In an era where capital markets are hitting the brakes on funding the US shale sector, operators have increasingly pivoted from production growth to maximizing the rates of return via lower-cost wells. One of the major challenges of this new era is the determination of optimal stage and well spacing for a drilling area. For much of the US, the trend has been toward increased job size and rapid downspacing of infill or “child” wells. The unintended consequence of this trend has been an increase in fracture interference and excessive cross-well communication, which results in an overcapitalization of acreage and underperforming child wells as the drainage areas of wells overlap and compete for depleted resources. Within the SCOOP/STACK play, child wells completed in 2017/2018 have been half as productive as their 2015/2016 parent wells, a trend theorized to be directly related to negative fracture interactions.
Determining an optimal spacing be-tween parent and infill wells is not a straightforward endeavor. An ideal development strategy is not just about well spacing, as decisions in completion design can exacerbate issues stemming from tight spacing. For this multivariate problem, operators have attempted to use bottomhole pressure measurements to extrapolate fracture interference or to use large data sets in a “trial-and-error” approach to understand well interference behavior. These approaches have significant downsides, relying either on data sets of questionable value or on extrapolating data to and from wells with significantly different geological conditions.
One operator in the SCOOP/STACK has attempted to understand well interference with chemical tracer technology. Using liquid molecular tracers, this operator achieved a quantified understanding of flow between parent/child wells with a high degree of confidence. This inexpensive technology has allowed the operator to experiment with well spacing and repressurization of parent wells. This, in turn, permits the rapid evaluation of mitigation techniques to optimize its field development strategy based on an accurate measurement of interwell fluid movement.
Tracer Selection
Two categories of chemical tracer are commonly used in conjunction with hydraulic fracturing operations: infused solid particulate tracers and liquid molecular tracers. While both tracer products have their strengths and weaknesses, liquid molecular tracers were chosen as a best practice in this study as they allow for quantification of the traced fluid phase, unlike infused solid particulate tracers.
To understand the basis of this decision, it is necessary to understand how these tracer products are used and behave within the reservoir. At the core of both products is a chemical tracer that is preferentially soluble within an oil, water, or gas phase. For solid particulate tracers, a carrier material is used that has a high adsorption potential for the chemical tracer and can be pumped in a fracturing fluid alongside traditional proppant; common particulate carriers include zeolite and activated charcoal/activated carbon beads. These sorts of solid particulate tracers are usually marketed as a means of marking the oil phase, often under a variety of names such as DIY tracers or oil-soluble particulate tracers. Inexpensive and exceptionally easy to use, these infused carrier particles are added to the blender during normal fracture operations to be distributed within the packed proppant pack. When they contact their targeted fluid phase, some quantity of tracer leaches from the particulate material into the fluid phase. Samples of produced fluid are collected at the surface at specified intervals and are analyzed for the presence of the tracers. If detected, the traced phase is said to be produced from the stage where a unique tracer particle has been placed.
While an effective method of establishing a binary yes/no as to whether fluid flow moves through a given fracture, infused solid particulate tracers cannot consistently quantify the flow through that fracture, as there is no consistency to the rate of tracer release. Consider an activated charcoal particle infused with an oil-soluble tracer—the rate of tracer release is a function of tracer chemistry, temperature, and the particulate surface area exposed to the oil phase. Activated charcoal is significantly weaker than commercial proppant and will inevitably experience some degree of crush during the pumping process and in-situ within the proppant pack. The degree of crush cannot be predicted, and the exposed surface area is effectively unknown within the fracture. In a worst-case scenario, the carrier material may be ground into such extreme fines that it is flushed back into the wellbore during flowback. Even if the particulate carrier remains within the proppant pack, it is uncertain whether the tracer will come into contact with the oil phase. Most commercial applications of infused solid particulate tracers use a very small amount of solid material per stage to minimize cost.
Within the Meramec formation of the SCOOP/STACK, a stage might reasonably contain 380,000 lbs of proppant. For such a stage, the solid particulate tracer comprises only 0.002% of the proppant pack by weight. As a result, the oil phase may bypass the minimal amount of tracer within the proppant pack via phase slippage, nearby proppant pack damage, emulsification, or a number of other common in-situ phenomena. With no consistency in the ratio of tracer to oil flow in the fracture, quantification of oil flow becomes impossible.
The application of liquid molecular tracers provides quantitative results. A liquid oil tracer acts as a hydrophobic material, dispersing itself evenly on the outer boundary of the fracturing fluid as a water-continuous emulsion. As that fracturing fluid breaks apart the reservoir rock and comes in contact with hydrocarbon, the liquid oil tracer is transferred to the hydrocarbon as its partitioning coefficient strongly favors solubility in the oil phase over remaining in the water phase. Now attached to oil, the liquid tracer begins to diffuse through the oil phase, tagging the oil in the fracture drainage area.
