Oil production in the Eagle Ford play is now more than 600,000 BOPD. Advances in horizontal drilling have made exploration of unconventional hydrocarbon resources commercially viable, and production in Eagle Ford will only continue to increase for years to come. The positive effects of this include potentially decreasing foreign imports of oil, and thousands of new jobs in the area.
However, the challenges for operators in exploiting this unconventional resource have been enormous, ranging from finding adequate human resources, transportation, infrastructure, formation evaluation, and water management.
With so many challenges front and center, chemical management can be relegated to the end of the priority list. However, there is a price to be paid for this, and it comes to light at a later stage in the life cycle of the well.
An inefficient chemical management system can not only be a major contributor to operating expense (Opex), but can lead to later problems with flow assurance and infrastructure integrity—corrosion and possibly even failures, particularly from hydrogen sulfide (H2S) corrosion.
Recognizing this, operators have recently become more mindful of implementing metric-driven chemical management programs (CMPs).
Challenges in Implementing CMPs
Two immediate challenges arise when trying to put in place a CMP in an unconventional resource like Eagle Ford. The first is consolidating production data from different wells, and the second is standardizing the collected data.
Data Consolidation
The first challenge concerns the nature of oil wells in an unconventional field. Where, in a conventional field, fluid from several wells comes together at one facility, therefore immediately consolidating the well production level data, at Eagle Ford for example, the wells may be so spread out and numerous that this may be impossible (Fig. 1). Therefore, chemical data management is conducted primarily at pad level or facilities level, but not at field level.
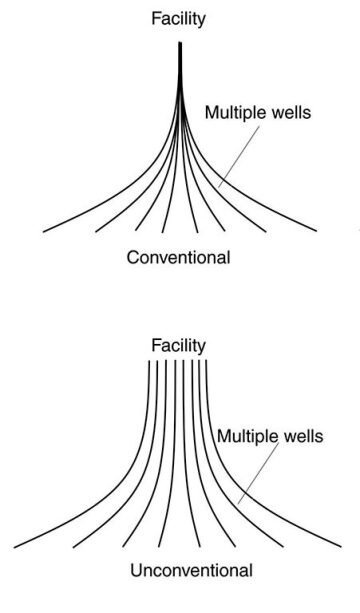
Data Standardization
The second challenge is data collection and reporting. To be able to use production data to perform statistical analysis for chemical management, as explained later in this paper, the data must be in a standardized format.
There is a need for adequate communication between the service providers and the operators so that field service reports are gathered in standardized formats. The data can then be pooled for analysis and identification of trends in chemical dosing.
In an ideal scenario, the operators, the service providers, process engineers, and production chemistry experts would all work together, submit their data in standardized reports that are gathered in a shared database, and a data analyst could run the models and analysis for successful management of chemical dosing and operation costs. In reality though, these organizations operate in silos with little communication between the field and the engineering team. Data are collected, but not used in a manner that is meaningful to managing the asset’s performance and deriving a continuous improvement program for Opex management.
Identify KPIs
A successful CMP must begin with identifying key performance indicators (KPIs) upfront. All the stakeholders must agree to the KPIs, which must be specific and define the expectations for every involved party for every application.
Examples of KPIs include the following:
- Zero incidents for health, safety, and environment
- Downtime for chemical injection pumps
- A 7-day supply of all chemical inventory available 90% of the time
- A database of recommended treat rates for every injection point maintained and actual chemical injection rates within 10% of the recommended rate
- Chemical storage tank levels always above 20% of the required level
- Oil export spec of 1% basic sediment and water met at all times
- H2S content on export oil and gas
- No downtime due to paraffin plugging
Table 1 shows an example of a typical KPI matrix that operators can set up to assign roles and responsibilities and manage data tracking.
