In the race to design higher-capacity facilities, separation vessels are becoming increasingly larger in size and weight. As we attempt to extend field life and defer abandonment costs, operating envelopes are becoming increasingly larger in scope. During early field life, vessels are expected to meet peak rates that may, at best, only be in place for several months; the same vessels may also be expected to handle large volumes of solids and water during late life. As a result, design engineers and equipment manufacturers are producing increasingly expensive vessels and associated instrumentation without reviewing the consequences on full life cycle operating conditions. This article aims to highlight unforeseen consequences as well as provide design solutions or operating adjustments based on historical troubleshooting that address the entire field life.
Introduction
Bigger is better, isn’t it? Like many other aspects of life, as an industry we have had a tendency to make separators bigger over time, in part to meet the demands of larger and larger production facilities. The bigger the separator the more oil that can be produced, right? Who doesn’t want more oil? Well yes, bigger separators can handle more oil, but there is a lot more to consider.
The evolution of separator design can be paralleled to the evolution of pickup trucks. These trucks started off as relatively simple and were practical pieces of equipment designed to meet the needs of farmers, etc. (Fig. 1). They were sufficient for the tasks of the day and if they’ve been looked after can still perform the same duties today—moving things from one place to another. Over the years they became bigger and more powerful as new technology was developed. The pickups of the 1970s and 1980s were still basically the same as the early versions and capable of performing the same tasks but in a little more comfort (Fig. 2).
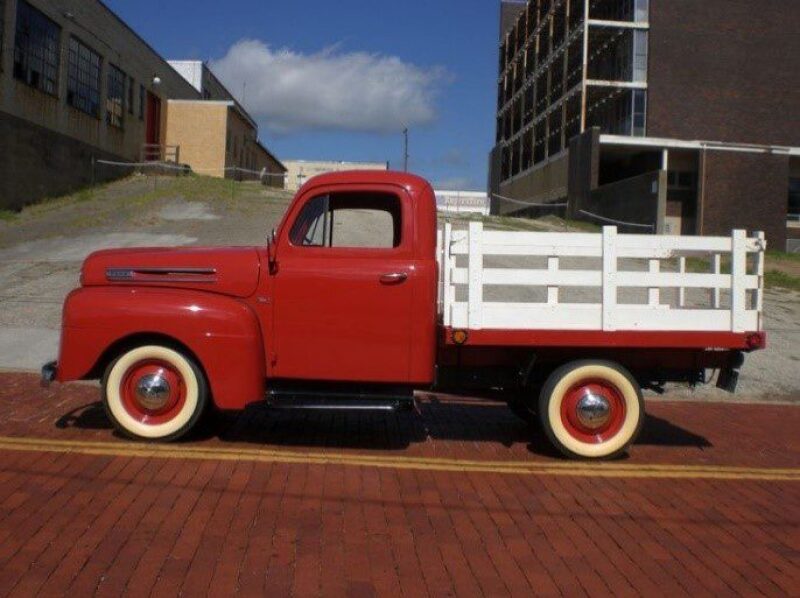
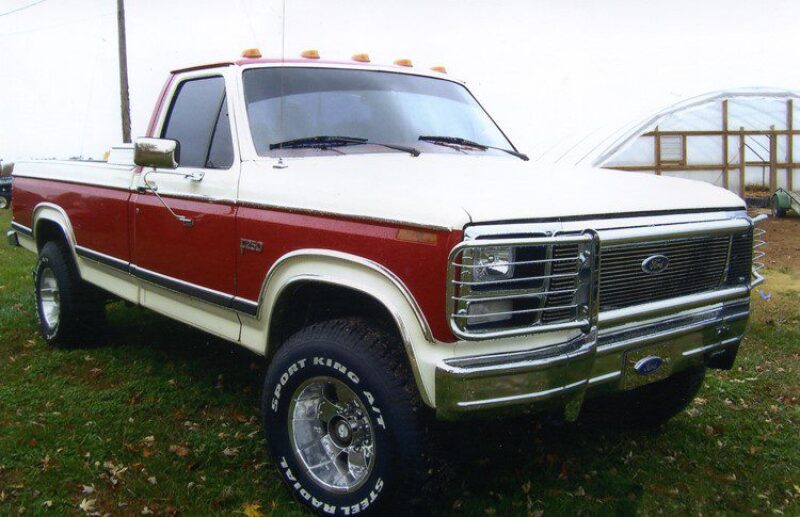
Fast forward to today and it’s clear to see that the pickup truck, just like separators, in many instances have become a whole lot larger (Fig. 3). But, is this new pickup really necessary, and is it any better at performing its most basic task? Well, for many, the answer is no, not really. But we’re a lot more comfortable doing it. And it looks good. And costs a lot more. And there’s quite a bit more that can go wrong, too. So maybe we need to revisit why we’re making separators so big in the first place?
