Few things in the oil and gas industry grab quite as much attention as the discovery of a new, untapped offshore field with a few billion or so barrels in the ground. One that eventually sprawls into a complex of wells that take years to be drilled. All the while, driving a mass of workers and welders at some distant yard to build the towering facilities that will bring in first oil.
But once a greenfield turns a darker shade, the margin for error narrows. Things don’t quite work the way they were supposed to. That’s when engineers need to step back in and work the problem.
BP has faced this reality recently at its heavy-oil field offshore the Shetland Islands where waterflooding problems are clogging up injection wells in a big way. Across the ocean, Talos Energy suffered from a different unexpected issue when a reliable but depleting asset suddenly lost most of its pressure support in the Gulf of Mexico. Sometimes the big problem is smaller in scale but still calls for critical action to be taken, such as a leaking subsea wellbore.
Each of these scenarios represent the backdrop of technical papers presented by a disparate cast of engineers at SPE’s Offshore Europe which was held virtually last week. Their work and presentations reveal how continuous improvements and innovative thinking are key ingredients to properly caring for aging assets. Highlights and links to the full papers for download are below.BP “Pumps Up The Volume” To Keep Shetland Wells Kicking
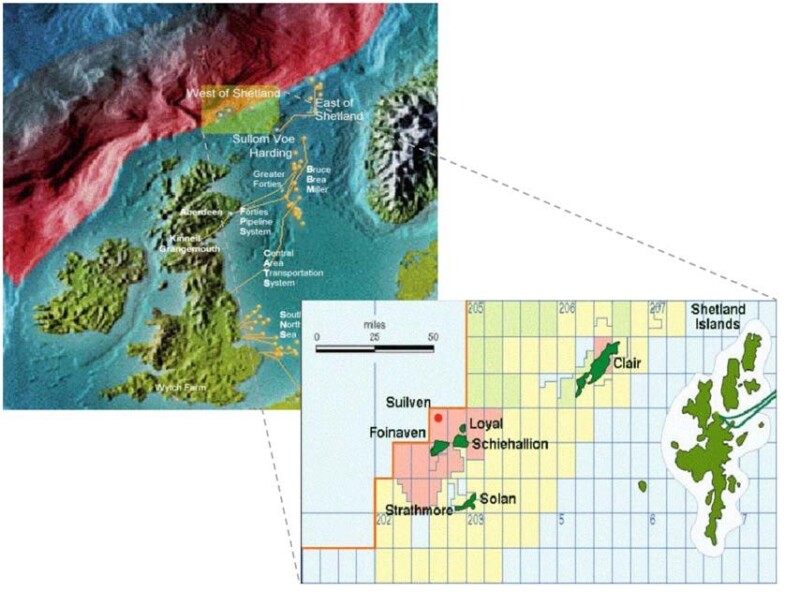
BP operates the Schiehallion heavy-oil field located 175 km off the west coast of the Shetland Islands where production began in 1998. In SPE 205426, the London-based operator along with Schlumberger and an equipment supplier, explain what it has recently taken to sustain the field which is one of the largest still producing in UK waters.
The Schiehallion field has had documented production issues and, along with two satellite fields, may have peaked in 2018 at 106,000 B/D before seeing a decline of at least 25%. This is according to S&P Global which pointed out that in 2020, Chrysaor, a 10% stakeholder, pegged output from Schiehallion at 60,000 BOE/D.
The production shortfalls started soon after a new floating production, storage, and offloading (FPSO) vessel was brought to the field in 2017. By then, the development strategy had become almost entirely reliant on being able to pump around 320,000 B/D of water into 36 injector wells. In each, a mix of seawater and all of the field’s produced water is reinjected.
BP favors produced water reinjection (PWRI) in this project and elsewhere around the world to mitigate environmental impacts—but there’s a big catch for the business case.
“If you are going to do PWRI, you do have to think long term,” said Alistair Roy at the conference. “You always start off and see water—it’s all very nice. Your long horizontals work great, and then you start pushing this stuff down towards [the wells] that doesn’t really help the equation.”
Roy is a principal petroleum engineer with BP and one of the coauthors of the paper that’s titled Pump Up the Volume—Massive Water Injection Increase Through Open Water Stimulations. It lays out the dilemma facing BP at Schiehallion and why it is now likely to depend on regular subsea interventions in order to perform.
Less than a year after commissioning the new FPSO, some of the injector wells started seeing up to 75% losses in their injectivity capacity. Subsequently, all 36 have suffered to varying degrees.
BP realizes that there are likely a few damage mechanisms at play, including residual oil droplets, sand grains, and calcite particles that have all been found in the field’s produced water.
This meant that part of the solution would require BP to get moving on improving the injection water quality to at least slow down the worsening conditions. Meanwhile, the first order problem remained how to remediate the plugging that had already strangled injectivity across the development.
