The Oil and Gas Facilities Savvy Separator series continues with its eighth article, this time on level settings and control in gravity separators.
When a separator has been designed, constructed, and installed, and the feed enters the separator, the levels are the most readily available variables to control the behavior of the unit. They serve multiple purposes: control the (superficial) velocities and residence times for the different phases in the separator; ensure that the various internals are surrounded with the environment they are designed to work in; and ensure that the downstream process is fed with fluids suitable for their requirements.
When the level controller struggles and the level falls outside a predetermined range, the operator is alerted or the process shuts down. This is to protect the process for off-specification situations, be it for machine protection, health/safety/environmental (HSE) concerns, or to maintain product specifications.
The level instrument is the sensor that determines the location of the level, and the level controller is the unit that manages the level. Level instruments and controllers are responsible for more than 70% of reported separator failures. Sometimes the instrument or controller just fails on its own, but sometimes it works exactly as intended and the failure is due to the selection of an inappropriate instrument for the service, or a limited understanding of the multiphase separation process and how it affects the selected instrument. This article attempts to cover some of these aspects.
Types of Gravity Separators and Associated Levels
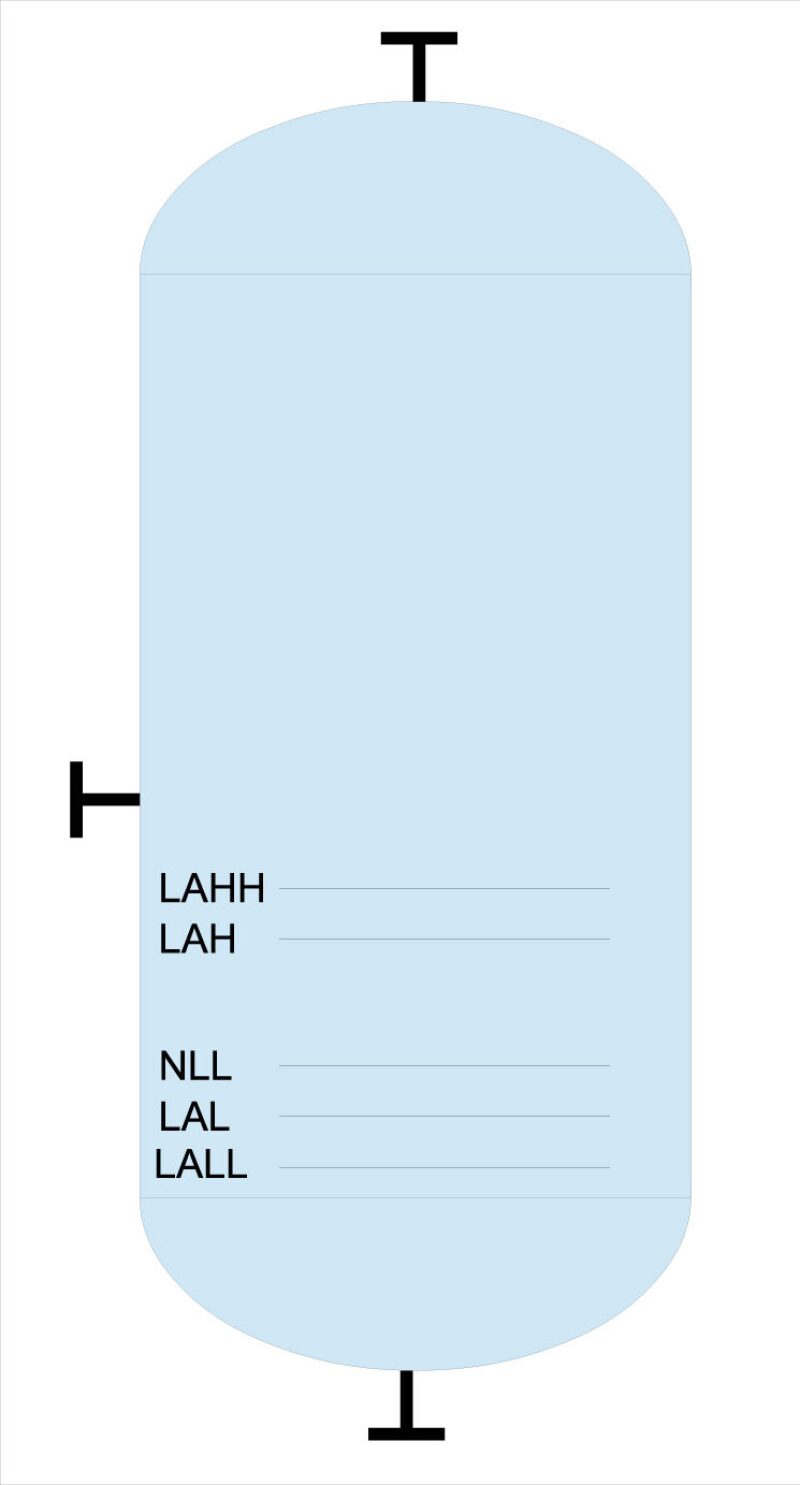
There are two main types of gravity separators in upstream service: two-phase (gas/liquid) and three-phase (gas/liquid/liquid).
