the water separating in the sample. More advanced NMR analyses are able to determine the water droplet size distribution (DSD) in the emulsion, and how the distribution changes during separation. It is also possible to obtain information on the droplet sizes at each position in the sample, as they change in time.
Bottle tests are limited to the visualization of the free-water layer. Measurement errors are common if the oil/water interface is not clear. Unlike the NMR, any water still emulsified in the oil cannot be measured as it is not visible. The formation of the rag layer cannot be identified either. In addition, the efficiency of separation calculated from bottle test results, or emulsion separation index (ESI), requires knowledge of the water cut of the sample. The production water cut can be provided by the oil-processing operations, but the value is hardly the same found at sampling points. If the water cut is not known, it needs to be accurately measured in the sample after the bottle test. Usually the total amount of water is measured after centrifugation. It is difficult to guarantee that the emulsion is fully separated, as some droplets could still be unresolved at the interface. Another test limitation is the determination of separation efficiency when the water quality is poor. The presence of an oil-in-water emulsion could be the cause of cloudiness, contributing to an inefficient separation. But most of all, no readings can be made if the emulsion does not separate spontaneously. With NMR it is possible to determine the sedimentation rate of water droplets, even if no coalescence takes place (and no free-water layer is formed).
NMR Assessment of Demulsifiers
A simple qualitative assessment based on NMR images was made to help operations predict the changes in emulsion stability, due to future well line-up changes of GOSPs. New wells producing medium-grade crude (Crude 1) are planned to be lined up to two GOSPs currently handling two types of light-grade crudes (Crude 2 and Crude 3). New demulsifiers were tested at the current Crude 2 and 3 production.
Crude oil samples from each of the wells—here referred to as Crude 1, 2, and 3—were sampled and recombined in the laboratory. This was necessary as the blends are not yet in concomitant production. The oils were dried and recombined—in a reproducible way—with the extracted produced water. The reproducibility was achieved by optimizing the mixing parameters until the prepared emulsion samples had a repeatable separation behavior. The demulsifiers tested are referred to as Demulsifier A, B, C, and D. A sample with the incumbent demulsifier in use at the GOSP and a control sample without any demulsifier were prepared for comparison. The demulsifiers’ effect on the emulsion destabilization was captured with NMR for each of the oils (Fig. 1), and for 1:1 blends of the oils, as well as a 1:1:1 blend of all oils (Fig. 2).
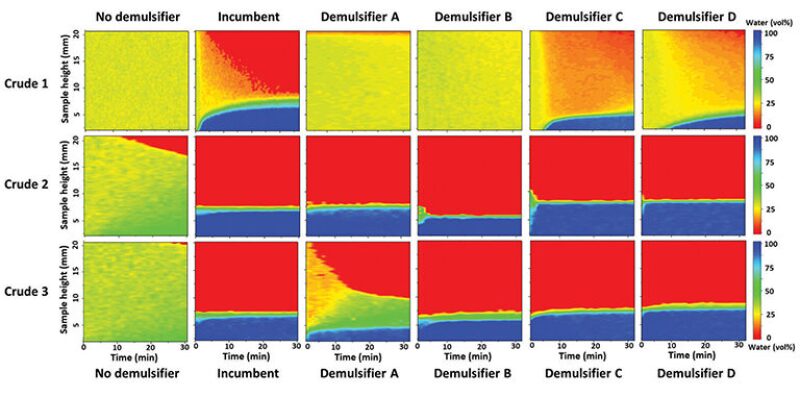
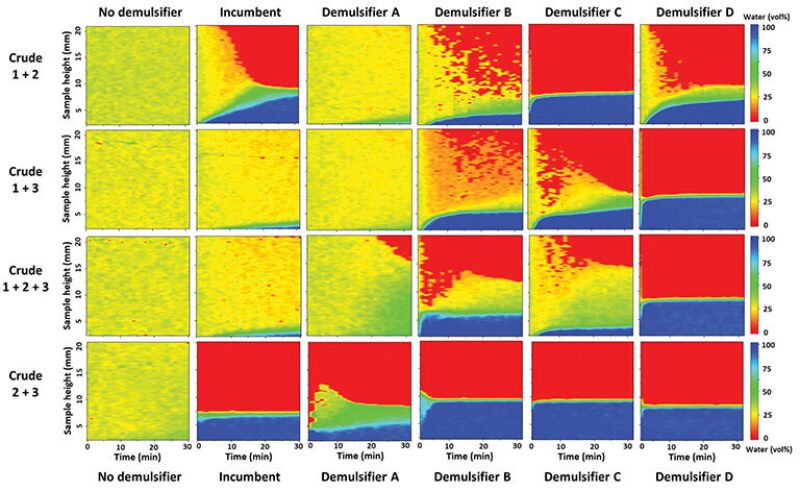
Working Principles
The responses to magnetic stimulation of water and oil are different. The interactions of the hydrogen atoms in the hydrocarbon and water molecules create the phase contrast measured by the NMR. It is set up to read only the water signal and suppress the oil signal, forming the images seen in Figs. 1 and 2. The colors range from 100% water (blue) to no water (red). The y-axis shows the position at the emulsion sample height (total of 20 mm). The x-axis is a superposition of several measurements taken for 30 minutes. The number of possible measurements within 30 minutes depends on the oil properties, ranging from 69 (Crude 1) to 24 (Crude 2) measurements. This type of plot allows the visualization of the emulsion separating through time. A representation of the emulsion layers in the sample—equivalent to the final state of the NMR measurement—can be seen in Fig. 3. In this example, the initial state of the emulsion was 30% water distributed through the entire height of the sample. The final state is a partially resolved emulsion with the presence of a rag layer. This result is an indication that the demulsifier in this sample does not effectively induce coalescence.