One recent criticism of liquid molecular tracers is that the tracer can be flushed back into the well during flowback, unlike solid particulates which are physically trapped within the proppant pack. However, this criticism is rooted in either a misunderstanding of the mechanism of action for liquid tracers or misleading marketing materials. Bench testing can demonstrate how liquid tracers may be flushed out of a fracture, but only if the fracturing fluid never encounters organic materials. This is expected, as a property of a properly chosen liquid oil tracer is its ability to be transported by the aqueous fracturing fluid regardless of its flow into or out of a fracture. Should any hydrocarbon be encountered, the liquid oil tracer will solvate into the hydrocarbon phase, eliminating flowback in the water phase.
To demonstrate the difference in the movement of oil tracers through a water- or hydrocarbon-coated sand bed, tests passing water and tracers through sand-packed columns were set up. Four columns were packed with sand, each column was saturated with either nothing (dry), water, a synthetic oil-and-water mix, or synthetic oil. Identical amounts of liquid oil tracer were added to the top of each column and water was eluted through the columns. The first 20 ml eluted from the column were collected in four 5-ml samples (samples 1–4), which were analyzed by GC-MS with detection limits at parts per billion (ppb) concentrations (Fig. 1). When the columns contained no hydrocarbon, tracer was detected in the first 5 ml aqueous sample collected. No tracer was detected in the subsequent samples. When the columns contained hydrocarbon, no tracer was detected in any of the aqueous samples. This outcome is consistent with field experience where many studies have been carried out to verify liquid oil tracer behavior. During these studies, water samples were taken when only water was flowing back to the surface prior to oil flow. Samples were subjected to solvent extraction to remove any oil tracers, and the solvent was tested for their presence. To date, there is no documented evidence of liquid oil tracer presence in the flowback water.
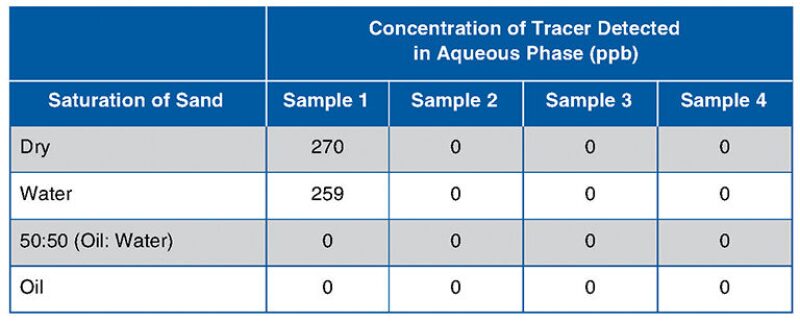
Tracer Investigations Into Parent/Child Communication
The Anadarko Basin has proven to be the most active and prolific within the state of Oklahoma, consisting of several unique plays such as the Marmaton, Mississippi Lime, Cleveland, and Granite Wash. While the majority of plays have been abandoned due to falling economic viability, the SCOOP/STACK is still the second busiest play in the lower 48 states after the Permian Basin. Operating within the SCOOP/STACK can be difficult, however, due to the high heterogeneity of reservoir characteristics. Hydrocarbon windows in the western parts of the play are often deeper with higher gas content, while acreage to the east generally exhibits increased oil percentage. Over the years, operators have explored different drilling targets to achieve the most profitable wells. Early development focused on the SCOOP, targeting the siliceous shales of the Devonian Woodford, with later wells expanding into the STACK and the Mississippian-age Meramec and Osage layers. These are reasonably thick layers, with the Meramec thickness ranging from 30–400 ft and the Woodford ranging from 50–1,000 ft. As a result, well spacing becomes a three-dimensional problem often with multiple horizontal laterals required to be “stacked” in the vertical direction to drain a single location.
This tracer study used liquid as opposed to solid particulate tracers to quantify hydraulic communication on two pads drilled with a similar stacked configuration; two child wells were landed in the lower Osage layer beneath an existing parent well within the Meramec. Due to previous work with Tracerco, the operator had established a trend of heavy upward communication from child/infill wells to established parent wells in an upper target and wanted to evaluate parent prefill to prevent these parent-child interactions.
Baseline Pad: Well Space as the Sole Mitigation Strategy
In pad one, the parent well in the Meramec layer had been on production for 2 years and so significant pressure depletion was expected. The consequence of this depletion is a shift in stress gradients within the drainage area of the parent well, with higher stresses near the boundaries of the drainage area and lower stresses around the fractured surfaces. When fractures are initiated from an infill well close to this drainage envelope, the fracture has a preferential desire to extend toward the depleted zone and area of reduced closure stress in that section, resulting in fracture interference. To determine if well spacing alone could overcome this behavior, a large lateral well spacing was used between child wells and parent.