For that, BP designed a subsea intervention operation that would have to escalate in scope and sophistication in order to deliver economies of scale.
On the first three wells, BP contracted a single construction vessel to deliver individual subsea well treatments. The first stimulation was performed on a producing well in 2018 and then the focus was squarely on injectors.
A pair of injector wells stimulated in 2019 saw their combined injectivity capacity jump by around 20,000 B/D of water. Sustained improvements were enjoyed for more than a year, spurring BP to continue with an 8-well campaign in 2020.
However, the vessel of opportunity hired for those first jobs only had “basic pumping capability and storage available,” BP said in the paper. In lacking all the specs BP ultimately decided it needed for its acid and chemical treatments, the single-vessel approach drove up project costs by “spending significant periods on loading, tank cleaning, port calls, and connected time.”
BP also suffered high last-mile costs because it relied on tanker trucks to deliver the remediation chemicals to a remote island port without experience in handling the potentially hazardous materials.
This is why for the 2020 campaign BP planners decided to “pump up the volume” by adding a purpose-built stimulation vessel to the mix. By switching to a two-vessel strategy, BP gained efficiencies and more pumping muscle that enabled rates as high as 8 bpm vs. less than 5 bpm. Some of the high-level results:
- Normalized costs on the two-vessel campaign fell by 34% compared with the initial stimulations, thanks in part to debottlenecking the chemical handling at the stimulation vessel's home port.
- It also enabled two batch treatments of three wells at a time and stimulations of more than 11,000 bbl of fluid in under 9 days.
- This is compared with more than 29 total days for the three single-well treatments (the producer with 645 bbl and just over 1,800 bbl of fluid for the injectors) pumped via the subsea construction vessel.
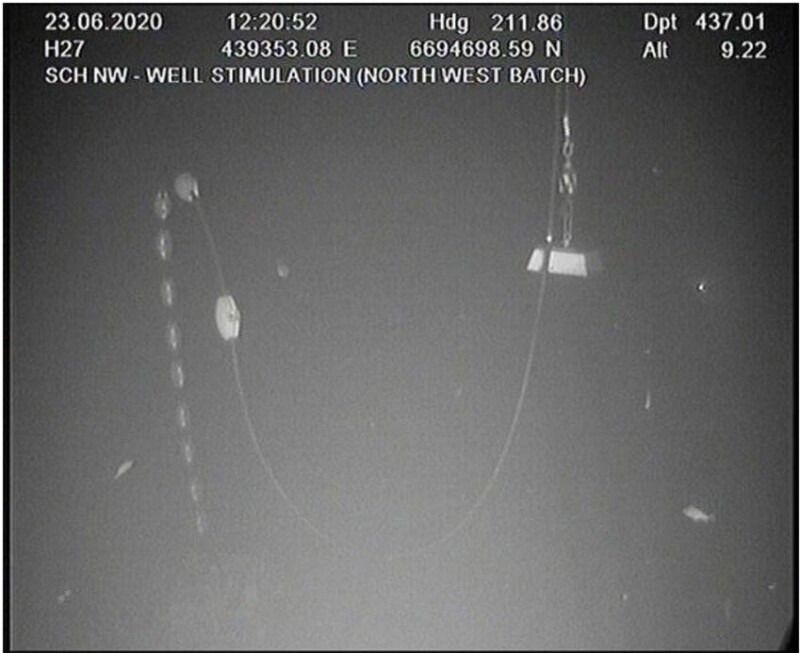
In terms of accomplishing its ultimate objective, BP reports that only 4 of the 10 injector wells sustained improved injectivity rates for longer than a few months post-stimulation.
Each of the successful cases involve wells that operate at close to or above the formation's fracture gradient. This point is something the paper's authors said might need to be replicated in other wells to achieve better results, yet it’s not as straightforward as that.
“Operating at the fracture gradient, however, can be incompatible with delivering conformance in long horizontal multizone wells. For PWRI systems, choices may have to be made to focus on maintaining water volumes at the expense of conformance,” the paper reads.
Aside from this, the short-lived improvements seen in most of the injectors has only increased the priority to solve for the root cause—the poor quality of the injection water. At the top of its longer-term to-do list is upgrading the PWRI system with filters and solids-removal capabilities.
In its shorter-term stimulation plans for the other injectors, BP is considering making improvements that may include using a different acid, adding chelating agents, scale treatments, and the use of a single vessel with greater capabilities.
