Collapsed tubing occurs when external pressure outside the casing is greater than the pressure inside. There are several circumstances which can lead to a collapse, including high pressure outside the casing during operations such as cement squeeze, pressure testing in the annulus, and when the mud level inside the casing drops due to a loss of circulation.
The well location within the rock formation can also have an impact on the potential for collapsed tubing. Seismic activity can cause significant damage to the casing and tubing so careful well design and strict operating procedures are essential to reduce the risk.
When the issue does occur, it can create a significantly restricted area in the wellbore and often results in failure to gain access below the collapsed area in a wellbore. This, in turn, can cause extensive nonproductive time (NPT) to remediate the issue. Planned drilling or intervention work is halted, and production may be deferred. In the most severe instances when the casing collapses the well is completely abandoned.
While the industry continues to focus on enhancing hydrocarbon recovery from existing wells, these operations must remain economically viable. Therefore, preventing and resolving well integrity and access issues have never been more important.
With advancements in expandable technology, it is now possible to reform the restriction in a tubular, enabling the inner diameter (ID) to be opened. This allows for either reinstatement of production back to surface or access to equipment below, permitting operators to resume operations with minimal NPT.
Coretrax recently deployed its ReForm wellbore repair tool when an international oil company experienced collapsed tubing in a remote well off the coast of Papua New Guinea. The solution uses hydraulic pressure applied at surface to reform collapsed, oval, or restricted tubulars.
Overcoming Traditional Limitations
During drilling and production activity, tubing and casing are exposed to a range of axial loads and temperatures as the operator utilizes various methods to reach, and then extract, hydrocarbons from the well. In drilling activity, mud losses can often be encountered through thief zones which leads to a lower mud level. With the consistent pressure outside the casing, the collapse resistance can be affected, resulting in full collapse in the wellbore.
Swaging is a conventional and widely used method of repairing collapsed tubing. The process involves a series of swages run downhole to gradually open the collapsed area. It can be done with specialized swage packers or with a hydraulic expandable swage. Both methods provide a bond to the existing casing once properly prepped. The technique can take a significant amount of time to open the area due to the number of different swages required. Each time a larger size is needed, the operator must use significant rig time to trip out of hole. While it can have successful outcomes for repairing damaged areas of well casing or screens for example, due to the weight required in the pipe to swage, this procedure is not suitable for shallow or lateral wells.
Milling can also be used to remediate collapsed tubing, however, this is not a preferred option given the limitations and risks it poses. The process creates a significant amount of debris which can require multiple cleanup trips to remove potentially harmful residue. This not only creates a more time-intensive operation, but it can also result in damage to the tubing or casing string architectures, potentially affecting the long-term wellbore integrity.
An Effective Solution to Collapsed Tubing
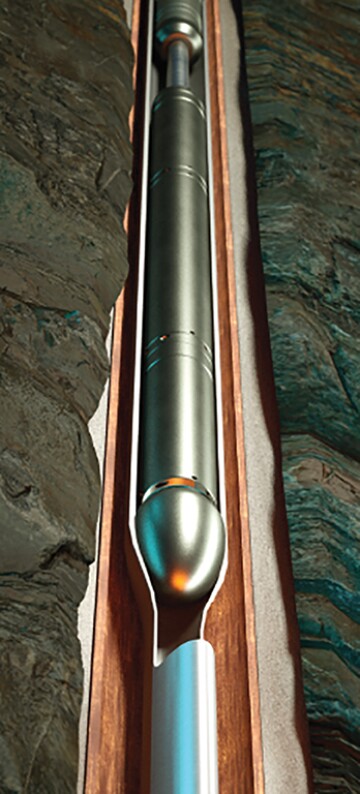
During a project off the coast of Papua New Guinea, an operator experienced collapsed tubing in a remote well due to suspected equipment failure downhole. The issue was preventing the operator from carrying out essential well intervention work as a wireline could not be passed through the wellbore.
The casing had collapsed just 2 m from the surface so swaging operations were not possible, and the operator did not want to risk further equipment damage from milling.
The wellbore repair tool was selected to remediate the issue as it allowed for restoration of the collapsed tubing without jeopardizing current operations.
The nondestructive system is designed for use in vertical or horizontal wellbores, specifically where there is limited setdown weight available for conventional swaging operations, and it can be deployed using coiled tubing or drillpipe.
The system comprises three main components:
- The drive unit which has hydraulic pressure pumped into it.
- The cone which physically expands the tubing to reform the collapsed section.
- An ID anchor which is placed on top to secure the casing.
Downward force is then applied to allow for surface-controlled reformation of the restriction.
To ensure the success of the project, the parameters of the well had to be clearly understood with several elements factored into the deployment.
Planning and Full-Scale Testing
Working closely with the client, the casing’s characteristics were first established to identify the size and grade of steel. Higher casing grades are often more difficult to reform due to their strength, and generally require multiple-sized cones to reduce forces. It was essential that these characteristics were identified early.
As the tool would be passing through an existing well, any remaining equipment within the wellbore, including completion architecture, was identified as a potential challenge. Due to the shallow location of the collapse, any equipment situated around the setting area was also confirmed to allow optimal placement of the anchor section.
Once all information was gathered, Coretrax carried out comprehensive, full-scale testing at its base in Houston. To replicate the client’s collapse as closely as possible, a pipe of the same grade steel was first mechanically crushed to a similar capacity. As the collapse location was in close proximity to the wellhead, a pressure cup was added to the back side of the tool during testing to provide a method to circulate the well in case of a well control issue. The company’s team of experts then tested the first proposed cone size in a controlled environment to ensure that the steel could handle the expansion.
Casing Integrity Maintained
Once final testing was complete, the solution was mobilized to the wellsite. A 3.250-in. cone was deployed first to ensure reduced forces would not exceed the casing limits. Following successful expansion, it was pulled out of hole and a secondary 4.760‑in. cone was deployed to further expand the collapsed intervals of casing, which measured approximately 10 m in length. The tool ensured casing integrity was maintained throughout while providing full drift of the casing ID.
The tubular was successfully expanded within 3 days, allowing the operator to continue with wireline operations. No further intervention was required.
Solutions for Well Integrity Issues
Advancements in technology such as expandables have made it possible for complex well-integrity issues to be addressed more effectively and efficiently. While gaining greater recovery from existing wells remains high on the industry’s agenda, innovations are essential to overcoming traditional limitations that many mechanical solutions present.
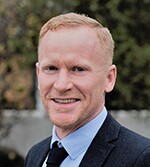
Murray Forbes is vice president of sales and marketing at Coretrax. He has more than 25 years’ experience in well operations, technical support, and product development. Prior to his role at Coretrax, he held several senior positions at Halliburton.