The recent surge in development of CO2 carbon capture and storage (CCS) projects has brought focus on the requirements for corrosion resistance in the injection wells as required by US Environmental Protection Agency (EPA) permitting.
In some cases, the long successful history of various metallurgies in enhanced oil recovery (EOR) wells has been cited as sufficient to allow the same completions for CCS injection wells. The lack of actual data on the long-term performance of these alloys in EOR wells in combination with the more stringent requirements for Class VI wells suggests otherwise.
Introduction
The recent significant influx of large amounts of government incentives for a variety of green initiatives including CCS and CCUS has created a rush to drill and complete CO2 injection wells. However, the necessary corrosion data to make informed choices for corrosion resistance in these wells is minimal at best. Some oil and gas professionals have argued that there is no difference between the more than 40 years of petroleum experience with CO2 EOR and planned CCS wells.
This comparison is not a valid one and can be risky considering the need for very long-term containment of CO2 required by regulators. This article presents a comparison between CO2 EOR and CCS for injection well metallurgy and explains why this comparison is invalid.
Background and Comparisons
There is a 50-year successful history of CO2 EOR in petroleum production that has led to a consensus, largely without merit, that corrosion of injection-well equipment is manageable and does not result in long-term degradation of certain components such as casing.
The reason there is little or no merit to applying this experience to CO2 CCS wells is the lack of data specific to the long-term corrosion resistance of casing that remains in the EOR wells. Rather, the industry generally simply plugs these wells with cement, and in the majority of cases without examining the casing before abandoning. Furthermore, industry rarely returns to inspect them after years of abandonment.
In a few instances, logging and retrieval of cement cores and casing have been performed and analyzed. For example, analysis of cement and casing from the SACROC field that had been exposed to CO2 for over 30 years showed corrosion along the casing-cement interface (Carey et al. 2007). Laumb et al. (2016) reported substantial casing corrosion for a CO2 EOR well in the Weyburn field based on a series of logs over several years. Koplos et al. (2007) provided survey data from numerous CO2 EOR wells and found that 11.1% of the wells failed mechanical integrity tests and concluded that injection-well mechanical integrity is a concern for CO2 injection and storage due to the corrosivity of CO2 on downhole materials.
There are also many factors that are significantly different between these two methods of CO2 injection. For one, EOR wells are typically shallower than CCS wells, and therefore the temperatures and pressures are often lower than for CCS. Moreover, the formations are often uniquely different. In the case of EOR, the formations are often partially depleted reservoirs containing some amount of oil in place that can moderate the corrosivity. In the case of CCS, the formations are typically high-salinity, nonpotable aquifers.
Another important difference between EOR and CCS wells is that historically the source CO2 for EOR was from gas plants that had few impurities such as typically H2S or occasionally small amounts of mercaptans. On the other hand, CCS injectate streams can contain numerous impurities depending on the source of the CO2 that can have a significant impact on corrosion of downhole equipment. These impurities are rarely seen in EOR.
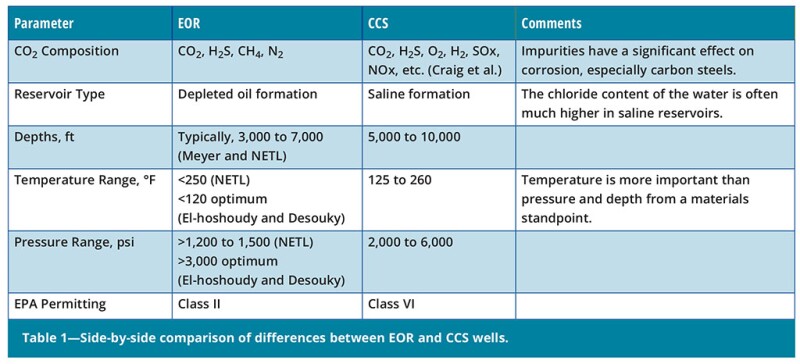
Another important difference between EOR and CCS wells is the permitting requirements. In most cases EOR wells are covered under EPA Class II wells while CCS and CCUS are required to conform with EPA Class VI requirements.
The EPA requirements for Class VI wells are:
“Ensure that the materials planned for all well components are compatible with the planned injectate and formation fluids that may be encountered, and that they can resist corrosion for the duration of the project.”