BP lists several more of its most important lessons learned from this project in its paper and notes that there are more than 100 subsea wells off the Shetland coast that may be candidates for similarly aggressive chemical treatments.Why Talos Had to Do US Deepwater’s First Dumpflood
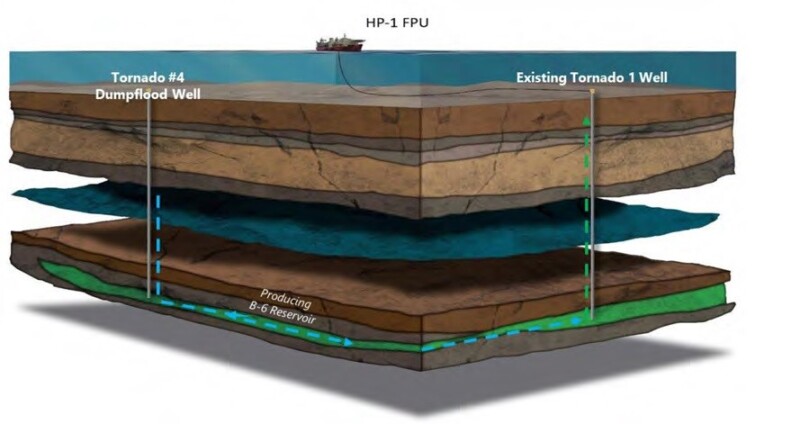
In presenting one of the non-European papers, SPE 205449, Houston-based Talos offers a detailed account of how and why it completed the first dumpflood operation in the deepwater US Gulf.
Faced with a small footprint to solve the problem, the largest pure-play independent in the Gulf was ultimately able to prop up production from the field. Time will tell if the positive outcome has offered a template for other deepwater assets in urgent need of a boost.
The dumpflood operation involved drilling a well in 2020 to tap into a saline aquifer that is above the Tornado reservoir. By the time the paper was submitted for the conference, Talos was using that single wellbore to inject around 20,000 B/D of aquifer water into the lower formation and seeing a 4,000 B/D improvement over pre-injection levels from the reservoir's first two producers.
Discovered in 2016, the Tornado field is far from qualifying as one of the most mature projects in the region but it has certainly seen some growing pains.
Bilal Hakim, a coauthor and senior reservoir engineer at Talos, noted during his paper presentation that the first two wells came on strong and held steady at a combined output of about 30,000 B/D. Then, after about 3 years of bountiful production, "severe pressure and rate declines started to affect the performance of the reservoir," Hakim related, adding that this meant there was "an imminent need for pressure support."
Whereas initial pressures were above 14,000 psi, now the bottomhole was measuring at just 6,000 psi. Instead of being a aquifer-driven reservoir, as was first believed, Talos was seeing the signs of what is described in the paper as a "predominate depletion drive or very weak waterdrive system."
Despite the situation, with excellent oil mobility and reservoir connectivity, Hakim said the modeling suggested a waterflood would be ideal. If Talos could figure out a way to do it, recovery rates might reach as high as 45–55% which Hakim noted would effectively be double primary recovery from the field. In June, Talos reported that 34 million BOE had already been produced.
Several options to achieve a new lease on the life for the field were considered but were for one reason or another ruled out.
- A standard topside water injection scheme was eliminated due to lack of deck space on the host facility, a floating production unit in about 822 m (2,700 ft) water depth.
- A subsea injection system would have been too expensive given forecasted field economics.
- Other concerns included reservoir compatibility risks that come with using produced water or seawater.
The constraints led technical staff at Talos to go with a dumpflood using a natural source of water at about 19,000 ft total depth to drive up pressures in the oil reservoir that is about 1,000 ft deeper. A final decision came after a study concluded that the aquifer water posed a low-risk for reservoir combability.
The company emphasizes that deepwater dumpfloods are rarely performed, and Hakim said the reservoir team could find no evidence that one had ever been done before in the deepwater of the US Gulf. He added that where dumpfloods are more commonly applied includes shallower US Gulf shelf locations that rely on dry tree platforms and in onshore fields.
It is also often the case that the dumpfloods are conducted without flow control or surveillance systems, which of course keeps costs down. However, this blind setup is far from desirable when the fate of offshore wells that each cost tens of millions of dollars is in question. So, Talos added those elements, e.g., inflow control valves, a downhole flowmeter, and permanent downhole pressure gauges.