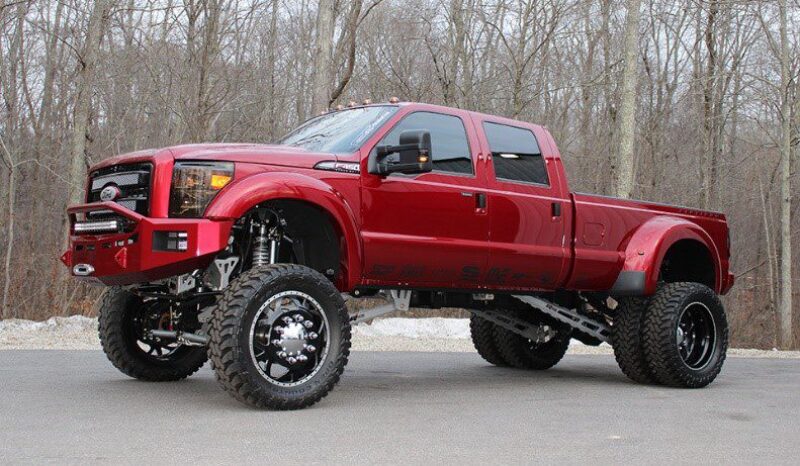
Separation System Design Basis—Designing Out of Hope?
As with most projects, the main driver behind the design basis and production profiles is economics. A larger separation capacity allows for higher peak production early in life. And higher production early reduces the payback time and increases the return on investment. But as we’ve been seeing over the last decade or so, facilities are producing for longer and it’s becoming evident that there is significant value in the production tail, which is normally not a major consideration in the design of a new facility.
All facilities are designed on the basis of an estimated production profile (Fig. 4). The production profile for the field begins with a peak production rate early on in field life. As the field matures, secondary recovery methods may be installed (e.g., subsea boosting, water injection, and additional sidetracked wells) to further maximize production. At one point, however, any further capital into the field is stopped, with the field naturally declining prior to eventual field abandonment. In an offshore environment, this process may take in excess of 20 years to realize.
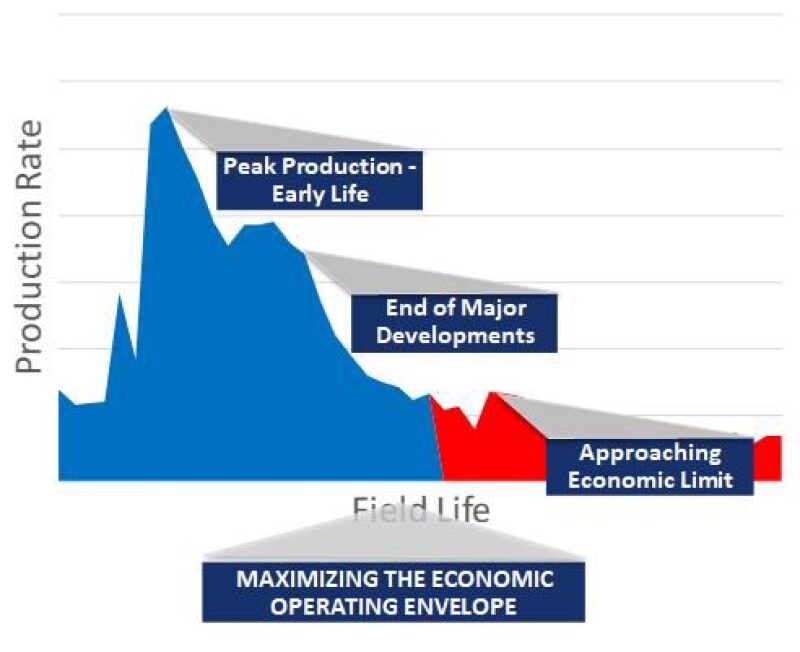
Based on this field life cycle, a single separator is designed to handle all cases through the production history by generating a flow rate profile of fluids throughout field life, an example of which is shown in Fig. 4. From this profile a number of design cases are generated, e.g., max oil, max gas, and max water. In some cases, a peak case is also developed above the max case to be used for sizing. In an ideal scenario, the oil production will reach a maximum rate and continue at that rate for a significant portion of the field life, as shown by the top (projected) lines in Fig. 5.
