Global drilling contractor Nabors Industries announced that it has made an $8 million investment in the developer of an emerging technology called the "plasmabit" drilling tool.
Founded in 2008, the new investment means that Slovakia-based GA Drilling has now raised more than $20 million to field test and commercialize the tool which it says enables geothermal wells to reach as far as 5 miles below the surface by turning hard rock into mere specks of dust.
The companies noted in their joint announcement that part of their aim is to introduce the European-developed technology to the emerging geothermal market in the US. The investment in GA Drilling comes only a few months after the Houston-headquartered drilling contractor struck partnerships with three other geothermal technology companies, Geo-X Energy, SAGE Geosystems, and Quaise Inc.
“Given the expected sharp growth in global energy consumption over the next decades, the world will require an even sharper growth in sustainable energy supply. I am convinced that geothermal energy will be a key contributor to the necessary increase in clean energy generation,” said Nabors CEO Anthony Petrello in a statement.
As consumers and investors call for cleaner sources of energy, geothermal technology is becoming a bigger part of oil and gas investment portfolios for its ability to deliver hot water or steam to the surface that can be used to spin a turbine or provide heating to homes and buildings. However, the biggest drawbacks of geothermal energy projects thus far include the limited number of optimal drilling locations along with the historically high capital costs associated with accessing ultradeep hot formations.
By developing lower-cost methods of drilling deeper, the firms making this renewed push hope to greatly expand the geographic scope of geothermal projects.
"The present agreement will allow us to move faster through the final stages of plasmabit development, leveraging the synergies to integrate this revolutionary drilling tool into the systems of the rig," Igor Kočiš, the founder and CEO of GA Drilling, said in the announcement, adding, "With this collaboration, we have made another big step toward delivering on our promise of 'geothermal anywhere.'"
What Is the Plasmabit?
In a technical paper published in December 2021, SPE 207852, authors from GA Drilling describe the plasmabit tool as a pulsed plasma drilling technology that does not melt or evaporate rock but instead “allows thermo-mechanical rock breakage” using “very short high-energy pulses with high frequency which suddenly increases rock surface temperature, and, thus, disintegrates its surface.”
The paper outlines efforts to test and validate key components of the system, which include a transfer line comprising a “ruggedized umbilical” to deliver the power, plasma medium, and fluids to the tool. GA Drilling also proposes to use a coiled tubing unit instead of a traditional drilling rig.
Laboratory testing has shown that the tool itself, which relies on an electric arc combined with a chemically assisted plasma pulse, can break apart the hard crystalline rock that represents the typical target for most geothermal wells.
In a real-world application, GA Drilling explained that conventional drilling technology would still be required to drill through sedimentary layers of rock. This is because in these softer rock formations, conventional drilling systems are able to achieve a more competitive rate of penetration (ROP).
