Propping open fractures to maximize production requires placing enough stout particles of sand or ceramic in a fracture to hold it open for years. The downside of bigger and stronger particles is that they are denser than the fluid used to deliver them, so some will settle in transit. It is also difficult to move proppant past the corners in networks of fractures. The end result is only a limited area gets well propped.
There has been a long line of methods offered to deliver more proppant deeper—lighter particles, viscous fluids, and coatings that limit settling. The SPE Hydraulic Fracturing Technology Conference has become a showcase for new ideas.
The most striking innovation presented at the March conference in The Woodlands, Texas, was from Oil Chem Technologies, which reported patenting a chemical combination designed to flow into a reservoir as a liquid, which then turns into strong, spherical balls able to hold open a fracture.
Saudi Aramco has invested in this innovation and is working with the Houston-area company to measure its properties, with a goal of field testing it later this year, said Paul Berger, vice president and technical director for Oil Chem.
“The goal of this technology development is to convert injected fracturing fluid into a highly permeable proppant pack in-situ,” according to the paper he presented at the conference (SPE 173328). “Since the fracturing fluid itself forms the proppant, it can penetrate the fracture length, height, and complex network, maximizing the effective fracture area.”
The fracturing conference also presented:
- Research at Shell to find a strong ceramic shape less likely to settle out of fluid has led to a W-shaped proppant design. Its complex outline causes drag, making it less likely to settle.
- University of Texas research into whether mild acid can be used to create lasting pathways in microfractures too small to prop open. The goals are similar to those for acidizing carbonate formations—etching production pathways by dissolving calcite.
- Fairmont Santrol’s large exhibit featuring its Propel SSP Proppant Transport coating. It was competing on the show floor with Trican’s MVP Frac, a coating which can make proppant buoyant by adsorbing gases such as nitrogen.
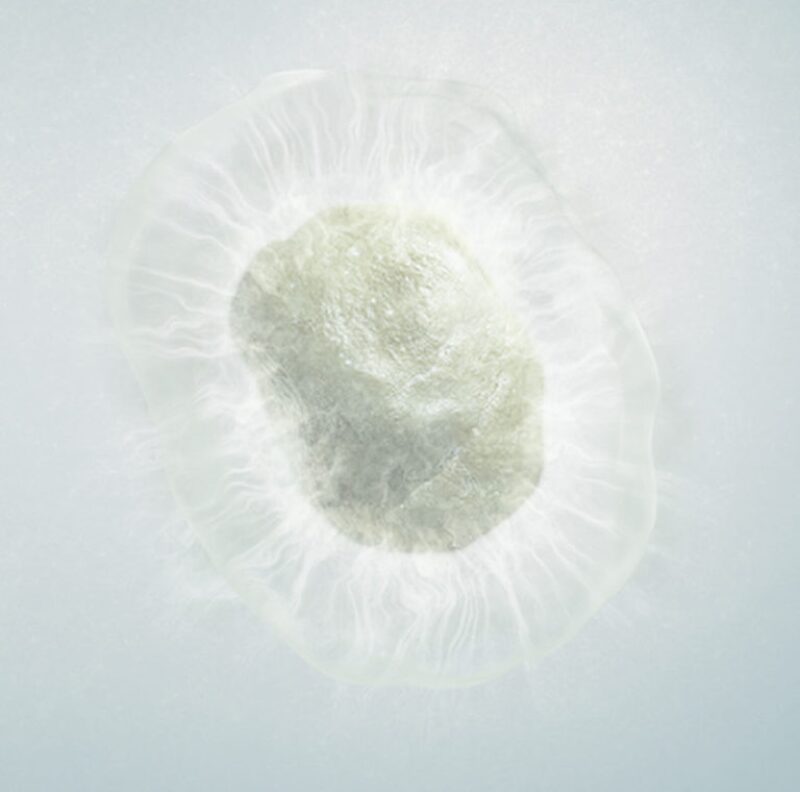
All were selling new ideas at a time when operators were reacting to the oil price crash by sharply reducing the number of wells completed, and relying more on the oldest type of proppant, which is sand.
Fairmount Santrol’s polymer coating is able to reduce settling allowing more proppant to reach fractures. The company has taken an invention that it debuted 2 years ago at the conference, and modified it so it can be practically delivered through its extensive proppant supply network. On a huge screen, the proppant supplier featured four promising field tests.