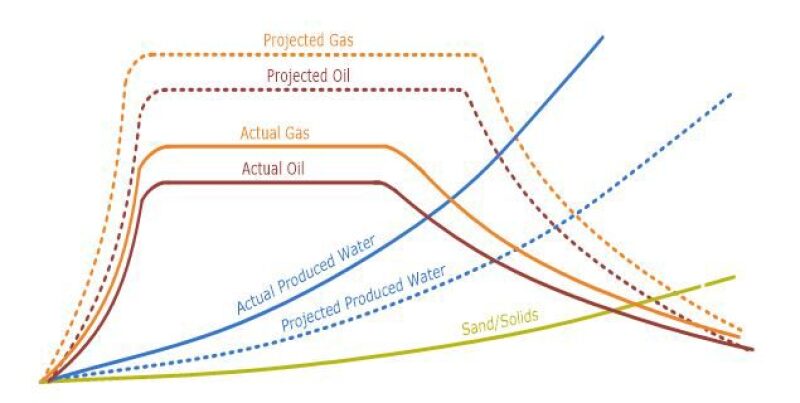
In reality, this period is significantly shorter due to a number of factors such as changes in well performance, flow assurance issues, excessive well drawdown, poor reservoir permeability, and too many others to list. Given the inherent uncertainty and difficulty in predicting production from new reservoirs, along with all the potential problems associated with actually producing the oil, the duration of the peak production period is often much shorter than the early profiles suggest, and the peak height is also typically lower.
The other aspect of production profiles and design cases is the estimated water and solids production. Water production is very difficult to predict and is often underestimated. In other cases the type of waterflood is changed once the field is producing (seawater to produced water or vice versa). The other factor affecting water production rate vs. design rate is that it is common for facilities to operate well beyond the original design life, with water production continuing to increase as the oil production decreases (albeit the fluid rates are still well below the nameplate capacity of the facility).
Data from the US Bureau of Safety and Environmental Enforcement in September 2016 showed that for deepwater US Gulf of Mexico (GOM) the total combined industry utilization is only 24.8% (Deaver 2016). Total oil production was 940,280 BOPD whereas nameplate capacity was 3,790,500 BOPD. While the author recognizes that fields are being discovered farther and farther out such that a 50-mile tieback to a shelf platform isn’t feasible, it also indicates that most fields aren’t producing near their nameplate capacity for anywhere near the intended duration. In many cases the peak production doesn’t actually reach the nameplate capacity, rather like the lower “actual” production curves in Fig. 5. Fig. 6 is from currently producing deepwater facilities in the GOM and shows the high but very short peak, sharp decline and long tail that is considered typical. In this example the facility never reaches the nameplate capacity even for a short duration and further highlights the overcapacity of the system.
