The market turmoil of 2020 left the upstream industry with diminished ranks, palpable concerns over long-term demand, and mounting pressure to reduce its carbon footprint. This made for what many consider a bullish case, asJPThas reported, for robotics uptake over the course of the decade.
But there are reasons to temper expectations. After all, this is the oil and gas industry. The upstream landscape is as vast as it is specialized. Each silo is a fortress of status quo to which robot developers must dedicate significant time and fortune in conquering. Some are worth the battle, especially in the offshore arena where factors of cost and safety have made this the most active corner of oil and gas robotics. Many other use cases may be worth bypassing.
About 70% of the world’s oil and gas supply is produced onshore which, of course, is much more accessible to human operators. That means a robot dog in the Permian Basin has to jump over a much higher bar in order to create value than a robot dog tasked with inspecting a platform in the middle of the Norwegian Sea.
Speaking of inspection, this is both the chief strength and upper limit for much of the current generation of robots. The next generation will be asked to fix things. And whatever they can’t do—or are just not the right tool for—look for it to be covered by industrial automation.
As a new class of oil and gas robots finds its niche, and fights for investment dollars along the way, here are a few developments to track and points to consider.
This Time It’s Different, Right Boss?
The upstream sector pulled back from exploring the frontier of robotics and drone technologies in the last decade relative to other industries, but it is now being pulled forward by societal and technological shifts, according to Ed Tovar who runs an Austin-based consulting company, InTechSys, that serves the defense and energy industry.
“It comes down to budgets, and leadership at the top,” he said of the slow pace of change for oil and gas robotics up to now. Tovar recalled a recent US onshore upstream research project involving unmanned cargo aircraft that was halted “due to the optics” of adopting job-replacing robots in the middle of industrywide layoffs.
He lists climate change, the global push to electrify equipment and transportation, and a political climate that favors renewable energy as the biggest reasons to expect this latest downturn to mark a turning point for the industry’s investment in robotics. “All the above are not bad but cannot be denied anymore,” and as a result, the industry will be forced “to make adjustments faster than we have in the past, and that normally starts at the top and in the boardrooms to push for greater and faster results,” said Tovar.
Placing Job Destruction in Perspective
Even with oil prices above $70/bbl, the industry is not hiring back at quite the same clip as it has during other recoveries, says Sumit Yadav, an energy service analyst at Rystad Energy. Yadav was the lead researcher behind the Norwegian consultancy’s recent report that found up to 400,000 oil and gas roles across the globe might be replaced by robots and automation by 2030. It’s a striking figure, and so it’s worth putting into perspective.
- Robots may soon be capable of taking over many positions, but Yadav points out that “the downturn was definitely more destructive,” in terms of jobs, and adds, “while it sounds like a doomsday scenario, I believe that in many cases these robots will have complementary work roles” to human operators.
- Rystad’s own estimates peg US oil and gas job losses as a result of the 2020 oil price crash to around 120,000 in 2020, down from about 1.08 million jobs in 2019. As the effects of the pandemic on the global economy remain uncertain, Rystad said in March that total staffing numbers could fall by another 10,000 in the US oil and gas sector by the end of this year.
- While easy to conflate with robotics, industrial automation deserves a distinction since it may deliver a bigger impact to much of the oilfield (e.g. artificial lift and drilling rigs) and therefore could limit the need for crawling robots with articulating arms. “With respect to this, I believe there is definitely faster adoption within the automation space…that it is the low hanging fruit,” said Yadav.
- Rystad found that the job groups to be most affected by robots are on the operational side and more specifically in the inspection, maintenance, and repair sector (IMR). For now, a heavy emphasis must be placed on the “I” since it represents the most expansive area of commercial solutions available to oil and gas companies.
- To bolster their value proposition, robot developers are being challenged to offer more than surveillance and inspection. “Robots are definitely making major strides,” in this regard, said Yadav, adding that, “Now, they are at least able to replicate the basic tasks pretty well.”
- In the short term, robotic welding may prove to be a popular use case in upstream while in the medium-term, automated trucking and equipment could bring the most disruptions to the logistics and supply chain sectors in onshore markets with tech-friendly policies.
European Experiments Will Shape Industry Direction
A key area to watch for a breakout on this front will be in Europe where several marquee research and development projects are nearing important milestones. The results of these programs are likely to be bellwethers that will inform the wider offshore industry about the feasibility of robot deployments in the near term.