Similar language is included in 40 CFR Part 146 Subpart H for Class VI wells.
"All well materials must be compatible with fluids with which the materials may be expected to come into contact …”
First of all, carbon-steel casing is never considered corrosion resistant under any circumstances, and secondly, the design life of many CCS wells can be 30 years or longer. Specifically, the EPA requires post-injection site care for 50 years after injection.
There are no such requirements specific to casing, tubing, packers, etc. for Class II wells.
Under no circumstances can carbon-steel tubulars be characterized as corrosion resistant; therefore, corrosion-resistant alloys (CRAs) must be considered for components exposed to the reservoir fluids in contact with CO2. The selection of the appropriate CRA for a specific well environment is a complicated process as detailed elsewhere (Craig, Rowe, and Doll et al. 2023).
Also, for Class VI wells but not required for Class II and EOR wells:
“The Class VI Rule requires Class VI permit applicants to develop and implement a comprehensive testing and monitoring plan for their projects that includes injectate monitoring, corrosion monitoring of the well’s tubulars, etc.”
Similar language is again reflected in the CFR. It is required that corrosion monitoring be performed with corrosion coupons or loops according to Class VI permitting, and that mass loss and thickness loss be measured.
This requirement implicitly assumes coupons are made from carbon steel which is not the case for the use of CRAs in the injection zone. By and large, CRAs don’t suffer from mass loss or thinning in these CO2 injection streams. Rather if they are susceptible to corrosion, it will take the form of pitting or crevice corrosion which in many cases will not be observed on coupons.
Conclusions
Since there are currently no standards or guidelines on what would be considered acceptable corrosion damage to casing and tubing in CCS wells, and since Class VI wells are required to resist corrosion for the duration of the project, the only choice for these components when water is expected to be present is CRAs.
For Further Reading
Analysis and Performance of Oil Well Cement With 30 Years of CO2 Exposure From the SACROC Unit, West Texas, USA by J. William Carey, et al. International Journal of Greenhouse Gas Control (2007).
Wellbore Corrosion and Failure Assessment for CO2 EOR and Storage: Two Case Studies in the Weyburn Field by J. Laumb et. al. International Journal of Greenhouse Gas Control (2016).
A Review of Injection Well Mechanical Integrity by J. Koplos, et. al. IEA Greenhouse Gas R&D Programme 3rd Well Bore Integrity Network Meeting, 12–13 March Santa Fe, New Mexico (2007).
Guidelines for the Selection of Corrosion Resistant Alloys for CCS and CCUS Injection Wells by B. Craig, A. Rowe, M. Warmack, et al. International Journal of Greenhouse Gas Control (2023).
Summary of Carbon Dioxide Enhanced Oil Recovery Injection Well Technology by J. Meyer. API (2007).
Carbon Dioxide Enhanced Oil Recovery. NETL (2010).
CO2 Miscible Flooding for Enhanced Oil Recovery by A. El-hoshoudy and S. Desouky. IntechOpen (2018).
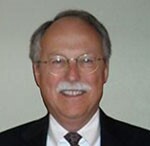
Bruce Craig is an SPE member and subject matter expert in metallurgy and corrosion with MetCorr in Denver, Colorado. He holds BS, MS, and PhD degrees in metallurgical engineering from the Colorado School of Mines. For more than 40 years, Craig has been involved with the selection of the facilities metallurgy for oil and gas projects around the world, including Mobile Bay in the Gulf of Mexico (shallow water), deepwater Gulf of Mexico, the Rocky Mountains, Asia, and the Middle East. In addition, he has most recently been involved in metallurgy selection for CCS and CCUS injection wells.
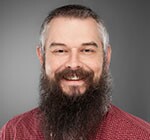
Adam Rowe is an SPE member and principal metallurgical engineer with Stress Engineering Services in Houston. He holds BS and MS degrees in metallurgical and materials engineering from the Colorado School of Mines. Rowe has specialized expertise in material evaluations, corrosion assessments, welding metallurgy, additive manufacturing, and metallurgical failure analyses. He has worked on a large variety of projects across several different industries, and recent project experience includes addressing manufacturing, fabrication, and corrosion concerns in CCS, hydrogen storage, and offshore wind developments.