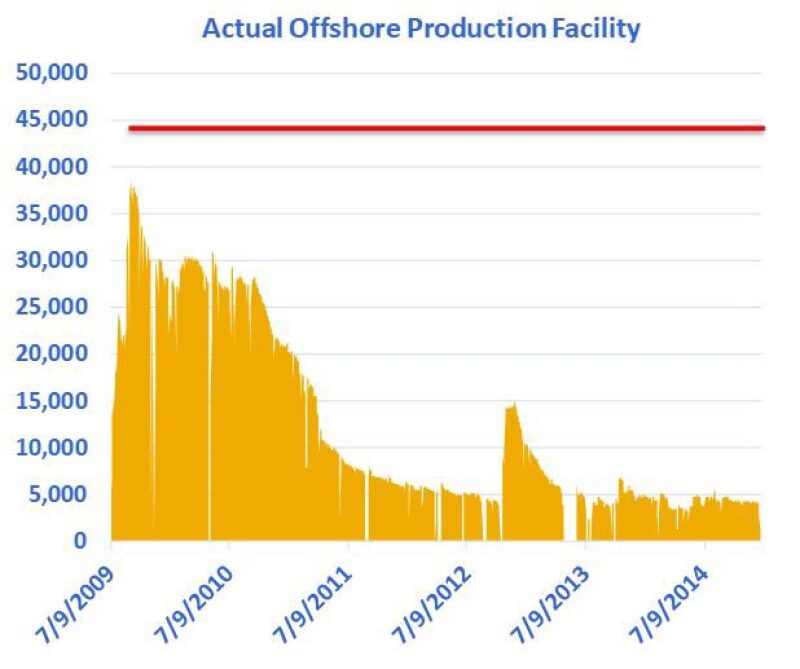
In many instances, the final design also includes an additional design margin (or a surge factor), whether this is added to the overall design case fluid rates or to the sizing of the individual equipment items. Given that for the majority of the field’s life the actual production is much lower than the design capacity, any additional design margin is often unnecessary. All the additional capacity is provided for the very low likelihood that production potential exceeds capacity for an extended duration.
As an industry we are risk averse. We put a lot of time and resources into reducing risk, such as ensuring peak production can be met, and oversizing separators is one of those areas. There’s always a question if the separators can handle the production rate while meeting the export/sales specification. One way to help mitigate that risk is simply to increase the size of the separators. Typically, however, the separators’ size isn’t actually a hard bottleneck as they do not limit the hydraulic capacity of the system. Rates above the nameplate capacity are often achievable albeit with the compromise of reduced separation efficiency. Reasons for not reaching the export specifications are more often related to the fluid characteristics and specific elements within the separators rather than the capacity. It’s worth noting that the actual capacity is not necessarily the same as design capacity; the latter may not be achievable in practice due to poor separator performance (resulting in operating issues that prohibit higher throughputs). Such experiences can fuel tendencies to oversizing vessels on future projects. Making vessels larger, however, does not address the root cause of the issue. It is primarily the quality of the internals design and performance predictions at design time that can make the design capacity achievable in practice and hence avoid the “need” to oversize.
There are other aspects to consider in the design of a separation system such as the number of trains and separation stages that will affect facility and equipment size. The decision whether to design for a single train or two separation trains will depend on the overall production rates and whether flexibility (due to producing from different reservoirs) is required (Fig. 7). Having two smaller trains is more likely to avoid issues with oversizing of individual vessels but may result in larger space requirement; facility weight can actually be reduced with multiple trains depending on design pressure and capacity and so should be considered early in concept design. However, while the separation system itself may be split into separate trains, this needs to fit with the overall sparing philosophy of the facility, including downstream equipment. If other downstream and utility systems aren’t spared effectively (or are not dedicated to a single train), this needs to be understood such that there isn’t a perceived sparing ability of the separation system itself.
Fig. 7—Number of separation trains by geography (SPE 90325).
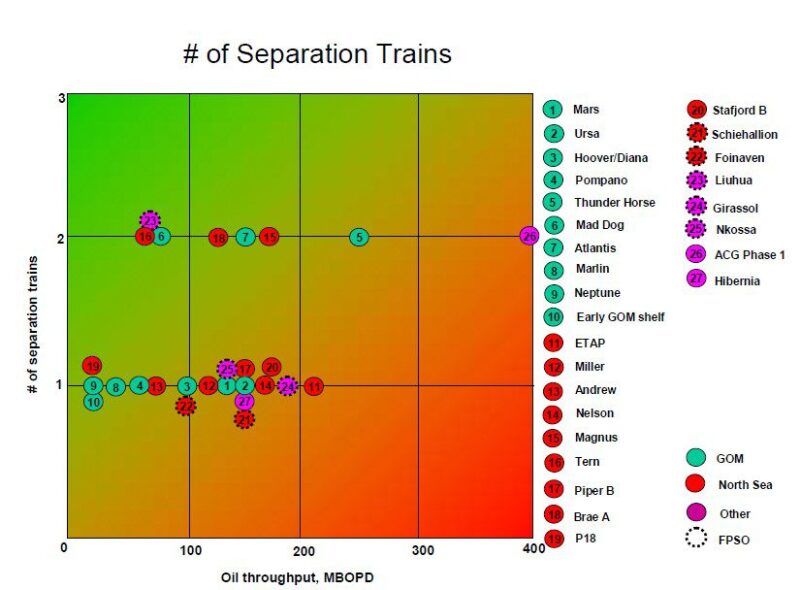
The number of stages in a separation system is aimed to simultaneously obtain the maximum recovery of liquid hydrocarbons while maximizing its stabilization (Fig. 8). The decision on number of stages is affected by reservoir pressures (and subsequent compression optimization), relative cumulative recoverable volumes of oil and gas, and downstream pressure requirements (e.g., vapor pressure requirements of the export pipelines). Generally speaking, the use of a high-and medium-pressure separator plus a stock tank operating near atmospheric pressure (effectively creating three separate separation stages) provide the most economical solution. For this particular arrangement, the selection of the medium-pressure separator is the most important factor as shown in Fig. 9.