The gas/liquid separators are often vertical as the separation is frequently limited by liquid removal from gas and controlled by gas velocity/momentum. A vertical vessel allows utilization of the full cross-sectional area for gas flow (Fig. 1). The gas/liquid/liquid separators are often horizontal as the liquid/liquid separation is settling- or coalescence-limited. In this case, a large interface area between oil and water is desired together with the settling velocity component being (advantageously) perpendicular to the main flow direction (Fig. 2).
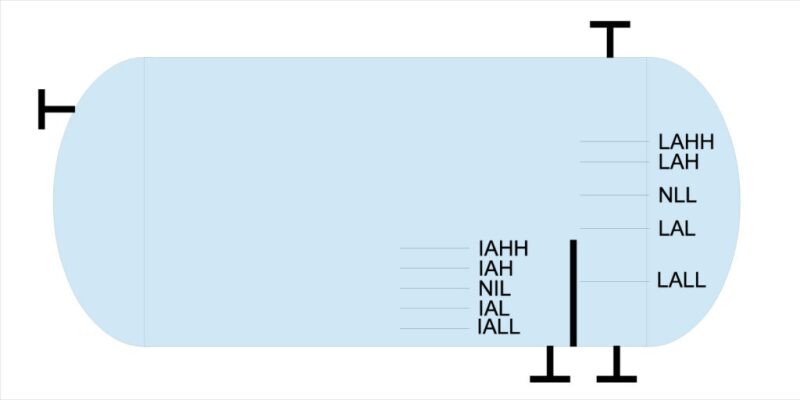
In a two-phase separator (Fig. 1), we are only concerned with one interface (e.g., the gas/liquid interface, the liquid level, or the liquid surface, etc.). We imagine a sharp transition between the gas and the liquid phase, and we design our level control system to manage the location of this transition. For the process calculations, we assume a level set point and name this the normal liquid level (NLL).
The separator is supposed to produce outlet qualities specified for each product, depending on the service and the downstream process. If the levels deviate far from their intended settings, the performance is at risk and the separator cannot be assumed to produce acceptable effluents: the surroundings must be protected, typically from a machine or HSE perspective. Machine protection is implemented to protect rotating machinery such as compressors or pumps. So we assign trip or shutdown level settings for these events, and a shutdown can be required on both a very low (LALL) and high (LAHH) level.
In between this, we want to give the operator a chance to intervene if the automated control system is unable to manage the level, so we assign alarm levels: a level alarm low (LAL) and a level alarm high (LAH), where an alarm notifies the operator that action is required. We can therefore have five defined levels: the normal liquid level (NLL), the low and high alarm liquid levels (LAL+LAH), and the low and high trip (or shutdown) liquid levels (LALL+LAHH). If there is a slug volume to be included (when sudden liquid transients enter the separator), an extra space is assigned between the normal and high alarm levels to provide volume for this. When the slug arrives, the operator is not bothered by an alarm.
In a three-phase separator (Fig. 2), there is one additional phase to control and one additional level to be concerned with (e.g., the liquid/liquid interface, or the interface level). The same process is followed: We imagine a sharp transition between oil and water and we set up a system to manage this. So now, we have up to five new interface level set points, otherwise similar to the gas/liquid levels: the normal interface level (NIL), the interface alarm levels (IAL+IAH), and the trip levels (IALL+IAHH).
A final word on levels: Only include the ones needed. If there is no requirement to shut down the process, the shutdown trigger can be omitted. For example, in a primary three-phase separator, the process can often live with some water in the oil and, therefore, does not require an IAHH. On the other hand, if there is no time for the operator to react, don’t include the alarm levels and only assign trip levels—the alarms will disturb the operators and they will anyway be notified about the eventual trip.