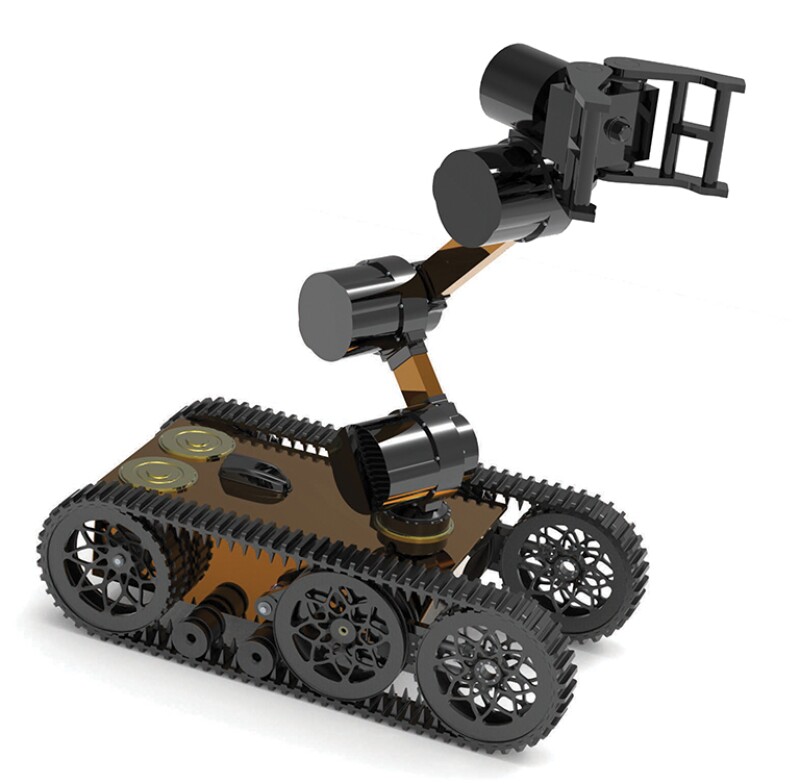
ARGOS
- Led by the newly renamed Total Energies, the ARGOS project has set a 2024 deadline to introduce an autonomous offshore work-class robot that can “operate a low-complexity production site like a wellhead platform of a well pad.”
- The robot, nicknamed Stevie-2 and built by Austrian firm Taurob, is scheduled to begin its first tests this year to prove among other things its durability. Designed to help scale up the use of normally unmanned facilities, the robot must require maintenance no more than once a year.
- The preceding generation, called the Taurob Inspector, has successfully cleared more than 2 years of offshore trials in the North Sea and is being deployed this year with ARGOS partner Equinor at its Johan Sverdrup field.
- Bottlenecks remain, however. Authors from Total highlighted in a 2020 technical paper (SPE 202667) that new skills are needed for those overseeing the robots, the ability to future-proof robotic investments remains a concern, and even though they are autonomous, an operations center is still needed to manage them all. Total found through a pilot project “that upscaling robotic solutions on site to a fleet of robots is far from obvious if the current scheme of one robot/one technician seen today is still applied.”
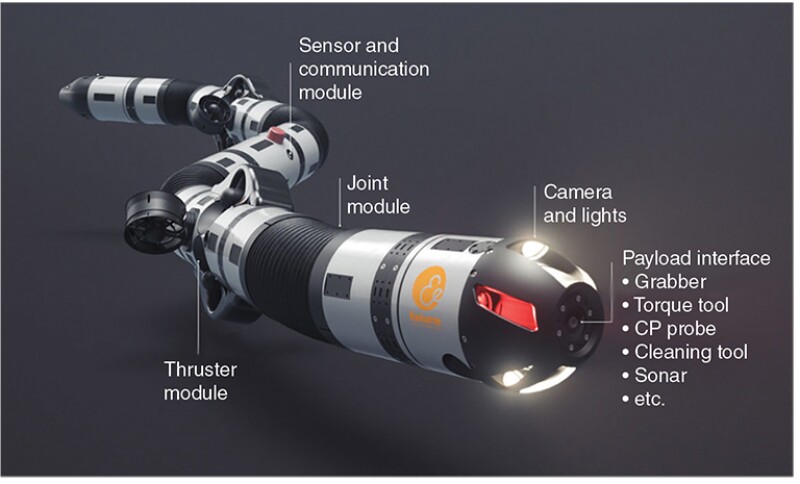
Eelume
- The Eelume is another high-profile innovation that is hoping to achieve commercial success soon. The eel-like system is a “resident” underwater vehicle with light intervention capabilities and was designed to reduce the need for support vessels and traditional remotely operated vehicles to check on subsea systems.