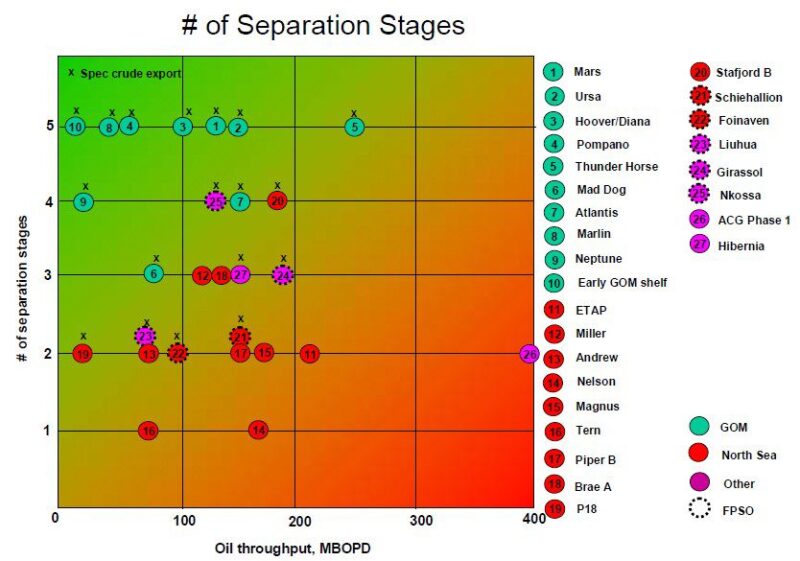
Since the increase in liquid yield is not linear to the addition of more stages, four to six stages are generally seen when producing at very high pressures. The overdesign of each stage leads to significantly higher facility weight and costs. Early understanding of likely separation performance (by undertaking appropriate laboratory testing) may help in providing tighter specification for gas, oil, and water quality from each stage and therefore reduce the capacity from each stage.
Fig. 9—Middle-pressure separator pressure selection (Penn State University: Design and Optimization of Separators).
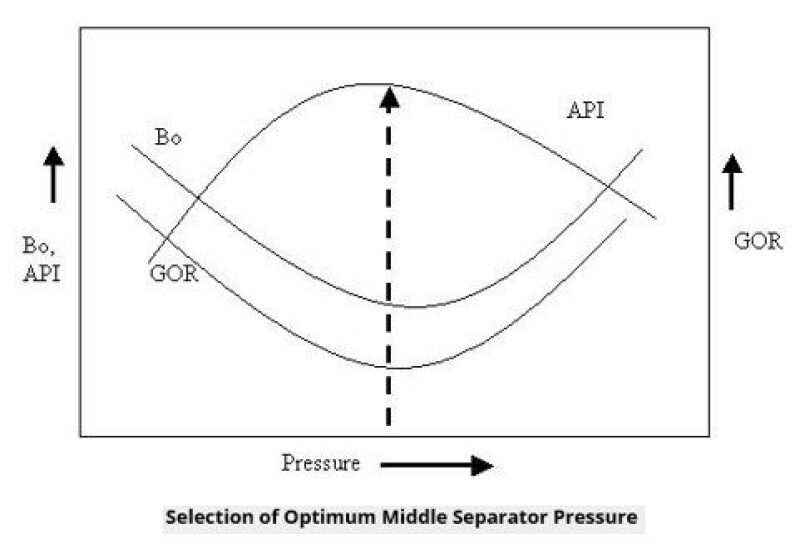
As fields are discovered in deeper water using improved technology, the complexity of the project and facility has increased (Fig. 10). Flow assurance problems may require gas lift and subsea boosting, which changes fluid composition and may result in stable emulsions that become difficult to separate. Additional subsea chemicals are now being injected in greater volumes due to increased flow assurance issues (e.g., paraffin inhibitors and solids dispersants) that will eventually impact topsides separation equipment.