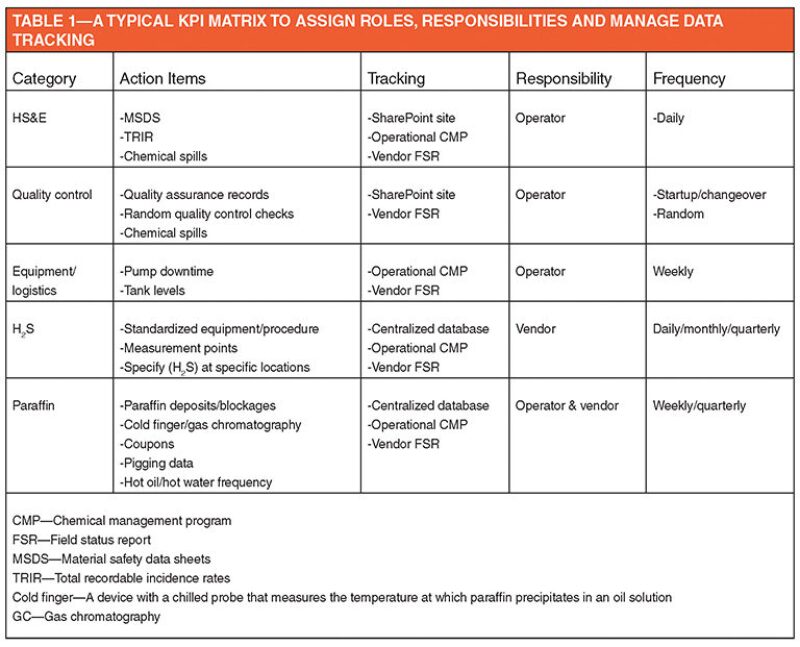
For each KPI, define how often measurements are to be taken, and/or the data are to be reported, and specify the format, or use a standardized form so that the data collected can be integrated into a database. For the purposes of tracking, operators can use a centralized database such as an SQL server, SharePoint sites, or Spotfire, an analytics platform. An “operational CMP” is a simple one-page document (a checklist) that field operators can use for reporting and daily monitoring and tracking of their chemical programs. This makes it possible for data from different sources to be consolidated and analyzed.
To manage chemical and service programs to achieve set KPIs, a performance or statistical framework can be used.
Performance Framework
Managing chemical treatment with a performance framework is a popular method in CMPs. However, it is crucial that operators and service providers create, share, and agree on KPIs, and monitor and adhere to them. Taking measurements at various points and looking at the overall operational results is the difference between out-of-control and carefully managed operating costs.
Injection of H2S Scavenger
The injection of an H2S scavenger is common in several Eagle Ford fields and a basic component of chemical programs. Two metrics to be tracked are concentration of H2S before chemical treatment ([H2S] untreated) and concentration of H2S post chemical treatment ([H2S] treated). Using these two values, scavenger efficiency can be calculated (lb of H2S scavenged/gallon of chemical).
Several other factors contribute to efficiency, including the following:
- Residence time
- Water cut
- Type of H2S scavenger (oil- or water-soluble)
- Injection strategy
- Treatment strategy (multiphase, gas phase, retention loops, and towers)
Fig. 2 is an example of using graphic visualization for decision-making for a chemical program. Scavenger efficiency was calculated from several Eagle Ford wells, which had similar residence times and in which a chemical was injected in multiphase with injection points located downstream of the choke valve. The evaluating KPI was a minimum of 0.15 lb of H2S scavenged/gallon of chemical.
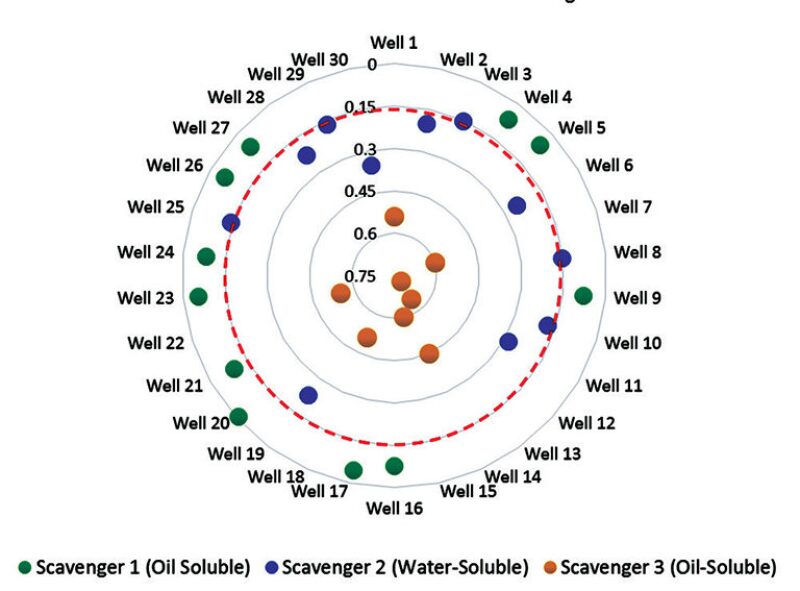
The graphic visualization, a target where numbers closer to the center are better performers than those at the periphery, shows immediately which chemicals are working most successfully. Scavenger 1 lies outside the KPI metric, therefore the operator needs to move away from this chemical in the field. Scavenger 2 and 3 meet the minimal KPI specification, but Scavenger 3 is more efficient than Scavenger 2.
