After years of enhanced oil recovery (EOR) tests in the Bakken, one method finally appears to have added to a well’s ultimate production.
The Liberty Resources well “is perhaps the first one that had clear, indisputable evidence of incremental oil. I do firmly believe we are on the right track for cracking the code for Bakken EOR,” said Jim Sorensen, director of subsurface R&D for the University of North Dakota Energy and Environmental Research Center (EERC) which provided technical support and funding.
The gain predicted after the treatment with water alternating with gas injection (WAG) is not huge. A paper on the test, which was limited to a single 30-day injection cycle, estimated it added 7,000 bbl to the ultimate production, based on decline curve analysis (URTeC 3722974). An updated analysis from EERC is expected in early 2023.
While there are endless arguments over the accuracy of decline curve analysis, Gordon Pospisil, development advisor for Liberty, said incremental oil estimates look solid: “The oil rate response to water alternating gas injection was clearly measurable at over 7,000 bbls over the baseline trend.”
The bigger news may be an injection method that can overcome two barriers to EOR in the Bakken and elsewhere. One is finding a way to keep the injected gas around the wellbore, and the other is significantly lowering the cost, primarily by slashing the volume of gas required.
“Overall, we were pleased with the project outcome to date as we were able to build pressure, contain the injection within the DSU (drilling spacing unit), and make incremental oil,” Pospisil said.
For the test, Liberty used a novel, computer-controlled injection system from a startup company, EOR ETC. This system can rapidly switch from gas to water injection based on the control system the company developed. This reduces the surface injection pressure required to significantly increase the downhole pressure level and helps contain the gas in the target zone.
“I have never seen anything like that. It performed as advertised,” Sorensen said.
The estimated long-term gain looks small compared to the 800,000 bbl of oil prior to the test. But Brian Schwanitz, president of EOR ETC, said the income from those barrels covered what they billed for pumping the job, which was a discounted rate reflecting Liberty’s willingness to be the first operator to use the device.
What it accomplished stands out compared to the futility of past Bakken tests where far more gas was injected with little impact on the downhole pressure because so much of it leaked off through the fractured formation.
The Bakken Debacle
For a decade, companies in the Bakken, often in partnership with the EERC, have searched for ways to get more oil out of the play where the ultimate recoveries are usually below 10% of the oil in place, which is in line with other unconventional oil plays.
Gas-injection EOR tests in oil-producing shale plays have been hit or miss, with most of the results in the Bakken in the miss column. The problem has been that much of the gas escapes from the target zone, making it impossible in some cases to achieve the pressure levels needed for effective EOR and it increases the volume of gas needed to uneconomic levels for gas-only projects to achieve improved ultimate recoveries.
Past gas-injection EOR testing was driven a few years ago by reports by EOG of production gains in the Eagle Ford using gas injection.
Significant production gains reported in a few investor slides set off an industry stampede to replicate the results reported by a company known for its technical savvy and its reluctance to share what it has learned.
In the Bakken, even EOG struck out. The recent Liberty paper noted that in 2008, when EOG injected 30 MMcf of CO2 over 11 days, the gas broke through into a well one mile away, leading to an early end to the test.
The EOG trial was in Mountrail County, the same location as the Liberty test on a five-well pad chosen because the geology favored containment. Past EOR tests in the Bakken suggest that locations that are totally isolated are a rarity in that highly fractured play.
A factor that may have affected the results is that the Liberty wells were fractured later than EOG wells. “The Liberty wells were completed with more stages, plug-and-perf cemented liners, and other frac design improvements to improve production and injection conformance along the wellbore lateral,” Pospisil said.
Even if better site selection could limit gas leakage, the volume of gas needed for gas-only injection has been a deal killer due to the cost, which makes drilling and completing new wells a more-attractive investment.
“The only time they [EOG] published the cost, it was averaging $13 million per pilot,” Schwanitz said.
In comparison, the paper cited the cost of the recent testing using water and far less gas at around $1 million.
A Faster WAG
Pitching a method that injects water and gas is going to raise the question: Why would you want to add water to the reservoir?
Skeptics will point to the risk of adding water to formations with a high clay content which may lead to swelling, which could close off fractures, said Todd Hoffman, a petroleum engineering professor at Montana Tech and a 2019–2020 SPE Distinguished Lecturer who spoke about unconventional EOR.
