The performance of unconventional wells depends on variables within operator control, such as stage length and fluid volume, and outside of that control, such as rock properties, geology, and market economics. The completion design must account for all of these factors. The other challenge has been the lack of availability of low-cost data that can be collected on a large scale to properly distinguish and separate the impact of these factors on completion performance. Collection and analysis are now possible with pressure data from the treatment and offset wells. The pressure data are a low-cost option to enable measurements on every well and implement established best practices for continuous improvement.
Complex, Multifactor Dynamic
Shale resource development is a complex, multifactor dynamic with optimization, commonly performed against one or more objectives: cost, resource recovery, and utilization. For the most part, the practice has been based on a few pilot projects in appraisal or early development and applying the lessons learned formulaically to capture economies of scale. This approach, although appearing straightforward, has fundamental flaws because of the variables within and outside operator control.
Although the data from these pilot projects are accurate, the data may not be fully representative of the conditions encountered during full-field development. These data become anecdotal instead of systematic by not fully and accurately representing the next pad or pads. If design A yields the same 90-day production at 10% lower cost in a series of wells than design B wells, is design A the better one? Without knowing the impact of rock properties and understanding whether A and B resulted in statistically separable outcomes, we do not know. Deciding to proceed with design A over B in the absence of such knowledge could lead to either understimulated or over-capitalized wells.
One popular approach to solve for this knowledge gap is to leverage public and private completion and production data comprising several hundred to several thousand wells within a given region. The data analytics can offer insight from correlations derived from measured completion parameters, production, and cost. A shortcoming of this approach, however, is extrapolating results into yet-to-be sampled completion design parameters.
For example, data were collected to adequately sample completion designs ranging from 5 to 12 clusters and were used to calibrate physics-based models. Should these models be used to predict the results for a new design with 16 clusters? In many cases, the model has not been calibrated and tested for 16 clusters to ascertain the accuracy and uncertainty in the model predictions, which could result in large uncertainties in future well performance. This commonly occurring situation of extrapolating results to the next wells with the inherent shortcomings can be resolved with pressure-based fracture measurements.
Accurate Design of Experiment
Pressure-based fracture measurements evaluate the separability of variables between two completion designs. These measurements can be deployed at a fraction of the cost of legacy technology, do not require a field footprint, and can be deployed at scale without affecting project economics. Operators are understanding and optimizing key completion parameters within and outside of their control to ensure an accurate design of experiment (DOE) that yields systematic insights. This approach is common to manufacturing industries.
In shale resource development, ongoing multipad data acquisition for optimizing the right completion design parameters had been expensive. That cost factor was the reason why, primarily, operators acquired fracture measurements from only 4% of their wells. But, with quantitative offset pressure monitoring in the past few years, this limitation is no longer a factor; the necessary data can be collected at a fraction of a well’s total completion. With the reduction in cost, some operators are embracing the necessity of routinely acquiring hydraulic fracture measurements to achieve continuous improvement.
With a simple pressure gauge attached to a wellhead, operators are acquiring affordable pressure data that offer unequaled knowledge into completion performance by measuring fracture geometry, fracture growth, and fracture interactions for a large number of stages. The following field example illustrates the relationship between data adequacy and a systematic DOE approach.
We wanted to understand which of five completion designs provide the best returns for the operator. The five designs were implemented on several wells to ensure adequate sampling of design parameters, such as stage length, number of clusters, and fluid and proppant volume, in addition to rock property and geologic variations.
The first step was to understand if the individual completion design results, as measured by hydraulic and propped fracture geometry, were statistically separate or if the designs yielded similar fracture geometries. In Fig. 1, the vertical axis shows the measured fracture half-length. The rectangles are the measured half-length for a single stage using a given completion design. If we look at a range of half-lengths, we have data from multiple designs that fall within this range. Can we say with any certainty if these designs are, in fact, providing similar results or if the results can be separable? This question can be answered if sufficient data have been collected as part of a design of experiment using existing statistical techniques, such as comparison circles.
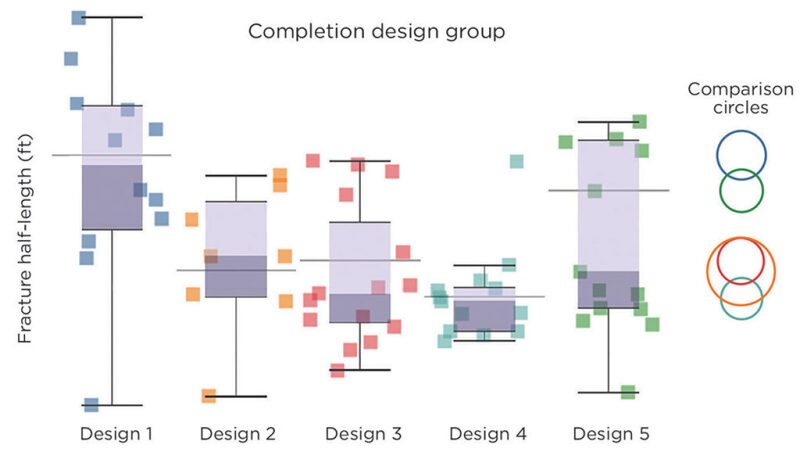
In the figure, the comparison circle colors coordinate with the completion design group. We can see that the comparison circles for designs 2 (orange), 3 (red), and 4 (green) overlap, but are separated from the circles for designs 1 (blue) and 5 (light green). This fact indicates that the three designs, 2, 3, and 4, provide similar results that are distinctly different from designs 1 and 5.
Bringing in information about production, geology, and cost enabled this operator to confirm the design that provided the best cost and performance going forward. Continuing routine and systematic offset pressure data enable the operator to select the best completion design for a given geologic setting as full-field development progresses. The operator can quickly decide if a unit’s varying geology requires a change in the treatment to support field development goals.
Statistical Confidence
With the simplicity and low cost of acquiring pressure data, operators are creating an accurate DOE for each unit to have statistically meaningful data within budget. These statistically significant results lead to improved completion designs. Pressure-based fracture measurements are a practical method to systematically separate, evaluate, and understand completion parameter effects on production within operators’ control and outside their control to reduce unit cost.
![]() | Sudhendu “Kash” Kashikar is CEO of Reveal Energy Services. He has more than 25 years’ experience in solving technology and business challenges. Before joining Reveal Energy Services in 2016, Kashikar was vice president of engineering at MicroSeismic Inc., where he supervised the commercialization of technology that quantifies unconventional well production behavior using microseismic data. At Silixa, he contributed to strategy development and implementation. During his 20 years at Schlumberger, he held leading roles in technology, operations, and business development. Kashikar holds several patents, in addition to authoring and coauthoring numerous technical papers and articles. He holds an MS in petroleum engineering from the University of Oklahoma and a bachelor’s of engineering in petroleum engineering from the University of Pune, India. |