- Founded in 2015, Eelume Subsea Intervention said recently that its nearly 20-ft long subsea robot is scheduled for a final round of tests this year with Equinor at its Åsgard oil and gas field located nearly 125 miles off the Norwegian coast. Eelume is hoping to follow up with its first commercial deployment next year, and within 5 years, the company says it may have as many as 50 robots operating in subsea fields around the world.
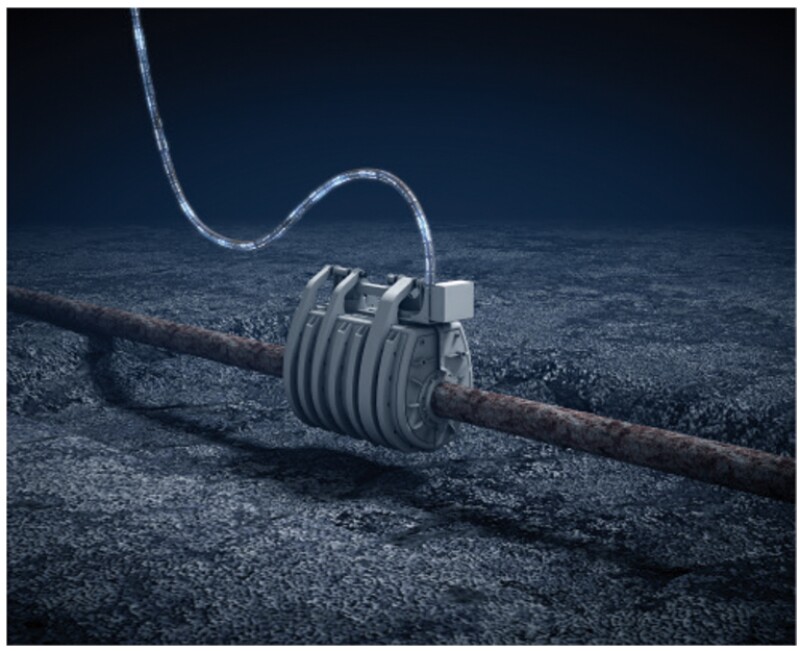
Nautilus
- The Nautilus, a pipeline and flowline repair robot, is a relative newcomer that was born from the venture capital arm of Thailand’s state-owned oil and gas company PTTEP and Norwegian robotics firm Kongsberg Ferrotech. The clamshell-shaped robot extracts portions of leaking or corroded pipe and then replaces them with new ones using composite material and 3D printing.
- In March, the companies announced that they would be working with Equinor on advanced testing for the Nautilus. Equinor invested in a similar robotic concept back in 2007 that was apparently ahead of its time after not achieving commercial success.
A Nod to the Production Helpers
Robots can climb up stairs and will soon be working around the wellhead on a routine basis, connecting hoses and opening up valves. But what about more complex jobs like improving production? As the following innovations show, highly specialized robots already exist for this in some cases, and in others there remains substantial ground to cover.
E-Line Well Tractor
- One technical paper (SPE 203064) outlines an e-line-conveyed robot built by Welltec and deployed by Saudi Aramco in 2019. In the case study, the UK-headquartered Welltec robot successfully moved via a tractor system several thousand feet down a horizontal well—its first-ever deployment in an open hole—where it took samples of the blocking material for future planning and remediated scale damage before returning to the surface.
- The robot and its controllers on the surface rely on an algorithm to detect blockages. If there is fluid in the wellbore, an auger tool is selected for scale removal; if there is loose material in the well, a suction system is selected.
- The pre-outbreak case study was a proof-of-concept meant to demonstrate that single-run robotic interventions are a viable, lower-cost alternative to rig-based or coiled-tubing interventions in the onshore market, even in open holes which present more challenges. Drilling a sidetrack in the lateral section during milling operations was a top concern, but was ultimately avoided by extending the robotic wheels to provide centration.