After pointing out the risks of adding water to a clay-rich shale reservoir—a better description of the Eagle Ford than the Bakken—he pointed out that the concerns do not deter operators from pumping millions of gallons of water during fracturing.
And it is not as if there’s no water in the Bakken. Liberty’s Bakken test well has produced 2.5 times as much water as oil over the years.
One reason Liberty was comfortable with a WAG approach was that key people on its management and engineering teams, including Liberty’s President and CEO, C. Mark Pearson, and Pospisil, have done it while working on Alaska’s North Slope. Operators unable to move their gas to market used the stranded gas to maximize the output from conventional fields.
The gas displaces oil from the rock while the water increases the downhole pressure to the level needed to increase the efficiency of the water sweep from the injection well to a producing one.
Different methods are required in the Bakken and other shale plays where the ultratight rock limits inter-well flows. The method that has worked, sometimes, in these formations has been huff ’n’ puff, where an injection period is used to pressure up the well which is followed by the production period—and that cycle is repeated.
EOR ETC’s approach changes the rhythm of WAG injection. It rapidly switches back and forth from water to gas at intervals as short as minutes or even seconds. In comparison, traditional systems may go without a switch for days or weeks.
The computer-controlled system wired to gather downhole data and send commands was developed by Stuart Scott, now the principal artificial-lift advisor Permian for ConocoPhillips. The control program included input from Cem Sarica, a professor at The University of Tulsa, who was hired as an advisor based on his work on multiphase flow through reservoir rock.
The computer-controlled system creates a series of slugs that are pumped down a dedicated line into the reservoir, which Schwanitz said played a key role in containing the gas around the well.
Properties that make slugs a problem in production wells, where the viscous blobs can damage processing equipment, can be useful in the subsurface.
Based on the Liberty test, the slugs injected into the reservoir are “stable and appear to hold the gas in place between them, transferring hydrostatic pressure to the bottomhole,” Schwanitz said.
The fluid included surfactant that was chosen based on testing funded by Liberty Oilfield Services and done by David Schechter, a professor at Texas A&M. He is an expert on selecting surfactants which can free more oil from the reservoir rock and allow it to flow readily. The testing also identified chemicals that can stand up to the downhole chemistry.
“Once we introduce water, it tends to contain the gas very well,” said Adrian Williams, vice president of operations for EOR ETC, during the paper presentation at the Unconventional Resources Technology Conference (URTeC).
Early in the injection cycle, they observed a small gas-rate increase in a nearby observation well. After water slugs were added, the increase stopped, suggesting they could control the extent of the area treated, the authors wrote.
The water injection allowed them to quickly raise the bottomhole pressure from 1,000 to 4,500 psi, well above the 2,500 psi (the minimum miscibility pressure) needed for effective gas EOR.
The method sharply reduced the gas injected, allowing them to rent a smaller, widely available compressor commonly used for gas lift. But by the end of the job, it left Liberty wanting more .
“The injection system performed reliably, but ultimately less gas was injected—about 46 MMcf vs. the targeted 90 MMcf—due to surface injection pressure limits,” Pospisil said, adding, “given that most objectives of the test were achieved, it was decided to look for ways to improve the process for the next cycle.”
The result was not the relationship EOR ETC envisioned in its business model. Its goal is to become a one-stop EOR service provider that saves customers the cost of developing the expertise and buying equipment needed for EOR.
Liberty has a different plan. “We feel we made good progress with the EOR ETC system, but we want to develop a process we can implement with our own equipment and facilities,” Pospisil said.
A Brief Look
The test plan called for two injection cycles. Liberty halted it after one as the late fall season brought colder temperatures to North Dakota.
Injection began on 10 September 2021, not long after the delivery of a skid-mounted injection system was delivered on two, flatbed trucks. It ended on 11 October.
At that time, Pospisil said, they were already concerned that increasingly cold temperatures could interfere with the delivery, storage, and injection of the fresh water used for the test.
He added that they had learned what they needed to learn from one injection cycle. Based on one round of injection, the paper reported the 30‑day average production rose above 68 B/D in the months after the injection, compared to the 55 B/D predicted without treatment.
The paper also reported a small gain on another well on the five-well pad. Output from a nearby observation well below in the Three Forks Formation averaged 54 B/D during the 30-day period, compared to 50 B/D prior to injection nearby.