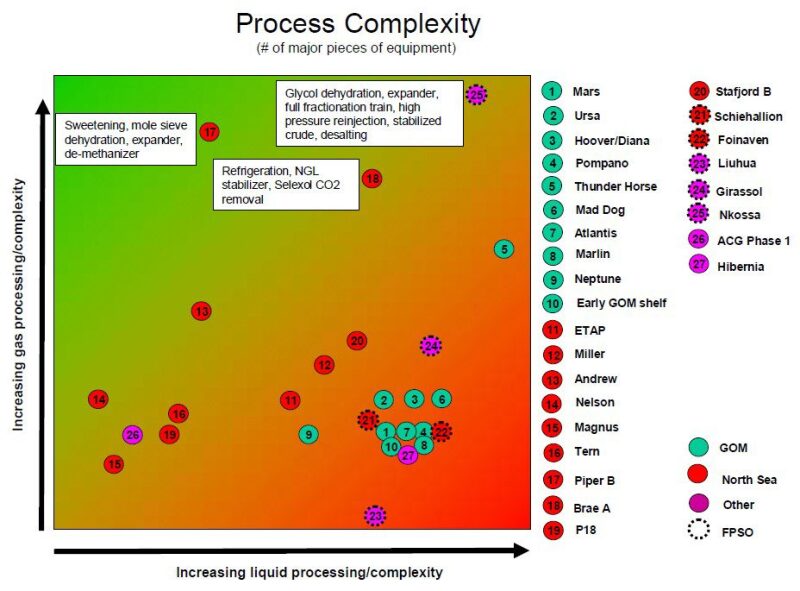
As the facility grows in size so too does the cost and complexity and therefore the project length. Each of the items listed above has a significant cost associated which can be quite considerable and lead to a much higher Capex.
Data collected from recent megaprojects ($5 billion and greater) around the world show that the majority (60%) result in some sort of cost overrun. In addition, these overruns are not as a compromise for increased schedules; nearly three-fourths of projects (73%) result is some sort of delayed schedule. Clearly as an industry there are problems delivering big projects, and looking at opportunities to reduce size should be investigated.
Engineering and Construction Considerations
Increasing vessel diameter has a big impact on weight. A 20% increase in inside diameter (ID) equates to approximately 40% increase in weight and a 40% increase in ID equates to approximately 90% increase in weight (Table 1). With this in mind, multiple trains can actually provide more capacity for the same weight, hence further engineering is required early on.
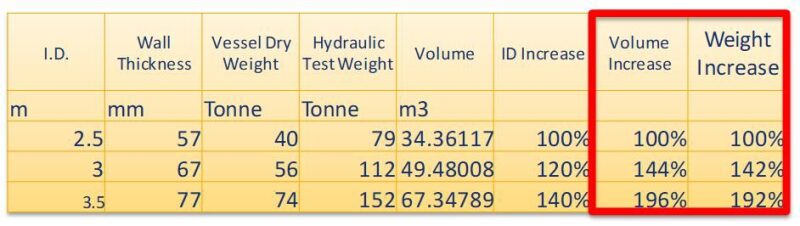
Moreover, the larger liquid volume can lead to more significant sloshing problems on motion-sensitive platforms (e.g., tension-leg platform) that will require more internals to mitigate.
Other Separation System Considerations
There are numerous parts to the design of a separation system that must be considered to ensure efficient separation and they must be considered holistically. Inlet pipe size and configuration, inlet devices, internals selection, and the placement of level instrumentation are all critical in ensuring effective separation efficiency throughout field life. It is worth emphasizing, however, the need for ensuring solids/sand management is handled adequately in late life.