Operators can also take economics into consideration when making decisions: Scavenger 3, an oil-soluble chemical, is approximately three times more expensive than Scavenger 2, which is water-soluble.
A visual representation of data in this manner creates a feedback loop for service providers that is based on actual performance data and minimizes the risk of higher than necessary Opex.
Pitfalls Associated with Lack of Monitoring
The cost of overtreating with an inefficient chemical is twofold. Firstly, it increases operating costs with no perceived benefit. Secondly, overtreating, specifically with water-soluble scavenger chemistries, can lead to secondary flow assurance issues caused by an increase in the water pH, and also have an adverse effect on process component performance, such as scaling. Underdosing could mean not seeing the benefits of the chemical program, and flow assurance and integrity management issues could crop up.
Best Practices for Use of H2S Scavenger
Determine the recommended injection rates for H2S scavenger based on theoretical stoichiometry with a correction factor based on operational experience and measured H2S concentrations in produced fluids. A target should be set to keep all injection rates within 10% of design rates to avoid unnecessary expenses with over-injection, but should be optimized based on monitoring results.
All metrics should be shared with service providers, including requirements for residual H2S levels at different locations in the process stream. This way, everyone knows the target that needs to be met, and can make educated decisions about chemical injection, which results in optimization of the cost benefit.
This is best executed by putting in place a standardized procedure for measuring H2S with all required equipment available in the field. For example, H2S content could be measured daily at each wellhead having an H2S concentration greater than 500 ppm, or weekly for wells with lower concentrations. The measurements could be used to determine the optimal injection rate for each well on a weekly basis. H2S levels in the gas phase and export line can be measured daily to ensure they meet the requirement.
Optimization of H2S Scavenger Application
To ensure optimization of the process, H2S should be measured quarterly in all three phases, and a chemical optimization trial conducted. Random wells should be sampled using Millipore filters to ensure that no solids are produced as a result of chemical injection, and any recovered solids analyzed to determine their nature and source. Ionic analysis should be conducted on high-water-cut and high H2S-producing wells at least every 6 months. Scale coupons should be installed in wells to monitor scale deposition, and 10% of these extracted quarterly on a rotational basis. In addition, scale monitoring can be done in strategic locations using sidestream devices and pressure drop as a metric.
Prevention of Paraffin/Wax Buildup
A best practice for managing paraffin inhibitors in a performance framework is when operators do their own due diligence to identify which chemicals are most effective in preventing paraffin buildup. By comparing the performance of different chemicals and understanding the laboratory tests and analyses required to make these determinations, the operators can independently evaluate the performance of the chemical services.
As with H2S scavengers, once a recommendation is set, actual performance of each chemical should be measured and then analyzed to optimize the right concentrations of paraffin inhibitor required to meet KPIs. The amount of paraffin collected after treatment should be measured to ensure that it is significantly different from the amount collected before treatment as a testament to the effectiveness of the inhibitor.
