For offshore exploration and production projects, corrosion is an accepted occupational hazard because there is no way to stop it completely. Over time, it will negatively affect the life of an asset, sometimes to a significant degree.
Inhibitor fluids are widely accepted as an optimal method for slowing corrosion rates and mitigating its damaging effects on a system. Nevertheless, operators and service companies are continuing to find new ways to better the process.
This feature takes a look at the work being done by companies to improve corrosion inhibitor fluids and inhibition techniques for offshore projects.
Clariant: Phosphate Ester-Based Inhibitor
As there is no technological answer to why oxygen, which plays an important role in the corrosion process, is present in a system, most oilfield corrosion inhibitors are developed under the presumption that no oxygen will be present. This means that most inhibitors perform poorly in solutions containing oxygen such as water (Wang and Wylde 2011). Typically, additional chemicals must be used to handle the increase in corrosion that comes from injected oxygen, with phosophate esters being among the most popular
(Yepez et al. 2015).
Last year, the oil service unit of Clariant, a specialty chemical company, tested the performance of a phosphate ester-based inhibitor against a commercially available imidazoline-based oxygen corrosion inhibitor at its laboratory in The Woodlands, Texas. The company wanted to see if the phosphate ester could limit the amount of additional chemicals typically used with traditional corrosion inhibitors. It used a potentiodynamic polarization technique in the presence of oxygen and carbon dioxide and conducted open-circuit corrosion experiments to examine the electrochemical behavior of each inhibitor.
The experiments used a brine containing 3.5% sodium chloride (NaCl), and the corroding gas was a mixture of 3% oxygen (O2) and carbon dioxide (CO2). Another experiment using 100% CO2 gas was also performed. The metal used in the experiments was a carbon steel.
Clariant conducted rotating cylinder electrode tests under the following conditions:
- Condition 1: 3% O2 balanced with CO2 gas in 3.5% NaCl
- Condition 2: 100% CO2 gas in 35% NaCl
- Condition 3: Inhibitor B (imidazoline-based commercial oxygen corrosion inhibitor) in 3.5% NaCl plus 3% O2 balanced with CO2 gas
- Condition 4: Inhibitor A (phosphate ester-based corrosion inhibitor plus sulfiding agent 2) in 3.5% NaCl plus 3% O2 balanced with CO2 gas
- Condition 5: Sulfiding agent in 3.5% NaCl plus 3% O2 balanced with CO2 gas
- Condition 6: Phosphate ester plus sulfiding agent 0 in 3.5% NaCl plus 3% O2 balanced with CO2 gas
- Condition 7: Phosphate ester plus sulfiding agent 4 in 3.5% NaCl plus 3% O2 balanced with CO2 gas
The sulfiding agent was systematically varied in the phosphate ester for some of the given conditions.
The injection of a different inhibitor into the solution from condition 1 produced conditions 3 through 7. The corrosion rate for each condition was measured from the intersection of the anodic and cathodic Tafel slopes (Table 1). A Tafel equation determines the rate of an electrode’s electrochemical reaction to its overpotential.
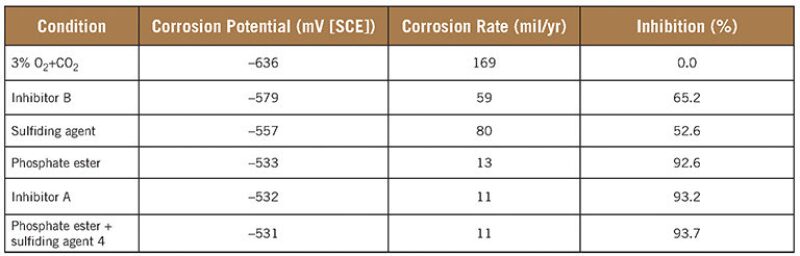
The degree of corrosion inhibition in the experiments was related more to the inhibitors’ anodic protection, where the chemical converts the electrons of the metal surface into the anodes of electrochemical cells, vs. their cathodic performance, where the electrons of the metal surface become the cathodes of electrochemical cells. Omar Yepez, a senior integrity management chemist at Clariant, said that this relationship was because of the phosphate ester-based inhibitor's effect on the the anodic current, as shown in Fig. 1.