Fig. 2 illustrates the lateral distribution; Child Well 1 was landed 360 ft below the existing parents and offset 1,750 ft laterally, while Child Well 2 was 360 ft below the existing parent and offset an additional 1,780 ft laterally. Total horizontal distance was 3,530 ft from the parent well.
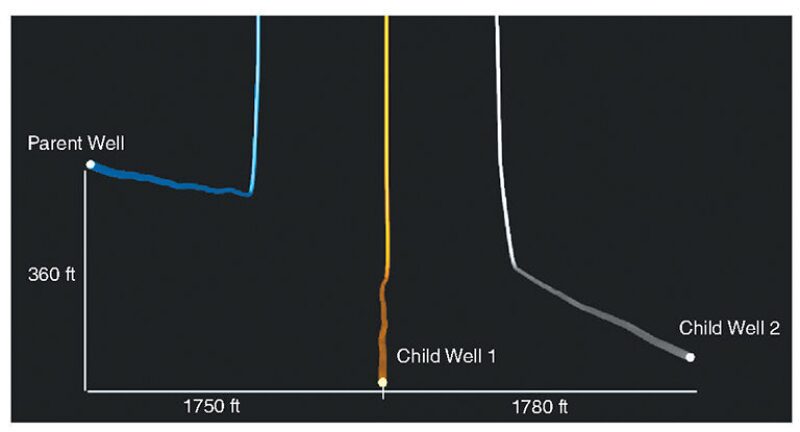
For both infill wells, a liquid chemical oil and water tracer was placed in each of the 28 stimulated stages of a given well. Over the initial 60 days of production, the tracer response revealed a very clear trends: While the large well spacing had resulted in lower communication than normally observed, the communication was predominantly between the child wells and the parent rather than between child wells, with water proving the more mobile phase. Demonstrative of this, over 17% of the water tracers injected into Child Well 1 during stimulation were ultimately produced from the parent well. Tracer data suggested that those tracers injected into the toe half of the well were most likely to migrate to the parent well; the rate of communication increased over the sampling period as the drainage area around the parent well was further depleted. Child-to-child communication was not avoided, with some migration of tracer from stages 17 and 18 of Child Well 1 and from the toe of Child Well 2, but this communication was minimal.
Experimental Pad: Pressurization of the Parent Well
Even with significant well spacing, communication between parent and child wells proved unavoidable. As mitigation, the depleted parent well was infilled with 30,000 bbl of fluid prior to well shut-in and infill stimulation. By prefilling the parent well and increasing pressure in the local pore space around the parent, the stress field would ideally be shifted so that propagating fractures would not find an upward trend toward the parent well to be the preferential pathway.
Like the baseline pad, the experimental pad had two infill wells landed 355 ft below the parent well in the lower Osage formation. As in the baseline pad scenario, the parent well was within the Meramec formation with the nearest child well laterally spaced 1,720 ft away. The second child well was stepped out an additional 1,310 ft laterally for a total distance of 3,030 ft in the horizontal direction. The three-well layout is shown in Fig. 3. Besides prefilling the parent, one additional variable change existed in the experimental pad: The child wells were drilled in the opposite direction of the parent well, alternating in a north-south direction.
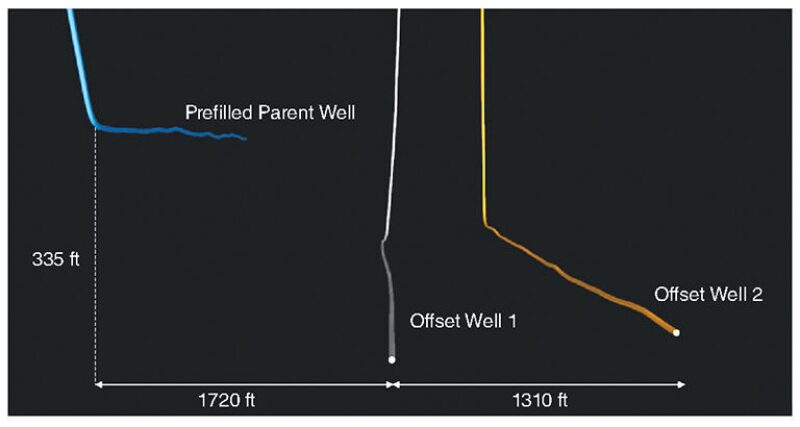
Within 30 days, tracer data clearly showed a distinctly different outcome. Though child-child interaction remained largely the same, parent-child communication dropped more than 51%.
Conclusion
Using liquid molecular chemical tracers, an operator in the SCOOP/STACK play was able to rapidly quantify the effect of different fracture communication mitigation strategies. With minimal cost, low risk, and without the need for a large data set or multiple trial-and-error efforts, the drilling and completion strategy was rapidly adapted with immediate improvements in estimated ultimate recovery and net profitability. The investment was repaid in the next incremental pad. The results of this tracer study justified additional tracer investigations into the effects of existing fault communications, alternate completion designs, and studies in other producing layers.