The 2010 Macondo oil spill marked a major turning point for the oil and gas industry. Whatever one thinks of the incident’s causes, the stringent safety and environmental regulations that came afterward fundamentally altered how offshore operations are conducted. But even before the incident, the challenges were already stacking up as operations moved into deeper waters with deeper, more deviated wells, higher pressures and temperatures, and the growing use of non-aqueous drilling fluids. All these factors have a determinative bearing on the system used to displace the drilling fluid and clean out the wellbore.
Displacement Before and After
Ideally, a displacement operation should displace the solids-laden drilling fluid with minimal fluid interface, remove all the residual solids, and leave the surfaces water-wet for an optimal completion phase. The presence of solids during the completion phase can cause crevice corrosion and hydrogen-sulfide stress cracking of metal tubulars, as well as damage the permeability and porosity of the geological formation, and that would negatively impact productivity from the reservoir.
Prior to Macondo, displacements were usually indirect, underbalanced, and quite slow to ensure a thorough cleanout. An indirect displacement entails the use of an intermediary fluid between the drilling and completion fluids. Most offshore operations entailed the use of enormous volumes of seawater pumped into the wellbore at pressures below the hydrostatic pressure of the formation (underbalanced) and then often simply discharged into the ocean. This technique is effective at providing a very clean, solids-free wellbore that also lessens the time and costs associated with using spacers and filtration, but it has some serious drawbacks. First, it’s not ideal from an environmental standpoint. Second, the use of an intermediary fluid adds time to the operation. Third, underbalanced pressures carry the potential for reservoir pressure to overwhelm the wellbore, leading to kicks and even a blowout, which of course pose serious safety and environmental risks.
The post-Macondo regulations said that operators had to maintain two barriers at all times, every barrel of fluid coming out of the well had to be accounted for, and any discharge had to be more environmentally benign than before. As a result, most operators switched to balanced or overbalanced displacements that were direct, without an intermediary fluid like seawater, but still conducted them slowly. This technique proved to be far from ideal, though, with unsustainably high volumes of fluid interface, in some cases upward of several thousand barrels of fluid requiring replacement, and levels of remaining solids so high that one would be hard-pressed to call the operation ‘wellbore cleanout’.
Most displacement systems consist of spacers formulated with surfactants—surface-active agents that reduce surface tension to captures solids and wet tubing surfaces—or both solvents and surfactants. The problem with systems containing solvents, which are usually petroleum-derived, is that they don’t work well with water-based fluids. The problem with surfactant-only systems is that they aren’t so good at cleaning away many synthetic-based muds, like those formulated with ester-isomerized olefin.
Innovating a New Kind of Displacement System
Confronted with a seemingly insurmountable problem, the industry really needed to totally rethink the chemistry and mechanics of offshore displacement, but it was a tall order. Any new solution would have to meet several demanding criteria with regard to safety, efficacy, regulations, and economics—namely, it would have to be:
- cost-efficient;
- environmentally friendly;
- powerful in removing solids;
- effective at leaving surfaces water-wet;
- capable of performing at high bottomhole temperatures; and
- dense enough to displace the denser non-aqueous drilling fluids used in ever-deeper wells.
Always eager to tackle a new challenge, scientists of the TETRA Innovation Group set about developing a solution and came up with the TETRA Advanced Displacement System or TADS,™ a 3-phase clear-brine solution designed for optimal wellbore cleanout. Engineered for use in the direct or indirect displacement of water-based, oil-based, and synthetic-based drilling muds, the system is highly effective at removing solids and rendering tubular surfaces water-wet for the completion phase.
But TADS is not a static, one-size-fits-all technology. It undergoes continuous improvement and is customized for each application. Based on wellbore conditions as well as the types of drilling and completion fluids the operator is using, TADS is composed of a tailored blend of low- or high-density halide brines and TETRAClean 900-series chemicals.
TADS Case Study No. 1
An operator in the Gulf of Mexico set out to temporarily abandon a deepwater well for later completion without the need for additional circulation or filtration. Water depth was about 2,000 feet and well depth 26,000 feet, with bottomhole temperature at 260°F. The first phase was a ‘dirty’ displacement using a custom-formulated high-density, solids-free, corrosion-inhibiting suspension fluid compatible with the Q125-alloy casing to displace the 16.5 lb/gal solids-laden synthetic-based mud that had been in the well for more than five years. The second phase was undertaken 10 months later and entailed the application of a high-density, solids-free TADS formulated with calcium bromide and zinc bromide.