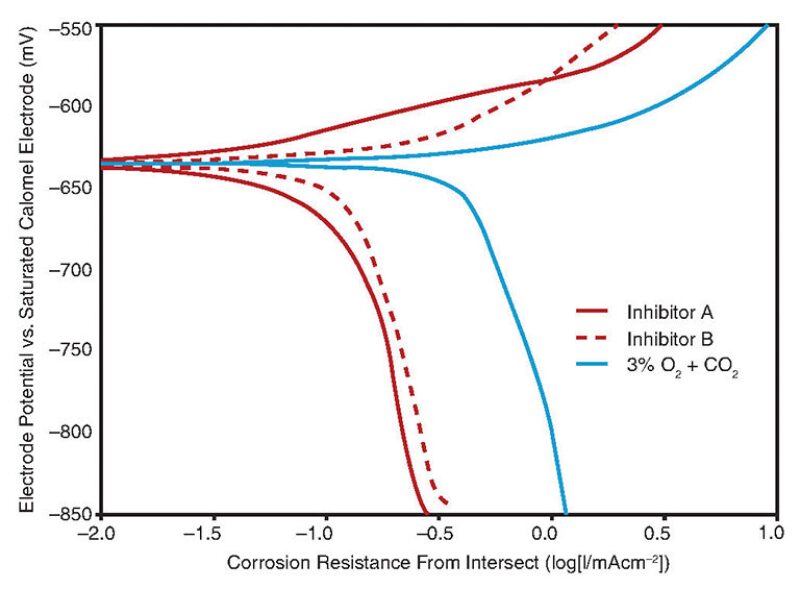
“In the cathodic branch of the curve, the imidazoline-based inhibitor is more or less similar to the phosphate ester-based inhibitor, whereas in the anodic branch of the curve, the phosphate ester-base inhibitor reduced the anodic current at least 10 times more than the imidazoline-based one,” he said.
Yepez also said he was surprised to see similar corrosion potentials for conditions 1 and 2, even though the cathodic and anodic currents for condition 1 were higher than those for condition 2.
“I was expecting something near 120 mV (SCE), but I measured –636 mV instead,” he said. “This is near the corrosion potential of carbonic acid corrosion, which is
–638 mV. This happened because the steel surface is not iron, in which case I would have measured 120 mV (SCE). The steel surface was iron oxide.”
A saturated calomel electrode (SCE) is a reference electrode.
The measured corrosion potential of carbonic acid corrosion was close to the standard potential of reactions in conditions 3 to 5, which was approximately -689 mV (SCE), but the measured corrosion potential for oxygen corrosion (–636 mV) differed significantly from the standard potential of reactions in conditions 2 to 4 (120 mV). As the presence of oxygen changes the steel surface potential, it was difficult to measure oxygen corrosion potentials (Yepez et al. 2015).
Imidazoline adsorbs under carbonic acid corrosion, which means no lateral reaction between adsorbed molecules occurs. It will be protonated at the pH of a given solution, meaning that a proton will be added to each molecule to form the conjugate acid in the solution. The protonated imidazoline heads will be attracted by the steel surface because the cathodic reaction makes them negatively charged. This also prevents water from reaching the steel surface, a process known as geometric blocking.
Because phosphate strongly adsorbs on oxidized iron surfaces, the phosphate ester-based inhibitor presented a higher inhibition of the cathodic current compared with imidazoline in the experiment, Yepez said. This produces a film on the steel surface that prevents water from reaching it, a process known as geometric coverage.
The study concluded that imidazoline acts as a good anodic inhibitor because the amidoamine compounds, a byproduct of imidazoline industrial production, act as a tridentate ligand that anchors ferric cations. However, Yepez said that phosphate esters are better inhibitors than imidazoline-based agents because the sulfiding agent prepares the steel surface for a significantly stronger interaction with the inhibitor, which allows the phosphate esters to perform well in anodic and cathodic conditions.
“The phosphate ester needs an oxidized surface, and the presence of oxygen does not guarantee that the entire surface will be oxidized,” he said. “The sulfiding agent helps this to happen, thus the phosphate ester made for a better coverage of the (steel) surface.”