Outside of the scope of the paper, but noteworthy, Talos executives said in an August earnings call that a third Tornado well drilled this year outperformed the 8,000 to 10,000 BOE/D initial production rate it had expected. The company also reported that its dumpflood injection rate has been bumped up to 30,000 B/D of water. Disposable Fiber Hunts Down Wellbore Leaks in Minutes
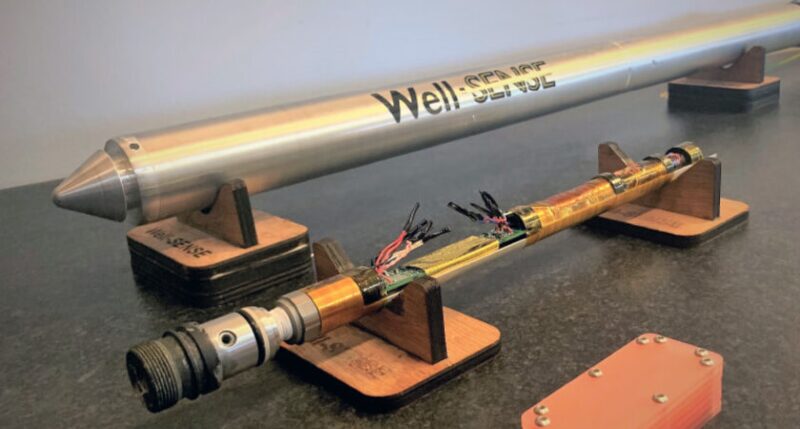
In SPE 205425, Well-Sense Technology presented details on the successful deployment of a disposable fiber-optic probe in a North Sea well. The technology represents a new and rapid way to detect leaks in aging wellbores and was recently licensed by one of the oilfield service giants which has onshore ambitions.
Launched down a shut-in well (of an unnamed offshore operator), a probe weighing almost 16 lbs and full of coiled-up fiber line, fell to a depth of 8,850 ft in just 16 minutes.
Less than a half hour later, the wellbore leak was found.
These case study stats are possible thanks to the fiber’s visualized temperature and acoustic data that left no question as to the source of the problem. The data also showed how fluids were moving through the leak, traveling up and down the lower section of the annulus.
Founded in 2015, Well-Sense calls the approach fiberline intervention (FLI) and has so far used it in about 120 wells around the world.
The UK-based technology developer notes in its paper that around 30% of the industry's subsea wells are believed to suffer from sustained casing/annulus pressure which poses risks for both late-stage production and decommissioning.
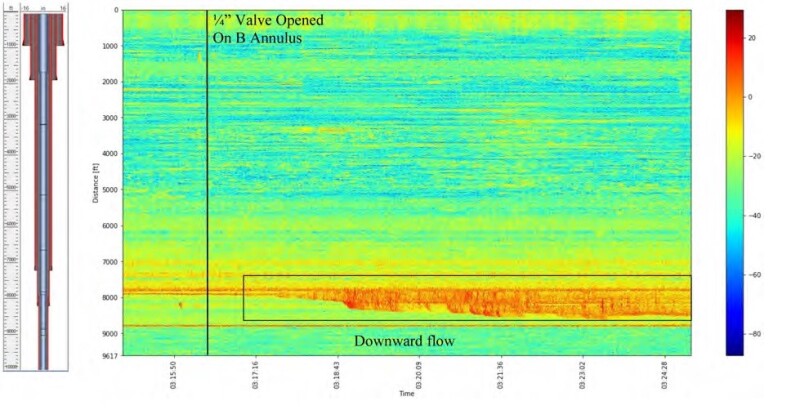
Once an FLI survey is done, the surface launcher is removed, and the fiber system is simply left inside the wellbore. At less than a quarter of a millimeter in diameter, the bare glass fiber will eventually soften and break apart once the well is flowing again.
This is according to Kevin Rose, an applications engineer at Well-Sense, who spoke at the industry conference about the technology. He described leak detection as the “spotlight application” while addressing the capabilities and limitations of the emerging technology.
“It doesn’t always work—it depends on the well,” said Rose, adding that Well-Sense has sharpened its definition of an ideal FLI candidate since its earliest days. That has pushed the firm’s success rate of reaching a desired depth to around 80%.
Well operators have traditionally relied on acoustic devices installed on bottomhole assemblies that must move down the well and stop once in a while to listen for the signs of a leak. Rose said a fiberline probe not only moves down the well much faster but that you “also get a richer picture than you would have if you were manipulating a work string up and down in a wellbore.”
In July, Halliburton announced it was licensing the FLI technology with the hopes of expanding its application to crosswell communication monitoring, an increasingly popular diagnostic used in US shale developments.
For Further Reading
SPE 205425 Disposable Fibre Optic Intervention System: Case Study of Successful Leak Detection Offshore North Sea by Craig Feherty, Andrew Garioch, and Annabel Green, Well-Sense
SPE 205449 First Successful Controlled Dumpflood in Deepwater Gulf of Mexico Results in Promising Incremental Rate and Recovery, by Bilal A. Hakim, Brandon Thibodeaux, Chris Brinkman, Joe Gomes, Kevin Smith, Ryan Cone, and Tom Messonnier, Talos Energy
SPE 205426 Pump Up the Volume—Massive Water Injection Increase through Open Water Stimulations by Alistair Roy and Anastasia Bird, BP; Samuel Bremner, Schlumberger; Lara Winstone, BP; Rustam Hashimov,OneSubsea; Doug Weir, BP; Judith Espinoza Perez, Maxtube Limited