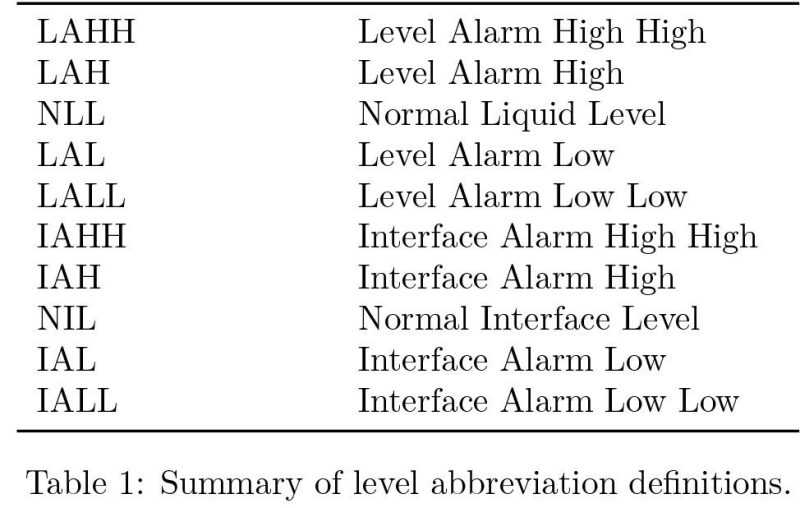
According to the Engineering Equipment and Materials Users Association (EEMUA) Publication 191 (2013), any alarm requiring less than 5 minutes response time is categorized as “immediate,” while Pinkney (2011) uses ≤ 10 minutes. And Harvey and Buddaraju (2012) showed a typical response time of 15–25 seconds for alarm response in a control room environment.
A summary of the levels described in this article is provided in Table 1. The alarm and shutdown levels have different names in different environments (e.g., level alarm low low [LALL] is also referred to as low level shutdown [LLSD], low low liquid level [LLLL], level switch low low [LSLL], and so on).
Standards and Typical Requirements
There are both process and automation requirements associated with the level settings. The process requirements are for obtaining sufficient outlet qualities and ensuring that internals dedicated to processing a certain phase are able to do just that (Fig. 3).
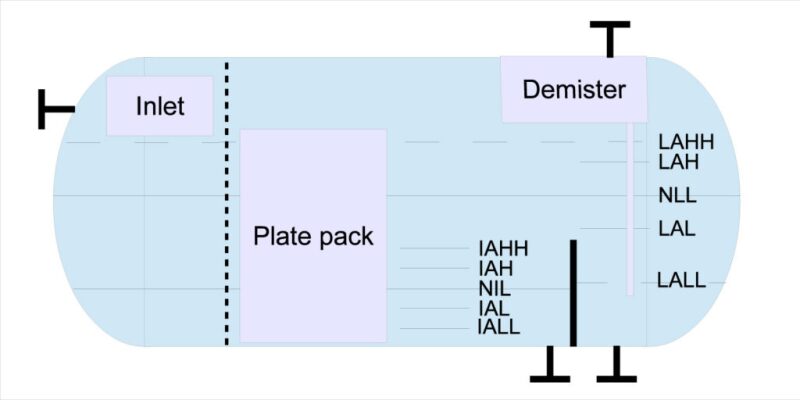
The inlet is usually required to be above the liquid surface (above LAHH) to avoid foaming, while plate packs work in the liquid phase (below LAHH). Gas cyclone demisters, having slight underpressure in their drain tubes, must be elevated a certain distance above LAHH, and the drain exit must be submerged below LALL. In addition, there are often residence time and interface area requirements for the liquid phases in order to achieve sufficient settling/creaming and separation of mixed phase layers (foam and emulsion), as well as cross-sectional area requirements (above LAH and LAHH) for the gas phase in order to keep the (superficial) velocity low.
The automation requirements are usually given in terms of time between levels (time between high and low alarm, or between alarm and trip) for operator intervention in terms of alarms, or machine/HSE protection in case of shutdown. These timing requirements are judged toward the design feed steady-state conditions, often with a required engineering margin. Also, automation requires a minimum distance for the level height measurement resolution—which may be increased if the vessel undergoes motion (e.g., on a floating, production, storage, and offloading vessel).
The American Petroleum Institute’s specification API 12J (2008) provides residence times as a starting point for process requirements. Actual residence time for separation is not based on the total volume of liquid in the vessel due to factors such as turbulence and nonuniform flow. The actual separation residence time (coupled with separation length) needs to be designed such that the required performance is achieved.
The Norwegian standard NORSOK P002 (2014) gives both process and automation requirements. The process requirements define liquid residence volume as the quiescent section (i.e., downstream of a flow-straightening plate), somewhat more conservatively than API. NORSOK P002 also specifies a minimum margin of 10% to the design rates for scrubbers, but does not provide residence time criteria based on oil characteristics. The automation requirements are a minimum of 30 seconds between levels (normal to alarm, alarm to trip) and a minimum of 100 mm. The automation requirements, however, include the full liquid volume (e.g., upstream the straightening plate and downstream the weir). Gas velocity requirements are included similar to API 12J, but are modified for high pressures following Gas Processors Suppliers Association (2004). For draining of demister internals, a margin of 100% is required on available drain height vs. liquid column from demister pressure drop.