Baker Hughes: Antiagglomerant Chemistry
In deepwater systems, operators often use low-dosage hydrate inhibitors (LDHIs) as an alternative to thermodynamic inhibitors, such as methanol or monoethylene glycol, to manage hydrates because they control agglomeration at lower dosages, thus requiring smaller storage capacities and creating fewer logistical challenges (Panchalingam et al. 2015). Antiagglomerants (AAs) are a popular type of LDHI since they allow hydrates to form while still limiting the growth and buildup of hydrate crystals. However, some AAs present a risk of pitting corrosion for offshore umbilical chemical delivery systems.
Baker Hughes tested these pitting tendencies on stainless and duplex steels in its attempt to develop an inhibitor that would address the problem. From 2013 to 2015, the company ran the electrochemical test method of cyclic potentiodynamic polarization (CPP) and an immersion test of stainless and duplex steels in solutions containing various AA formulations.
LDHIs must meet stringent criteria before they are injected into the umbilical lines of deepwater applications. Two of the most important criteria are the viscosity of the formulated products and the compatibility with the umbilical’s material of construction.
Vaithilingam Panchalingam, a research scientist of products and technology at Baker Hughes, said the specifications are often set by customers because meeting the deliverability requirements is particularly important in long-reach subsea tiebacks. Chemical compatibility with the umbilical’s material of construction is important to the overall integrity of the system.
A third crucial element of subsea chemical injection is the overall stability of the chemical, said Panchalingam, a coauthor of the paper detailing the study.
“If the product precipitates at a low temperature, it can deposit along the umbilical or settle to the bottom, which can lead to plugging,” he said. “If the material decomposes at high injection temperatures and forms materials, it can again plug the umbilical.”
AAs are typically injected at a high concentration range over a long distance, which makes the pitting corrosion risk in the umbilical a significant challenge for operators. To eliminate corrosion risk entirely, a possible solution is to switch from a methanol-based solvent package to a nonalcohol-based package, However, nonmethanol solvents create a high viscosity in the AA formulation, which negatively affects the applicability for a deepwater system (Panchalingam et al. 2015).
Table 2 lists the AAs used in the experiments. The researcher said that AA-B was more valuable to the experiments because it is based on improved technology, thus leading to better treatment efficiency than AA-A. The corrosion inhibitor used in the test is an additive that is commercially available from Baker Hughes. The study referred to this additive as additive C.
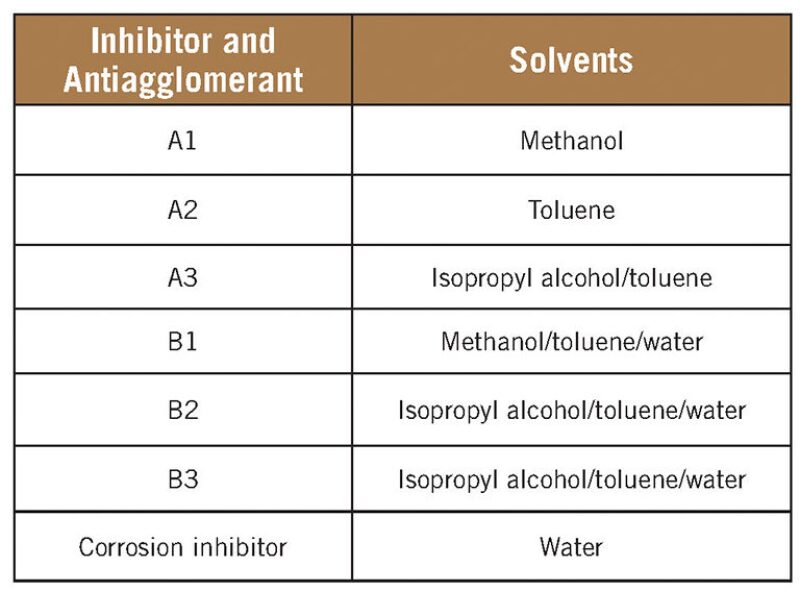
The CPP test showed that additive C changed the open circuit potential on the stainless steel to a more cathodic value, and the protection margin increased (Fig. 2), which suggests that the additive reduced the tendency of pitting for the antiagglomerant formulation. Positive hysteresis happened in CPP tests with and without the corrosion inhibitor.