That gain suggests that injecting into one well on a pad could benefit others. If where the gas goes could be controlled and more of it delivered to nearby wells, it could spread the reach of a huff ’n’ puff method beyond a single well.
If that idea lives up to its promise of significant production gains, it could open “a whole new range of possibilities with unconventional wells,” Schechter said.
Testing Is Needed
What has occurred since the Liberty-EOR ETC test shows there are competing ideas about how to do WAG EOR.
Pospisil said Liberty plans to go back to the original well for further WAG cycles. They plan to switch from fresh water to produced water, which is free and reduces the cost of injection-well disposal.
The high salinity of the produced water, nearly 1,000% greater than ocean water, means it freezes at significantly lower temperatures. But it also requires finding chemicals that are salt-tolerant, which are likely to cost more.
“We are working to identify a surfactant that is effective even for Bakken produced water,” he said.
Pospisil said they plan to try “a more traditional WAG. We feel like we made progress working with EOR ETC. We want to make a home‑grown solution.”
They plan to inject water and gas for longer intervals, “alternating for a few days each to achieve the target injection volumes of gas and produced water.” The injection period is again expected to run for about 30 days.
Liberty will also be using a more-powerful compressor capable of a 4,000-psi surface injection pressure, allowing more gas to be injected as the bottomhole pressure rises. It is bigger than the one used for the first test, but considerably smaller than the massive machines used by EOG.
Meanwhile EOR ETC was busy at URTeC meeting with potential customers.
Schwanitz said they are grateful to Liberty for the opportunity to report on a successful first test, but now they need to find customer No. 2.
Having the results from a field test is valuable, but one injection cycle followed several months later by spring floods that shut down production in the area leaves engineers wanting more.
The authors wrote that while the decline curve analysis showed a “consensus” 7,000-bbl gain, EERC simulations put the total at 4,400 bbl. EOR ETC put the gain at 10,000 bbl.
Petroleum engineers argue about future production estimates from wells with far more data from normal production.
The test was a bit like the first flight of the Wright brothers, which traveled 180 ft. In retrospect, Orville and Wilber Wright demonstrated innovations that could lift and control a powered flying machine. But at the time, skeptics said that short hop into a strong wind didn’t prove their plane could fly.
North Dakota has taken a long-term approach to finding ways to recover more of the oil in the Bakken, where a 1% gain represents a lot of oil. Field tests now are relying on lab work the EERC did years ago showing liquids-rich field gas is as effective as carbon dioxide for enhancing oil recovery.
Hoffman is encouraged by the rebound in field testing with an upcoming test by Hess. Over time this work will show which unconventional EOR ideas work.
Based on the incremental progress over more than a decade of work, Sorensen is optimistic. “The goal is to take what was learned from that cycle in the East Nesson and optimize it,” he said.
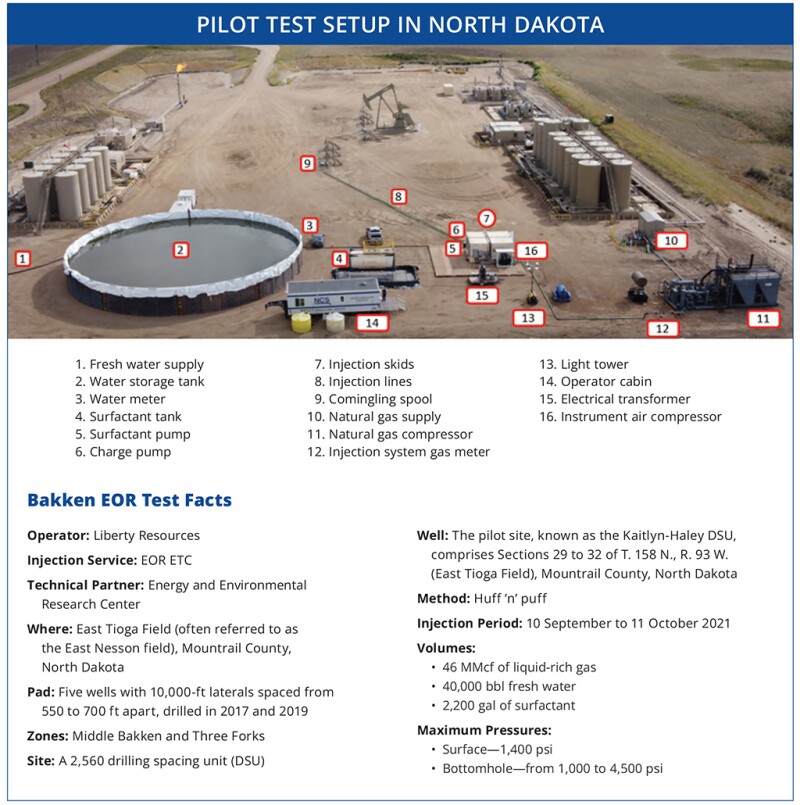
How Much More Could a Well Pad Produce if Every Well Were Treated Early and Often?