Many operating companies, contractors, and vendors have their own practices or specifications to these issues as well, with more or less detail. These are, in general, proprietary. Some typical criteria in two-phase separators are mentioned by Bothamley (2013).
Typical Level Design Procedure
The process design data sheet is the starting point for level design, and normally contains the design cases which specify flow rates, densities, and viscosities. Surface and interface tensions should be included, but the data source and quality should be scrutinized. Based on the service of the separator (wellhead or farther down in the process, upstream a compressor, on a floater, and so on) there may be additional requirements for design margins.
For a vertical two-phase separator, the gas velocity is often the sizing criterion, so the minimum diameter to obtain the required velocity for the highest gas load is first determined. The liquid levels are then calculated based on the automation requirements, degassing/defoaming, etc. for the highest liquid load, and the vessel size is then determined. From a cost/weight perspective, a desirable length/diameter (L/D) ratio is typically between 3 and 5; if the ratio is higher, it may be advisable to increase the diameter and redo the calculations (if it is lower, there is a lot of gas to process and there is limited scope to increase the ratio). For a horizontal three-phase separator, the process is slightly more iterative as the extra degree of freedom (the area is not uniquely given by one phase) results in multiple possible sizes: the gas flow will be in part of the cross-sectional area (and not the full, as for vertical separators). Still, the gas velocity needs to be kept within the requirements, the liquid levels must provide sufficient residence time as well as distance and holdup for control, and there must be physical space for the internals selected. The desirable L/D ratio is the same for horizontal as for vertical separators, so a fixed L/D of 3.5 and allocating two-thirds of the volume to the liquids may be a good starting point.
Level Instruments and Measurement Principles
All level instruments are based on measuring a parameter that varies between the different phases. Density is most commonly used, perhaps since density difference is also the basis for the separation process. Other principles in current use are based on electromagnetic or acoustic properties. Several technologies are discussed further below and in an SPE webinar, Level Control Detection Selection.
When measuring the level based on density, the control system interprets some sort of average reading. For an externally mounted instrument (which includes most of them), this reading is between the instrument level nozzles. The Bernoulli equation applies (neglecting losses):
\(p_1 + \rho_1 g h_1 + \frac{1}{2} \rho_1 v_1^2 = p_2 + \rho_2 g h_2 + \frac{1}{2} \rho_2 v_2^2\)-----------------------(Eq. 1)
\(p\) is pressure, ρ is density, g is acceleration by gravity, h is height and v is velocity, at different locations (1 and 2) in the same flowing fluid system. With a differential pressure (DP) level instrument we read a pressure difference ∆\(p\) = \(p\)1 − \(p\)2 between the level nozzles at h1 and h2. We assume that the velocity components can be neglected (make sure that this is reasonable, as discussed later), and the two clean phases with densities ρ1 and ρ2 combine with respective heights \(h'_1\) and \(h'_2\) (summing up to the height H between the nozzles) to produce this static pressure difference. If phase 1 is the heavy phase, \(h'_1\) is then the interface level between the two imaginary clean phases.
\(\Delta p |_{v \to 0} = \rho_1 g h'_1 + \rho_2 g h'_2 \\ = \rho_1 g h'_1 + \rho_2 g (H-h'_1) \\ = h'_1 g (\rho_1 - \rho_2) + \rho_2 g H \\ \)
\(h'_1 |_{v \to 0} = \frac{\Delta p - \rho_2 g H}{g (\rho_1 - \rho_2)}\)
For a gas/liquid interface, if the gas (phase 2) contributes very little (again, make sure that this is reasonable, to be discussed later), we eliminate that as well:
\(h'_1 |_{\rho_2 \ll \rho_1, v \to 0} \approx \frac{\Delta p}{\rho_1 g}\)
Frequently used density-based level instruments are:
Sight glass: An (external) translucent standpipe connected to the separator by nozzles and filled with process fluid. The bottom of the glass is connected to the heavy phase and the top to the light phase. The interface in the glass moves with the interface in the vessel and can be read manually or with optical sensors. Sometimes a flow gets induced in these (e.g., thermally induced) so that the interface in the glass deviates from what is inside the vessel. In heavy oil applications, they can cool down and the viscous oil gets stuck. Also, they can foul from solids or bacterial growth.
Floater: Similar to the sight glass except not necessarily in a translucent material: a floater with an intermittent density sits on the interface inside the standpipe and gives a signal to a sensor. In addition to inheriting some of the issues with sight glasses, the floater also sometimes get stuck even though the interface is moving.