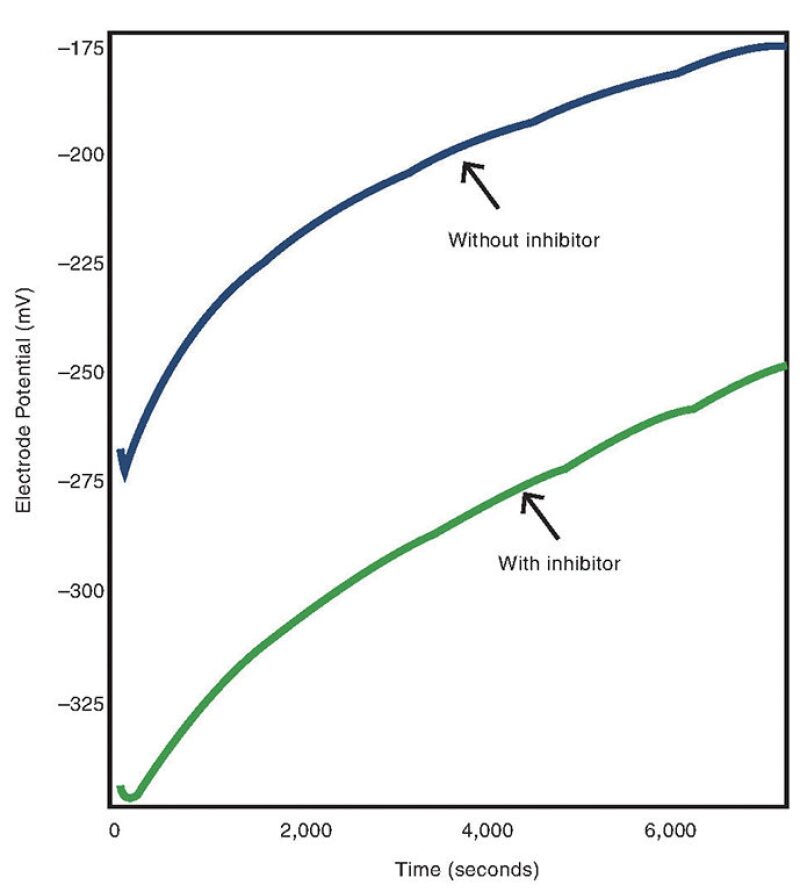
For the duplex steel, the CPP tests also showed positive hysteresis with and without the inhibitor. However, the current increased in the passivation region up to the pitting potential, while the stainless steel experienced no change in current. This meant that the duplex steel was a more active material.
The immersion tests showed no signs of pitting on the stainless steel after 30 days, 60 days, and 90 days. However, the duplex steel showed pitting, indicating that corrosion was not stopped under the given test conditions. Increasing the inhibitor volume from 1.5% to 3% produced some improvements. The duplex steel experienced no pitting after 30 days, but pitting occurred after 60 days.
To fix the problem, a new solvent package was created with toluene and isopropyl alcohol as the solvents. The blend protected the duplex steel against pitting for AA-A, but it did not show any protection for AA-B.
Panchalingam said the water in AA-B was the primary reason for the lack of corrosion protection on the duplex steel because water solvates the chloride, which tends to promote corrosive behavior. The solvent switch from methanol to toluene confirmed the observation. Results of a CPP test of AA-B made with the least amount of water showed pitting protection for the duplex steel with no additional corrosion inhibitor, while a test on the stainless steel showed that a lower volume of 0.5% corrosion inhibitor was needed to protect against pitting.
The tests showed that adding the corrosion inhibitor and switching the solvent caused no adverse effect on the performance of the AA.
Modumetal: Nanolaminated Alloys Used in Coatings
The search for better corrosion protection does not only involve developing fluids. A company, Modumetal, is working on nanolaminated alloys that could potentially lessen the need for operators to use inhibitor fluid in offshore facilities.