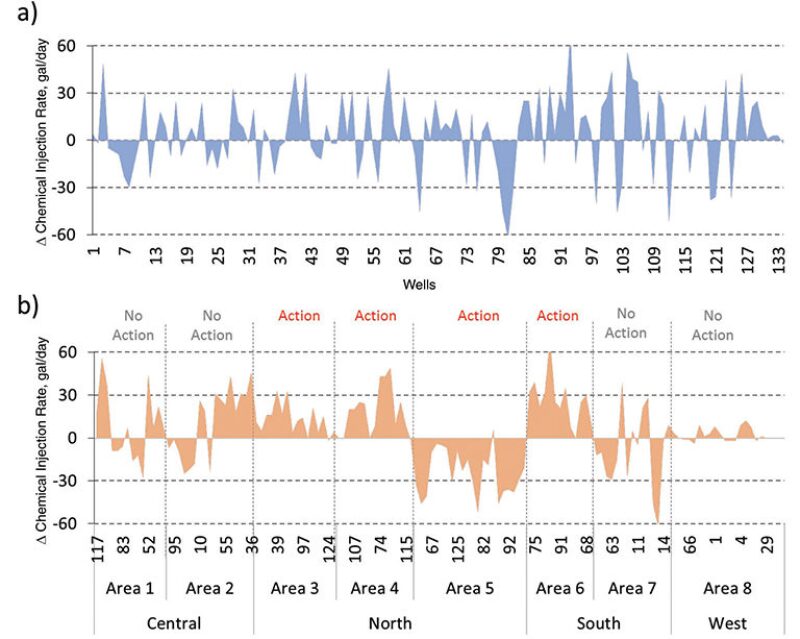
To measure program effectiveness, pressure drops along well flowlines can be measured and monitored daily to ensure that there is never more than a 30% increase at constant flowing conditions. Coupons can be installed on high-paraffin-content wells and withdrawn on a rotational basis with quarterly reports of the data collected. The suction pressure of the export pump, the frequency with which the export pump strainer is changed, and the quantity of paraffin recovered from the strainer are metrics to be included in the service reports and monitored. A cold finger test and gas chromatography analysis should be performed every 6 months. (The cold finger test uses a device with a chilled probe to measure the temperature at which paraffin will precipitate in an oil solution.) A good benchmark for paraffin inhibitor success is cold finger test results that indicate more than 50% protection for 80% of the wells.
Statistical Framework
CMPs can be improved by putting in place a statistical framework by which the program is monitored and managed.
Standardize Data Collection
Standardization of data collection is the first step in implementing a statistical framework. All reports should be tracked by well, facility, and field name, and more importantly, service providers and operators should make sure that the names used for each well, facility, or field are the same across both parties’ reports.
Ideally, the data analyst will provide a standard form on which data can be recorded. This data can then feed into a database to be collected in a centralized location.
Collected data can include the following:
- Health, safety, and environment performance
- Recommended dosage rates and the technical basis for treatment rate
- Actual dosage rate of chemicals with percentage of recommended rate
- Equipment downtime
- Personnel in the field
- Samples and analyses results
- Usage, delivery, and inventory of chemicals
- All KPIs
Calculate Base Recommendation
To successfully assess injection performance, the service provider and operator should use available data to create a base recommendation for injection, against which the actual amount of chemical being injected can be compared. As data are collected and the chemical performance is monitored, the recommendations can be adjusted, and the actual amounts injected can be continually measured. For every injection point, the service provider must record the actual amount injected as compared to the recommendation.
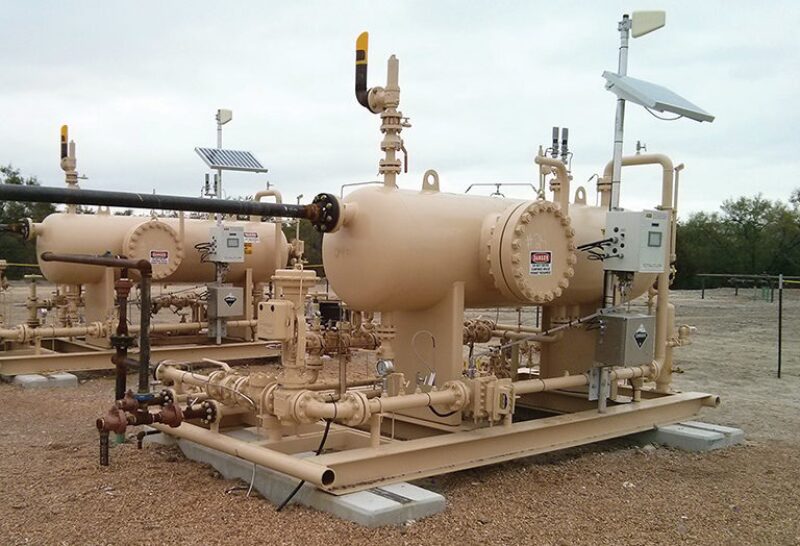
Calculate Deviations From Recommended Chemical Injection Rates
Fig. 3 shows a discrepancy between the actual amount of H2S scavenger injected versus the recommended amount for several wells in the Eagle Ford play.