Differential pressure (DP): Given the bulk phase densities, the interface is calculated by converting static head for the measurement range. They are typically connected to the separator with sensing lines, which can get filled with impurities (remote seal is available though).
Nucleonic: The density is measured between a (often internal) source and detector, and the interface is calculated given the bulk densities. These can be assembled into sensor stacks, measuring the density with approximately 20 mm vertical resolution—even solids buildup can be measured. They are, however, more advanced for the operators to use, and costly. It is possible to have nucleonic readings from outside the vessel, but the gamma rays will be attenuated through the vessel wall, which can increase the source size for thick-walled vessels, again requiring greater shielding for HSE purposes.
Commonly used instruments based on other principles may include:
Inductive probe: Measures the conductivity of the surrounding phase, and many inductive elements can form a sensor stack. As the conductance difference between oil and gas can be small, it is more suited for oil/water interface detection.
Capacitive probe: Measures the dielectric permittivity of the surrounding phase. The process fluid needs to be in contact with the sensor. These are subject to preferential wetting (typically these have a steel outer surface which is preferentially water-wet) and fouling.
Guided wave radar: A radar pulse is guided by a conductive rod into a multiphase region, and part of the wave is reflected at each dielectric discontinuity (between gas and oil, between oil and water)—so it actually measures the interfaces and does not produce an average interpretation. If there are mixed phases (foam, emulsion) there may be multiple reflections, or just the bottom or top of the mixture.
Sonar/ultrasonic: A sound wave is beamed toward the interface and the reflection is timed. This is typically only used to measure the gas/liquid interface—which is then directly measured. The signal may be diffracted in the presence of foam.
Level Controllers
The most used device for controlling a level in a separator is a control valve—the level control valve. It is also possible to use a pump, and modulate the motor frequency, or to use a fixed speed pump and a valve to control the throughput. There will be a controller sending a signal to the valve actuator (or motor variable speed drive), and this controller is most commonly a proportional-integral-derivative (PID) controller. P is the proportional constant, and is an amplification: the difference between the measured level and the desired set point is being amplified by P before outputting to the controller. If only P is set, there will never be steady operation as the level will oscillate around the set point with frequency from delays in the control loop and magnitude proportional to P. For this reason, controllers include I, the integral constant, which determines how far back in time the controller takes into account: higher I makes a slower controller and makes it more stable. With an I there is an over/undershoot of the set point which dampens out to a steady value. The D is the differential constant, and determines how much a sudden change in input is reflected in the output signal. For separator level control the D is rarely used.
Instead of a PID controller, there can be a high/low dump switch. This acts on two levels: when the level reaches a high set point, the switch opens the valve; when the level reaches the low set point, the switch closes the valve. If (near-) zero or very small liquid feeds are expected, a switch can be a good choice: an on/off valve (or fixed speed pump) can be used and can limit the valve action/wear. For typical liquid feeds the PID controller and a modulating control valve is preferred.
Finally, the flow is forced through the valve(s) by the pressure in the separator compared to downstream of the valve (or, in the case of the pump, the pressure differential and the pump hydraulic energy input) so it is preferable to maintain a fairly constant operating pressure as this will also impact the flow through the outlets. The gas outlet of the separator is commonly connected to a pressure-controlling system of some sort.
Common Problems, Mistakes and Pitfalls
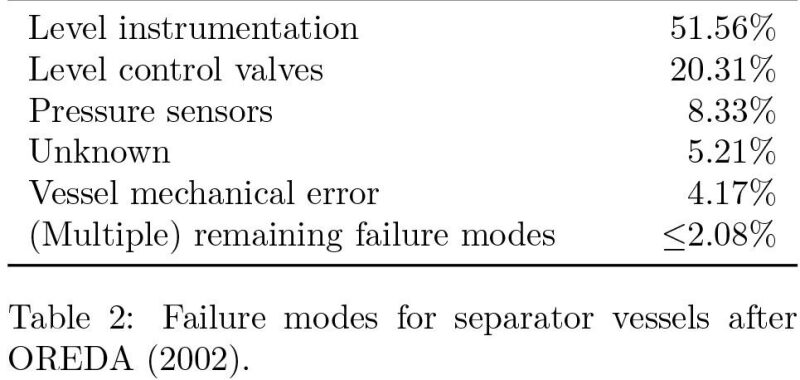
Following Offshore Reliability Data (OREDA 2002), the statistics that apply for failing separator vessels are as shown in Table 2. There are of course vastly different consequences between vessel rupture and level control failure, but the level instrumentation apparently has some room for improvement. Improving the level instrumentation and control extends to design of the separator and how we define levels, select instruments, and interpret their signals in the control setup.