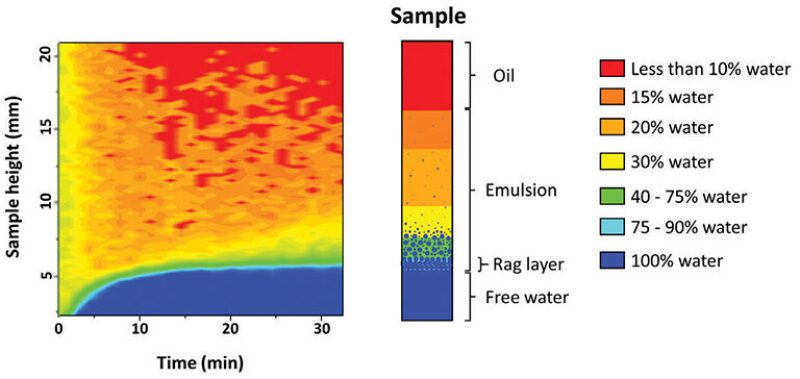
Results
The separation profiles in Fig. 1 show that none of the demulsifiers can fully resolve the Crude 1 emulsion within the observation time of the experiments (30 minutes). The emulsion of Crude 2—the lightest oil—is easily separated; all demulsifiers were able to resolve Crude 2 within the first minutes of observation. The emulsion of Crude 3 is also easily separated, but Demulsifier A is relatively less efficient.
The separation behavior shown in Fig. 2 is quite different than expected, based on the individual separation performances. The incumbent demulsifier was the most efficient in resolving Crude 1, but it was not the most efficient to resolve the Crude 1 blends—even though it can easily resolve Crudes 2 and 3 independently, and the 1:1 blend of Crudes 2 and 3. Demulsifier C is the best demulsifier to resolve the blend of Crude 1 with Crude 2, albeit not the best to resolve Crude 1 individually. And likewise, Demulsifier D is the best to resolve the emulsion of Crude 1 with Crude 3 and the blend of all oils, regardless of the individual performance with Crude 1.
Conclusions
NMR is an excellent technique to assess emulsion stability and destabilization behavior. A digital image of the emulsion separation is obtained from the one-dimensional water quantification in time. Unlike the bottle test, NMR can show the water still emulsified in the oil phase, as well as the dry oil formed at the top of the emulsion. This detailed spectral image provides valuable details of the stability and nature of the emulsion that can be used in the operation and design of an oil facility.
For the purpose of predicting the impact of blending medium-grade crude with lighter-grade crudes, the results show that the emulsion stability of an oil blend cannot be correlated to the emulsion stability of the separate emulsions. The stability of blends should always be re-assessed. This qualitative study allowed for careful selection of the oilfield demulsifier required to ensure that production remains within specifications, as the relative proportion of Crude 1 in the blend increases with time. If the majority of the light-grade crude in the GOSP is Crude 2, then Demulsifier C would be recommended when blended with Crude 1. If the amounts of Crude 3 became significant in the blend, then Demulsifier D would be recommended. The other demulsifiers either do not induce full separation or lead to the formation of a rag layer.
Finally, the NMR revealed that blending the three crude oils did not give rise to different stabilization mechanisms, resulting in emulsions unexpectedly hard to break. If demulsifiers had been proven unable to resolve the emulsions, upgrades to the emulsion-separation equipment would have been considered.
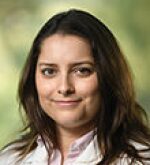
Since 2014, Debora Salomon Marques has worked as a research scientist in the Oil & Gas Treatment division of the Saudi Aramco Research & Development Center, in Dhahran, Saudi Arabia. She specializes in crude oil emulsions, particularly in the characterization of the emulsion-separation process using nuclear magnetic resonance (NMR). Marques holds a bachelor’s degree in physics from the State University of Campinas (Brazil), and masters and PhD degrees in material science and engineering from the King Abdullah University of Science and Technology (Saudi Arabia). debora.salomonmarques@aramco.com.
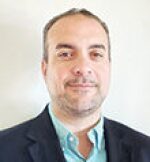
Ramsey J. White is a chemical engineer and the lead process engineer in Saudi Aramco’s Southern Area Oil Operations Technical Support department. He has over 20 years of professional experience. Before joining Saudi Aramco, White worked at SNC-Lavalin in Houston, Texas, as a process engineer on several petrochemical and refinery upgrade projects. For the past 13 years with Saudi Aramco, he has worked on process troubleshooting, risk analysis, process and energy optimization, and GOSP upgrade and technology projects. White holds a bachelor’s degree in chemistry from the American University in Cairo and a master’s degree in chemical engineering from the University of Houston. ramsey.white@aramco.com.