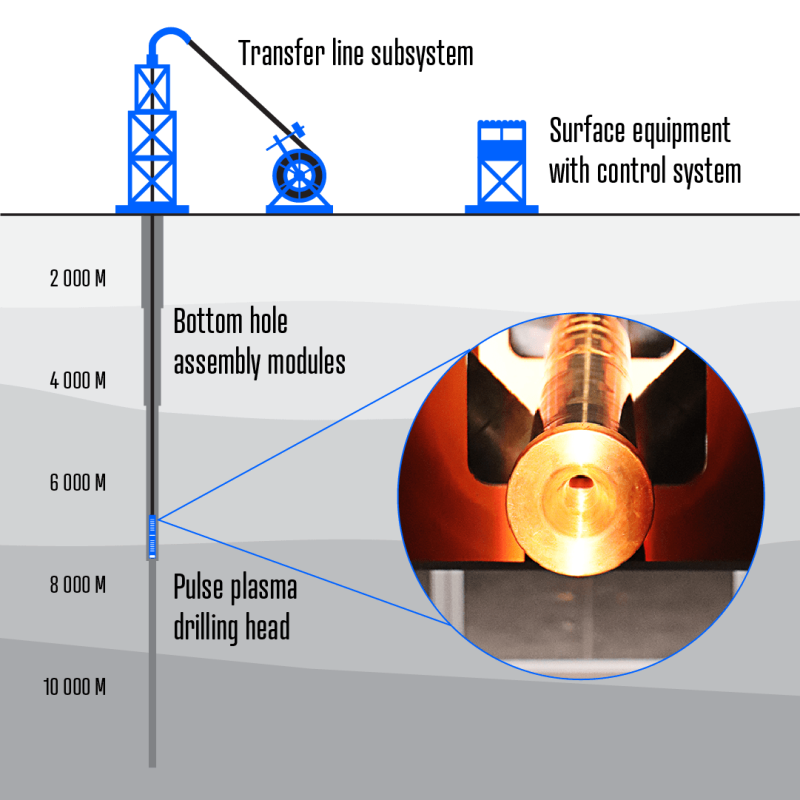
Where the plasma tool is hoped to come into play is when the wellbore reaches the harder crystalline, or basement, rocks (e.g., granite, quartzite, and gneiss).
In a hypothetical illustration of its technology’s potential, GA Drilling compared its estimated performance of the plasmabit to the actual performance of a roller cone bit used to drill one of the world’s deepest geothermal wellbores in Otaniemi, Finland.
That ongoing project is targeting a hot rock layer found more than 20,000 ft below the surface where a roller cone bit averaged about 7.7 ft/hr in one of the deepest sections of a recently drilled wellbore. Under the same conditions, GA Drilling said its base case estimate for the plasmabit was an ROP of more than 23 ft/hr.
By deploying the still-developing bit technology from coiled tubing units, the developer said drillers will benefit from continuous circulation to remove the disintegrated rock fragments from the wellbore.
Coiled tubing deployments will also enable tripping speeds of more than 3,200 ft/hr, which according to GA Drilling is almost threefold the trip times achieved in most conventional drilling operations. Further, GA Drilling estimates that its technology would have required only two or three trips out of the Otaniemi wellbore example compared with the 11 trips recorded using the roller cone bit.
GA Drilling listed in its paper other advantages over conventional drilling systems. This includes that its system requires a lower energy input than rotary-based drilling technology and can be “highly automated, thus reducing drilling personnel requirements.”
Unproven Potential, New Competition From Existing Technology
Though the new investment from Nabors could signal that there is genuine potential for plasma-based geothermal drilling, GA Drilling’s expectations as summarized above have yet to be proven out in the field. The company said last year that it aims to reach that milestone by deepening existing geothermal wellbores in projects scheduled for 2023.
And as promising as the figures shared by GA Drilling may be, the ROP data of conventional drilling equipment cited in its 2021 paper are based on historical averages and may not be reflective of recent developments.
A paper published last month by authors from Texas A&M University, SPE 208798, shares new details about how off-the-shelf technology was recently used to significantly improve ROP in hard-rock drilling.
The highlighted work involved using PDC bits—the fixed cutter bits used commonly in shale development—instead of roller cones, along with a faster drilling method that was first developed by ExxonMobil.
This technology package was used at the US Department of Energy’s FORGE underground laboratory in Utah to achieve an ROP of more than 20 ft/hr, which is near parity with GA Drilling’s estimated figures based on the Finland project.
However, a key difference between the two projects appears to be that the hardness of the granite drilled through in Finland was nearly twice that of the granite at Utah’s FORGE site.
For Further Reading
SPE 207852 Update in Development and Deployment of Advanced Pulsed Plasma Drilling Technology by Matus Gajdos, Igor Kocis, and Tomas Kristofic, GA Drilling.
SPE 208798 Drilling Practices and Workflows for Geothermal Operations by Fred Dupriest and Sam Noynaert, Texas A&M University.