The evolution of the SPE Separations Technology Technical Section (STTS) from its inception to its status today reminds me of an engineer’s little boy who asked for a simple tire swing hanging from a tree branch in the backyard, but ended up with a roller coaster and no tree. However, in the case of the STTS, the results are for the better. Separations technology-related content has been expanded and made available to SPE members through several venues.
The idea for the STTS originated about 10 to 15 years ago during my discussions with Ed Grave, fractionation and separation adviser at ExxonMobil. We considered the formation of a simple technical group to exchange ideas and experiences about separations. Separation design combines science and art, and we knew there was industry experience that could offer a base of shared understanding. How could we tap into that wealth of experience?
This idea lingered until 2011 when I mentioned it to Ken Arnold, senior technical adviser at WorleyParsons, who led me to John Walsh, SPE technical director for projects, facilities, and construction, and principal engineer for water treating at the GHD Group, and Shasta Stephenson, SPE technical activities manager. As a result, the STTS was born. This will teach me to talk to Ken again!
In less than a year’s time, SPE launched the STTS website, on which discussions were started by participants, and the STTS hosted a webinar, “Flow Conditioning Impact on Separations.” The 2012 SPE Annual Technical Conference and Exhibition (ATCE) included a special session, “Knowledge Sharing on Separations.”
The session covered separation topics ranging from issues with conventional separator design to emerging technology trends. Discussion centered on whether or not we really know how to design separators. The consensus was: maybe.
As Paul Jones, subsea manager at Chevron, wrote in “A Facilities Perspective” in Oil and Gas Facilities (December 2012), we have successful separators designed by various methods that include droplet settling and retention times. Arnold and Mark Bothamley, senior staff engineer at John M. Campbell, guided us through the industry’s design of separators.
Arnold concluded that we do not know much about separation. We need to admit this inadequacy and develop an understanding of the sizing of separators and improve our ability to predict the performance of separation equipment. Bothamley tackled the issue of our ability to reliably design conventional separators. He pointed out that the trade-offs between required performance and costs are often significant drivers in our designs. Luis Caires, director of R&D engineering at Cameron, tossed into the mix the ubiquitous monkey wrenches of surface chemistry, contaminants, and chemicals.
A panel discussion about emerging technology trends concluded the session and included comments by Grave, Ole Økland, manager of subsea technology and operations at Statoil, and Jimmie Riesenberg, engineering manager of compact modular processing systems at Chevron. And if you are not excited by separations, take a look at Fig. 1 showing the complexity and advancements in subsea processing.
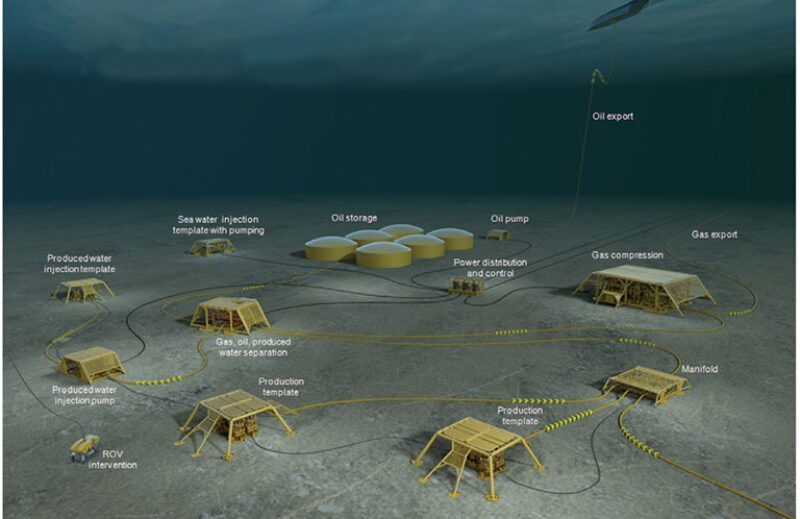
Statoil aims to develop the elements required for a subsea factory by 2020. Suited for resources located in deep, cold waters and harsh environments, the factory will make it possible to use remote-controlled transport of hydrocarbons at any offshore facility.
