Poor separation performance is typically blamed on the separator itself with the main target being the internals. However, after an analysis of the issues, the root cause is often found to be a failure in areas related to the separator/internals. Shortcomings in design, installation, instrumentation, and operation can lead to poor separator performance.
Part 1 covered design issues. This article will focus on installation issues. Brief problem statements, root causes, and lessons learned associated with case histories of troubleshooting separators are given.
Additional installation and inspection guidance can be found in a 2018 SPE webinar by J.P. Sena, “Separation Internals: Field Installation and Inspection To Enable the Potential for Good Performance.”
A) Cyclone decks
Cyclone mist eliminators typically come in “boxes” of two to six. The boxes are hung from a support deck with bolts. Gaskets are required between the boxes and the deck. Moreover, the deck itself consists of plates with vertical edges that can be bolted together and/or to a support ring welded to the vessel wall. Gaskets are required between deck plates as well as at the support ring.
In this case, the liquid carryover was significant enough that the plant was shut down just to investigate this carryover issue. During inspection, it was found that several gaskets on the cyclone boxes and deck plates were not installed, allowing gas and liquid to bypass the cyclones.
Installation reports showed that the internals were properly installed with all gaskets and were signed off by the internals supplier contracted supervisor.
Lessons learned:
- You don’t get what you expect; you get what you inspect!
- On gasketed internals, do a flashlight test to look for unsealed areas.
- Every installation should be documented with pictures and reviewed with the end user prior to closing up the vessel.
- Internals installations, especially on shutdowns, happen under time pressure, but quality should not be sacrificed. A few extra hours to do the job carefully and correctly would have saved the cost of another shutdown.
- Provide feedback to the supplier and end user on proper installation to prevent a reoccurrence.
B) Dual mesh pads
In some scrubber applications, dual mesh pads are installed. The lower one is designed for removing large drops, hence reducing the liquid load to the upper mesh and agglomerating smaller drops. The agglomerated drops are then caught by the upper mesh pad. In addition, the pressure drop across the lower mesh helps improve the flow distribution to the upper mesh.
On inspection, it was found that the mesh pads were installed in reverse order leading to high carryover.
Lessons learned:
- Some equipment may look alike but can have significantly different performances. When there is an order of placement required, mark the equipment appropriately. Tags or markings of “lower” and “upper” would have prevented the error and helped ensure proper installation.
C) Materials mismatch
Incoloy internals were supplied (inlet vane device, vane pack) for a vertical scrubber. However, during installation, it was found that stainless-steel (SS) bolts/clips were supplied. Because of schedule impacts, the SS bolts/clips were used and would be replaced at a future planned shutdown. This error could have led to significant damage and an unplanned shutdown due to corrosion damage.
Lessons learned:
- Don’t forget about accessories and material requirements.
- Check the manifest. Require Positive Material Identification (PMI) as part of final inspection prior to shipping; 10% PMI is typical, but 100% PMI should be required on nonstandard material such as Incoloy.
D) Gaps in mesh coverage
A vertical vessel was suffering from high liquid carryover. It was found that the installed mesh was not fully covering the flow area. For whatever reason, the vessel was unusually out-of-round (the term for when a vessel’s cross section is not perfectly round). Mesh is typically oversized to account for out-of-roundness. However, in this case, the supplied mesh was not sufficient.
Lessons learned:
- You don’t get what you expect; you get what you inspect!
- Ensure installers have the proper installation training.
- Do a proper installation and inspection.
- Atypical conditions should be communicated to the designer/supplier.
E) Wire mesh tied together too tightly
A vertical scrubber with a mesh mist eliminator was suffering from high liquid carryover. Typically, wire mesh sections are tied/wired to supports. However, in this case, the mesh sections were tied to each other as well. The mesh section-to-mesh section tie wires had been tied (squeezed) so tightly that the mesh no longer filled the vessel. A gap remained when the last sections were installed. Tying the sections together also increased the upward force so that the resulting flow differential pressure could have affected the supports.
Lessons learned:
- You don’t get what you expect; you get what you inspect!
- Ensure installers have the proper installation procedures.
F) Vertical vessel corrosion
In most cases, the inlet pipe is not long enough to mitigate swirling flow that can affect the performance of an inlet device. In this case, the inlet vane device was designed with antiswirl blades that were bolted to it. At a planned turnaround, the vessel was opened for inspection. The welds of the antiswirl itself had corroded and failed due to galvanic corrosion. Moreover, corrosion was found on the nozzle wherever anti-swirl blades touched it.
Lessons learned:
- Internals are typically made of material different from the vessel so be aware of galvanic corrosion.
- Do proper isolation of different materials.
G) Reinstalling and reusing mesh mist eliminator
In a turnaround situation, the wire mesh mist eliminator was removed to allow for vessel inspection. However, instead of replacing the mesh, the same mesh was used. The resulting symptom was liquid carryover.