The need for solids removal within a vessel will depend on the expected sand production rate (and water production) along with the characteristics of the oil. In many instances fouling of separators is the main cause of poor separation performance as it reduces the residence time and can cause remixing of the oil and water. It also reduces the available vessel capacity if not removed. If the solids loading is high then no matter how much additional capacity was allowed for in the initial design it will be filled with the solids and provide no benefit.
Note that increasing the diameter/capacity of a separator requires more banks for jets/desanders, etc. and may result in poor coverage/removal. Larger systems should also be automated to ensure regular use and avoid creating blockages within the sand removal system, which is common in systems that are commissioned but not used or not used regularly.
Where solids loading is expected to be low, a larger vessel means more sand/solids can be collected before impacting on separation performance and can be removed during maintenance periods.
Moving To Fit-for-Purpose Design
Understanding Fluid Properties
Key to optimizing oil/water separation is understanding the properties of the fluids, namely densities, viscosities, surface/interfacial tension and emulsion viscosity/tendency. Having reliable data for these properties over the range of temperatures that the process is to operate at will give engineers the best basis to avoid oversizing the separator, which is often done to compensate for unknowns in separation behavior.
One example is in the sizing of a new separator for gas/condensate/water separation. Separating condensate and water can be difficult despite the larger density difference due to the low interface tension of the condensate droplets, which causes them to break easily and impede coalescence. These properties also make water treatment difficult and places more emphasis in achieving good primary separation to lessen the reliance on the water treatment system. In the case presented in Table 2 the condensate surface tension was not well known but expected to be low based on analogues.
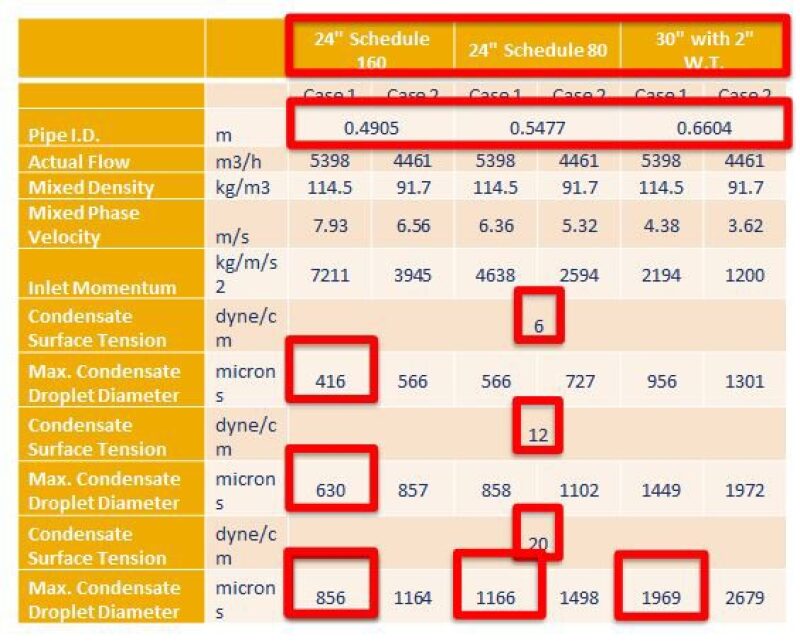
A range of surface tensions was used to calculate the expected droplet distribution entering the vessel, which is then used to size the vessel based on gravity separation and required separation efficiency. It can be seen that the surface tension has an enormous effect on droplet size which governs the settling time and therefore required separator size. In this case the minimum surface tension resulted in a vessel nearly twice the size of the maximum. And as we tend to design for the worst case, this was used as the sizing case.
Separator Sizing Case Definition
Typically separators are sized based on 2–4 cases, such as max gas, max oil, max water, and max liquids. Often these cases are overly simplified and do not accurately reflect what the separator will need to process. Further definition of the phase flows during the life of the facility will allow improved understanding of how the operating levels will change through the production life. This in turn will improve the design of the internals such as weir height and its required adjustment, level setpoints, and level instrument ranges.