The Evolution of Separations Technology
Separations technology has come a long way from the onshore settling tanks to vessels on offshore platforms, and finally to the mudline that lies thousands of feet subsea. Application of subsea separation may offer economic advantages. By performing a three-phase separation on the seafloor, it is possible to increase cumulative oil production, reduce flowline infrastructure, enable viable flow assurance strategies, and to perform these functions with less power and fewer pumping requirements than subsea multiphase pumping. Subsea separation may be particularly attractive in deepwater fields, where the combination of low water temperatures and long risers presents challenges. Water separation and injection reduce the possibility of hydrate formation and may enable longer distance tiebacks.
Some of the most recent subsea installations are Statoil’s Tordis gas/oil/water separator in approximately 650 ft of water, Total’s Pazflor gas/liquid separator in approximately 2,700 ft of water, Petrobras’ Marlim inline separator unit in approximately 2,900 ft of water, and Shell’s Perdido caisson electric submersible pump gas/liquid separators in approximately 8,000 ft of water. The Marlim separating unit is multifunctional with a desander, gas/liquid separator, oil/water separation, and de-oiling.
Moving water treating facilities to the seafloor, with subsea separation and injection, reduces the requirements for topside facilities, operating costs, and environmental risks during upset conditions, and increases production.
Other examples of subsea processing are Statoil’s Aasgard and Shell’s Ormen Lange subsea compression projects. Both companies and their partners are in the process of qualification and testing of the subsea scrubber and gas compression units.
Currently, ExxonMobil has embarked on a significant testing and qualification program for its subsea applications. Its goal is to create a complete toolkit of subsea technologies that can be readily applied across the slate of prospects. This includes a three-phase gravity separation for shallow fields and a compact multicomponent system that enables three-phase separation for deepwater applications with a number of crude slates and gas/oil ratios.
Although subsea separation may be a new area of interest, the upstream and downstream onshore and topsides separation technologies are the main focus of the STTS. They offer plenty of challenges and room for improvement, and we learn to design for subsea from them.
Surface separation continues to encounter problems with large wash tanks for heavy oil dehydration, liquid carry-over from small compressor scrubbers, gas carry-under from production separators, and foaming in all parts of the separation train including contact towers. Water separation continues to have issues with tiny oil droplets and solids. Enhanced oil recovery methods bring in their share of separation problems.
There are many cases of successful separation designs and applications. However, the not-so-successful designs offer more opportunities for learning through the identification of root causes of the problems, and the development and application of the solutions.
The determination of root problems may involve field tests, computational fluid dynamics modeling, the changeout of internals, and chemicals. The problem ranges from the simple shearing of the fluids by a control valve to the complications found with foamy emulsions in a sloshing separator. And who has never encountered a problem that appears for a day or two and then resolves itself without an identification of its cause?
STTS Advances Information Exchange
The STTS offers a means of information exchange, developing designs, and networking. Its mission is to provide a forum in which technical professionals and academia in the area of separations can:
- Share knowledge, experiences, and best practices
- Identify major issues and technology areas in which to focus cooperation and discussions
- Maintain and promote industry awareness of separation-related issues and technologies
- Enhance their own technical competencies that meet the needs of the petroleum industry
The STTS is also striving to initiate change on a larger, industrywide scale by pursuing the development of a global joint industry program (JIP) to enhance separation technology and make qualification more cost-effective by qualifying separation equipment only once for members.
The proposed JIP could streamline the validation and qualification process and help in developing global testing procedures, guidelines, standards, and provide an avenue for cost-effective fundamental separation research.
STTS members can follow the progress of the JIP at http://communities.spe.org/TechSections/STTS/default.aspx, where webinar and 2012 SPE ATCE presentations are available.
The STTS membership has grown to more than 150. The nominating committee is currently looking for SPE members to take on leadership roles starting in October. If you receive a call from a member of the committee, please consider accepting the nomination.
If you have not already done so, join the STTS and check its website forum discussions on separation issues related to enhanced oil recovery and design methodologies. Keep an eye out for the three separation focused webinars planned for 2013. We also welcome your ideas and suggested topics for the special session on separations, now in the planning stage, for the 2013 SPE ATCE in New Orleans. The annual STTS meeting will be part of the special session, so we hope to see you there.
R