Unconventional enhanced oil recovery (EOR) tests have treated one well at a time using huff ’n’ puff while the production problems to be cured affect hundreds of thousands of wells.
A recent paper describing an EOR test in the Bakken suggested that stimulating a five-well pad using alternating injections of water and gas appears to also have increased the production at another well on the pad.
“We definitely see communication with nearby wells,” said Adrian Williams, vice president of operations for EOR ETC, while presenting a paper on the test at the recent Unconventional Resources Technology Conference (URTeC 3722974).
Gordon Pospisil, development advisor for Liberty Resources, who also saw some interaction during the water alternating with gas injection cycle (WAG), said it suggests that a huff ’n’ puff treatment on one well can increase the production on more than just the injection well.
It is enough to inspire thoughts about huff ’n’ puff pads. The wells on the pad would be treated sequentially, with the injection at one well aiding nearby wells.
Pospisil and Brian Schwanitz, president of EOR ETC, would like to see that tested to determine how treating a larger area by moving from well to well may affect long-term production and do it more efficiently.
Realizing that vision will require some well-pad changes to reduce the time and money required to change from production using artificial lift to injection and back.
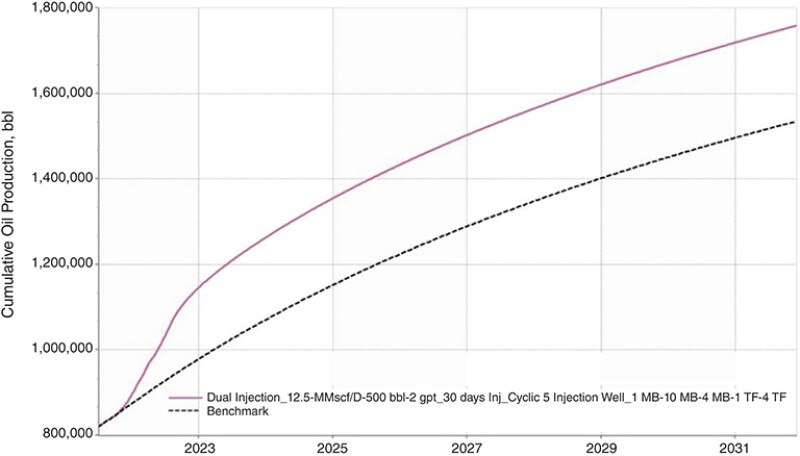
During the test, Liberty showed it could convert wells using jet pumps for lift to allow injection equipment to be installed without having to bring in a workover rig. Pospisil wrote that the cost of the changeover was reduced by employing “pump and casing tubing operations” to allow injections down the casing tubing annulus.
The downside of that approach is that jet pumps are low on the list of lift options.
A bigger challenge to changing the approach is that production engineers do not want to see good wells shut down for huff ’n’ puff with no guarantee the added production will cover the revenue lost during the injection period. They also worry the process may damage a good well.
A huff ’n’ puff pad could put that loss in a different perspective. Only a fraction of the pad’s production would be off at any time, and it may be possible to increase the production of wells during the injection period for a nearby well.
“The larger the area under injection, the more effective the use of gas and equipment becomes. EOR economics will be best when implemented at scale,” Pospisil said.
The payoff for doing an EOR project is also greater if it is done early in a well’s life when its production is higher, and the downhole pressure increase required for effective EOR is lower.
This again raises alarms from those who do not want to trying something new that could damage a good producer. Pospisil countered, “My view is if we take a well and double production to 500 B/D, that is better than several wells where they increase it by the same percentage to 100 B/D.”
For Further Reading
URTeC 3722974 East Nesson Bakken Enhanced Oil Recovery Pilot: Coinjection of Produced Gas and a Water-Surfactant Mixture by Gordon Pospisil, Liberty Resources, et al.