It was later found that the reinstalled mesh had gaps in flow coverage. Mesh is not “springy” and is deformed when removed from the vessel. It loses its ability to fill gaps. Removing mesh makes it out of shape and reinstalling them makes them even further out of shape. In addition, the mesh sections may not have been installed in their original locations.
Lessons learned:
- It is good practice to always replace the mesh if it is removed from the vessel.
- If mesh is reused, number the sections so that they can be reinstalled in the same locations.
- Additionally, mesh cannot be adequately cleaned, so reinstalled dirty or fouled mesh can lead to performance issues.
H) Plate pack coalescer
Plate pack coalescers are typically supplied as square blocks comprising parallel plates with a specific plate angle (typically 45° or 60°) and plate spacing. The plate angle and the plate spacing varies depending upon the service (severity of fouling), efficiency requirements, etc. During installation of a 60° inclination of plate angle coalescer, some blocks were flipped and not oriented correctly, thus resulting in the blades making 30° with the horizontal instead of 60° as intended by design. The whole installation happened without the presence of vendor representative, and the error was caught during documentation when the vendor received final installation pictures for reference. The respective OEM and fabricator had to remove everything and reinstall the internals causing a delay in final shipment to the end customer.
Lessons learned:
- It is always good to have a vendor representative present during actual installation.
- Review internals drawings (along with notes pertaining to the installation) with installation crew in detail.
- Loosely assemble components on the ground to familiarize personnel with the general layout and the specific hardware locations.
- Have the field installation supervisor visit vendor shop during final QC inspection so he/she can have a first look at the mockup assembly.
- ALWAYS REQUEST INSTALLATION INSTRUCTION.
I) Separator shipped with internals installed
To save on cost and time, it is becoming a common practice to have the internals installed at the fabricator and then shipping the separator with internals already installed in the vessel. Things that could go wrong include
- Bolting coming loose.
- Because the vessel is transported in horizontal position, some vertically oriented separator internals shift to one side, thus creating gaps.
- Once the separator is installed at the site, proper inspection of all the internals is difficult (unless some internals are removed and reinstalled) due to manway location and the type/quantity of internals. Inspection is avoided as everyone is in a time crunch.
Lessons learned:
- When the vessel is shipped with internals installed in it, it is a MUST to recheck all internals after erection of the vessel at job site before startup.
- Don’t just look at the internals while rechecking. Make sure the hardware is torqued per vendor’s requirements for subsequent bolting sizes. Random checks will give a good feel for it.
- Convey upfront during the bidding stage to accommodate additional temporary bracing requirements for internals if the intent is to have the vessel shipped with internals installed in it.
- Design the internals to have internals manways to provide access to other internals.
J) Cyclones installed at the top of a contact tower
As a last example for the reader to ponder, a cyclone mist eliminator was installed at the top of a contact tower fitted with bubble-cap trays. The tower suffered from high liquid carryover.
- What do you think are the root causes?
The main lessons learned are:
- You don’t get what you expect; you get what you inspect!
- Do proper isolation of different materials.
- Don’t forget about accessories and material requirements.
- Look for the obvious mistakes such as gaps in the mist eliminator flow coverage.
- Be aware of transport requirements for internals preinstalled in a vessel, and do a reinspection after vessel is installed on site.
- Training, training, training.
If you have a separator story to share in a future article, the author may be reached at r.w.chin@att.net.
Read the Savvy Separator Series for in-depth insights about all things separation-related.
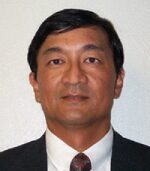
Robert (Bob) Chin is a cofounder and past chair of the SPE Separations Technology Technical Section. He is author/editor of the series of Savvy Separator articles published in SPE Oil and Gas Facilities magazine, and creator of the Savvy Separator Training From Home Video Series. Chin is a consultant and cofounder of Padden Engineering. He retired from Shell in 2014. He joined the company in 1981 and conducted advanced research on multiphase flow, leak detection, and separations. In 1999, he left the company to form a separator design and supply company. He returned to Shell in 2006 and led teams in facilities for enhanced oil recovery and subsea processing research and development. He may be reached at r.w.chin@att.net.
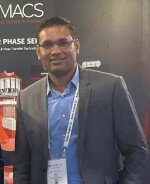
Moize Turkey is the vice president of engineering at AMACS Process Tower Internals, where he is responsible for technology development, benchmarking, and qualifications for phase separation and mass transfer internals. Over 16 years of his tenure, his experience with AMACS (previously ACS) includes process/applications engineering, technical sales, operations, and project management. He currently leads the pre-order sales engineering team, along with project management and mechanical design and drafting. Turkey serves as the communications chairperson of the SPE Separations Technology Technical Section and is an active member of the API 12J Committee. He holds an MS degree in chemical engineering from Texas A&M University–Kingsville and a BE in chemical engineering from University of Pune, India.