The growing amount of heavy crude processed worldwide has created additional separation challenges, leading some operators to turn to alternative technologies. In some cases, electrocoalescence has been an effective tool to separate oil from water.
Morad Amarzguioui, senior research engineer at Wartsila, told the SPE Gulf Coast Section’s Project Facilities and Construction study group that most of the world’s lighter-oil fields have been developed or are end-of-life fields. As the industry searches for additional crudes, the newer discoveries are generally heavier, which presents unique separation challenges.
Heavier crudes have high viscosity, small density differences between continuous and dispersed phases, and small droplets, often because of the shearing that occurs with the use of artificial lift pumps.
Lighter crudes also have separation challenges. They are prone to asphaltene precipitation and result in incompatible compositions when mixed with heavier crudes. “There is always a problem when you mix light and heavy crude oil,” Amarzguioui said.
Traditionally, the separation of water and oil in a stable emulsion has been divided into two main processes: coalescence and sedimentation. Optimal separation usually requires both processes. “These are the two techniques which dictate how well the separation process will go,” he said.
Operators use four approaches to the separation of the different grades of crude: raising the processing temperatures, increasing the chemical dosages, increasing the vessel sizes, and increasing the number of treatment stages. Each approach affects capital or operating expenses. Increasing processing temperatures, for example, generally means using more equipment (which increases capital expenditures) and an increased energy demand (which increases operating expenditures). Making vessels larger also means higher capital expenditures, Amarzguioui said. “A significant drawback to the conventional solutions is that they often demand increased energy consumption, higher material costs, (higher) operating costs, or larger space for the production facility,” he said.
Using electrical energy up-front can make separation more efficient, particularly for heavy crudes that present unique separation challenges. “Applying electrocoalescence represents a more efficient and cost-effective way of resolving separation challenges,” he said.
Electrocoalescence is a technology that applies a high-voltage electric field to an emulsion, causing the water molecules to realign and their droplets to coalesce, which results in larger droplets.
The settling velocity of water droplets in oil depends on the viscosity and density of the fluid and on the square of the size of the droplets (from Stokes’ law). The electrocoalescer increases droplet size and makes the first stage of separation more efficient.
Electrocoalescence is a technology that has proven effective for dehydration, but its use in separators is relatively new. The newer application uses fully insulated electrodes that are capable of withstanding a harsh chemical environment and can tolerate 100% gas or water. The newer technologies can be installed in three-phase separators at all stages in the separation train, Amarzguioui said.
The electrostatic treatment increases the coalescence of water and makes the separation process less dependent on chemical surfactants. The physical properties of the emulsion determine the efficiency and predictability of the separation, he said. The newer technologies installed inside the separator can handle oil from 12° API to 50° API and are suitable for retrofit and newbuilds.
The plates are from 2 m to 5 m long and can weigh approximately 22 kg each, but they do not take up much space inside the separator. The distance from the insulated plate to an electrode is approximately 5 cm, and the plates are assembled in a way to discourage solids from depositing on them, Amarzguioui said.
For heavier crudes, electrical coalescence improves the efficiency of the first separation vessel and is more efficient than a freewater knockout unit. Tests have shown that when an operator applies electrocoalescence, water and oil separate more quickly and more reliably than when only a demulsifier is used.
The insulated plates allow an operator to locate the electrocoalescence process upstream in the separation train, where the water cut is highest and the enhancement in separation performance is greatest. As a result, more water can be separated at an earlier stage. The technologies allow emulsions to be treated at a significantly lower temperature than in conventional separators, resulting in lower energy demand, reduced emulsion layers, improved level control, and the potential for increasing production.
Amarzguioui cited an application of electrocoalescence at the Fahahil South degassing station in the Dukhan field in Qatar, where winter temperatures made separating oil and water difficult (AlQahtani 2012).
The winter operating conditions were as follows:
- Operating temperatures down to 4°C
- Operating pressures of 170 psig
- Feed flow of 64,000 B/D
- Water content in oil outlet was >5% volume
- Average consumption of demulsifier was 30 ppmv
After installation and a trial, the operator observed the water-in-oil range was reduced to basic sediment and water (BS&W) 0.05–0.2% from 0.2–1.2% BS&W before modification (Fig. 1). A 60% reduction in demulsifier was achieved in low temperatures with optimization.
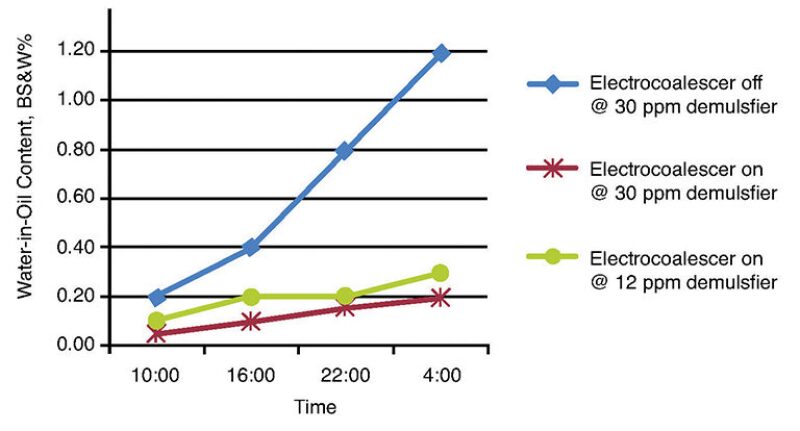
For Further Reading
SPE 156067 Vessel Internal Electrostatic Coalescer Technology by A. AlQahtani, Qatar Petroleum.