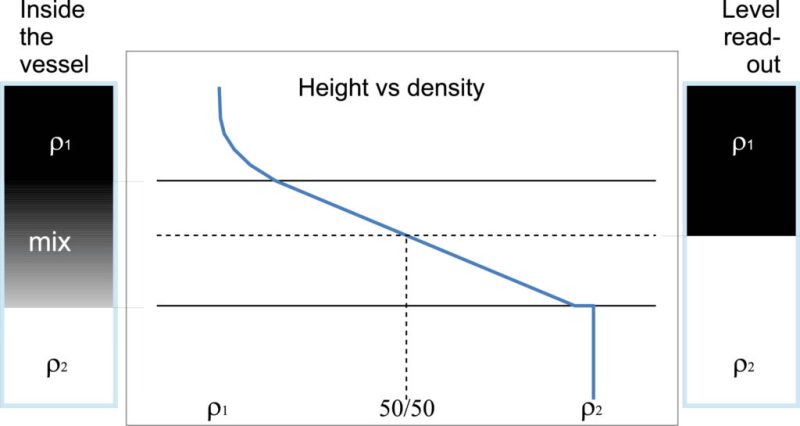
Earlier, we assumed sharp levels and well-defined densities for the various regions in the separators. This is unfortunately not always the case. There may be gas dispersed in the liquid, as rising bubbles or as foam. There may be dispersed water settling in the oil, forming a dispersion (or emulsion) layer. There may be both, and these mixed phases can be further stabilized by organic or inorganic precipitates, amphiphilic molecules, etc., which aggregate at the interface. These phenomena affect level instrument readouts differently based on the principle by which they work (especially the meters which are based on averaging). A visualization is provided in Fig. 4. The true interface of the mixed phase and the bulk phase is not detected, and the readout of the “clean”’ level based on the total hydrostatic height is somewhere inside the mixed phase (often near the 50/50 mark as the density profile is often linear).
- The sight glass is “calibrated” by nature to give the approximate 50/50 density interface between the measurement points (the nozzle connections). Whatever mixture is inside the vessel, when there is a sharp interface in the sight glass, this indicates the equivalent internal level where the density is equal to 50% of each phase, assuming that the nozzles are located in regions with pure phases. For example, if a light foam is present, the indicated level is near the bottom of this, and if there is a heavy foam, the indication is somewhere closer to the middle of the foam layer. If the sight glass contains a mixture, there is probably an induced flow in it, and the reading should not be trusted.
- Assuming that there is a sharp interface in the floater standpipe, the floater sits on this interface and gives the same reading as the sight glass (above).
- The DP level measurement is typically calibrated by the controls department to the average density equivalent; this can be changed but will produce an offset. It has been known to happen that the wrong density has been used in this calibration, which is something that cannot happen for the sight glass or floater standpipe.
- The nucleonic density sensor stack actually measures the density in 2-cm-high zones, so if desired, the mixture densities can be read directly and the true interface can be detected (or the 50/50 density if desired). There are few technical disadvantages to this instrument as long as the signal interpretation is done right (i.e., the density bands for the different phases—clean and mixed—are set up correctly.) Handling/HSE and regulatory requirements, however, are more complex when radioactivity is involved.
Problems are not solely due to the selected instrument principle; the designer sometimes errs as well. For a gas/liquid separator, the liquid phase can actually be a mixture of oil and water, and this mixture may separate to an unknown degree in the separator liquid volume, depending on factors such as the load. The operator may also want to run it with just one of the liquids without being concerned with recalculating the level controller based on densities. If the designer has assumed a fixed liquid mixture density when designing the levels, and kept the volumes to a minimum, chances are that the level control will “fail” with liquid carry-over or gas carry-under and no alarm or trip. It has occurred that the process data sheet providing input data for the design has contained a hypothetical “mixed” liquid phase with mixed properties and no information on the actual liquid phases entering the system, causing errors not only in the level design. This should never be done.
Remember that the gas phase weighs more than zero; if there is a high (maybe even high and varying) operating pressure, a low liquid phase density, and some distance between the level measurement nozzles, the weight of the gas will impact the level. The level instrument was typically calibrated for atmospheric conditions during the factory acceptance test, where the air has an insignificant density compared to the gas at process conditions. Even using the Ideal Gas Law will be better than just assuming zero gas density.
If there is a velocity component onto a DP cell sensing line, it will impact the reading. If there is a velocity component passing the level nozzle, it will set up a recirculating flow inside the nozzle, which will impact the reading. Traditionally the liquid velocity in gravity separators is in the order of 1 cm/s, and direct impact (with water) amounts to a dynamic pressure equal to around 5 µm water height. A typical liquid velocity in piping, 2 m/s, amounts to 20 cm height. Again, Bernoulli’s equation (Eq. 1) applies.