Apply
appropriate
design margins only if absolutely necessary
In many instances the production profiles used as the design bases already include a margin and/or is optimistic in terms of likely production. Coupled with the fact that for the vast majority of a separator’s life the production rate is well below nameplate, adding additional margin is unnecessary. Only in instances where the separation characteristics are not well understood should additional margin be added.
Prioritize separator components individually
Each of the components that contribute to the separator size and performance should be considered and optimized individually and as a combined system. All aspects of a separator can enhance or detract from its performance and affect the reliability.
An example is the inlet pipework, which is often not prioritized and engineered last and without detailed consideration. Both the size and the configuration is important by way of determining droplet size distribution as well as the distribution of the phases entering the vessel. Hence they both have a significant impact on the performance of the individual internals within the vessel and the overall separation efficiency.
Understand the impact of the max design case and larger vessels
Given the effect that oversizing of separators, as well as the overall design case, has on increasing the size of the entire facility, it is important that the reservoir team as well as the process engineering team understands how big an impact increasing the design cases will have. Resources should be spent early in concept design determining the impact of increases and decreases in the max cases on Capex, Opex, and project schedule.
Replacement of internals for late life
In most cases the selection and design of the internals is based on the high-gas/-oil cases and little consideration is given to the production tail. Based on our experience more focus should be placed on flexibility and retrofitting internals to help ensure the vessel is capable of achieving the necessary separation performance later on when water cuts increase and separation becomes more difficult. Retrofitting a vessel is often seen as an inconvenience and expense that is best avoided, but if more emphasis is placed during the design phase on easily enabling changing/removing internals then it will be cheaper, easier, and more likely to be done.
Investigate use of compact and in-line technologies
There are a number of different in-line technologies that provide initial bulk separation, thereby reducing the total flow and required separator capacity.
Debottlenecking
It is rarely the size of the separator that constrains production or limits efficiency, but typically other components (heater/cooler, produced water treatment, etc.) or the internals within the separator. It is much easier to design turndown on heat exchanger equipment than it is for a separator. If separators are the issue, address the internals first before throwing everything at the size itself. Debottlenecking is an effective use of resources and allows targeted improvement of the process once its operation and the fluids are better understood, rather than increasing the size of the system early on.
Summary
While few engineers are penalized for overdesigning, the fear of equipment undersizing results in margins being added on top of margins. Oversizing ensures that the separator design meets the entire life cycle requirements of the facility, but we need to ask ourselves if we are setting ourselves up for failure in the long run. The weighted focus appears to be on the peak rate, which is further exacerbated given that it typically arrives early-on in field life. With peak rates typically being short-lived at best, or at worse, well beyond actual production rates, more weight needs to be given to the tail-end of production. Rather than kick-the-can and create a make-work project for another engineering/operations team in 10 years, teams should look at the total cost of ownership when it comes to late-life modifications required for lower flow rates and higher solids loading. The oversizing of vessels has a knock-on effect far beyond the additional cost/space/weight of the vessel itself. With the move toward subsea tiebacks using a hub-and-spoke approach, facilities need move toward fit-for-purpose designs to be able to accommodate new tie-ins at lower commodity prices. Finally, increasing vessel size as a means of achieving oil/water specifications neglects a multitude of other factors that needs to be addressed as part of effective fluid separation.
References
SPE 90325. Bothamley, M. 2004. Offshore Processing Options for Oil Platforms.
Deaver J.R. 2016. A History of Too Much Capacity and Too Much Complexity in the Deep Water Gulf of Mexico. Joint AIChE/SPE Workshop: Next Generation Deepwater Facilities.
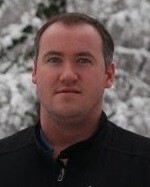
Graeme Smith is a process engineering consultant who has spent over 10 years working on a range of global upstream projects including concept development for new offshore facilities, troubleshooting, and optimization of oil/water separation processes and equipment through to design reviews and provision of operator training. He holds a bachelor’s degree in chemical engineering from Monash University, Australia.

Bryan Arciero is responsible for flow assurance, production chemistry and process engineering for Murphy’s Gulf of Mexico assets. He holds a bachelor’s degree in chemical engineering from McGill University, Canada, and is an MBA candidate at Rice University. He is a registered professional engineer in Texas, Newfoundland, and the UK (IChemE).