The company uses an electrochemical process to coat metal components. Similar to electroplating, this process involves the immersion of metals in a bath containing different types of metal ions to create a thin layer of coating. The process is repeated several times by varying the electrical current in the bath to control the way the ions are deposited, with each layer building on top of another and up to a desired overall thickness (Bullis 2015).
Christina Lomasney, president and CEO of Modumetal, compared the nanolayers to the rings found in the cross section of a tree, which are formed by changes in the tree’s surrounding environment. Putting two dissimilar metals together leads to a greater control of the nature of the interface between them, and this control improves in the performance of an alloy, she said.
“We’re leveraging that phenomenon,” Lomasney said. “We’re controlling it. We’re putting dissimilar metals together with a little bit of potential difference. It’s not quite as dramatic a difference as, say, steel versus zinc, but if we create a little potential difference, we find that we can create zinc that performs better than a homogeneous zinc.”
Nanolayer coatings may help with extending the life of an asset by strengthening the metal components used in facilities. Another benefit of the technology is the protection against corrosion, as the nanoscale layers delay the exchange of electrons in electrochemical reactions that leads to corrosion. While nanoscale coating is not a direct alternative to the injection of corrosion inhibitors, the protection it provides could allow operators to use less inhibitor fluid over time, potentially saving costs.
“You use a corrosion inhibitor to prevent that kind of electron exchange,” Lomasney said. “Now, if you don’t have that in the first place, or if you have a coating that’s providing that kind of protection, then you don’t need as much chemical to provide that protection as well, and so the whole idea is not only to reduce the cost of corrosion inhibition, but also to reduce the cost of the asset itself.”
The company tested one of its latest nanolaminated materials, the NanoGalv zinc-based coating, for corrosion in several settings. Modumetal performed a salt-fog performance test comparing its technology with hot dipped galvanized steel panels. The tests were carried out until more than 5% of the surface of the panels was covered in red rust or 4,300 hours had passed, whichever came first.
The hot dipped galvanized steel panels showed rust after 744 hours of testing, while no rust formed on the NanoGalv panels. Another salt-fog test of studs and nuts stressed to 10% yield strength produced similar results. The NanoGalv-coated metals showed no signs of corrosion after 240 hours of exposure (Lomasney et al. 2015).
These coatings were also tested in offshore field trials conducted with ConocoPhillips and the United States Coast Guard. Lomasney said the technology is suited for harsh offshore environments, particularly in warmer climates.
“It has more to do with the environment the facility is in than anything else,” Lomasney said. “So if it’s a particularly aggressive rig located in a hot, tropical environment like a lot of them are, and if there’s a lot of seawater around like a lot of them tend to have, those are the types of environments where we see an opportunity.”
Last year, Modumetal expanded its prototype production facility and commissioned the construction of a new facility that will support the production of coatings and claddings for production and casing tubulars. Lomasney said the company can produce components as long as 15 ft, and that it hopes to scale that capability up to 45 ft by the end of the year.
Although it has been in existence for a long time, the technology that produces nanoscale coatings had not been widely used because the manufacturing processes were impractical, Lomasney said. She described previous production attempts of the material as better suited for small samples of model system alloy. However, she said her company seeks to be a viable commercial alternative.
“We can do it on a large scale,” she said. “We’re building up the infrastructure.”
For Further Reading
OTC 25830 Developments in Nanolaminaated Materials to Enhance the Performance and Longevity of Metal Components in Offshore Applications by C. Lomasney,L. Collinson, and T. Burnett, Modumetal.
SPE 173721 Development of Novel Anti-Agglomerant Chemistries with Reduced Localized Corrosion Potential to Stainless and Duplex Steels by V. Panchalingam, Z. Liu, G. Rivers, et al., Baker Hughes.
SPE 173723 Development of Novel Phosphate Based Inhibitors Effective for Oxygen Corrosion by O. Yepez, N. Obeyesekere, and J. Wylde, Clariant Oil Services.
Bullis, K. 2015. Nano-Manufacturing Makes Steel 10 Times Stronger. MIT Technology Review. (accessed 13 May 2015).
Wang, H. and Wylde, J. 2011. Corrosion Inhibitor Development for a Slightly Sour Environment with an Oxygen Intrusion Issue. Journal of Materials Science and Engineering 5: 41–55.