Although TETRA engineers were confident the displacement and cleanout would be more than satisfactory, the operation actually exceeded expectations, greatly reducing the number of wellbore cleanout strings both to suspend the well and later to initiate the completion phase. The TETRA solutions ultimately saved the operator $5.4 million, provided a more efficient temporary abandonment, and yielded an ideal preparation for the completion phase.
TADS Case Study No. 2
An operator in the Gulf of Mexico used TADS in a subsea well in 4,400 feet of water to displace a 14.4 lb/gal isomerized olefin-based mud with a 13.9 lb/gal calcium chloride and calcium bromide completion fluid. TADS removed all the mud and residual solids from the wellbore and riser, returning the completion fluid to the surface with only 75 barrels of contaminated fluid interface. By contrast, before TADS was applied, contaminated fluid returns typically ranged from 700 to 800 barrels. TADS reduced solids loading on the diatomaceous-earth filter press, enabling longer filtration cycles and lessening cleanup time. Turbidity was reduced 94% to 14 NTUs with negligible solids, and examination of the wellbore cleanup tools showed very effective hole-cleaning and water-wetting of tubular surfaces.
A Solution for the ESG Era
Since its introduction, TADS has repeatedly proved to be exceptionally effective at displacement and wellbore cleanout. The system meets all the key criteria: it’s cost-efficient, environmentally friendly, effective at removing solids and rendering surfaces water-wet, capable of withstanding elevated bottomhole temperatures, and can be formulated dense enough to displace the weightier drilling fluids used in extremely deep wells.
Regarding outcomes, TADS is tailored to each job so it produces the best results possible. It’s so effective at cleanout that wellbore cleanout tools come out of the hole looking practically new, it minimizes fluid contamination and reduces waste, and it cuts rig time and displacement costs. Crucially, too, is that it’s environmentally friendly, a major benefit as regulations continue to grow more and more restrictive with each passing year. Finally, in recognition of its excellence, TADS is a 2022 winner of a Hart Energy Special Meritorious Award for Engineering Innovation.
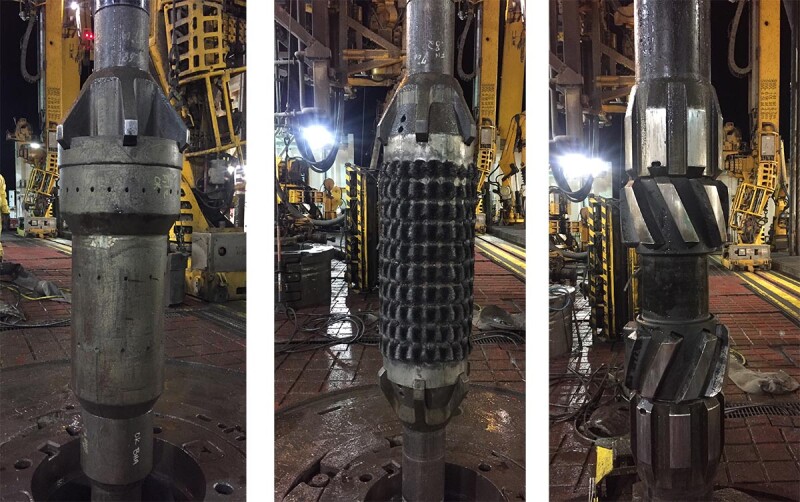
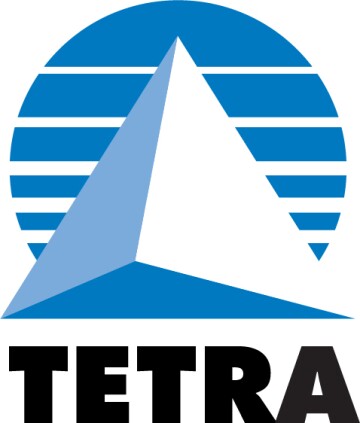