The company is seeking early adopters to make a case for its polymer coating, which it says can improve production and reduce the cost of pumping jobs. “People are looking for technology,” to improve results, said Brian Goldstein, product director for Propel SSP technology at Fairmount Santrol. “The change in the market changes the way you think.”
Shell reported it has found a way to mass-produce the complex ceramic shape, which “does not settle in a stable manner. It tumbles and flips end over end,” said Yinghu Liu, a production technologist for Shell. But he added that “cost is challenging.”
The University of Texas team was able to observe porosity and permeability gains in lab testing and is seeking partners for field testing, said Mukul Sharma, the petroleum engineering professor supervising the work. One potential drawback is that the acid also weakens the rock—reducing the surface hardness by 30% to 70%—which could mean the openings created would soon be squeezed shut.
Turning a good proppant idea into a commercial success is a challenge. One proppant innovator, Oxane, which used nanotechnology to create proppant it said was strongest pound per pound, recently announced it had shut down its only manufacturing plant and laid off the 70 workers in Van Buren, Arkansas. Oxane has not commented beyond a short announcement warning of layoffs associated with the plant shutdown.
Floating Schedule
Oil Chem’s unnamed liquid proppant is created by mixing two chemicals at the wellsite before pumping. The formulation used will determine how long it will take before the liquid turns into a solid. Berger said this could range from minutes to hours. Varying the timing can be used to manage how deep the proppant is placed in the fracture network.
After a set period of time, the liquid mix turns into smooth, translucent spheres, whose size is based on the space they are in when they harden. The diameter can range from millimeters down to microns.
Aramco is working with Oil Chem as part of a larger effort to find improved fluids and proppant for use in its reservoirs. In the past, the Saudi Arabian national oil company has relied on acidizing to enhance the output of its carbonate formations, rather than using hydraulic pressure and proppant. The paper points out that using acid to etch textures in a rock to enhance production has its limits.
“In carbonate reservoirs the in-situ proppants can effectively overcome the short etching pattern suffered during acid fracturing. … They also eliminate the concern of corrosion caused by a large-volume acid injection,” it said.
Selling this liquid technology to big users of proppant will require changing their view of what proppant is made of, from mineral to a high-tech plastic.
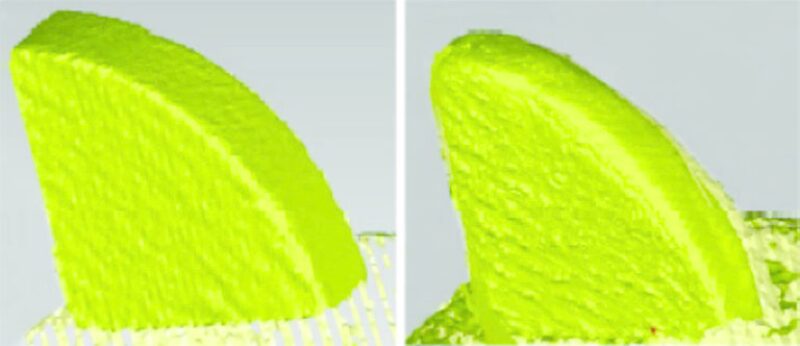
The planned test with Saudi Aramco would use seawater as a solvent, but oil, alcohol, or acids can fill that role. The fluid used becomes part of the proppant, eliminating the need to flow it back before production begins.
Oil Chem has subjected the spheres to pressures of up to 14,000 psi and none of them have shattered at that level of stress, Berger said. When squeezed in a press, the balls deformed and grew stronger, he said. Saudi Aramco will subject the material to further testing, using sophisticated testing devices to determine how it will perform in harsh reservoirs.
Others have tried and failed to create a liquid-to-solid proppant formula. The Oil Chem paper cited a 1968 patent for a “Method of Fracturing and Propping a Subterranean Formation,” which used a liquid that hardened in the formation. That approach relied on “dispersed removable material” to establish production pathways. Strength was reportedly a problem. The paper explained that if only a small amount of material was removed, conductivity was a problem, while removing a lot made it weak.
The Oil Chem material was discovered accidentally. Two years ago Berger was trying to create a material that could be used to plug reservoir passages that allow injected production enhancement chemicals to bypass reservoir rock.
Instead the mix did something that would have never been expected based on its chemical structure, which he described as “a polymer, but not in a way a polymer is normally seen.”
The result was not the plug they were seeking. But company president, Christi Lee, who worked for years on fracturing at Halliburton’s technology development center in Duncan, Oklahoma, quickly saw the potential as a proppant.
Berger said one of her skills is, “When something goes wrong, she finds something right about it.”