The data were manipulated to show the statistical deviation for each well (how many gallons over or under the recommended amount were injected). The deviations on the top are positive, indicating over-treatment, whereas those at the bottom show under-treatment.
To convert the information embedded in Fig. 3a into actionable data, the deviations were consolidated by geographical area. The wells were grouped into geographical areas, and the deviations were summed up for each area—illustrating an overall picture by geographical area (Fig. 3b).
The representation and review of data in this way provides an analyst with a clear picture of the action that can be taken by identifying areas of over-treatment and under-treatment. If the data are collected on a weekly basis and analyzed over each quarter, a system is established to provide checks and balances on over-use or under-use of chemicals.
A similar statistical approach can be applied to a paraffin inhibitor program. Data are collected and reported as above and the deviations from recommended amounts are calculated.
In areas where there is over-treatment with paraffin inhibitor, but without resolution of paraffin deposits, the effectiveness of the chemical can be investigated, instead of continuing to increase the chemical injection rate.
Where there are no deposits, the amount of chemical injected can be continually adjusted and results observed and recorded to find the minimum amount of inhibitor required to achieve the desired results.
Recording the data and creating graphs and visualizations gives operators a way to effectively monitor chemical delivery and performance in the field. Multiple chemical programs over several years and across assets can be effectively evaluated and managed with as little as one visualization.
Continuous Improvement in Chemical Treatments
Frequent measurement and monitoring of chemical treatment is important because H2S levels can change dynamically. Therefore, the recommended rate does not stay steady, and a system needs to be in place to monitor and make the adjustments.
Several factors can lead to over-treatment or under-treatment, including a lack of monitoring and bad weather, which causes solar-powered pumps to go down.
With regular data monitoring, the deviations can be brought into check and a baseline agreed upon beyond which deviations will be investigated. For example, constant deviations of more than 10% over a defined period could be cause for an investigation.
Conclusions
Gathering and monitoring metrics is an effective way to implement chemical management in unconventional plays. Beginning with the identification of agreed upon KPIs, implementation of a CMP must be put into place systematically. Operators, engineers, and service providers must communicate clearly to agree upon KPIs and then collect and share data in a standardized fashion. The data can be fed into one database for analysis.
A performance framework monitors and evaluates performance data to determine the necessary alterations. The data can include the efficiency of H2S scavengers or paraffin inhibitors and the performance of different chemicals. Data collection and sharing is vital to the process.
A statistical framework lays down a base recommendation against which actual injection amounts are compared and deviations from recommendations are continually monitored. The base recommendation is revised and optimized using performance data. Deviations from the recommendation are continually monitored so that significant deviations can be addressed and over-treatment or under-treatment avoided.
Both approaches keep Opex in check while minimizing flow assurance and infrastructure integrity issues and meeting export specifications. Using graphic visualizations gives stakeholders another tool in their arsenal to quickly evaluate the effectiveness of their chemical programs and make data-driven decisions.
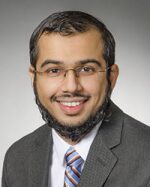
Huzeifa Ismail is a consultant in production chemistry and process modeling at Maxoil Solutions. He has addressed production engineering and chemistry needs and challenges in the oil and gas industry for more than 6 years, first at Baker Hughes as a subject matter expert and then at Maxoil. He has authored more than 20 technical articles and holds numerous patents. Ismail holds a BA and MS in chemistry from Brandeis University and a PhD in physical chemistry from the Massachusetts Institute of Technology. He can be reached at hismail@maxoilsolutions.com.