Some internals, typically plate packs and flow-straightening baffles, produce a pressure drop which can vary during operation, and which also results in a change in level across the internals. Keep this in mind also when placing the level instrument nozzles: place them where the sensors will measure the relevant level for control. And place instrument nozzles for both control and shutdown in the same zone so that they measure on the same level—or you may get uncorrelated behavior between your control and shutdown system.
Example: Level Control Failure
A two-phase gas/liquid separator with a mixed liquid phase had dual redundant level instruments: one based on DP and one nucleonic (not a sensor stack though—a sectionalized type where the reading was averaged over six zones, each of length 60 cm). During operation, a loss of level was experienced where the two instrument principles varied between each other (Fig. 5).
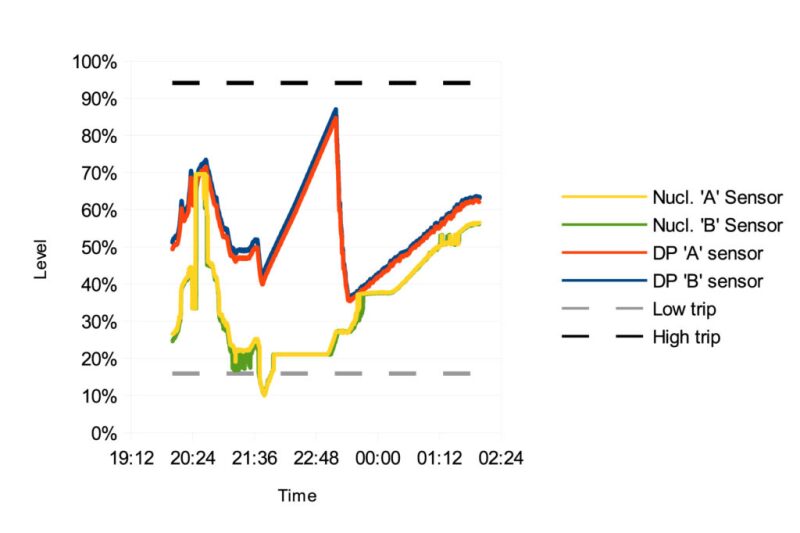
At the time, the separator was operated on DP level control and although the operators responded to the high level alarm, the instrument readouts were confusing and had already resulted in gas carry-under to the downstream pump. Looking at the chart, the level readouts are contradictory and it took quite some time and digging into the underlying control definition to figure out what had happened.
In this case, the designers knew that the liquid phase was a mixed system, and they also knew that they could not predict the degree of mixing in the liquid volume. However, since they had a sectionalized nucleonic detection system, they decided that they could use the reading from the lowest section and feed this back as the liquid density. This reading was then used as input for the DP level instrument.
It is highly doubtful whether the lower liquid density readout was representative of the liquid occupying the vessel—a robust design would have been to use a mixture liquid density and allocating margin on the low and high side for either pure liquid phase, but at least the issue was considered.
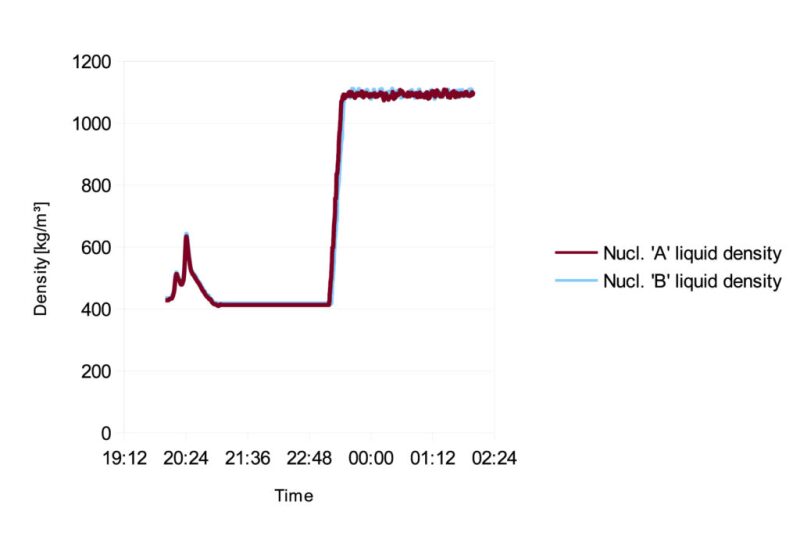
Looking at Fig. 5, both the nucleonic and the DP level instruments are dual and we see that the two DP signals agree internally, as well as the two nucleonic ones, so the instruments appear to be functioning. Digging further into the data log showed that the density returned by the bottom nucleonic probe progressed as shown in Fig. 6 (this density readout was not available on the operator screen). The lowest liquid density in the system was around 650 kg/m3, so values below this represent a mixture of liquid and gas. The instrument had then been limited by the vendor to not output liquid density values below 400 kg/m3, which is where the curve flatlines.