- Though they were first introduced in the 1990s, this class of robotic downhole tools could benefit from renewed interest among capital-sensitive operators that are focusing more on harvesting production from existing wells. Additionally, workover rigs require more manpower and are facing scrutiny for their carbon footprints, which may make e-line robots more attractive.
Annelida
- Petrobras is working with partners in Brazil on a robot called Annelida that is designed to remove hydrate and paraffin plugs from offshore flowlines. The most recent technical paper (SPE 196015) describing the experimental trials cites these flow-assurance issues as the top business driver, noting they can stop a well from producing for months, “causing huge financial losses.”
- While still in the development phase, the robotic tool is envisioned to be loaded into a flowline from a floating platform where it will move via tractor systems (one for moving forward, a separate one for moving backwards) down to clean hydrates and waxes. The development team says the Annelida robot may have several other use cases, including inspection of “unpiggable” flowlines.
- Current techniques include depressurizing the flowlines, using heated lines, and chemical injections—all of which may not be effective and are considered expensive options in any event. Petrobras’ proposed robot would be a jack-of-all trades, using several remediation techniques: mechanical removal, chemical removal, or controlled heating. The first field trials were slated for the end of 2020.
Industry Likes Robots, But Does It Love Them?
It’s not just automation but the whole idea of driving efficiencies through software that’s generally more attractive to oil and gas companies than is robotics. This popularity contest may negatively impact robotics uptake by siphoning funds toward other technologies.
- AI-based logistics, analytics, and machine learning, along with cloud computing, wireless networks, and the Internet of Things have all seen more implementations and pilot tests than oil and gas robots, according to a PricewaterhouseCoopers (PwC) survey done after the onset of the COVID-19 pandemic.
- Based on the responses of more than 200 oil and gas companies, PwC found less than 20% have implemented any kind of robotics program and only a sliver said they were in the midst of pilot programs. Predictive maintenance technology claimed the top spot in the PwC survey with around 70% of respondents at some stage of implementing, piloting, or planning to use it. Ranking last on this list of priorities was robotics and drones.
- A separate report on “The Future of Work” commissioned by the American Petroleum Institute and led by IHS Markit serves as a bookend of sorts in that it captured the thoughts of industry professionals immediately prior to the pandemic. It too shows that while robotics is an interest area, it is not the top priority for the upstream sector.
- Like PwC, IHS grouped robotics and drones together for its analysis and found that they receive more attention from larger exploration companies while smaller producers focus the bulk of their technology budgets on digitization and automation. IHS also noted commercial struggles with the new wares and that “several industry drone programs have recently been terminated owing to cost concerns.” Despite this, IHS says robots and drones are on track to become “force multipliers within the oil and gas industry” and may even reach maturity prior to many AI applications.
For Further Reading
SPE 196015 Annelida, a Robot for Removing Hydrate and Paraffin Plugs in Offshore Flexible Lines: Development and Experimental Trials by Hugo Francisco Lisboa Santos, Petrobras; Eduardo André Perondi, UFRGS; André Viegas Wentz, Senai-RS et al.
SPE 202667 Operation Room: A Key Component for Upscaling Robotic Solutions on Site by Jean-Michel Munoz, Eric Bartoli, and Serge Macrez, Total.
SPE 203064 Wireline Conveyed Robotic Intervention for Obstruction Cleaning and Sampling in Horizontal Wells Completed with Open Hole—Worldwide First Job Experience by Timofey Yakovlev, Hani Sagr, and Sultan Al Harthi, Welltec; Fahmi Aulia, Saudi Aramco.
Want To Learn More About Oil and Gas Robots? Don’t Miss This OTC 2021 Technical Session: Advances in Robotics, Wednesday, 18 August @ 10:14-12:04 |
· Autonomous Subsea Field Development - Value Proposition, Technology Needs And Gaps For Future Advancement - ExxonMobil; Saipem · First Use Of ROV Remote Operations From Shore In The Gulf Of Mexico - Oceaneering International; Shell · SeaRAY Autonomous Offshore Power System (AOPS): Results Of Sea Trials And Payload Support Demonstration - C-Power · Aerial Robotic Systems (Drones) For Contact-based Ultrasonic Wall Thickness (UT) Measurements At Height – Apellix · On The Subsea Production System Availability With Resident Drones. A Reliability, Availability, Maintainability (RAM) Analysis - Saipem |