Reinterpreting the DP data set in Fig. 5 with a mixed liquid density of 875 kg/m3 gives data as plotted in Fig. 7. Now the DP curve makes more sense—the level had possibly already passed the low trip set point before the data were gathered, and is nowhere near the high trip. There is still a discrepancy between the DP and the nucleonic meter during loss of level; the underlying models used by the nucleonic meter to report level are unknown and have not been adjusted, but it is apparent from Figs. 5 and 6 that the density reading affects the reported level value also for the nucleonic level sensor. As such, the instrument principles implemented were not dual-redundant and displayed a common mode of failure in this case.
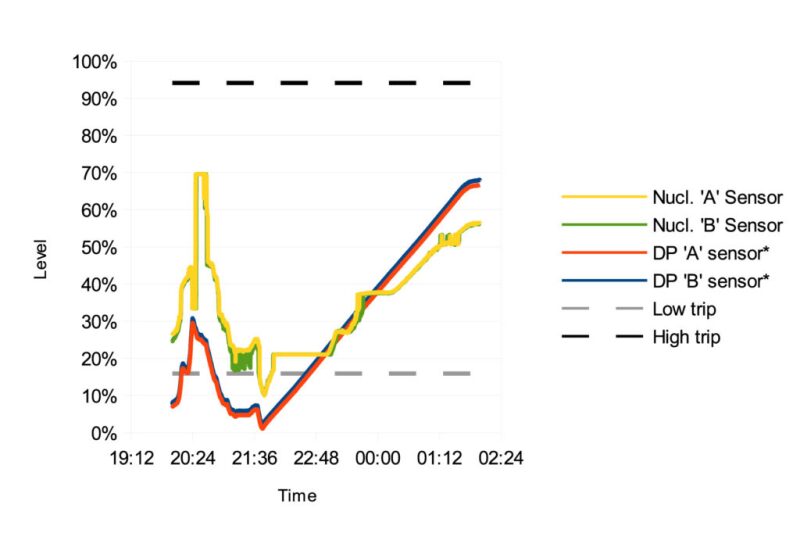
When the liquid level rises, there is a fairly constant offset between the two curves. This is then the effect of using an average liquid density for the DP and a measured one for the nucleonic, as well as not compensating for the weight of the gas (the separator was at the time filled with only aqueous phase as shown by the density return). This event was reported as a level instrument failure, but it was not the instruments that had failed: it was the logical signal interpretation.
Concluding Remarks
The level instruments available to us work by different principles and all have various advantages and drawbacks. The output they provide needs to be understood and correctly interpreted in the context of the multiphase environment in which they work. Today they are overrepresented in failure modes for separators, and this is in large part due to common misconceptions and misinterpretations of the multiphase separation process and inherent phenomena of mixed phases.
And know your Bernoulli.
For Further Reading
API 12J, Specification for Oil and Gas Separators. 2008. Eighth edition. Washington, DC: API.
Bothamley, M. 2013. Gas/Liquids Separators: Part 2—Quantifying Separator Performance. Oil and Gas Fac 2 (5): 35–47.
EEMUA 191, Alarm Systems. A Guide to Design, Management, and Procurement. 2013. Third edition. London: Engineering Equipment and Materials Users’ Association.
Level Control Detection Selection. 2013. SPE Webinar.
GPSA Engineering Data Book. 2004. Twelfth edition. Tulsa: Gas Processors Suppliers Association.
Harvey, C. M. and Buddaraju, D. 2012. Performance of Control Room Operators in Alarm Management. API Cybernetics Symposium.
NORSOK P002, Process System Design. 2014. First edition. Oslo: Standard Norge.
OREDA, Offshore Reliability Data. 2002. Fourth edition. Trondheim, Norway: SINTEF.
Pinkney, I. 2011. Rationalisation: Learnings from Practice. Abnormal Situation Management Consortium.
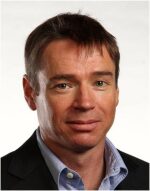
Richard Arntzen is a director of the SPE Separations Technology Technical Section. He is the principal technical expert of separations in Shell. He has 20 years’ experience in the upstream oil and gas industry, primarily with multiphase separation. Before joining Shell, he worked for 12 years with an engineering contractor. Arntzen works as a subsea process engineer in Norway and has worked with research and design, project engineering, commissioning, and testing. He holds a dr.ing. in chemical engineering from the Norwegian University of Science and Technology and may be reached at richard.arntzen@shell.com.